At any given time I’m likely to have multiple projects in-flight, by which of course I mean in various stages of neglect. My current big project is one where I finally feel like I have a chance to use some materials with real hacker street cred, like T-slot extruded aluminum profiles. We’ve all seen the stuff, the “Industrial Erector Set” as 80/20 likes to call their version of it. And we’ve all seen the cool projects made with it, from CNC machines to trade show displays, and in these pandemic times, even occasionally as sneeze guards in retail shops.
Aluminum T-slot profiles are wonderful to work with — strong, lightweight, easily connected with a wide range of fasteners, and infinitely configurable and reconfigurable as needs change. It’s not cheap by any means, but when you factor in the fabrication time saved, it may well be a net benefit to spec the stuff for a project. Still, with the projected hit to my wallet, I’ve been looking for more affordable alternatives.
My exploration led me into the bewilderingly rich world of aluminum extrusions. Even excluding mundane items like beer and soda cans, you’re probably surrounded by extruded aluminum products right now. Everything from computer heatsinks to window frames to the parts that make up screen doors are made from extruded aluminum. So how exactly is this ubiquitous stuff made?
The Die
The basic process for extruding aluminum is, outwardly, as simple to understand as the extrusion process used by a 3D-printer: heat material and force it through a die with the desired shape and size. But when PLA is replaced by giant aluminum log, and a Bowden cable and stepper motor by an enormous hydraulic ram, the details quickly cloud the simplicity of the underlying concept.
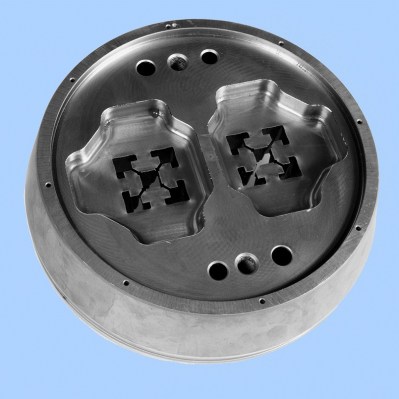
Die design is perhaps the most critical part of the extrusion process. Dies have to withstand tremendous forces at high temperatures, and must maintain their dimensional stability while doing so. Extrusion dies start life as round bars of tool steel up to a meter or more in diameter but typically around 30 cm. Dies are usually fairly thin in profile relative to their diameter, since the longer the path the aluminum takes as it passes through the die, the greater the friction it experiences. More friction means more force, which means bigger presses, more wear on the dies, and generally higher costs.
Dies are generally created by specialty manufacturers that employ skilled die design engineers and machinists. The process of turning a design into a die usually starts with roughing out the blank on a CNC lathe, then proceeds to a sequence of CNC milling operations. Electric discharge machining (EDM) is used extensively to get the fine detail needed to provide a smooth finish, and to achieve the precise geometry needed to control the flow of the aluminum through the die.
Most extrusions will have one or more hollow chambers, like the lumen of a pipe or, in the case of our 80/20 profiles, the negative space of the T-slots and the central bore. The die has to create those features, which require parts of the die to “float” in the incoming flow of softened metal. Diemakers accomplish this by suspending these features on arms that bridge the space in the upstream part of the die. The shape and surface finish of these arms has to be carefully designed so that the metal flows around them and joins together to create a smooth, continuous stream of material without voids, which could lead to weakness in the finished product.
Careful consideration of the hydrodynamic forces exerted by and upon the flowing metal are also important to die design. While the exit side of the die is pretty much exactly the size and shape of the finished extrusion, the entrance side is anything but. By some estimates, half of the energy used while extruding aluminum goes into overcoming friction between the metal and the die, so everything that can be done to reduce those forces is like money in the bank. The entrance of the die has to be designed to direct the incoming metal as smoothly and easily as possible into the final shape, which is part of the reason die designers include very generous draft angles over the width of the die.
The Squeeze
There are a number of different ways to approach the extrusion process, each with its own pros and cons. Direct extrusion is basically what you’re familiar with in 3D printing, or if you’ve ever used one of those squeezy things in a Play-Doh set: a slug of softened material is pressed against a die, which then flows through the die to assume its final shape. Indirect extrusion turns that around, forcing the die to move relative to the material. Both approaches have their pros and cons, and both result in extrusions with different metallurgical properties.
In either process, a large log of aluminum, called a billet, is heated in either a gas furnace or by induction. The temperature varies with the specific alloy and the complexity of the die, but it’s important to note that the billet is not melted, just softened. The die and much of the hydraulic press are also heated, to prevent thermal stresses from breaking anything in the machinery and to prevent the aluminum from cooling too soon and sticking to the die.
