If you are an electronic engineer or received an education in electronics that went beyond the very basics, there is a good chance that you will be familiar with the Fairchild μA723. This chip designed by the legendary Bob Widlar and released in 1967 is a kit-of-parts for building all sorts of voltage regulators. Aside from being a very useful device, it may owe some of its long life to appearing as a teaching example in Paul Horowitz and Winfield Hill’s seminal text, The Art Of Electronics. It’s a favourite chip of mine, and I have written about it extensively both on these pages and elsewhere.
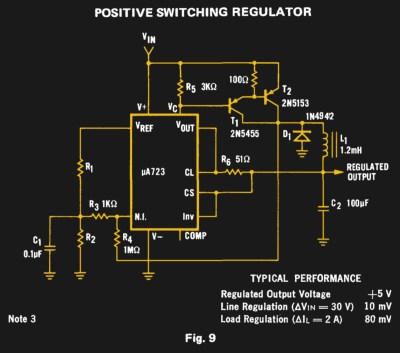
For all my experimenting with a μA723 over the decades there is one intriguing circuit on its data sheet that I have never had the opportunity to build. Figure 9 on the original Fairchild data sheet is a switching regulator, a buck converter using a pair of PNP transistors along with the diode and inductor you would expect. Its performance will almost certainly be eclipsed by a multitude of more recent dedicated converter chips, but it remains the one μA723 circuit I have never built. Clearly something must be done to rectify this situation.
Looking at the circuit and referring to the data sheet, it becomes obvious that the μA723 is configured as an oscillator through the feedback provided by the 1 MΩ resistor R4. Extra loop gain is provided by the combination of the PNP Darlington pair of external transistors and the μA723’s internal output transistor, and pulse-width modulation is achieved through the internal comparator seeing the output voltage on its inverting input in comparison to the reference voltage derived through R1 and R2. The resulting oscillation switches the current into the network composed of D1, L1, and C2, forming a textbook buck converter.
Dusting Off an Old Circuit Design
Fifty years has passed since that data sheet was published, and in that time the electronics industry has moved on to the extent that many of today’s components would be unrecognisable to an engineer from the 1960s. The resistors and capacitors perform the same function, but the μA723 is a rare survivor in semiconductor catalogues while the two transistors and the diode have passed into history. Meanwhile there are a plethora of ready-wound inductors to replace the suggested hand-wound one in the original.
To build a μA723 switcher for 2018 then it is necessary to perform a few searches for modern equivalents to the 1967 parts. For the semiconductors, this means taking a look at the data sheets for the originals, and matching modern parts with similar gain, current handling, power dissipation, and speed. I settled upon the 2N4403 as a replacement for the 2N5545 and an MPS751 as a 2N5153 equivalent, though since transistors have improved so much in five decades I could have picked from many others. You’d expect the diode to be a fast rectifier, and I settled upon a 1N4837. The most recent Texas Instruments datasheet has an unexpected choice though in a 1N4005 general purpose rectifier, so perhaps speed isn’t as critical after all. There are multiple manufacturers of inductors suitable for small buck converters, the Taiyo Yuden part I selected is simply one of many.
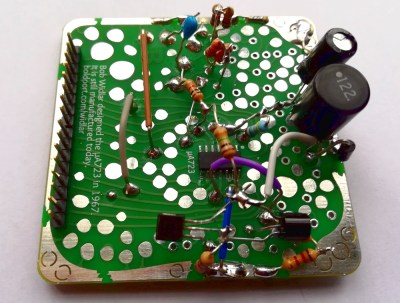
Building the circuit took advantage of a recent Boldport Club project, a μA723 dev board and Widlar tribute. Regular Hackaday readers will know Boldport’s Saar Drimer for his distinctive artistic PCB design, and the Widlar project is typical of his aesthetic. The switcher takes it slightly off-piste, but the board has been designed to accommodate any circuit. Time for a bit of responsible disclosure: it’s a board I’m intimately familiar with because Saar asked me to write its instructions when he designed it a few months ago.
