The typical machine tool you’ll find in a workshop has a base and frame made of cast iron or steel. These materials are chosen for their strength, robustness and their weight, which helps damp vibrations. However, it’s not the only way to make a machine tool. [John McNamara] has been working on a CNC mill with an epoxy base, with impressive results.
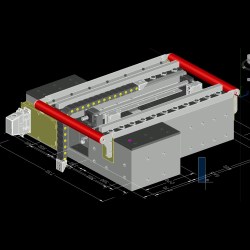
The build is one that could be readily achieved in any decently equipped makerspace. [John] used lasercut steel parts to construct the molds for the epoxy base, with some custom turned parts as well. The precision cut parts fit together with great accuracy, and with proper control of the casting process there is minimal post-processing of the final cast piece required. The mold is built with zero draft angle, and is designed to be taken apart to remove the finished pieces. By using steel, the same mold can be used many times, though [John] notes that MDF could be used for a one-off build.
The base is cast in epoxy, mixed with granite aggregate and sand to create a strong, heavy, and vibration damping material. There are also steel reinforcements cast in place consisting of threaded rods, and conduits for various electrical connections. After casting, [John] has spent much time measuring and truing up the mill to ensure the best possible results from the outset.
It’s an impressive build, that shows that building your own accurate machine tools is quite achievable with the right tools and knowledge. We’ve seen similar work before, too – epoxy really does make a great material for casting at home.
I’d like to know where people are getting epoxy. Locally, it’s crazy expensive (like $180 CAD for a half gallon). eBay and Amazon, it’s still at least $100 a gallon. Is there some secret Epoxy warehouse store that I’m not aware of?
No, I think everybody who does it splurges.
On second sought, that might be why they are often high quality: only the most motivated and prepared people do it, nobody want to waste that much money.
I can get you fantastic epoxy st $50 a gallon
where?
Please, do tell where!
Same here, I’ve been wondering this for years!
Oh yes, epoxy is ALWAYS expensive. If done right it can still be cost effective for your use case though. I know a lot of sculptors that swear by epoxy. If you really get into it though, you have to worry about bubbles, and have to deal with vacuum chambers or a vibration unit (like paint at home depot). Reynolds in Boston is a reasonable example: https://www.reynoldsam.com/product/epoxacast-650/ This is just one of the products, and $66/gallon is before shipping. So if you can find a local source it can be worth it to drive over.
The epoxy used in this project is ‘Megapoxy H’ which is about $100 for a 1gal jug, or a bit over $300 for a 5 gal pail. I estimate he used somewhere between 5-10 gallons of epoxy for the build (keep in mind that the machine is 80-90% granite so a gallon of epoxy goes a long ways) so he probably spent a bit over $500 for the epoxy. Not too bad for 500lbs of finished product!
I use MaxBond epoxy it’s about 60 USD a gallon and is in my opinion the best epoxy you can buy, they have many different formulations for different applications.
I was thinking about going with Polyester resin. Much cheaper, smells bad and some people say it’s not that stiff. But that’s what people say when they use polyester in thin layers of glass fiber sheets. I think it will hardly make any difference in such huge block of resin (or resin granite). And that brings me to another way to save money. Add rocks to resin to make polyester granite. This not only saves resin, but also increases stiffnes and vibration dampening.
Polyester isn’t suitable for this. It cures exothermic which is why it’s only used in thin layers. Beyond maybe a centimetre or so it will cure hot enough to smoke. At the thicknesses used in this mill it will warp, crack and probably catch fire. Polyeurethane is marginally better but still not suitable for casting in these thicknesses. Filler aggregates will mitigate this, but only to a degree.
If you’re trying to reduce the cost, don’t use polyester resin, use concrete.
…with these caveats:
– Pretension the concrete with threaded rod.
– Anneal the concrete, either by casting it inside rigid insulation (to retain the heat) or by heating it up after it has set.
The right contractor supply place should sell epoxy grout at least in 30-gallon buckets. I don’t know if they sell to people without sales tax IDs very often. The people doing tiling have to buy there stuff somewhere after all.
and it cost me 10 bucks for two small tubes
Now, just need an exotic hardwood slab for a live edge river pour ???? I would have just stuck with sakrete and saved the splurge for the tool head and bits.
It would be interesting to see a head to head comparison of this epoxy product to 5000psi quickrete…
As I understand concrete always fails in extension, whereas it’s crazy strong in compression. I’m sure that the epoxy would be somewhat better in extension but probably not as stiff…
I wonder how much work it would be to use beat up surface plates or even granite counter scraps. If lamination is impractical I bet using them for bulk filler would at the very least save money on epoxy.
Here is an example of building a cnc mill using surface plates – https://www.youtube.com/watch?v=ewU8zWnuE3s . The video series is really great and shows how to construct it yourself and makes it look easier than other methods.
I know it can be done, but hefting surface plates around isn’t as convenient as dumping aggregate and resin in a mold. Also shipping could quickly even things out out making it all together impractical.
What’s needed is a large scale 3D printable static mixer that can blend parts A and B of epoxy with crushed granite of mixed particle size.
I’d love to see some company buy the tooling from Intelitek for the old ProLight benchtop mill. It was the only CNC mill of that size capable of a 100 pound working load. When Intelitek bought Light Machines they didn’t build the blue machines for long, likely just until the parts inventory was depleted.
