Last week, we had a look at a carbon-infused PETG filament. This week, I’d like to show you two composites based on a more common thermoplastic in 3D printing: ABS. Among a whole lot of other engineering plastics, the french company Nanovia manufactures Kevlar-like aramid-fiber-infused and carbon-fiber-infused ABS 3D printing filaments. These materials promise tougher parts with less warping while being just as easy to print as regular ABS. Let’s check them out!
Lucky enough to obtain a huge pack of samples from Nanovia’s endless list of highly exotic filaments (Thanks Jacques!), I was able to run a few test prints on the carbon-fiber-infused ABS and on two colors of aramid-fiber-infused filaments. These filaments come with detailed datasheets, including exact printing parameters, which makes using them a great experience — toss the values from the sheet into your slicer and get great results right away.
Aramid Fiber ABS
The exact fiber content of this material seems to be a proprietary trade secret, but I was told it’s above 5%. According to the data sheet, one gram of the filament contains 5 million tiny aramid fibers with a diameter of about 10 µm and a mean length of 215 µm – so basically it’s dust. Taking the composite’s density of 1.08 g/cm3 into account, a bit of math and educated guessing lead me to believe that the volume-specific fiber content must be in the range of 9 % (13 % by mass). That’s a fair amount that should have a noticeable effect on the material’s properties.
Plain ABS is already valued for its toughness, but — in 3D printing — also known for its tendency to warp. Its high thermal expansion coefficient of about 70 µm/(m K) is to blame. Aramids have a slightly negative thermal expansion coefficient in the range of -2.5 µm/(m K), which helps to prevent warping issues when printing aramid fiber compounds. In contrast to carbon fibers, aramid fibers act as a thermal insulator. They also are not harmfully abrasive, making this material a great alternative for printers that cannot be equipped with a hardened steel nozzle.
Print Quality
To get an all-round impression of a material’s surface-finish, overhang- and bridging capabilities, printing a Benchy is the way to go. I printed one for each color at 255 °C with 0.2 mm layer height, and it turned out beautifully, as you can see below:
Basically, the aramid fiber ABS prints just like regular ABS. The bridges and overhangs at the Benchy’s cabin-windows worked well, so did the overhangs at the bow. All details came out nicely, and the interesting semi-matte surface finish of the uncolored, naturally yellow aramid blend is not as rough as one might expect from a fiber infused material. In the darker aramid blend, the fibrous nature of the material become more visible:
Carbon Fiber ABS
From the notes in the data sheet I conclude a volume-specific fiber content of 5 % (10 % by mass) for this filament. Just like the aramid fibers, carbon fibers lower the thermal expansion coefficient of the composite, making this a low-warp material. Carbon fibers are very abrasive, so a hardened steel nozzle is recommended when printing carbon fiber composites. Even though this filament is supposedly antistatic, it’s worth mentioning that this material is not conductive enough to print electronics. It does, however, conduct heat.
Print quality
The carbon fiber ABS also had to undergo the same Benchy-test at 255 °C and 0.2 mm layer height, with almost identical, perfect results to its aramid infused siblings. The surface finish is slightly more rough than the aramid filament but very consistent.
Resilience
While both the aramid and carbon fiber filaments produce noticeably stiffer parts than plain ABS, they are also noticeably more flexible than parts from the PETG based XT-CF20 I tested last week. Looking at the data sheet, none of their properties particularly stands out from the crowd – on first glance.
Nanovia Aramid Fiber ABS |
Nanovia Carbon Fiber ABS |
ColorFabb XT-CF20 PETG |
plain ABS (typical) |
|
---|---|---|---|---|
Flexural Modulus ISO 178 / ASTM D790 |
2.3 GPa printed specimen |
2.7 GPa printed specimen |
6.2 GPa molded specimen |
1.9 – 2.3 GPa molded specimen |
Tensile Modulus ISO 527 / ASTM D638 |
2.4 GPa printed specimen |
2.7 GPa printed specimen |
N/A | 1.9 – 2.5 GPa molded specimen |
Elongation At Break ISO 527 / ASTM D638 |
7.5 % printed specimen |
10 % printed specimen |
7.5 % molded specimen |
8 – 9 % molded specimen |
Glass Transition Temp. | 101 °C (213.8 °F) |
101 °C (213.8 °F) |
80 °C (176 °F) |
<105 °C (221 °F) |
On a second look (and a few emails), it’s due diligence for a manufacturer of engineering plastics for 3D printing to not only test their materials through merciless, standardized test procedures — but also actually run those tests with 3D printed specimen.
