There’s an old joke about the Thermos bottle that keeps things hot and cold, so someone loaded it with soup and ice cream. That joke is a little close to home when it comes to FDM 3D printers.
You want to melt plastic, of course, or things won’t print, so you need heat. But if the plastic filament gets hot too early, it will get soft, expand, and jam. Heat crawling up the hot end like this is known as heat creep and there are a variety of ways that hot ends try to cope with the need to be hot and cold at the same time. Most hotends today are air-cooled with a small fan. But water-cooled hotends have been around for a while and are showing up more and more. Is it a gimmick? Are you using, planning to use, or have used (and abandoned) water cooling on your hot end?
Heat Break
The most common method is to use a heat-break between the heating block and the rest of the filament path. The heat-break is designed to transfer as little heat as necessary, and it usually screws into a large heat sink that has a fan running over it. What heat makes it across the break should blow away with the fan cooling.
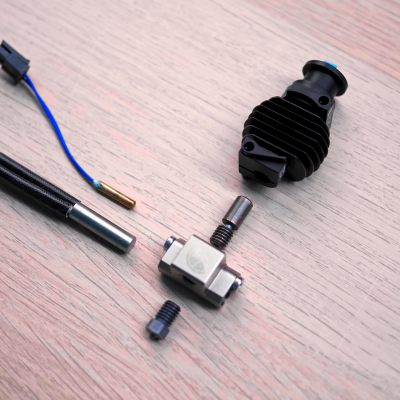
High tech solutions include making heat-breaks out of titanium or even two dissimilar metals, all with the aim of transferring less heat into the cooler part of the hot end. More modern hot ends use support structures so the heatbreak doesn’t need mechanical rigidity, and they can make very thin-walled heatbreaks that don’t transmit much heat. Surely, then, this is case closed, right? Maybe not.
While it is true that a standard heat-break and a fan can do the job for common 3D printing tasks, there can be problems. First, if you want to print fast — time is money, after all — you need more power to melt more filament per second. If a heatbreak transfers 10% of the heat, this increases demands on the upstream cooling. Some engineering materials want to print at higher temperatures, so you can have the same problem there as well. If you want to heat the entire print chamber, which can help with certain printing materials, that can also cause problems since the ambient air is now hotter. Blowing hot air around isn’t going to cool as effectively. Not to mention, fans that can operate at high temperatures are notoriously expensive.
There are other downsides to fans. Over a long print, a marginal system might eventually let enough heat creep up. Then there’s the noise of a fan blowing during operation. True, you probably have other fans and noisy parts, but it is still one more noise source. With water cooling, you can move the radiator outside a heated enclosure and use larger, slower, and quieter fans while getting more cooling right where you want it.
Water Water Everywhere: Nothing New?
High-performance computers have long relied on liquid cooling. A heat exchange block has an inlet and outlet for a liquid that absorbs heat better than air. A pump circulates the liquid and another heat exchanger allows the liquid to cool before it is pumped back to the hot part of the loop. Why not apply that to 3D printing hotends?
Why not, indeed. There are several entries in the field, going back a few years. None of these have become super popular for general use. We’ve also seen renewed interest and products lately. If you want to do it yourself, we’ve looked at a very easy way to water-cool an E3D-style hot end.
It is somewhat surprising how long ago these first started to appear. The Titan Aqua from E3D was hardly the first entry in the field and its intro video is from December 2017.
https://www.youtube.com/watch?v=Yn5wdQac7Xg
[DIY3DTECH] looked at a cheap eBay-sourced water-cooled hotend about a year later, although we didn’t find a follow-up video, so we wonder if it sat on the shelf or if it just sprung numerous leaks. Dyze Design had water cooling back in 2015. So it isn’t new, it just isn’t that widespread. At least, not today.
Modern Times
Even the newer hotends can participate. Slice Engineering has a liquid version of their Mosquito hotend. Trianglelab has the Arethusa, and there are still custom projects like the one in the video below.
Of course, adding a heat exchange block and a quantity of water can add weight to a hotend and that’s not desirable. However, in practice, the tubing and fittings don’t weigh much and there shouldn’t be that much water inside the heat block at any given time. However, if you are doing your own design, you should be mindful of adding too much weight.
