Electrospinning is a fascinating process where a high voltage potential is applied between a conductive emitter nozzle and a collector screen. A polymer solution is then slowly dispensed from the nozzle. The repulsion of negative charges in the solution forces fine fibers emanate from the liquid. Those fibers are then rapidly accelerated towards the collector screen by the electric field while being stretched and thinned down to a few hundred nanometers in diameter. The large surface area of the fine fibers lets them dry during their flight towards the collector screen, where they build up to a fine, fabric-like material. We’ve noticed that electrospinning is hoped to enable fully automated manufacturing of wearable textiles in the future.
[Douglas Miller] already has experience cooking up small batches of microscopic fibers. He’s already made carbon nanotubes in his microwave. The next step is turning those nanotubes into materials and fabrics in a low-cost, open source electrospinning machine, his entry for the Hackaday Prize.
As always in fundamental research projects, a whole lot of parameters have to be tuned just right. To speed up the process of finding suitable values for the electric potential, dosing feed rate, emitter to collector plate distance, temperature, and humidity, [Douglas] build his machine with a CNC controlled vertical axis and syringe pump, that can dispense even the smallest amounts of a given solutions accurately. Temperature and humidity control will be added as the project progresses. A host software and GUI allows for easy control of all parameters and will also save and recall presets for different spinning solutions once everything has been dialed in. [Douglas] already ran a few tests, spraying saline solution from an old 3D printer nozzle, and we can soon expect first tests with polymer solutions from the better-suited syringe nozzles he installed.
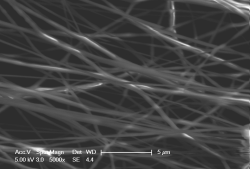
To keep the build affordable and easy to reproduce for other makers, [Douglas] uses available materials and came up with a few design tricks that could also be applied to other projects. The belt-driven vertical axis is based on PVC pipes, on which a 3D-printed bushing block slides up and down, adjusting the distance between the nozzle and the collector plate. An acrylic door with a safety switch prevents the polymer spray from escaping from the spinning chamber. In the heart of the machine sits an Arduino Uno with a gShield, controlling the stepper motors and talking to the host computer. The 3D-printed syringe pump, a custom design, swings out from the side of the machine to allow for easy refilling. Submerged in mineral oil, which may have been chosen to reduce the risk of overheating and arcing, lies a half-wave series voltage multiplier, cranking up the voltage from an AC power supply to a maximum of 30 kV DC.
I’ve never read about this before! Sounds like an advanced cotton candy machine.
I would not want to be in charge of quality control; too many variables.
Wow, awesome concept! Can’t wait to see how this evolves.
Well, you are correct, there ARE a lot of variables involved. Material being used, ratio of polymer to solvent, voltage, distance between emitter and collector, temperature, humidity and extrusion rate being some of them. That’s the challenge, to make a machine as cheap as possible that will allow anyone to reproduce results time and time again. I think I’m off to a good start. :)
apparently, upon reading on wikipedia, PLA is one of the materials that can be electrospun by melting it, instead of using a solvent that goes away through evaporation.
why haven’t I thought of this before?
That’s the reaction I’m looking for! If I can get others to go look it up, read all about it, and then take it in even more directions, I’d love it.
‘why haven’t I thought of this before?’
If I had a dime for every time I’ve said that I’d be pretty well off.
My friends startup does this: http://www.electroloom.com/