The last time we discussed machine tools, we talked about how to choose the size of the new metalworking lathe that your wallet is itching to pour itself into. The next big decision to make is “new or used?” If you’re in North America, this question has a lot of overlap with the classic question “Import or American?”. The answer boils down to what your needs are, and what you want to get out of this machine.
If you are new to machining, and want to learn the skills, I recommend starting with an Asian import machine. If you’re careful which one you select, you’ll end up with a very reasonably priced lathe that can do precise work right out of the crate. If your interest is in learning how these tools work, and in doing a restoration project, an old American machine is a great choice. Let’s look at these two routes in more detail.
Navigating the World of Asian Import Tools
Buying an Asian import can be challenging, because there are a lot of choices. To complicate matters, there are a lot of local-to-you resellers who import these machines, fix them up (or not), repaint them (or not), and resell them. Sometimes you get technical support and an English manual in the bargain, sometimes you don’t.
It’s tempting to look at machines from Little Machine Shop, Harbor Freight, or Grizzly, see that they all look identical, assume therefore that they come from the same factory in China, and are thus equivalent in all but price. Don’t make that mistake! These resellers often have a deal with the factory to build their machines differently (better bearings, different bed treatments, etc), and some resellers refine the machines themselves after import. Research is key here.
You really do get what you pay for. If an identical-seeming machine is priced $400 higher at Precision Mathews over Grizzly, it may be because they upgraded the bearings or include a higher quality chuck. Contact the resellers, research online, and know what you’re paying for.
Consider the Timeline for Outgrowing Your First Lathe
That said, the average quality level of these machines is now good enough that if you’re just starting out, you’ll learn a lot and can do good work on any of them. Buying higher quality up front will help you take longer to grow out of the machine, so spend as much as you can afford. The more skilled you get, the more you can get out of a good machine (and the more you can still manage with a bad one).
Machinist snobs still refer to these imports as “casting kits”. The joke being they need so much fixing up to be good that they’re useless except as a bucket of lathe-shaped cast iron bits that you can use to make a lathe. That may have been true back in the aughts when this consumer machine tool wave started, but it’s definitely no longer the case (much).
“Old Iron” or New Production
Now let’s talk American. There’s little debate that the machines built in the 20th century by Americans (and also Germans, Swiss, Brits, and others) are top quality. These machines were not built to a budget price point like the consumer grade Asian machines of today are. They were built to last a lifetime with a company depending on them to do real production work, and were priced accordingly.
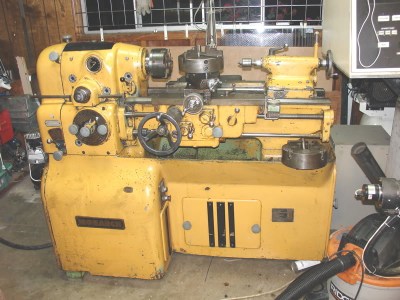
Nowadays, since the production in these countries has gone CNC, the old manual machines can be had for very little money. They are often in very good shape, since the initial quality was so high. The number one thing to look for in an old lathe is bed (aka “ways”) wear and damage, especially near the chuck. You can learn to work around worn areas, but it’s arguably unrepairable. If the ways are good, everything else is fixable (depending on your willingness to do restoration work). It can be challenging to find a ready-to-run vintage machine at a good price, though, so the Old Iron route is best if you’re looking for a project.
Note that restoring an old lathe also often requires access to a lathe, because you may need to make shafts, bearings, bushings, etc. It’s also worth noting that the Old Iron is usually big and heavy. Really Big. And Really Heavy. Before buying that beautiful Monarch 10EE, ask yourself, “Self, do I have the means to move and service a 3300lbs beast of glorious burden for the rest of my natural life?”. Moving one of these machines without a forklift and a loading dock can be a multi-day project, and you need to know what you’re getting in to. It can be done- people have moved them down narrow basement stairs, but research the techniques involved to see if you’re up for it.
In some parts of the world, Asian import will be your only choice, because the Grand Old Ladies of the 20th century are basically impossible to ship outside their country of origin for any kind of price that would be worthwhile. They will forever remain in their country of birth. If you’re based somewhere like Australia, Japan, or South America, look for local resellers who can take the guesswork and risk out of buying directly from the Chinese and Taiwanese factories.
Only Spend Half Your Budget
I’ll leave you with a final thought to burn deep into your psyche. Only spend half your budget on the lathe itself. You will spend that amount or more on tooling. Experienced machinists always say this, and new machinists never believe it. It is true. You will be amazed at all the tool bits, tool holders, drills, chucks, indicators, micrometers, files, stones, grinders, reamers, scales, squares, blocks, gages, calipers, etc that you will need, and how quickly you will need them. Also don’t underestimate the cost of stock. When learning, you want to use high quality free-machining steels, aluminums, and brasses; not scrap Mystery Metal™ you found behind the dumpster at Arby’s. Quality stock can be quite expensive, but it’s very helpful when learning and will help you do quality work, so don’t forget about it.
There are lots more considerations around specific lathe features that will determine the right machine for you, but we’ll get into that next time!
That last paragraph is really key, certainly the machine will be a significant part of the budget, but all the tooling, cutters and other stuff will cost as much or more.
hoping for a comprehensive article on this soon
Its surprising how much can be achieved without a fortune in tooling. All of the machine shops i’ve been in and grew up around have a fraction of the fancy guides & tooling even “amateur” machinist channels like “this old tony” have. Of course this is offset by experience and training, its different when you live it 40+ hours a week. Most of them are running Taiwanese machines these days (at least in AUS), they just dont expect them to last as long or do sub 1 thou precision on long lengths.