Those mills and lathes weren’t replaced with anything. In that overall size of mill there’s been nothing before or since with its load capacity. The ones with the 4 channel controller are rare, mainly due to the hideously expensive HAAS 4th axis which was really a bit oversized, it was almost as wide as the table. One source says Light Machines sold somewhere less than 50 4 axis PLM 2000 mills.
If you come across a PLM 2000 that still has its original Animatics servo controller, I have all the old software to get full access to all its capabilities. Some guy at Moog-Animatics who stayed after the merger found it on an old backup drive. One thing it can do, which Light Machines didn’t exploit, is running a headless canned cycle. Upload G-Code to the controller and it will repeat every time you hit the start button. So if you need to mill a lot of one thing, set up the code so the mill always returns to its starting position then waits for the operator to poke the button after swapping out the work. The PLM 2000 has a ‘robot’ interface for custom additional equipment to do things like loading and unloading and starting the sequence.
I have a plm 4 axis, and I need the software for it, if you’re offering…
this sounds like a plot from a neal stephenson novel. When does Alan Turing arrive
Hi All
The Epoxy (MegapoxyH) cost a little less than 400 Australian dollars. I bought a 20 Litre pail and had about 4 litres in stock so 24 litres used. (I have no connection to the company, I am just a very happy customer)
I did not vibrate the mix, I do have a small vibrator that I tried, It made little difference. The moulds are heavy 5mm .250″ steel plate that and the contents (Plus a heavy granite slab used for rail mount alignment) made Vibrating unsuitable. I also did not vacuum degas.
I guess many of us if interested in this method of construction have browsed the net and found many many thousands of posts. Endless talk of optimising the epoxy/aggregate mix, with or without exotic buckyballs, carbon fibre and many other additives. And yes if I was building a machine to be used in aerospace manufacture I would consider using them.
As you can see all the main castings are completed. To keep it simple I have used a basic mix tamped in place by hand in layers, I expected and got small blemishes when I stripped the casting from the molds, Note the use of “Contact” self adhesive plastic draw liner on all mold faces before casting, the casting does not stick to it. no other mold release was used, not a single problem stripping the molds. Note also that the molds have no welds at all, they fit together with tabs and mating holes plus threaded rod to hold them together. Each piece is just un fastened given a light tap with a rubber hammer and it pops off. This method also means that no draft is needed at all, a welded mold would have required this.
Extensive use of plain mild steel reinforcement, precision placed symmetrically around the neutral axis where possible, check the blog photos, has been used. Nothing special just 12mm about 0.5″ threaded rod, very inexpensive, get the long lengths. There will be some differential movement between the steel and the mainly stone casting, when I checked the numbers it was pretty small. Also note all the threaded inserts placed in the mold before casting no drilling and tapping later. Yes I missed one! easy to fix with a masonry drill and a little epoxy.
This machine will be accurate, In fact it will have pretty good accuracy, I am confident of this now I have been able to take initial measurements on the actual test assembled machine. The laser cut moulds are very accurate within a few thou. Being very massive I am pretty sure it will also be rigid and able to control vibration from the cutting tool and the drives.
I am really enjoying the journey building this machine, I will try to answer any questions here, and will keep posting to the blog link above, keep an eye on it it is regularly updated. The ball screws and linear rails are yet to arrive from the supplier. I am using Hiwin rails and TBI C5 ground not rolled ball screws medium preload. Not inexpensive.
Regards
John
Epoxy granite is awesome. I would like to see some projects using more affordable materials though, like maybe gold, rare earth elements or perhaps human souls.
You don’t have to start big experimenting with epoxy/granite known also known as mineral casting in Europe, here is a link to a tool and cutter grinder I built a while back, (page down to see the start and many images) it is a long article https://www.model-engineer.co.uk/forums/postings.asp?th=51617&p=2 This machine used only a litre or so of epoxy I use it every day and I get a mirror finish on the tools I sharpen on it. thanks to the vibration damping properties of epoxy granite. Apart from buying a motor and the epoxy the rest of the steel came from the scrap bin.
Hi John,
My name is Craig Smith. I’ve followed your building process for a while now, as well as all your comments on the marathon CNC Zone thread. I’m a boatbuilder and like many others have a dream of making a CNC. Composites are my business these days, so Epoxy Granit, as well as all its other advantages is right in my comfort zone.
From your writings I understand you have had great success with Megapoxy H. Never used it personal, but I’m sure it’s very good. If anyone is interested, I use epoxies all day every day. There are a ton on the market and for the most part it’s probably a mistake to say that one is better than another.
Generally speaking, each has a specific use in the market place. For instance, I think after 40 years of using it, West Epoxy 105 with either the 205 of 206 hardener is one of the best and versatile general-purpose epoxies for gluing, filling and holding stuff together, but just awful as a laminating resin, and probably not ideal to use in large quantities in an epoxy granite machine. Others are great for laminating but not flash used as fillers or glue.
Anyway, all this just to say that as an alternate source of good quality epoxy resin for us here in Oz (not sure this is available in Europe) is a product called Areldite M. It is from Meury Enterprises. Not sure where you are, but I’m down Frankston way, and Meury down here is in Mulgrave, but I know there is a branch in Sydney.
Last time I got a price for a 30kg kit it was around $466. So approx. $15.55 a mixed kg. That was a couple of years back, so probably gone up. It’s made by Huntsman these days, but was originally one of the Ciba Geigy Areldite products.
I use several different makes of epoxy resin for differing applications and like you I have no link to this particular company, they just happen to sell a good quality product, at what is in epoxy terms, a reasonable price. Like I said, not sure Huntsman in Europe stock this one, but hope this is of some use.