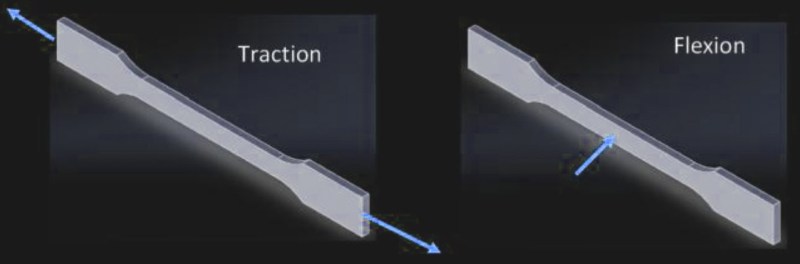
Nanovia happens to do this, and there’s a whole lot of information on how these tests are conducted in their paper on the impact of carbon fiber in 3D printed materials. The paper suggests a 35 % increase of the tensile modulus over non-infused filaments, and either way, it’s good to know the properties of the material once it’s out of the nozzle.
However, since most filament manufacturers simply copy the test values for their technical data sheets from their resin suppliers (which, of course, use injection molded specimen), it’s hard to independently compare these values to a stereotypical, non-infused filament.
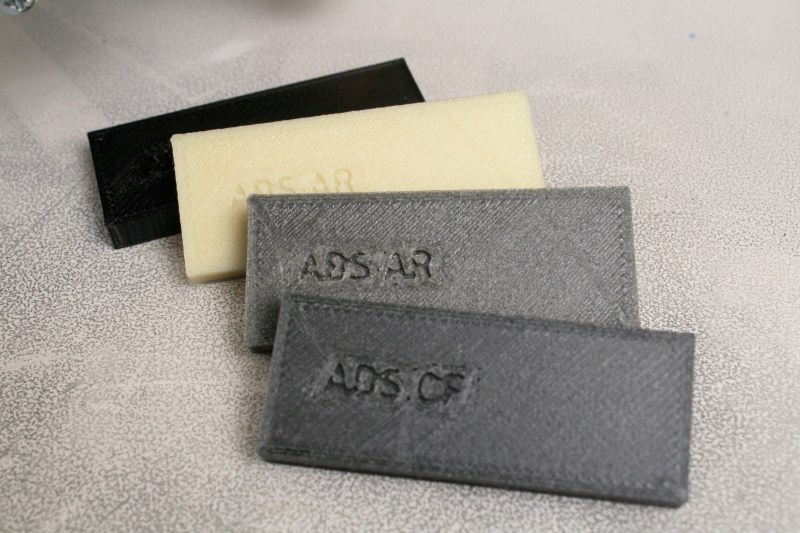
Breaking stuff is the ISO 527 of the common man, and so I printed a few test blocks just to break them into half. The results are shown below, and at least give you an idea of how the fiber content modifies the material’s behavior under stress. The little testing bricks were printed at 70 mm/s and 270 °C and bent to a 90° angle by meticulous professionals using a lab-grade vice and a standardized lot of force.
While regular ABS clearly shows how the fracture rips the joints between the tool-paths apart, the fractures in the infused materials happen distinctively more uniform, indicating proper bonding between the laid down strands of material. Also, a large stress whitening zone suggests that the composite materials distributes stress more effectively across the entire block. Below you can see the cross-section of the fracture. I’ll be happy to hear your additions to these conclusions in the comments — and feel free to debunk them entirely.
Conclusion
I like these filaments. Both materials come with a great, compromise-free print quality and produce tough parts even at the upper-end of their print speed recommendation: blazing 70 mm/s. Since I only had about 20 grams of each filament from the sample pack, I could not experiment much and had to rely entirely on the printing parameters from the data sheet. I was not disappointed and the demo prints shown in this article came out great in the first instance. A complete data sheet with well-tuned printing parameters and actual, 3D-printing-relevant mechanical properties is certainly something I’d wish to see with more filaments out there.