It’s true if you have only a single budget to spend on tools. If you have a budget to spend now, and a trickle of budget to spend later, spend it on a good machine, and maybe a QCTP. A lathe doesn’t need much more to run for basic projects, and you’ll be much happier a year or two later when you’ve finally built up your collection of tooling and still don’t hate your machine.
Agree. A QCTP is really, really useful for the time it saves in switching toolbits and not having to readjust to centre height each time. They are far better than a four-way toolpost, which in turn is miles ahead of the lantern toolpost. For some reason I can’t fathom a lot of US-made lathes have lantern tooposts. Dreadful things (by comparison) they are, if you’ve had to use them. Change it out for a QCTP and you’ll be a lot happier. I have a QCTP on my Myford ML7 and also one I share between my Unimat 3 and Taig Micro Lathe II.
Also, get a set of carbide toolholders that use the replaceable triangular and diamond-shaped bits. Even on a tiny lathe like the Unimat they make a BIG difference. Wish I had got onto them decades ago.
I started machining in 1979 in school, 1981 in real life, so that’s what, about 150 years ago. Right at the time when carbide started getting fairly popular, but cemented inserts, not indexable inserts. These days, young guys can’t deal with grinding a HSS or carbide tool by hand, but I’m still doing it, those old HSS and cemented tools ain’t dead yet, I get very good results working in a tooling shop.
I was going to comment on the qtcp being needed early on, for years I had a selection of tooling that I just kept with their packing shims elastic banded to them in the box, so I could put them back in with the right shims immediately. Shim stock is cheap, and so are elastic bands. Couple this with a 4 way toolpost, and you have something workable. I’d use a boat style toolpost as a flotation test device straight away though.
Really I’d invest as much in the lathe itself and worry about a toolpost later. I’ve changed my toolpost about 4 times already over the years (currently I am using a multifix b, but making new/custom toolholders for it is a bit of a chore) and two of them were different style qtcp’s :-)
A knockoff AXA is like $100 with enough holders to get you started. It doesn’t add much to the cost of the machine, and they’re really convenient. I was just suggesting that instead of trying to buy all the tooling you think you’ll need when you buy the lathe, that you should just get the best lathe you can afford. Tooling can come later, as long as you’ve got a few basic cutters.
What do you mean by “boat style tool post”? Gggle images only confused me by the wide variety of images it produced.
I think he means lantern style. The rocker device that supports the tool holder looks like a little boat.
George is correct. See Wolf’s photo further down. It refers to the half-moon rocker piece the toobit holder rests on. Best try not think about it, just think “I want a quick-change!” instead.
Agreed. Also to add in; be sure if you are buying a new machine to ask the seller if there are any boxes of tooling that go with the machine. Often you can get them to throw that in for free and you can get extra chucks, holders, steady rest etc for free or cheap.
Also become friends with local manufacturers. Some will sell cut-offs for cheap, and even if you don’t know what the stock is; it is uniform in composition and you might be able to get it in quantity.
By new I mean new to you :).
My kingdom for an edit button………
Quinn is writing a series on starting out machining over on Blondihacks.
She covers some of these areas pretty well and offers some real-life advice and examples of buying and setting up a new machine.
I would spend all on the machine and build up tooling over time, inexperienced users may buy tooling they use very little, machining takes time to learn so best not rush things.
“the painful tail of transporting old iron”
I was thinking “tale” would be the proper word to use here,
but then again, it may have been a pain in the butt!
and never forget that lathe are high perched iron thing, prone to tumble when mishandled.
Altogether too true. I recently sold a beautiful 1936 13″ South Bend in amazing shape. Or thought I had until the buyer let it tumble off the trailer as it was being loaded. It went from a beautiful vintage machine to scrap in seconds.
AAAAAAAaaaaaaarrrrrggh!!! thinks I, …and undoubtably exclaimed by you and the other fellow simultaneously.
Depends who was holding the cash.
+1 a lot of metalworking tools match this description
Nah, it was not bad.
Last time I moved, I paid a rigger to move the lathe. It is 1800 pounds. It took me 3 evenings of hard work to get it off the trailer and in place in my garage with an engine lift, hydraulic jack and some lumber. It took the rigger 15 minutes to get the fork lift in and have the lathe on the trailer. It was worth the money. The rest of the shop was manageable. with the engine lift and a pallet jack.
My dad recently passed away and left me his old Atlas.
How did you located a “rigger” to do the work? What price range should I expect?
I belong to a metalworking club in Phoenix, AZ. There was a guy that had equipment and moved stuff for several club members. In 2010, the guy charged me $600 to load the machine, drive it 120 miles and unload it in the new house. He supplied the truck and forklift. The club connection was a good one.
Atlas? no need for a rigger for anything Atlas badged. They were lightweight machines, and movable by two reasonably healthy people. Minimal disassembly might be needed, such as removal of the tailstock and motor on a lathe, and separating the way frame from the chip pan and legs or bench.
Expect to need to realign the machine when it is in the new location anyway, so there is no loss to breaking it into several parts for the move. I have done this several times with m Atlas lathe, as well as a midsize shaper and other machines. This pretty much is the case up through the mid sized south bend class machine.
A heavier machine, like a LeBlond, larger Hardinge, or Pacemaker, really needs to be moved as a unit and may need a rigger. A 48″ Harrington is a true pro job.
“When learning, you want to use high quality free-machining steels, aluminums, and brasses; not scrap Mystery Metal™ you found behind the dumpster at Arby’s.”
Even though I haven’t machined metal, I can easily believe this, I once spent a good part of a day trying to drill several holes in recycled “box” steel, wearing and breaking a number of drill bits. There is no telling what is in that stuff, but I encountered something really hard to drill.
