If you’re looking for a get-rich-quick scheme, you can scratch “Doing small-scale manufacturing of ultralight aircraft” off your list right now. Turns out there’s no money in it. At least, not enough money that you can outsource production of all the parts. Not even enough to setup a huge shop full of customized machining tools when you realize you have to make the stuff yourself. No, this sounds like one of those “labors of love” we always hear so much about.
So how does one do in-house manufacturing of aircraft with a bare minimum of tools? Well, since you’re reading this on Hackaday you can probably guess that you’ve got to come up with something a bit unorthodox. When [Brian Carpenter] of Rainbow Aviation needed a very specific die to bend a component for their aircraft, he decided to try designing and 3D printing one himself.
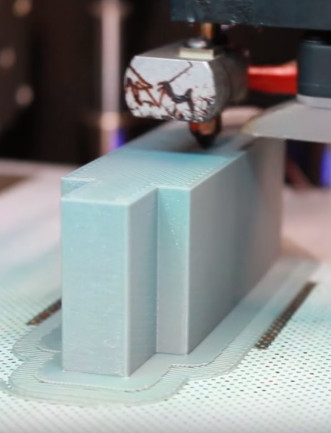
He reasoned that since he had made quick and dirty dies out of wood in the past, that a 3D printed one should work for at least a few bends before falling apart. He even planned to use JB Weld to fill in the parts of the printed die which he assumed would start cracking and breaking off after he put it through a few cycles. But even after bending hundreds of parts, wear on the dies appears to be nearly non-existent. As an added bonus, the printed plastic dies don’t mar the aluminum pieces they are bending like the steel dies do.
So what’s the secret to printing a die that can bend hundreds of pieces of aluminum on a 20 ton brake without wearing down? As it turns out…not a whole lot. [Brian] attributes the success of this experiment to designing the die with sufficiently accurate tolerances and having so high of an infill that it may as well be solid plastic.
In fact, the 3D printed die worked out so well that they’ve now expanded the idea to a cheap Harbor Freight brake. Before this tool was going more or less unused as it didn’t have features they needed for the production of their parts, namely a radius die or backstop. But by 3D printing these components [Brian] was able to put the tool back to work.
We’ve previously covered the art and science of bending sheet metal, as well as a homebuilt brake that let’s you do it on a budget even Rainbow Aviation would scoff at. So what are you waiting for? Go build an airplane.
Thanks to [Oahupilot] for the tip.
This is a great hack and a terrific testiment to the genius born of necessity.
I can only disagree. I’d have that part machined out of scrap nylon in about 15 mins.
+1
This is a good solution for hackers because they are more likely to own a 3D printer than a piece of scrap nylon that is big enough for the task. Plus it’s a great video that aptly points out the surprising strength and durability of a 3D printed part. Well done!
You better be joking. Even if you don’t have a suitable piece of plastic lying around it can be had for pennies or maybe even for free if you ask nicely.
The thing is that whrn you have a bussiness, making tools is something you dont directly make money from. Printing a tool allows you to quickly design a tool and leave the printer doing its job while you can makr money doing the things that dont need that tool right now. Also the only sources i have for nylon sheet and bars are still really expensive
1″ x 3″ Nylon maybe goes for about $30 per foot. You can always rationalize a solution based on hypothetically free material. But I’m looking around my shop and I don’t any free nylon to be honest. If you have a free source of material please share a link.
I think it would be more likely for a “hacker” to have a 3d printer than a milling machine like a Bridgeport. I’m lucky enough to have both and a decent lathe so I get aigoj’s point. In the end he used what he had access to and got the job done.
So you’d have a shop with a powered bending brake, but no milling or cutting machinery of any sort? Not even a drill press?
Dax I’m not gonna lie…i didn’t watch the video before commenting, I was responding to aigoj’s call out. Having tried it for myself in the early days a drill press is a disappointing mill at best. To be honest if I needed something like that and didn’t have access to a mill I would have roughed some steel with a die grinder and finished it on a bench grinder…but I’m old school like that and it takes considerable skill and confidence to go at it that way. By 3d printing the part he showed that 3d printed parts are capable of something most would think it would be inappropriate for.
As a personal experience, I 3d printed some vee blocks for a flow drilling machine at work. Before I started the boss was cheaping out and having the blocks made from aluminum, they wore out very quickly because we mainly work with 316L which is much more hard than the aluminum. At first I machined a new block out of aluminum bronze which should have been almost as hard as the 316L and work hardens…the idea being that it would harden up after a while and maintain its shape. It didn’t work out, the aluminum bronze lasted longer than the previous aluminum blocks but not as long as hoped. I then printed a block out of nylon and it has been in service since with very little wear except for some marring from red hot stainless on one side of it. Could I have machined another block from some exotic alloy? Yes I could have but it would have been something truly special as normal tool steel could contaminate the 316L and lead to future corrosion; the 3d printed nylon was the safest bet and to date has been the best solution.
Agreed. Aluminum, mild steel, nylon… The geometry is too simple to bother with a 3d printer.
Sure you could– but they had a 3D printer and gave that a try instead and it worked out for them. Doesn’t mean some other solution wouldn’t also work, or even work better– or even cheaper and easier. It’s still a hack, and it’s still genius.
My favorite use of 3d printing is to make things that make things .. jigs, molds and now beake molds are on the menu.