Aluminum extrusion presses generally have a horizontal orientation, with a massive hydraulic ram facing the die across a narrow gap. The preheated billet is placed into the gap, and the hydraulic ram starts to press it into the die (or, in indirect extrusion, moves the die over the material). The softened metal begins to flow into the spaces of the die, around the arms, and narrowing down into the final shape as it exits the die.
The growing extrusion exits the press and is almost immediately quenched with either air or, more commonly, a water bath. The quenching process is important, because as the extrusion exits the die it is still soft and liable to be deformed. Quenching also sets the crystal structure of the metals in the alloy, giving the finished extrusion its desired metallurgical properties.
Stretching and Aging
But even with quenching, the extrusions that come out of the die onto the long outfeed tables are far from complete. The tremendous forces exerted during extrusion coupled with the thermal stresses of quenching inevitably warps and twists the profiles. This is corrected with a stretching operation, where extrusions are literally picked up and stretched out the long way with hydraulic tools. This restores the profile to its intended shape; the few percent change in the length of the profile necessarily changes the profile dimensions slightly, a fact which has to be accounted for by the die designers.
Curiously, fresh extrusions need to be aged somewhat at elevated temperatures before reaching their final specified strength. This is accomplished in large aging towers over a period of hours to days, depending on the alloy. Aged extrusions are then cut to length, possibly have a finish applied — clear or dyed anodized finishes are very popular for 80/20 extrusions as they protect the aluminum from oxidation — and packaged for shipping.
Given the amount of material that goes into an aluminum extrusion, and the investment needed to run the massive machines that do the job, it’s easy to understand why 80/20 profiles cost what they do. So now maybe I’ll just bite the bullet and order what I need.
Featured images: F&L Industrial Solutions, Inc.
Never understood why they cost so much – apart from the die, they should cost a bit more then their weight in aluminum.
A large part of the finished cost is due to monopoly factors. Another is the production yield in % that must be reworked.
Then the die design cost and the die life. Then add the cut and trim, delivery, annealing, tempering, warehousing etc.
Even if the aluminum was free, you can see how these add up on their own, as these videos show. There are a few standard extrusions that are made by many people – these are cheaper as monopoly factors are less of a factor, and being standard sizes, each die makes very large volumes of product.
Monopoly factor??? Not hardly. I am employed as a controls engineer for one of the larger extruding companies and the field is quite competitive. We deal in the larger items, like the extrusions used for storefronts, hospitals, office buildings, etc. Scrap is a large component of the cost. Shipping, manual labor costs, anodizing, all add to the cost of the product. Extrusion, while a science, also has some black magic involved in the die designs. It is a fascinating business, and designing and maintaining the electrical controls is really …ok…fun!
I had a ton of these made nearly 10 years ago. I did the math at the time, without delivery, the ton of extruded bars cost me 32% more than raw alu was worth at that time. I think it’s really not much.
They don’t cost much at all, they are widely used and very inexpensive.
Right? and 99% of the time the ends are NOT square.
So disappointing when you spend so much and you order them to the exact length only to get them in the mail and stand them up on end side by side and they point in all different directions.
SQUARE YOUR DAM SAWS!
Maybe change vendor?
never had any that were square. set them on end and turn them 1/4 turn at a time and watch them go out of whack.
Never had that problem with 80/20. I build what I want in 3D using their AutoCAD plug-in, it spits out a full BoM, and 7 days later, I get a kit of what I drew; cut to length, drilled & tapped where necessary, with all the hardware. It’s pretty fantastic.
These are cut on the fly, just as wood is. The result is imperfect. It IS a damned shame, but that is an assembly line type, constantly moving process for you.
Extrusions are cheap. Minimum order size is the smallest billet which is about 500lbs. It’s expensive if you only want small quantities.
Huh?
These are all almost universally made from H13 tool steel- which is massively more expensive than aluminum. Occasionally they might be made of Inconel, but that’s for forging dies, I’m certain of that. I know this because I used to recently make them.
The main cost is these though is in the skilled machine time and subsequent finishing and polishing operations needed to make them. Shop cost, is billed per hour, and quoted per amount of hours, and usually starts around a minimum of 75$ per hour, and up- that figure is based on normal shop rates where I live that I know of- and it’s more I’d imagine for the die shop I worked for.
Simple dies still take more than an 8 hour shift to make, depending on how much finishing they need, and there’s multiple steps to it- premachining raw tool steel for fixturing and near final cavity size, then paying for the heat treatment to harden the dies, then final hard machining or EDM work, not to mention the extra cost of EDM time- for both machining custom electrodes to burn the final die features, and the slow pace of EDM work- and the costs really add up.