I just bought few cheap cobalt drill bits in the sizes I use the most, and had no problems with drilling metal…
Yeah, one of my cow-orkers finished that job with a single decent drill bit (cobalt? titanium?)
I have some pieces of metal that are almost impossible to process with my limited equipment. Have destroyed some quality inserts trying to work with it :/
It’s some strange titanium alloy.
It could also be air-hardening tool steel. I’ve bought some of that as scrap, and even carbide has a really tough time with it because my lathe isn’t powerful enough to cut through the full depth of the work-hardened layer.
Depends on your bits too– I got lucky and my local CARQUEST carries some badass bits (Consolidated Toledo Drill, American made too!) for about $100 for a set up to 1/2″ set, and I even used these things to drill through broken taps and bolt extractors– though, a dremel tool is nice to have for re-sharpening them manually, they may last you a lifetime if you use them at appropriate speeds. Mystery metal or not (long as it aint titanium!).
“drill through broken taps” ?
I’m listening!
http://www.ctddrill.com/
We use Tap Magic extra thick for titanium, works great, keeps the tooling sharp longer.
Also Tap Magic for mild steel.
“Only spend half your budget on the lathe itself. ”
I found that out when I bought a used wood lathe…
Tools, replacement tool rest, chucks, apron, face shield…
“BUYING MACHINE TOOLS: FOREIGN OR DOMESTIC, NEW OR USED?”
Paper or plastic? :-D
If they accept a credit card, plastic; otherwise it is paper, cash or check.
B^)
Check local auctions… The heavy stuff typically does not sell for much.
I got mine for a few hundred, with all the tooling:
http://www.wolftronix.com/lathe/images/P9090028.jpg
I have a workbench like that, only I used cross bracing on the back and 2x8s for the table top.
Nice catch, BTW!
Nice lathe, but if it sits on the bench, it isn’t the heavy stuff. Atlas’ tend to be low in many places, but step up to a Logan or South Bend, and the price jumps. Atlas’ are quite serviceable, but lack rigidity, and often are worn to the point of needing major work.
That said, one of my machines is a low hundred $US Atlas. (TV36). Also a TV48 for parts (the ways were beyond help when I bought it for scrap price for the taper attachment and spare parts). I have considered upgrading to something with a QC gearcase, but I grew up on large machines with change gears (48″X20ft was a fun one), so it isn’t a big deal. The bird in the hand, so to speak.
I upgraded from one of those not that long ago… See if you can find the Atlas version of “How to run a lathe,” if I’m remembering it correctly, it calls for installing that machine on something with a laminated 2×4 (the 3.5″ thick top way to laminate) with threaded rods through it at a specific interval to be sturdy enough to the keep the ways straight. Don’t forget to level it with shims under the cast bed feet to keep the bed straight the entire distance or you’ll turn a taper. Good luck and happy turning!
I built the SO a table for the kitchen like that, with 2×4’s on end and threaded rods. Worked well. We have a bridge next to our house and it is built out of what look like 2×8 or 2×10 laminated together like that. It is blacktopped on the top so you would never know it, but if you look at it from the bottom you can clearly see the wooden construction. That’s where I got the idea in fact.
Your bench looks nice, but I seriously recommend a few triangles in that.
As the owner of the 10ee above it has been worth every penny spent and all the time involved in going to get it and going through it. I have used everything to cheap Chinese 7x12s and 9×20 (which are and will always be boat anchors) to very large lathes. The 10ee is a wonderful machine.
One of the advantages of buying used American (or domestic) is you often get a ton of extras with the lathe. Mine came with 3, 4, and 6 jaw, face plate, 5c collet nose, steady and follow rests, taper attach, live centers, etc. just add some carbide holders and you are up and running.
I think the only reason I could see not to buy used domestic machines would be size, weight and power requirements. I find that even a slightly worn domestic lathe will outperform the new Chinese lathe on day one. Most people don’t realize that in the machine world heavy is an advantage not a disadvantage. In reality there is not too much difference in what you need to move a 1000 lb machine or a 5000 lb machine. By the way, the 10EE you have is beautiful but I also think it might not be a great first lathe unless it is in great condition or you love complex projects. As you know the 10EE has a pretty complex drive system that can get into lots of bucks to restore and there are lots of 10EE lathes that have had their drive replaced (some are great replacements and other methods can lose a lot of the low speed capabilities of the machine).
Getting a 2.5 ton machine home may be a challenge.
It’s very straightforward to rent a truck, a trailer, a hoist and even the big burly dudes to do the heavy lifting, the biggest challenge is finding the phone book. If you are splashing out on a big machine tool then you should go the extra mile and get real movers to move it for you, the lathe will be no fun if you mess up your back or drop the chuck on your foot. The challenges are building up the floor so it doesn’t collapse under the weight of the lathe and all your other goodies, and setting up the electricity so you don’t blow the main breaker if you try to start the lathe motor while the dryer and the stove are on.
Yep, here are a few options. Hire a real rigger to move it. If you want to go a bit cheaper and can get the machine up on skates, you can often get a flatbed wrecker to handle the load for you. If you want to go really DIY look up a drop bed trailer (the bed drops straight down flat on the pavement and then picks the whole bed up so no ramps). Two men and a truck is a cheap option as long as you can provide skates or jacks as necessary. They come with the muscle a trunk and standard tie downs. 5,000 is well within the capabilities of a lot of moving methods. You can get equipment to help you from industrial rental places like Sunbelt who also rents drop bed trailers.
If your going to use that large of a machine, get a trailer that can hold it and a vehicle that can tow it. It will either be useful moving the things you make, be generally useful, or you could use it to make a pound or 2 on Saturdays and such. Citydwellers I pity you
Wouldn’t the best reason be that you don’t have adequate knowledge to determine if the machine is in serviceable condition?
