OpenSCAD has a lot of fans around these parts — if you’re unaware, it’s essentially a code-based way of designing 3D models. Instead of drawing them up in a CAD program, one writes a script that defines the required geometry. All that is made a little easier with the Belfry OpenSCAD Library (BOSL2).
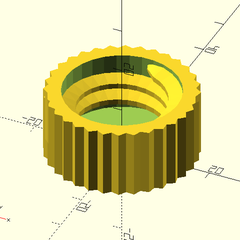
BOSL2 has an extensive library of base shapes, advanced functions for manipulating models, and some really nifty tools for creating attachment points on parts and aligning components with one another. If that sounds handy for designing useful objects, you’re in for even more of a treat when you see their functions for gears, hinges, screws, and more.
There’s even one that covers bottle necks and caps. (Those are all standardized by the way, so it’s never been easier to interface to existing bottles or caps in a project.)
OpenSCAD really is very versatile software. It powers useful tools like this screw, washer, and nut generator as well as having more unusual applications like a procedural terrain generator. It’s free, so if you’ve never looked into it, check it out!