The other problem you may worry about is leakage. Today, a failed extruder fan might lead to a jam. But spewing water all over your printer is probably going to be worse. You want to use connectors that are unlikely to fail. In addition, you might think about the liquid you use. Any additives or chemicals in the liquid should probably survive contact with your nozzle without disastrous effect.
As we’ve seen before, homebrewing a liquid-cooled hotend doesn’t have to be a big undertaking. Most hotends already have some heatsink so you only need to flow water over it. The video below shows a self-described “janky” method, but it proves the point: this can be a fairly simple modification to many printers. On the other end of the spectrum, the Blackbox printer uses it right out of the gate — no modification required.
Your Turn
Do you have any interest in water cooling your 3D printer? Or have you done it? How did it work for you? Let us know in the comments.
If water is too simple for you, and cooling with oil isn’t messy enough, we’ve also seen people opt for peltier devices to cool their hot ends. There are a few problems with this, though. First, they do take a lot of power. Also, while one side gets cold, the other side gets at least as hot, and that heat has to go somewhere. So now you might be back to a fan or — yep — water cooling.
Bigtreetech have also made the H2 water cooled extruder thing! – What a time to be alive
I’ve only ever done resin printing. Can someone explain why the FDM hot ends are not inductive heated with micro tubes that flow water? That just seems like the minimalist possible approach. 2 wires, 2 tubes, 1in square…
1 in cubed🙄😆
https://www.himmelwerk.com/en/applications/indirect-heating/
– 2 wires that have to be shielded otherwise they’ll radiate crap into other (unshielded) wires, wreaking havoc on the electronics
– micro tubes means delicate (read – expensive) machining
Radiate more than stepper motors? What frequency is used for inductive heating?
for something as small – 10s of kHz at minimum
What would be the benefit of inductive heating compared to resistive?
Quicker heating? I’m not sure if that’s necessary.
As for their switching frequency, 7khz to 1.2Mhz . Compared to 6khz for a stepper.
wake me then when you have an inductively heated bed.
Inductive heating only gives you a benefit if the thing you want to heat is a conductor, it then acts as a shorted one turn transformer. However if your object is not conductive you still have to heat it by contact (or radiation). Then restive is totally the way to go. Besides it’s way way easier and lots cheaper.
Anybody remember the water cooling technique from Zatsit? Though the Zatsit project kind of disappeared (I believe the guy had medical problems), there were some cool ideas there that I haven’t seen followed up on. For reference, see the second picture here: https://reprap.org/forum/read.php?152,824251
Based on the comments on his Kickstarter, he up and left without delivering.
But that NEVER happens!
Sorry, couldn’t resist.
The water cooler is just a filament guide pipe (the throat/heatbreak) poked through a hole in piece of flexible tubing. The tubing material seals around the pipe and apparently this setup provides all the contact area needed. The rest of the cooling system is just standard plastic tubing to a small water pump in a reservoir. It really seems like the most keep-it-simple approach. This video shows the assembly of the hot-end: https://v.kickstarter.com/1643867915_1a98f1157475696ca06ba08ec4fb0b1c09d10616/assets/022/179/186/0f35f4db806a769bc1b549a4396c618d_h264_base.mp4
What is the priority — being fanless, or having superior cooling above the hotbreak?
If cooling is the goal, it seems you could improve on current designs by using a heatpipe with fan – more simply.
That adds lots of volume and mass to the hot end – which probably means you loose print volume or the machine the gets bigger, and you can’t print as fast without more rigid frame, powerful steppers etc.
As you have to move the hot end around in almost all printer design keeping things small matters quite alot (and the ones that move the bed have to be huge – or at least have huge working area for the build size)..
Oh also worth pointing out that in the heated chamber situation the bigger heatpipe design will still fall into rapidly diminishing returns – build chamber air at least 60 C (seems to be about the lowest temp commonly used) so the delta between the acceptable temperature for heatbreak end of the hotend and ambient gets rather low, might even end up being negative (as in that side of the hotend may want to be colder than the heated chamber – going to be rare that you really want to print in such a hot enviroment but can’t accept a higher temp, but some wacky blended filaments perhaps could push you into that).