Best option is look in your local area for someone doing piece work machining out of their garage. It is usually an old guy that wont mind you stopping by to make small talk about machines and he may even be happy to either tell you what your looking for or go check it out with you.
Is anyone familiar with the Sherline tools? Wondering how they compare… certainly pricier than a Grizzly, but they have kits to turn their lathes into CNC that seem appealing. If you can work under the limited size, anyway.
We used to have a Sherline mill were I used to work, and a Bridgeport…
The Sherline was small and cheap, but it was used for little stuff.
Sherlines are tiny machines. We used them for making armature parts for puppets at Laika. Same with taig. They are decent machine. Just freeking tiny.
Taig makes lots of the lathes from Harbor Freight, LMS and others. They kind of run between Sherline and full size lathes. The small lathes are really good if you do lots of small stuff like clocks and such. The Sherlines are very high quality in the small size machines. Taig not so much, they range from total garbage Harbor Freight to more tricked out but still low end Precision Matthews and LMS.
You are thinking of Sieg, they are the OEM for a lot of Chinese lathes.
Taigs are different, they are small machines made in the USA: http://www.taigtools.com
Anybody’s got experience with Taig lathes or just Taig tools in general? How’s their product quality and post-sale support?
You are correct, I mis-spoke. It is in fact Seig that makes the cheap Chinese imports. They do also seem to be capable of making pretty good stuff when you are willing to pay for it as well.
I am a big enthusiast of tiny lathes like the Unimat, Taig and Sherline as absolutely incredibly underrated machine tools and capable of more than you’d think. Their shortcomings are abviously the limited size of job and they have much lower power motors, coupled with the reduced overall rigidity you will need to learn to take more and lighter cuts.
If you’ve got that time, they are great. You can pick up the baseboard it’s bolted to (always put them on a base board) and turn them upside down to shake the swarf off, then put it in the cupboard.
My favourite is the Unimat 3, had mine for about 37 years now. It’s little, but a quality machine. The Taig is not as good (no fine longitudinal feed carriage or tailstock) but a lot cheaper. I’ve never used a Sherline, even though they originated in Australia as the Clisby lathe, of which I have seen some for sale here.
There is a benchtop metal(?) lathe at the local Horror Fright.
The amount of play in the cranks sends a shiver up my spine!
Those really are the lowest of the low imports. The same basic models are available with better quality controls and features from LMS, Grizzly and such. All really come from the same sources like she said but HF is really the worst that I have seen,
What, 1/8 of a turn of backlash is bad? The HF machine tools are best considered kits. It takes some doing, but basically you pull them all the way apart, clean out ALL of the swarf left from manufacturing, then rebuild them from there.
Lucky me, I’ve got a super cute Unimat SL-1000 so I can just walk by the Central Machine 7×10 on the way to the clamps section.
Cleaning up a HF machine doesn’t change the fact that you still have a HF machine though.
Yeah, you can only do so much before you are replacing major components. If you replace say the tool holder (junk), the gears (plastic), the motor (weak), the speed control (notorious for giving up the magic smoke), the lead screws and nuts (cheesy v thread forms), the chuck (which has a ton of runout), the included tooling (which can barely open the cardboard box they came in), the paint (which will probably already be removing itself), and finish that machining you can have a pretty good Harbor Freight lathe. This is oft repeated cliche advice but really buy the best you can afford even if you have to wait awhile. The good stuff will last more than your lifetime.
I started in 98 with a 7×10 mini lathe and I still use it today. However, I eventually bought a South Bend 9×48 and then a South Bend heavy 10. While I like my larger South Bends I still use my mini lathe.
For a beginner I always recommend a new small Asian lathe, they are easier to move, run off of 110 volts and are well supported in social media. The biggest issue is quality and capacity. These lathes are well documented and you can research which machines are better. However, capacity is capacity and sometimes small lathes just can’t do it.
When buying a large used lathe it is not easy to move them, they normally run off of 220 of 3 phase, they have to be leveled and there is always some wear in them. It is hard to help someone when they are have issues when there machine is half worn out and not leveled. I was glad that I spent a couple of years on a smaller lathe before I bought a bigger one.
Here is a engine I built with a 7×10 and a mini-mill, https://youtu.be/UC1_RxI1b9c
I understand what you are saying but having learned on South Bends and having run everything from LeBlond, Monarch, Clausing, Lodge and Shipley, and new CNC stuff, I can tell you that for sure the most difficult machines I have used are the small underpowered Chinesium lathes. The bigger equipment is way more forgiving if your feed rates or tooling are not quite right. I would recommend that if you have to stay small, 110 volts, and easy to move I would rather go real small and get a Sherline. If you insisted on going Chinese lathe I would at least get an LMS, Precision Matthew, or a Grizzly to get at least a little quality control
This article could be improved with specific details.
Rather that *repeating* vague urban legends and internet myths, why not supply an actual list of each name brand and *specifically* which bearing upgrades, or modifications have been applied.
Otherwise you’re just repeating crap.
How about checking the Internet and check out the zillions of comparisons that are already out there? I think her article was good solid advice from someone looking to get into a lathe. I am a machinist and think that is all about right. I did not see any urban legends of myths. The machines do vary and if you Google around for about five minutes you will know what the differences are.
How about supplying some links with reliable info? For every random article I’ve found, there is another that refutes the results or with the opposite info.
Try Youtube and decide for yourself who you believe. If I sent you links then you would be assuming I know what I am doing. You could also try the numerous machine shop forums and look in there. The one thing she was absolutely correct on was that when buying machinery new, more expensive almost always equates to a better machine. I have been a machinist for a long time and cannot tell you what to buy because I dont know what you are going to make. You have to know how big, how small, what materials you want, and how precise they have to be. If you are turning candle sticks for gifts you can go cheaper, if you are turning turbine engine parts or watch parts you need better more expensive hardware. If you watch and read enough you can figure out who knows what they are doing by the work they are turning out.