In terms of resilience, neither material’s datasheet blows your socks off with unrealistic values from injection-molded test specimens, but they are exceptionally tough. A major benefit of the fiber content is the composites’ reduced tendency to warp, allowing you to print larger structures with higher shape fidelity. This is something to consider, if you — like me — love working with ABS, but sometimes run into applications where even the slightest warping is intolerable. Or if you — like the Oak Ridge National Laboratory — set out to print the world’s largest solid 3D printed object to date, which is also printed from carbon-fiber-infused ABS. I’d put this material into the category of productive work: it’s a tough material that simply delivers great results at a reasonable throughput.
I hope you enjoyed taking a look at another special filament. There are a whole lot more in the box, like PTFE, glass-fiber infused filaments and others, so stay tuned for my further 3D printing adventures. Got a melting-hot tip on a great filament or experiences with your favorite (or most hated) filament to share? Put them right there in the comments!
Test conditions
Printer: Prusa i3 Einstein Rework (Proosha IIIo , photo) Hotend: E3Dv6 w/ 0.4 mm hardened steel nozzle, E3D PT100 thermocouple kit, narrowly ducted, axial nozzle fan, super-power-bestowing jolly wrencher fan guard Drive System: GT-2 belt drive with 20T pulleys for XY, M5 threaded rod for Z w/ cardan coupling, 0.9° 1.7 A Wantai stepper motors, DRV8825 Stepper Drivers in 8x microstepping mode for XY, IGUS RJ4JP-01-08 dry lubrication bushings on XY, LM8LUU linear bearings for Z Electronics: Ramps 1.4, Arduino Mega 2560, 12 V / 500 W ATX power supply Build plate: Makertum MK1 500W AC heated bed, Vishay NTCLE203E3 thermistor, PEI printing plate clamped on top, capacitive distance switch for auto bed leveling Firmware: Marlin-RC7
How would they turn out with some acetone treatment?
Aramid Fiber ABS …. MUST HAVE!!!
Where can I get some to play with?
BTW: nice review Moritz
Thanks! If you’re in the US, you should be able to get it directly from them. In Europe, some of their filaments are actually available on amazon.
I looked, but I was unable to find any store link. Is it one of those things where you have to ask for a quote? If so, they probably don’t want to talk to someone as poor as me.
http://nanovia-technologies.com
great write up.
I am absolutely fascinated by the various choices you printer’ers have now!
A decade ago there were only a dozen simple filaments and now it has become like a supermarket. Someday I’ll purchase a FDM. :)
Cool ! More !
Print a bulletproof vest?
No no no!
The interweaving of the Kevlar and multiple layers is the most important thing.
Then again, make anything thick enough and it will eventually become ‘puncture resistant’.
Didn’t work. Much blood. Kevlar my ass. False advertising.
Certainly won’t be bullet proof. All these carbon fiber or carbon infused filaments are just using carbon cloth that has been ground up mixed into melted plastic. Actual carbon fiber is a woven fiber mat, it gets it rigidity from the resin. Same deal with kevlar. The fibers have high tensile strength.
I honestly don’t know if this is more useful than pure plastic. In this particular instance, the plastic is the glue holding together a big brick of shredded carbon fiber. There might be some form of interlocking action happening at the micron level, and the plastic is just providing the backbone to hold the carbon in a suitable shape. This also might explain the slight increase in rigidness. Ultimately, the parts might be a *little* bit stronger. It’s essentially the same properties as high temperature resistance PLA.
Another good write up. Could you include cost as a category in the article? It’s great to know what the benefit of a reinforced polymer is over plain abs, it would be even better to know what we have to pay for the privilege.
On a related note, it would be really interesting to violate a cheap and an expensive version of a Stargate filament such as a basic abs or pla. We know that better quality filaments are more consistent in diameter but I would be interested to know if they also have better mechanical properties.
Compare! Not violate. Dyac!
Oh dear. I think I need to surrender my keyboard licence. that should be standard, not Stargate!
and I’d been looking for that Stargate filament for sometime now :(
“Engaging bed plate.”
“Bed plate engaged.”
“Engaging hot end.”
“Hot end LOCKED!”