My take on prototype construction is a little rough-and-ready, and I apologise if it offends your delicate electronic sensibilities. A mixture of through-hole and pads on the board to support a piecemeal spider-web of components, it’s not exactly pretty. It places the voltage reference divider R1/R2 and associated components to the left of the μA723, the inductor and diode above it, and the two transistors to its right. The divider is chosen for a 5 V output, and the 1 MΩ feedback resistor loops in an ungainly manner over the top of the chip.
Success, Partially
Astoundingly, my μA723 switcher build worked on first switch-on, rewarding me with a 5.01 V DC output into a 50 Ω load from my 12 V input. Connecting up the oscilloscope though revealed another side to this regulator though, and demonstrated why you might rarely see a μA723 in this configuration.

The yellow trace in the screenshot to the right shows the ripple on the DC output, while the blue trace shows the waveform on the transistor collectors. The circuit is oscillating at just over 100 kHz, higher than might be expected until it is realised that the whole thing is a free-running with a frequency dictated only by the characteristics of its loop rather than being derived from a separate oscillator as might be the case in a more recent design.
The 260 mV peak-to-peak ripple on the DC output is the killer with this circuit, an unacceptably high figure for all but the most undemanding of applications. It provides an object lesson in how more recent devices with significant thought put into how they handle their PWM generation have improved performance in this respect. I’d urge anyone with an interest in this topic to read some of the Linear Technology application notes written by Jim Williams, particularly AN35 and AN29. Despite the free-running μA723’s rather basic PWM generation, it is easily possible to see the duty cycle change with the conditions. Dropping the input voltage to just before it starts to lose regulation at a rather high value of about 9 V, the duty cycle increases from 50% to about 70%.
So the μA723 is no star as a switching regulator, which is hardly surprising. There is another feature of the circuit that makes it entirely unsuitable for a modern environment, being a somewhat powerful 100 kHz source it produces a significant quantity of RF radiation. An AM radio anywhere within range is wiped out as soon as it is powered up, reminiscent of the effect of some older CRT TV sets. It’s extremely unlikely that this would make it through an EMC test.
This has been an interesting foray into switching regulator construction and a chance to fill that last gap in the μA723 data sheet. It’s a design that works, but one has the sense that it made it to the data sheet because the chip had the capability rather than because it was a sensible choice even by the standards of 1967. One wonders whether this is a hardware hack from Bob Widlar, pushing the chip beyond its design, one that has survived beyond expectation in every μA723 data sheet since. If that is the case then I metaphorically take off my hat to him, it’s a circuit I wouldn’t have had the chutzpah to publish had I been the sheet’s author.
“off-piste”
something I had to Ggggle as I had never encountered it before,
it is not similar to, or opposite of, pisted-off.
B^)
So Jenny, do you feel the Boldport Club is a worthwhile membership?
Holy cow, that was my big takeaway from this too. Expensive, but really pretty! I’d consider investing for my kid.
Amazing kits, as you’d expect. But not cheap, you get what you pay for. I would say if you are flush with cash then do it.
Did you try bigger caps or another inductor to smooth the output?
At least a sime try or 2 to show the futility (if so,) would have been the icing, but, a good cake. Thx.
Substituting parts to improve the linearity of the output is left as an exercise for the student.
B^)
Same question here.
No. The purpose was to build the data sheet circuit. But yes, something could surely be done.
And, just because it’s the fundamental reason for switchmode, what was the efficiency? Better than linear?
Yes, I’d be interested in the efficiency. Also, 12V in, 5V out, 50% duty cycle???
Yeah I caught that too. I would be interested to know what is up as well. I can’t say that I have used one of these that I remember (I’m old lol). Interesting read though. I may have to do some poking around the internet tonight.
The Darlington would drop about 1.4V, and with a small resistive drop in the inductor this adds up to about 50% duty cycle.
The ripple would seem to be caused by insufficient output capacitance and especially high ESR; is the cap an low-ESR type, suitable for switchmode converters? After all, it’s 100kHz and 50%, and it doesn’t matter how you got there, the frequency, duty cycle, and inductor value determine the ripple current, which together with the properties of the output capacitor determines the ripple voltage.
I powered my first computer (Z-80 CPU and a 5″ TV, in 1978) with a motorcycle battery, regulated down to 5V using the switching regular circuit provided in the 7805 application notes. It was similar to this, but I think it used just a PNP transistor rather than a darlington pair. It worked first try, and gave me about 75% efficiency, which isn’t great, but a lot better than the 40% a linear regulator would have given.