That’s why it’s left up to the reader to do the research: any information or comparison that’s published could be out of date by the time they hit “publish.”
Good used? Most old US iron is worn to uselessness in my experience, that’s why I chuckle at folks who say they pick this stuff up in scrap yards. Usually looks like a lathe shaped lump of flaking rust. I think cleaning and painting junk is a hobby to some, but my hobby is making parts on machine tools, not rebuilding scrap iron.
Its out there it is just a matter of separating appearance from function. I know what will clean up easy and what is a deal killer. Believe it,,,a lot of good stuff goes to scrap yards only because it is too much effort to sell and there is just not a high demand for the stuff. I see it both ways. I love the new Haas and DMG Mori stuff I have gotten to use and my dad has an old Lodge and Shipley monster that is super fun and does great quality work too. Realistically most people are never going to recover their investment in machinery, this is a hobby and if you take satisfaction in resurrecting old machinery and then using it, it perfectly valid. You will also know what makes that old machine good, bad, or otherwise.
You may know. Assuming every one else does is going to far.
Chinese machines are a known factor as long as some higher-end branded variants are used. They have less mass and less finish than a big professional machine but they are known to work. Old hardware can be a bargain or it may be a money sinkhole.
Note I don’t think the least expensive Chinese lathes are a known factor. Some have won the lottery and got a very good machine while some other have something where parts barely fit together.
Exactly. I recently picked up a used knee mill and have been looking for a lathe. The thing with old iron is that it’s in one of three conditions:
1. Great shape stored in someone’s basement. Amazing find!
2. Sitting in someone’s back yard / unheated garage / barn / scrap yard and is covered in rust. Restorable but it’s going to take a fair amount of elbow grease
3. Being sold by a shop/garage, appears to be in good condition. But it’s been beat on for 30 years of daily use in a real shop, meaning the machine is pretty clapped out. Ways need rescraping, feed screws have tons of backlash, etc etc. There’s a reason manual shops sell manual machines… they are worn out.
Scenario #2 and #3 are far more likely than #1. I checked out multiple version of #2 and passed because it was too much work for me. I almost bought a #3 style mill from a shop, but after playing with it for a bit it became clear why the shop was selling. Only after looking for a few months did I find a #1 scenario, and even then the mill needed a good amount of restoration, repainting and rebuilding the spindle.
Old iron is great if you can find a great deal… but a lot of it is literally just old, rusting iron.
The hard part is that newbies often don’t know this and buy up a clapped out piece of old domestic iron, because of the constant preaching online. They they get home with a disappointing machine that probably performs worse than a cheaper/lighter import machine.
I agree. That was my experience. I bought a ’60’s vintage US lathe based on that advice that turned out to be a $1200 paperweight because the ways and carriage were worn out. I didn’t realize it was worn out until after I spent several years finding small odds and ends of parts it needed. I’m sure it was a nice machine in its day, but to have the bed and carriage reground would have been cost prohibitive. I could have bought a new chinese machine machine that worked right out of the box for not much more, and been learning how to machine instead of looking for parts for several years. And then there’s shipping. It’s rare to find anything available where I live and shipping would cost a fortune. Shipping from places like PM or Grizzly is a fraction of what it would cost me to even rent a truck and put gas in it, not to mention time taken from work.
One thing I have noticed is that small South Bend used lathes tend to go for a lot more than much higher end larger machines. If you have the room and can handle the weight, dont be scared to take a step up to the LeBlonds, Monarchs, and Lodge and Shipleys. You will also find people scared off by three phase stuff which is not that big a deal with modern VFDs.
I have found that to be true in so many areas, small shop sized machines go for more than large machines. From sheet metal shears and brakes to tractors. I saw an auction where a large CNC machine, it had to be near the size of a car, went for much less that an old manual bridgeport mill.
Set up is critical for machining Metals with any hope of accuracy and sanity. Steel stand, thick concrete floor, all level and bolted! You will form the opinion that heaven must be made of thick concrete!
BIG SECRET AND TECHNIQUE TO LEVEL A MACHINE !!
1. NOTHING IS STIFF BY ITSELF. REALLY.
2. Level DIAGONALLY! Start with “catty corner” feet and put the level aligned with the line between them.
3. Switch to leveling the other two feet. You will notice that this adjustment ROTATES/TILTS **AROUND** The line between the first catty corner leveling.
4. Retrace these last two steps. It makes it incredibly easy and FAST to get a machine very level.
I use this technique (modified for many more feet) to level 140′ x 20′ Gantry table sections to within a couple of thousandths.
It’s humorously EASY. Once you understand and see clearly WHY it’s easy, leveling anything will no longer scare you.
Really? Sounds like I should rush out and screw the floor my entire machine shop,
In the event reading your post puts someone off getting a machine or workshop together, IRRC the only machine I bothered levelling to the extent of getting the bubble on my machinist level to not move more than one graticule element on the table was my wire edm, and that’s because it makes setup easier when aligning things in the tank.
You can wind up the jack screw on one corner of my harrison l5a lathe, and it makes no observable difference to the bed twist on the machinists level. And that’s just a medium sized engine lathe on the factory steel stand. In fact the factory says just to level it so the coolant drains correctly. If you have some wanky old antique with split foot and headstock support feet or something that the factory stand has the rigidity of a wet noodle to start with ymmv, but its not critical for every case to have any hope of accuracy.