*prints for only 38 minutes and then shuts down*
:D
With the canceling of the series, the supply of Naquadah has dried up, so there’s not going to be any Naquadah infused filament. ;)
I’m interested in the filaments (and thus their cost) as well. These might be nice filaments, but if the cost of the material is too high, there’s next to no point in using them for prints that don’t absolutely require these filaments.
makershop.fr seems to sell the nanovia filaments, so I looked at some of their prices:
Carbon Fibre ABS: EUR 58.00/500g spool (= EUR 116.00/kg)
Aramide ABS: EUR 39.30/500g spool (= EUR 78.60/kg)
Carbon Fibre and Aramide ABS: EUR 61.90/500g spool (= EUR 123.80/kg)
ABS (plain): EUR 45.30/500g spool (= EUR 90.60/kg)
PLA (plain): EUR 47.00/500g spool (= EUR 94.00/kg)
As nice as these materials may be, I think they are far too pricey. I’m not sure why they are so expensive, though. It’s a real shame, because they seem to provide sensible datasheets and all, but I don’t think many people are willing to pay such a premium. I certainly wouldn’t buy these filaments on a whim, but use them as a last resort, when everything else fails.
Margin my friend ;) You can contact directly Nanovia if you are a professional.
An exemple for PETG Carbon 1.75 mm :
Makershop 500gr = 62,90€
http://www.makershop.fr/filament-expert/765-petg-carbone.html
Imprimante3dfrance 1000gr = 77,40 €
http://www.imprimante3dfrance.com/en/filaments/petg-175mm/nanovia-carbon-fibers-petg-1-75mm-detail.html
Thanks for the suggestion. I’ve been thinking about this and decided against it for several reasons. I’m afraid it would not yield much useful information for a particular reader, since prices vary from seller to seller, from region to region, and they change a lot with time. I’ll reconsider this if more requests like yours pop up!
You must have quite a collection of benchy’s by now. (c:
Yupp.
Anyone who prints 1000 Benchy’s will be granted one wish by the gods.
It’s actually 1024, and you can choose between world peace and a list of kickstarter campaigns that won’t fail. The list is a total ripoff.
I’m going to have to see results on a machine without the jolly wrencher fan guard.
Lol, variables! ;)
sounds like a super effective way to inhale carbon fibers
The carbon and / or aramid fibers are too long and specially compounded to not be inhaled, except in case of sanding of course…
But if you only printed small parts how do you know it doesn’t warp with longer print? I hope this press lately on all thees “carbon fiber” filament is true.
Several industrial customers printed parts 1m40 wide for automotive application with laser dimensionnal control and validation at the end of the process. This is the reason why this aramide material is widely used in industry.
it would be cool to have some comparisons of common filaments, as well as some “bottom of the barrel” filaments, just to see what a good and a bad filament looks like. love these thorough articles!
Here’s a good one.
http://hackaday.com/2016/08/13/a-trove-of-3d-printer-filament-test-data/
Boo. You raise a good point in the difference between 3d printed and resin strength specifications, print out nice test blocks, and then break them by hand?
Why did you not measure the tensile and other strengths for yourself?
Boo! Good comment, but the tone! I hear you. Of course, we need real ISO/ASTM standardized testing in the long run.
The data mentionned on the TDS are ISO 527-2 no tape tests.
Needs to build or find a surplus IZOD impact tester.
One question flying around in my head for a while:
How does Filament (especially PLA) perform over long time?
I have some big spools of old PLA laying around (>3 years) and am currently not able to print them properly. I have tried drying them, because they weren’t stored in an air tight container, but that didn’t help.
Any experience in filament aging?
For the US: you can contact directly contact@nanovia.pro. We can arrange some shipment if needed awaiting a local distribution network. Best regards
Jacques
Would you be willing to share the make and model of printer you used as well? Perhaps the mileage, (read hours of operation), on it too?
Dear Jeff, I’ve got pictures of printed tools but I will share only with customers authorization (automotive and aerospace production tools) so not at the moment, sorry for this. I can share some data concerning these printed pieces with over 13 customers feedback. Printing times between 50 and 350 hours depending the size. average 160 hours. Parts weight average: 7 kg. max: 14 kg. Max size: 1m40 x 95cm x 47 cm. For thermoforming applications: average target=50 thermoformed parts with ABS aramide molds, max up to date: over 200 thermoformed parts. On standard printers, for other customer (ultimaker) 250 pieces per production (small parts around 10x5x5 cm) 17 x250 pieces delivered at the moment over 11 months.
Standard industrial spool ordered by industry: 2.2 kg spools (both in 1.75 & 2.85mm). J.
Had the opurtunity to print in carbon fiber (40%) ABS couple months ago, for a project for Red Hot Chilli Peppers :)
the print is veeery durable, if you print it… the printer jams every couple hours and when printing something for over 14 hours it was impossible to finish the project :/