I never actually used it to the point where the battery ran down, so I don’t know what the battery life was; the main reason for this power source was that I didn’t have any mass storage, so loading a program involved loading a small boot program from toggle switches, which then allowed entering the (octal) main program using the keyboard and monitor. Turning the computer off lost everything, so the battery was there more as a UPS, and a way of transporting the computer from home to work and back without losing what I was working on.
Sime > simple. I kintbtipe… esp of these keyless nanokybds.
But I have an interest in regulators, and working on a shunt regulator for old tiny 6v motorcycles, which cannot afford the typical (or ANY) overhead. Even non-shunts help to keep my rusty gears, lubed. ;>)
I thought you were abbreviating “simulate”
B^)
Yeah, it led me to online etymology dictionary. It must be the Winter Olympics bug. Slalom, was next. I remember the 723, I was glad when 3 terminal regulators came out.
The 723 WAS a 3-terminal regulator. The only advantage the 78xx regulators had was that the voltage divider that determined the output voltage was internal, saving two resistors.
And how much current is the 723 good for without an external pass transistor?
It is a flexible IC, but it mostly needs those extra parts, which is why it gets complicated.
Three terminal regulators were introduced as “on board regulators”, I can’t remember what National called them. But only needing one or two capacitors, you could put the regulators near specific circuits, rather than on massive regulator in the power supply. It was distributing the regulating, distribute the heat if nothing else.
It was a big shift for hobbyists. No more fussing with zener diodes and dropping resistors, no fusing at all. Pick a voltage, and you had it. I thought it was a 5V regulator first, certainly I heard about the 309 first, but soon there was a wide range of voltages, which got bigger with time. I’ve seen some odd voltages, not sure if they were “standard” or custom, but generally you could get what you needed. No need for the external parts, for a lot of hobby use you didn’t need more than 1A.
The first regulated supply I built did use a 723 and I can’t remember why. The three terminal regulators had to be out by then. Eventually that 723 did change to a 7812.
Michael
Yep – my mistake. I was conflating the 723 with the LM317, which is the 3-terminal I think you’re talking about. Yeah, I guess that was a big improvement.
“Your scientists were so preoccupied with whether or not they could, they didn’t stop to think if they should.”
Sure, you can make a 723, or 317, oscillate and regulate, but that doesn’t mean it’s a good idea — even the crusty MC34063 at least has current limiting!
If you’re adding transistors, you can do better with a 555. I’m not aware of anyone else who’s drawn up a current mode 555 circuit, so enjoy: https://www.seventransistorlabs.com/Images/555%20Boost.pdf
Similar ideas could be applied here of course, but then you end up with something that’s really not much better than, say, stepping back and doing it all with transistors (which I’ve also done — fun for a project, not at all practical, just tedious).
Or, you could use a microcontroller to sense the output voltage and drive the darlington pair. Arduino FTW!
It requires a fair bit of head scratching to do the software part, 20MHz clock speed is woefully too low for a stable feedback loop to keep up at any reasonable switching frequencies…
Let’s see: for a 100 kHz switcher and a 20 MHz clock, there are 200 clocks per switching period. Seems like there ought to be enough cycles there to decide when to turn the switch on and off. If you use an AVR (since I mentioned Arduino), you can use a PWM output and an ADC input. The pulse width is set according to a basic PID algorithm, based on the difference between the measured voltage and the target voltage. The output capacitor is made large enough that under worst case loads (maximum and zero), the supply doesn’t change faster than the ADC can keep track of it.
This isn’t much different from how you might do it with a 555.
Just kidding about the darlington pair, btw. Obviously everything’s better with MOSFETs.