Mind you, I’m not one of those people claiming to be able to work to sub micron accuracy in a non temperature controlled environment…
As the machines get bigger it becomes more critical to level them up. They can get so heavy as to sag under their own weight. The real big stuff is often dropped on a layer of grout on the concrete so they get 100 percent contact. Smaller units have enough stiffness to self level mostly, then you just shim to avoid vibration.
It is not splitting hairs or being overly anal to say a lathe specifically should be properly leveled before use.
I have transported full size atlas lathes with cast iron stands to makerfaire for live machining demos with forklifts and still leveled them before use.
If you have the time and money to actually buy a lathe, it stands to reason that you intend to make something more complex than a cylinder or at the very least spend a significant amount of money toward your hobby. So to be perfectly frank I don’t understand the rationale and flippancy behind simply disregarding taking 20 minutes to properly level your lathe. If you don’t have time to level it you probably shouldn’t be using one.
You can get away with a mill being out of level but a lathes inherent accuracy depends on it being level because of complex issues of torque being transmitted to an out of level bed. It doesn’t need to be leveled with Micron accuracy but you should make some attempt to make it as level as you can. If you have enough torque you can distort the frame over time from running it if it is really out of level. This isn’t is critical for micro lathes, but yes if it is out of level it will also affect the accuracy of your measurements and may create uneven wear on your bed to your saddle and gibs. Over time this can create a very difficult to repair condition on the bed, and it will make trying to get accuracy and play and vibration dialed away harder and harder.
For something like a Taig lathe or a little Seig, something that doesn’t have a lot of mass it is less critical. If it is a monarch 10ee toolroom lathe or even a South Bend anything with significant mass, you are just asking for trouble. If you have the time to use a lathe don’t treat it like a dirt bike, take 20 minutes and level it. If you can’t find time to do that, you really shouldn’t bother learning machining because you won’t have the patience to be successful at it.
Drew, read my comment completely again. The Harrison install documentation states that there is no specific need to level this lathe beyond making sure the coolant drains out. Are you saying they, the manufacturer of this machine are wrong and I should ignore it?
Again because you seem to have missed it. It has a large rigid steel stand which the machine itself was shimmed to at the factory (which the factory also recommends you *never* should routinely separate the machine from for transport because apart the cast iron frame of the machine WILL creep over time and require realignment) . It was designed to be just thrown in place and used. None of its accuracy depends on the stand being set level on the concrete floor (which is only 4″ thick too, although it has fibres in it) and I’ve tested that with my machinist level on the saddle in different conditions after being deliberately left out of level for days to allow it to creep.
This is a 1700lb machine, not a compact desktop model. Its also a engine lathe not a toolroom lathe, but I often machine bearing seats to acceptable limits and other closer tolerance things on it to the accuracy of my measurement equipment and environment, for 17 years on this model so far (I’m on my second because I wore the bed out on the first one, regrind economics, keep same tooling, plus I still have the first as a grinding use lathe in another room)
You might recognize one of my aliases from elsewhere, except I have renounced internet youtube reputation narcissism, because people’s comments should stand and fall at that point in time on the facts contained therein, not their reputation or how many fans they have to get involved in slanging matches. Its also why I took my content off youtube + pulled my galleries. Its all about earning income now. I’m not even sure why I come to hackaday nowadays. In fact thank you for helping me to come to a decision on that also.
Dude, I meant no hate, chill. If the comment if a guy you don’t even know makes you not come here anymore, I would find that dissapointing.
I may not have understood what you meant.
I have seen machinery walk across the floor slowly when it is large and not level and used for a lot of heavy work. I’m sure I’ve not been the only one that’s seen that.
The guy that taught me Machining in the very beginning used to among other things laser level 100 + ton engine lathes for a company called Elliot, known in the naval and nuclear industry. This is stuff that he told me and that I was led to believe is correct.
I never had to make sure my watchmakers lathe on a bench was perfectly level to get good parts out of it but then again it was a mono bed lathe so maybe that had something to do with it, and it couldn’t twist as much.
I think the idea is with any bed that isn’t a single round bar or anything that’s under a lot of weight and thus a lot of torque undercutting is adversely affected by things like being out of level.
I know sometimes my comments on the site come off like a know-it-all, but I really never mean to be rude at all. If I feel I know something is correct where I feel like I have something I can add I add it. I have a lot of weird unique experience with stuff like this and I don’t pretend to know everything or I would just say I am right I am sure there are mitigating circumstances. I am saying this is what I was taught and don’t let somebody’s disagreement with you keep you from enjoying this wonderful site. You can always choose to ignore somebody if you want to.
I’m in the middle of a “Look before you leap” lessons learned. I bought a mini-lathe, and started learning. The problem is, this is really a hands directly on skillset. I don’t have the time. Now I’m stuck with a mini-lathe I don’t have time to use, and a couple hundred bucks of tools for it.
Time to hit Craigslist…
Where are you at? (c;
Just saw this, I’m in Maryland, in the US.
I’m not sure I understand the complaint here. With minor effort (and some YouTube videos) you can get decent results. Literally, with a few hours time, you can achieve quality results.
I’m working multiple jobs, and have a pretty sick family member. Literally don’t have the time or money to pick up a new skill like this.
I’m not sure about the advantages of the Chinese machines. There are many current tales of woe. Precision Matthews has a reputation as a better supplier, but this guy has had quite a time with his new machine.
http://bbs.homeshopmachinist.net/threads/75664-New-toy-coming-PM-1236
Also, the image of the lathe sitting on a table made out of 2x4s and deck screws or nails shows a fundamental error on the installation of this class of lathe. The lathe will not be stable on a support like that and will not work to it’s best potential. It will be more prone to chatter and taper cutting on long cuts.
