Imagine the scene: You’re puttering along in your vehicle when, at least an hour from the nearest help, one of your tires starts losing air. Not to worry! You’ve got a spare tire along with the tools and knowhow to change it. And if that fails, you can call roadside assistance. But what if your car isn’t a car, has metal wheels for which no spares are available, and the nearest help is 200 million miles away? You just might be a Jet Propulsion Laboratory Engineer on the Curiosity Mars Rover mission, who in 2017 was charged with creating a new driving algorithm designed to extend the life of the wheels.
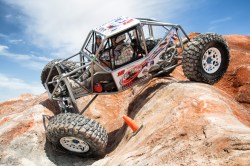
You could say that the Curiosity Mars rover is the ultimate off-road vehicle, and as such it has to deal with conditions that are in some ways not that different from some locations here on Earth. Earth bound rock crawlers use long travel suspensions, specialized drivetrains, and locking differentials to keep the tires on the ground and prevent a loss of traction.
On Mars, sand and rocks dominate the landscape, and a rover must navigate around the worst of it. It’s inevitable that, just like a terrestrial off-roader, the Mars rovers will spin a tire now and then when a wheel loses traction. The Mars rovers also have a specialized drivetrain and long travel suspensions. They don’t employ differentials, though, so how are they to prevent a loss of traction and the damaging wheel spin that ensues? This where the aforementioned traction control algorithm comes in.
By controlling the rotation of the wheels with less traction, they can still contribute to the motion of the vehicle while avoiding rock rash. Be sure to check out the excellent article at JPL’s website for a full explanation of their methodology and the added benefits of uploading new traction control algorithms from 200 million miles away! No doubt the Perseverance Mars rover has also benefited from this research.
But why should NASA get to have all the fun? You can join them by 3d printing your own Mars rover and just maybe some Power Wheels derived traction control. What fun!
Not a lot of info on the actual algorithm. This is the whole thing.
“The traction control algorithm uses real-time data to adjust each wheel’s speed, reducing pressure from the rocks. The software measures changes to the suspension system to figure out the contact points of each wheel. Then, it calculates the correct speed to avoid slippage, improving the rover’s traction.”
ABS?
I went looking for more information on the current state of the wheels, and found this detailed analysis:
https://www.planetary.org/articles/08190630-curiosity-wheel-damage
Thank you.
Thanks for posting this. The original article was pretty light in details. It seems the problem is related to higher than expected contact forces on the wheel, partially due unexpected rock features and also the geometry of the suspension. In addition they were driving all the wheels at the exact same velocity, like a spool. Which does increase the forces experienced at the contact point.
So the analogy of “spinning a tire” isn’t really accurate. Instead they need to allow the wheels to move at different rates in certain conditions. The articles don’t make it clear exactly how they are doing this.
Personally if faced with the same problem I would try to emulate the action of an oldschool automatic-unlocking differential. All you need to know is the drive current and displacement for each wheel and the algorithm is pretty simple from there.
Excellent article, thanks for sharing.
“They don’t employ differentials, though, so how are they to prevent a loss of traction”
Not employing differentials *is* a great way to prevent traction loss, at least on loose ground….
Agreed! But not having a differential means there’s no opportunity for a limited slip diff or a diff locker. Hence the need for some other kind of traction control :)
I ain’t no rocket scientist but I would think the wheels should be tough enough to drive over rocks
They are- it’s when they spin on sharp rocks that damage is done. Preventing them from spinning when they’ve lost traction (the traction control being discussed) has extended their life by preventing as much damage as possible.
It’s a trade-off. Tough wheels means less weight for experiments. So they erred on the side of experiments. To my eye what they did badly was to make wheels with sharp inside corners on the ribs which raise the stress levels and cause cracking. They also had those ribs suddenly end in the thin sheet, creating a piercing feature very much like the way a can opener works (the punch kind) Too bad they didn’t call me first /s
He’s not a rocket scientist here, he’s a rock scientist.
That rover has travelled about 14 miles at pretty low speed and weights about 750 lbs on Mars. Seems like a bit of a fail that the wheels are breaking like that. After all, they did know there were rocks on Mars right? I know weight and materials are an issue in that environment but still seems like someone could do better than that.