I did once a 555 flyback converter with both voltage regulation and switching current limiter. It was meant to power nixie tubes at steady 80-150V, and I was actually stunned it worked at all…
It’s likely that the EMI arises from the construction method, there’s a lot of stray inductance and capacitance in all those traces and leads, as well as some considerable radiation area. State of the art switcher design relies heavily on surface mount components and use of copper planes to reduce parasitic effects. Output ripple may be due to construction practices, output cap ESR, DCR of the inductor, or a combination. Or, just using a 40 year old part that, as Jenny points out, wasn’t exactly designed for the application. ;)
Yep, I’d expect the EMI is a function of construction layout (and inductor type), plus the radiation from the power supply leads (notice no capacitor from Vin to ground, so those leads to the battery/power source had better be short). The choice of 100kHz might be something to change, but basically: the major factors determining the ripple, efficiency and radiation are not coming from the 723 circuit – it is supplying a reasonably standard PWM square wave, as any regulator – modern or otherwise – would have to do; it is up to those components around the chip – the PNP transistors (or P-Ch MOSFET or whatever you might use) plus the inductor and capacitor and board layout… I’d suspect modern chips with exactly those external components would do as badly (except in drop-out voltage, perhaps, but that’s mainly because the 723 wants a supply significantly higher than it’s 7.1V output reference supply circuit… a 12V output version would do better, and a change from the Darlington PNP circuit to a single modern PNP or a MOSFET could do even better still, although substituting a MOSFET would involve changes to the circuit around CL/CS/VOUT and possibly some fanciness in the gate circuit to speed up the switching times without forcing R5 to be too low).
Overall, I think the 723 is still a good chip for all sorts of modern designs so long as the supply voltage isn’t under 9v, even for switchmode applications… but this particular switchmode circuit isn’t great – partly because it doesn’t make use of good components that weren’t available back then, but also because it seems to be designed to cope with a wide range of high input voltages (hence the constant-current supply into T1’s base, plus the Darlington configuration to reduce power dissipation in the IC that might occur only when the supply is high – the 723’s output transistor could drive T2 directly otherwise).. In general, if you try to make a circuit flexible (in terms of input voltage, for instance) you get a performance that is a bit worse than one designed specifically for a narrower range of conditions.
Back in the 1970s DEC used the 723 as the main control element of switchmode power supplies. However it was used in a circuit that was considerably more complex than the datasheet example circuit.
Likewise Data General. It was used in a couple of fairly heavy-duty PSUs and used to confuse the heck out of people when they saw the number on the top of the chip.
Just curious: did you try the circuit as shown in the TI datasheet? The Darlington 2N5455/2N5153 section replaced by a 2N5005 and the feedback via a segregated 2N5153 path?
NOTE that the July 1999 TI datasheet, page 9, Figure 9: has a MISTAKE in what looks like “segragated feedback”… the collector of the 2N5153 must be connected to the collector of the 2N5005 and the top if the inductor; the original Fairchild circuit was drawn with something I don’t like – a 4-way junction of lines – the blob/dot was missed out by the people drawing the TI version (as can happen – I always recommend drawing two sets of 3-way connections, otherwise it can look like 2 wires crossing without being connected).
> Clearly something must be done to rectify this situation.
Heh. Nice one.
(Alright, it probably wasn’t intentional because there’s no rectification involved here but when talking about power management, well, I laughed anyway)
Damn, you beat me to it…
I agree with Ward. I think the author’s assessment of the 723 was overly harsh. I don’t think it’s fair to blame the chip for all the circuit’s shortcomings.
I see thin, high inductance traces on the PC board, they need to be much heavier. The high switching currents cause ground currents that interfere. Put some 10 uF low ESR MLCCs on input and output. And the worst thing is using a Darlington pair for switching. Use just the MPS751.
Is the 723 usually a linear regulator? In that case, is it being used here for more than just, say, the job of a transistor? For a chip whose purpose is not to oscillate or vary it’s output at all, that’s pretty clever making a switcher.
That said that board would qualify as “art”. In the sense of it’s massive lack of function, seeming pointlessness, and being done purely for the sake of it. Is there a reason it’s… like that?
If you want to have some real fun, try hacking an AT/ATX supply. Many of them are built around the TL494, and there are schematics out there. I once converted one to a 250W 13.8V supply for a mobile 50 MHz transceiver. They seem to be fairly versatile and are pretty easy to hack into a nice bench supply, since you end up removing lots of the components,since you’re going from a multi-output to a single output supply.
And the raw materials (an old supply) are pretty much free.