[NotLikeALeafOnTheWind] has created many LED-based display projects, and shares his method for making attractive LED panel frames and mounts. At first glance it may look as though slapping a rectangle of aluminum extrusion around a display is all it takes, there is also the mounting and management of wiring, power supply, and possibly a Raspberry Pi to deal with. The process of building an attractive frame also has a few hidden gotchas that can be avoided with a bit of careful planning.
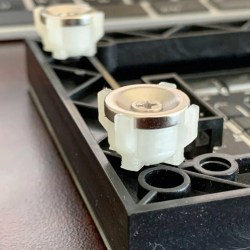
Here is one tip that will resonate with some readers: don’t rely on specified dimensions of parts; measure the actual parts yourself. There can be small differences between what a data sheet says to expect, and the dimensions of the actual part in one’s hands. It may not be much, but it can be the difference between an ideal fit, and something that looks like a bit of a hack job.
[NotLikeALeafOnTheWind] provides some basic frame layouts, and suggests using two- or three-channel extrusions to provide a flat bezel around the display edge if desired. Mounting the LED panel itself is done with magnetic feet and providing a length of steel bar to which the display can attach. This can provide a flush mount while avoiding the whole issue of screw-mounting the display panels themselves, or sliding them into channels. For mounting all the other hardware, a piece of DIN rail and some 3D-printed parts takes care of that.
The result looks slick and sturdy, and some of the tips are sure to be useful even if the whole process isn’t applied. We like the way the basic design scales and is flexible about the thickness and size of the LED panels themselves, making it a promising way to accommodate perfectly functional oddball panels that end up in the trash.
Those are nice looking frames. Though, I was hoping the article was about more than extrusion frames. I would also like to see something about regarding mitered corners which would really have to be perfect to look good.
Probably the best bit from the article is to measure the actual product you are framing. This goes well beyond framing LED arrays. Anything you buy on eBay/Amazon/Aliwhatever will have some degree of variance from the listed measurements, some pretty profound. So, the old maxim – measure twice, cut once – applies here.
Especially 16 x 2 line displays.
They all use the same generic listing picture, and what you get rarely matches the picture.
Even when ordering the same ones a month later.
I always wait until they come in and then measure the display to see if I have already made a 3d printed enclosure with the correct display opening, offset, and mount hole positions.
Just when I think I have them all covered, a slightly different one will come in. ;P
Interesting idea. A couple of suggestions: (1) Spellcheck your displays text:-) (It’s Arrival) ), (2) Consider mitred corners. If you cut the joins at 45 degrees instead of 90 degrees, I think the end result may look a bit less ‘boxy’; the L internal connectors should still fit.
^This. My other favorite way to do corners is with the corner connector cubes. They’re a bit pricey at $7-11 each and you have to tap the ends of the profiles, but they look great and have nice rounded corners that wont rip your forearm open if you accidentally graze the edge of a cute profile.
Why do you assume it was intended to be “Arrival?” Does that even fit in the space provided?
Always consider multiple possibilities before deciding a decision was merely a mistake. Often it will be an intentional decision you could have learned something from.
So… What did you learn?
Because “Arrival” is a word.
>There can be small differences between what a data sheet says to expect, and the dimensions of the actual part in one’s hands.
Do a sanity check with real parts, but keep the datasheet in mind. Dimensions in a *good* datasheet would cover the manufacturing variations/tolerances.
your screenname is very shiny