It removes much more heat above the hotbreak. I’ve considered a heat pipe too, but I don’t think it would work as efficiently in a heated build enclosure. PC’s want cool air around them, that’s why the heat pipe works, because there’s somewhere for that heat to go. In a heated enclosure, the heat pipe would not work as well as it does on say a processor.
I also run my cooling loop to a block I mounted to my extruder motors. Keeps them nice and cool. I’d had trouble with excess heat from the stepper motor softening some filaments, and causing failed builds.
I would like to thank you for mentioning of Alex Kenis who did a lot for the printer community and made lots of very interesting YT videoos l
Running a water cooled hemera into volcanoes. I can’t say it’s any worse that air cooled, maybe both hot ends in a heated enclosure would be too much for a fan.
FDM is already complicated enough
Recently starting converting almost all my printers to liquid cooling. What a difference it makes! I have the biqu H2o which works well. I have one printer getting the trianglelabs matrix lc. And I have a another printer with a bowen style liquid cooled volcano that I got from Amazon. I can’t wait to see the push for liquid cooling to come back. I found it interesting that it was available back in 2015 and I never became popular. The biggest plus is complete control of the ambient air movement inside a chamber, and no more heat creep!
I’ve been running watercooled hot-ends for about a year now. I love them, worth the investment. When you’re trying to print high temp materials, in a heated enclosure, I found a fan just can remove enough heat, and I was plagued with hot-end jams. I did have to switch to 24VDC for the heating elements, because it worked too well and pulled away too much heat causing the firmware to throw faults because it wasn’t heating quickly enough.
Totally worth it.
Not that I’m against using 24V, been wanting to make that upgrade for my motors for a long time now. But, couldn’t you have the water cooler pump not turn on until the hotend is approaching the target temperature? I know there’s a Marlin option for controling the fan motor that way, why not the pump motor?
I could have done that, sure. My preference was to have that cooling loop running whenever there was power to the machine, so I didn’t bother. I never wanted to deal with a hot-end jam ever again, and this would make that all but impossible. I also ran the loop to cooling blocks on my stepper motors, I’d been having trouble with excess heat softening the filament, and failing the build. Now they’re super cool no matter how long I print.
I came to find that I like running 24VDC on the heaters better than 12VDC. Heats up much much faster. I’m planning to switch my heated bed to 24VDC at some point.
Also, I’m running Klipper instead of Marlin. I like it a lot better, the config file is much easier to setup than Marlin. It’s worth it if you’re running Trinamic Stepper Drivers, Marlin doesn’t run fast enough to get the most of their drivers.
I have done that, I have a primary pump for the electronics (motors, mainboard, ect.) And then a secondary pump on a heatbed mosfet that is triggered by the “hotend fan” when the hotend turns on.
has anyone ever tried making a heatbreak out of a peltier element? In theory you apply a current and one end gets hot which adds to the heating power of the hot side while the other gets cool keeping the filament nice and chilled.
There are two basic problems with peltier coils.
The first is you need to do “something” with the heat or you risk frying the coil. This means you still need some sort of heatsink and fan/pump to cool the hot side of the coil.
The second problem is humidity. Peltier coils aren’t sensitive to it but they will collect air humidity as condensation and can even freeze the condensation making ice blocks on the coil.
I’ve had my printer water cooled for about 3+ years now on the hot end. I use a printed water jacket around a custom machined heatsink I machined from a large m6 aluminum standoff. I’m on the 3rd generation of the system and it works really well so far. Doing everything from ABS to Polycarbonate in a heated enclosure printer. Aiming to go hotter with everything but it’s very much a custom system for my own personal needs.
Me too :-)
After some Iterations I’ve made a cooling element from brass foil leading into a custom HE with two heating cartridges, 100W@24V, faaast. But: there have to be a Heatbreak to prevent clogging bc of my lightweight direct extruder. Your HE is a combined cooling/heating element? Can You provide a picture?
best regards
I converted my D5s to water cooling a while back. Just replaced the heatsinks with a block of aluminium and some 4mm copper pipe. Works a treat. I’ve linked my YouTube video below.
Definitely helped for printing ABS in a warm enclosure…
https://youtu.be/zAQjekM1TrM
I use an Ord Rova printer. Dual extruder, water cooled. I use it mostly for abs, asa and nylon. A little cumbersome to rework the hot ends, but works well. No longer available though. A little ahead of it,s time perhaps.