If a true machinist’s level is used to align the lathe, you will be able to see the lathe twist when you push down on the bench with your hand. It really needs to be on a steel stand of some sort, shimmed to level, and the stand needs to be bolted down. My South Bend lathe of a similar size is mounted on a factory stand, and I could easily see changes in the alignment of the lathe with shims as thin as aluminum foil under the feet.
You will be much happier with you lathe if it is properly aligned. Google “Leveling a lathe” (It really doesn’t need to be level, just straight, which can be determined with a machinist’s level. It’s OK if it is uniformily tilted.)
Wow, this was a great article and, as a former machinist, I can say that the advice given was excellent.
And if you’re truly unlucky, you’ll find a Great Deal on a nice flat belt lathe. That said, there’s one ironworks / artist out there with a steam powered shop. (and was on HAD too I think)
Atlas lathes can be decent, but they either seem to be ones hardly used or harshly used. The 12″ (also sold as “Craftsman Commercial) is a very good one.
Logan (and the 10″ Montgomery Ward made by Logan) and South Bend bench lathes have a plentiful parts supply on the used market, along with Atlas. There are also some 3rd party new parts. Some Atlas and Clausing parts are still available from Sears. Logan still offers a range of new replacement parts. Grizzly may have a few parts left for South Bend.
Never buy a LeBlond or Monarch (or pretty much any other) that’s missing parts, especially not the bigger models. The exception may be the Monarch 10EE due to its very long production history and popularity.
I have a Monarch 12CK (14.5″ actual swing diameter) that I rescued from a scrapyard for $400. There was a cover plate on the headstock I had to make. It had a broken clutch lever (turned a new part and welded the cast iron lever on), and the tailstock was missing plus one of the four shift levers was in bad shape. I lucked out finding a 12CK on eBay with a broken gearbox. After convincing the seller to part it out I got first dibs for the shift lever and tailstock. The rest of the lathe went fast to other 12Cx owners who needed parts.
Same story with a 17×72” LeBlond ‘trainer’. Bought at an auction, missing a bunch of parts. Found one on eBay with a shorter bed that was very badly worn. I got the parts I needed to fix up mine to sell to a shop that works on Caterpillar machines. They needed something long enough to hold the axle shafts.
There really is a difference though in the brands. Its a tradeoff. A lot of South Bends, Atlas, and Logans were made for schools and home shop use (that why Wards and Sears). They are not high end production shop machines, Having said that, the used ones will often be in better shape because they sat in schools, garages, and basements idle most of the time. A lot of LeBlonds and Monarchs are ragged out because they were worked to death in production which causes the worst wear in concentrated areas. You just have to find that diamond in the rough. As far as the 10EE you better make sure you always see it under power. They have complex expensive drives and even though they were around a long time there were multiple drive systems so it matters what production years you are in. You have to learn about the issues common in any machine you are considering. LeBlond for example had an issue with certain early servo drive systems that makes them hard to fix. Earlier and later machines are just fine.
You are right about not buying anything with broken components that are hard to replace like castings. I don’t mind goofed up handles or nasty gear because worst case you can make them yourself. If you cant see it under power buy it for no more than its scrap value. If the ways are torn up, walk away. If it has been sitting outside, forget it unless its free and you want a project.
If you NEED a lathe, by all means go and buy a new one that suits your needs and get on with it. If you just WANT a lathe, take your time and keep an eye out for a bargain. Look for small shops closing. I have also seen stuff go real cheap at heavy industry auctions. It is real common for an large industrial company to have a small under-used machine shop just for repair work even if their primary work is not machining. The people at the auction are usually not there for stuff outside the main line of the business. A lot of farm auctions will also have small equipment lightly used.
I bought one Bridgeport mill from a company I did some work for. I saw a really nice Bridgeport sitting in there shop covered in dust and piled up with stuff. I knew it was nice because all of the scraping on the machine was super factory fresh and the table was flawless (which is rare). I told the guy to let me know if they ever wanted to get rid of it. He told me to load it up and get it out of there and asked for a case of beer. He said no one there even knew how to use it and he wanted the space.
Sometimes you can find a real deal on a 460V machine or a three phase, just factor in and have a source for a replacement motor or possibly a VFD. Know that a lot of people will walk away without researching how much a conversion would cost.
Look for crash marks on the cross and compound slides. These tend to be common on school shop lathes, especially when the teachers don’t show the students how to avoid running the carriage into the chuck.
On gearhead lathes a crash can be quite destructive, especially on the smaller ones. Especially prone to crash damages are the 13″ ‘trainer’ version LeBlonds. Most of the gears in their headstocks are only 5/16″ thick.
The ‘trainer’ LeBlond lathes are built lighter (but still weigh a heck of a lot) and are easy to identify by the swing diameter inches cast into the front of the headstock in a recessed square. They do not have the LeBlond name cast into the headstock or anywhere else.
When looking at an old lathe you’ll want to test *every gear*, and check all power feeds in both directions. If it’s variable speed you want to run it through the full range. Any bad noises and you should pass on it, unless you know you can get parts or repair it.
The other big trick to buying old iron is one much talked about on the machinist forums, but I don’t see mentioned here: walk in *very, very, very* informed. Go to sites like Practical Machinist, Hobby Machinist, Home Shop Machinist and Vintage Machinery. Read about someone who brought home the machine you’re thinking about. Watch Youtube videos about that model. Find a manual online and see what accessories the company sold for it back in the day. I’ve been to sales and bought machinery where over in a bucket, under a bench on the other side of the shop was an accessory I wouldn’t have found or wouldn’t have found for less than the price of the machine on eBay, and just for the asking it came along at the original price. Read about how to evaluate condition and point out problems when negotiating the price. Don’t be afraid to walk away when it turns out that the entire drive system has been replaced with something cobbled together and nothing like the original.