There’s a lot to making these- and I’d wager for most extrusion dies, EDM work with either wire or dies inking EDM is involved- so you are looking at the most skilled workers only running that stuff- at higher shop rates.
Many of the dies I worked on were between 10-15k$ a piece.
There is no way you get dies of any kind made cheap- unless you go to China- in which case you will almost certainly be paying twice- the second time for Americans or otherwise to fix the terrible shoddy work of Chinese die shops in this particular field.
The costs to create this stuff are quickly clear now I hope.
This isn’t normal machining- it’s some of the highest precision stuff out there. Cost follows that.
Sarcastic intent not indicated. You watched that video, and the only inputs you noticed where the aluminum and the extrusion die? Respectfully a profitable business may not be in your future. Sarcasm on my part intended.
Off topic:
A job I once applied for, produced fiberglass supports through “pulltrusion”.
I haven’t heard that term used before, or since.
https://en.wikipedia.org/wiki/Pultrusion is mostly used on extruded composites, which aren’t so common because the process doesn’t give the same strength as vacuum-bagged (and much more expensive) fabric layups, but isn’t really cheaper than metal extrusion.
Thanks Bikeperson!
This process is also used to put the PVC sheathing onto electrical wiring, the wires are pulled through the dies as the PVC is squirted out to form the sheathing around it.
I have visited two of our cable suppliers. Multiconductor cables and twisted pairs are fun to watch being made.
Commercial Diving umbilical production too.
Every fiberglass ladder starts with a Pultrusion, produced by fiberglass rovings , mat and resin pulled through a precise heated die, curing in the process. Extrusion of aluminum is a pushing process. Pultrusion is a pulling process. Both depend on precise tooling.
I was surprised how in the video, they stretched the extrusions to get them back into spec.
I was surprised that they just crushed the end of the bar, instead of using a custom clamp or something. I guess it’s cheaper to recycle the few inches of extrusion that gets crushed than to add even more custom tooling to this process.
Extrusion companies often produce to order and change dies as often as 5-20 times per 8 hr shift with often wildly different profiles being extruded.
Depending on the equipment and line setup, the material at the stretcher jaws is often the same material which must be removed as process scrap due to “transverse weld” (beyond this post to explain), so the crushed ends are not extra scrap.
Not quite the same as, “drawn,” but a sorta sister.
Fun fact! I’m the guy that created the smoothieboard stuff, and exactly at the time I started that project and joined Reprap, I was also part of the contraptor.org project, and started a metric version of it. I had nearly a ton of aluminium pressed as part of that, both punched angles ( like contraptor is based on ) and t-slot bars like this. All in 20mm dimensions and cut in many pre-defined lengths multiples of 20mm. I sold quite a bit of it over the years to random makers, but still have a few hundred kilos around in storage nowadays. Smoothie was more succesful than the open-source metric construction set, and so one project went to the side with time. Hadn’t though about this for a long time now, thanks for jogging my memories :)
Have you tried to put the remaining stock on Tindie?
The part will shrink as soon as it cools.
Most of the time, it will not shrink evenly.
The larger the cross section, the more it will shrink.
This means the the die has to be designed to compensate for the amount and direction of the shrinkage.
A new die will go back to machining multiple times as it is fine tune, especially for precision parts.
My first job out of college was working night shift in a vinyl extrusion plant (we made tracks for windows).
It was an interesting process, as there was a relationship between the screw speed (extrude) and feed rate (the “tractor”) that pulled the extrusion. You could make minor screw speed adjustments to help keep the parts in tolerance, though the fooling frame (with both air jets and water spray) would control some features, as well as overall warping.
It was as much an art as a science. Our day shift supervisor was a master at getting it setup. I was “in terror” the entire shift until 3d shift came in (their guy was also good)
Is it basically the same process for magnesium extruding?
Probably. Some types of pasta are made the same way, but without stretching or aging…
Pasta undergoes drying and boiling instead, which affects dimensions and rigidity even more so. (Also tastes better.)
Misumi extrusion is what’s up. Custom cut lengths, custom holes, custom alterations, all done by part number, no machine shop needed, and it’s cheap.
8020.net will do all that as well
Same goes for TSLOTS, only difference is Bonnell Aluminums owns TSLOTS so they are made in house.
You missed your chance to say “So now maybe I’ll just bite the billet”…
Not much changed in 3 decades since I worked in an extrusion plant for a summer job. I didn’t get exposed to many of the tech details though, so don’t expect me to consult on your garage setup with bottle jacks for extrusion rams.