Btw, speaking.of menus, it’s pretty easy to make custom bakeware … these forms for baked donuts we’re made by 3d printing positives and then taking.impressions in food-safe silicone.
http://www.biorealize.com/news/2016/9/2/microbial-donuts-with-biorealize
“beake” ffs .. amd no way to edit
Same can be done when making wax injection molds
Wait, are you making mods out of wax, or injecting wax into molds?
No reason you can’t do both :P
My first in-house 3d printed parts was a fixture to hold parts for a secondary ops.
Very intriguing use of 3d printed parts. I would never have guessed that it was possible for 3d printed parts to have the strength and durability to be used in such a fashion. Color me impressed!
Even as a big believer in 3D printing, I have to admit I was still very surprised to see how well these parts held up. If I had to guess, I would have said they would have crumbled up like cardboard in this application.
That’s precisely what I would have expected also.
It helps that they’re relying on the structure of the fuselage to provide strength with minimum weight, so the aluminium sheet is quite thin.
Z-Ultrat, the filament used, is basically ABS with some lubricants and a touch of Polycarbonate thrown in.
From the MSDS Sheet:
COMPOSITION / INFORMATION ON INGREDIENTS
a. ABS (Acrylonitrile-Butadiene-Styrene) – 90~100 % CAS:9003-56-9
b. Typical Stabilizer – 0~5%
c. Typical lubricants – 0~2%
d. Mineral oil – 0~4% CAS:8042-47-5
e. Tallow – 0~4% CAS:67701-27-3
f. Wax – 0~4% CAS:110-30-5
g. PC – 0~3% CAS: 111211-39-3
h. Anti Oxydant – < 2%
I think the lubricant is what helps the break last.
3D printer – In most cases, it’s a solution waiting for a problem to solve, which is THE reason I don’t own one. Oh, I’d love to own a 3D printer but every reason I’ve come up for owning one, I’ve solved with something else more efficiently!
How about for fun? It’s ok to buy stuff just for the joy of playing with new tools :)
I have plenty of tools for fun. I bough a metal lathe and end mill last year for fun, plus I’ve posted quite a few fin projects on instructables.com.
https://www.instructables.com/member/Tom%20Hargrave/instructables/
I see a 3D printer as a valuable prototyping and sometimes a valuable production tool for a very narrow list of clients.
A 3D printer is a more affordable and compact but limited alternative to a CNC machine. (Technically, a 3D printer could be considered a type of CNC machine, but that term typically refers to machines that work by cutting away at a solid block of material.)
As much as I would like a full machine shop, it’s kind of hard to find the space for it in my area without paying a fortune. A 3D printer, however, is easily at home in even a tiny apartment.
You just need to know someone with one, no need to buy one imo.
Absolutely. Featured on an episode of “tool hoarders”. :-p
My 3D printer more than paid for itself with one job, accomplishing in a couple of days what would’ve taken a week or more with conventional making of master models, silicone molds and castings.
I’ve also used it for several things for repairs and other useful items. Rather than buy a new switch cover for a paper shredder, I designed and printed a tiny rectangular tube to super glue to the upper part of the original cover, after breaking off the remains of the original plastic fingers that fit over the switch lever. Another one was designing and printing an oval plastic screw grommet for my 1982 GMC truck when I installed a new dash pad. Total time was about 30 minutes. I could’ve bought a new part for 95 cents and probably triple that for postage, and waited at least 3 days – but I needed to get the dash pad installed that day.
As a guy who owns a few printers and uses them frequently, I’d actually agree with you – most people who buy a printer have no use case for it. If you know how to use 3D design tools and you have a need for small plastic things (I do and I do), then they are super handy. If you don’t, you’re left pressing the “go” button on other people’s projects.
Buying a 3D printer without learning CAD is most of the problem here, the utility of these tools is substantially limited by one’s own design abilities.
one should add CAM profiency to the shopping list before 3D printer too :)
Why do you need CAM proficiency the slicer is the CAM processor an now it is mostly drag and drop to use those?
I just got a 3D printer, without any experience with normal CAM software, I have printed several things I designed myself with no more difficulty than stl files downloaded from the internet.
Either CAD or artistic 3D modeling tools, depending on what you want to make.
My take from this the reasons are why this was successful are because the creator has experience in regard to design, and materials selection than your average Joe or Jane who owns or has access to a decent 3D printer. The video and associated YouTube channel appear to be good learning tools. Myself I need a decent drill press and a bench belt/disk sander before I need a 3D printer.
Agreed, you want a drill press before a 3D printer. But honestly, you probably want both. :)
mostly depends on the job you are doing, plus with a 3d printer you can make a jig to convert a cordless drill into a drill press (i’d say with some rigidity downsides of course, but given how this brake die turned out, i’d be confident for it to being suitable for a basic job with good engineering and steel tubing reinforcement). but yeah i ‘d like to add a belt sander and something suitable for basic milling to my workshop.
I have a printer but no drill press, and I rarely run into an issue where I wish I had a press.
Probably if you do machine shop type tasks though instead of electronics and props and decorations you’d want a drill press though. Or a CNC.
This is being done in actual research by aviation companies already as in the auto industry. Nothing really ground breaking about it.
These kinds of comments are being done by others. Nothing really groundbreaking about this one.
A tiny bit of difference. The 3D printers used for making tools in the industry is generally of a completely different class than anything normal people have at home/workshop.
Even with optimal settings with 100% fill in a very tuned machine the characteristics of something made on a filament printer will not be that of a SLS/SLM etc. part. Layers will not be fused together completely.
Oops, meant to reply to the OP.
Should’ve submitted it to the tip line then
Great use of 3d printing, surprised it worked.