Me too, although it was more like 15 years ago for me.
I did cutting and packaging and sorting kind of jobs. I visited the plant again about a year ago for some data gathering sort of stuff that i didn’t end up doing, because of other engagements, but i got a tour out of it.
There’s definitely a couple cheaper alternatives out there, and for my uses, I haven’t noticed any difference. I hate to say it, but I think 8020 is maybe 5% to 10% higher priced just for brand recognition.
I’d suggest that it’s not just for recognition. 8020 are a huge business compared to the alternatives, with by far the highest number of component designs. Their target customers are businesses and enterprises where getting it right quickly is usually more important that saving 5-10% on component costs. AutoCAD plugins cost money to develop, and the components need to closely match the models. 8020 is well-engineered, and has strong quality assurance.
Most (not all) of the competitors are basically cheap knock-off copies who only exist because they can piggyback on 8020’s success by offering “8020 compatibility”. They achieve this by copying the extrusion designs. You’ll usually struggle to find decent engineering information, and component choice will be much more limited. If that works for your purpose, great.
Sure, if you really need that one very particular profile, then 8020 has it. But, that has to be a very particular case. I haven’t experienced compatibility issues, so as knocked off as it may be, it’s far more affordable. Unless I’m pushing material limits, I wouldn’t think twice about saving the money. I’ve seen a lot of industry projects use alternatives to 8020, even in medical research.
Auto Desk is a big company, and in many situations, someone will insist on using it. That doesn’t make it the only sensible choice for everyone when freeware can do at least half as much.
I honestly haven’t had the privilege of working with a company that just doesn’t care about saving money. You can hardly assemble anything for less than $100 from t strut, 10% adds up quick. Value engineering: what benefit are you getting by paying more, and does the project require it?
That first video had ALL the buzz words.
For a Hackaday article to cover the complexity of this process this well is excellent, well done to the author.
This is what I do for a living- die and punch maker though, and not for extrusion, but for forging titanium aerospace parts.
Well, until layoffs hit me…soon.
I know someone who did pro video work. He videoed where cameras aren’t allowed. Inside then Alcoa now Arconic aluminum extrusion plant, some very high tech is used and they like to keep it in house. The videos were for job training at Alcoa and featured such topics as Dealing With Ingot Butt Cracks. Don’t let one do a raspberry on the product.
We were a high value target during the cold war, as lots of helicopter blades were produced here. Now they have the biggest lithium-aluminum alloy plant in the world. Stronger-lighter than normal alloys. Probably still are.
So how are hollow channels formed? Are there several die with different profiles stacked together with the ones towards the end smooshing it all together?
He touches on the topic of a floating die but it would be neat to see more details of how the center die is supported. I assume airfoil like shapes holding the center up in molten alum.
“and the central bore. The die has to create those features, which require parts of the die to “float” in the incoming flow of softened metal”
Yep that just about sums it up.
https://vitexextrusions.com/aluminum-extrusion-die-types/
Thanks!
For those yearning for more information, check out AEC.ORG (Aluminum Extruders Council). This is a fantastic repository of knowledge regarding aluminum extrusions.
magnesium is a bit more difficult, as it has a tendency to crack at higher strains, thus your working envelope is much much shorter with Mg than with Al. There is work underay on novel Mg alloys which use Mg-Y and Mg-Zn-Y to increase ducitility during straining processes.
The room-temperature formability limits for Al (Al-60XX) are on the order of 30% (biaxial dome-test) [1], whilst Mg is much smaller (I can’t quickly find a reference for room-temp). Of course this massively changes at higher temperatures, with Mg going out to up to 1000% [2], but you have to go hot and slow, which may damage the final product, due to internal changes in the Mg alloy itself (eg grain-growth, particle annealing etc).
[1] https://www.researchgate.net/profile/Hakan_Gueruen/publication/311510898_Forming-limit_diagrams_and_strain-rate-dependent_mechanical_properties_of_AA6019-T4_and_AA6061-T4_aluminium_sheet_materials/links/58498d2508ae5038263d86b0/Forming-limit-diagrams-and-strain-rate-dependent-mechanical-properties-of-AA6019-T4-and-AA6061-T4-aluminium-sheet-materials.pdf
[2] https://pdfs.semanticscholar.org/17d1/ba14961dcaa5a9b98e26ba6d0bbc10d6a783.pdf
https://youtu.be/Olytr4PEDPs has this entire thing in one video from manufacturer “Hydro”