In my case, I try to walk into a machine purchase with knowledge of, at a minimum, what he thing weighs and how many pieces it comes into, hopefully what those pieces will look like or how much they’ll weigh on their own. I finally caved and bought a hanging load cell in the middle of bringing home the Alexander Pantograph 2A I bought last year to make sure that carrying the pieces into the basement with friends and no winched rigging would be at least reasonably safe, since it was in pieces and loaded into my car (you read that right — car) by a fork lift. Don’t pick up anything beyond your capability and don’t use untested, unrated rigging — buy the stuff that you can trust so that no one gets crushed.
Finally, don’t be afraid of old iron! It’s fun, it’s awesome, it has a real history. I love my 30k+ pounds of basement carried and winched machine shop. I just want people reading articles like this to know where to go to be properly informed before they walk into a bad situation or worse, someone gets hurt trying to do something they shouldn’t. Proper preparation saves *huge* amounts of work later on.
Actually, HAD writers/editors, a feature on Vintage Machinery would be pretty cool. Maybe/especially one on Keith Rucker’s book scanner and the sheer amount of information they have up…
Seconded- hackaday over the years has done some good articles on serious machinery but it’s mostly been the soldering iron 3D printing crowd. It wouldn’t be a stretch to occasionally delve into actual machine tools like this in a series of featured articles to give people the basics of where they need to start researching and looking for serious understanding. This place is not Practical Machinist but there’s an enormous range of things as a maker you can do if you understand a basic Mill and a lathe!
Trained machinist and watchmaker hacker/maker.
Im in Pittsburgh and never knew Mathews Precision! Looks like they make nice stuff- awesome.
I started with usa made Taig manual mill, eventually bought their lathe. Taig stuff is well made- but decievingly simple robust construction. They have great customer support, I’ve even talked with them about engineering modifications- they are really open nice people who make the most beefy micro machining tools in the us.
Taig’s only real disadvantage is their lathe has no threading attachment. I wish they would just make one already! Don’t be fooled by the gumband powerfeed- it works well, and is designed that way for safety. If it breaks- you need a bigger lathe.
It is only made for micro work. But it’s darn cheap!
Have a friend who recently bought their cnc mill- quality of base castings has actually gone up, build quality is still there. I know the school I went to for watchmaking uses them too- retrofitted to cnc- to machine watch plates, but that was years ago. They can do good micro work if you really tweak them carefully.
Not affiliated with Taig, just like their stuff. Sherline is well made but just nowhere near as beefy or rigid. Their lathe has threading attachment though. Are you listening yet Taig???
I have restored an old Atlas lathe with help to working condition and upgraded to power crossfeed. Seconded- they are often worn out and very beat up. They can work decently if taken care of. Old iron- research. Here in US, best normal old lathes are probably southbends. Monarch 10EEs are overkill for most casual makers- but if you want precision, they got it. More iron means more machine rigidity means more precision. Look for beat up ways near the spindle and crashes from the chuck into the saddle! That will save you so much grief down the road if you avoid stuff you find that on. Lathe ways can be rescraped but it is very expensive. Best used stuff you will find in estate sales of old machinists. Avoid the temptation of buying stuff that came from community college or student use- it’s often abused and heavily destroyed. Craigslist is your friend if you look for old shops closing out equipment. Ebay is usually more expensive. Machinist estate sales are a goldmine for affordable quality tools and tooling.
Tooling WILL be the majority of the cost of owning a mill or lathe. Taig mill cost me around 800 8 years ago- and immediately cost around another 800 to get really tooled up with accessories like good vices, cutters and measuring tools etc. The figure in the story of spend half of what you have on the machine is very accurate.
Remember- you only pay for quality once. If you buy a tool that is not going to last it will end up costing you more money. A lathe you plan on using for a while is a serious investment, research heavily before you buy because there is a lot of junk out there- like the harbor freight metal lathe at a store near me that has the morse taper tailstock center chucked into the 3 jaw headstock chuck- ruining it. Research carefully before you buy! And whenever possible- check the fit and play of machine tool slides and ways in person before you buy something worn out. Some things can perpetually be rebuilt- like a Bridgeport mill. Choose….wisely.
The Schaublin 102 I inherited from my grandad – only out of my dead, cold hands!
A precision marvel…
I own one! Best small precision lathe ever made hands down.
If you want to make watches clocks or precision Instruments,
It doesn’t come much better if you have one of those fully outfitted.
Nice to see somebody who appreciates such quality most people have never heard of them
For those of you looking for a source. There is a guy on You Tube called Ox Tools his name is Tom Lipton that does a video on how to buy a lathe. There are a lot of those on You Tube but this is one of the best. Tom himself is a very accomplished machinist that has a day job making prototypes at one of our National Laboratories (I believe it is Lawrence Livermore but cant recall). You Tube actually has a very active machinist community and it is an amazing mix of home gamers, retired geniuses, and pro machinists (who I admire because you must really love your job if you are a machinist at work and machine at your home shop for fun). A good example of a pro that is also a hobbyist is Adam Booth who is known as ABOM on You Tube.
Look up Robrenz, Clickspring on youtube too. For the record, working as a machinist sucks. Having to make things that you don’t want to make for other people and doing it in a hurry so your boss doesn’t yell at you and working around busted equipment it’s just not fun. Machining for yourself like most of the people do on YouTube and you’re seeing their projects they do for themselves, it’s the exact opposite and it’s deeply pleasurable.
Yeah Clickspring is in my opinion the BEST free content out there. The production value is unbelievable. One thing to take note of…the vast majority of the pro and high end amateurs on YouTube are using old iron machines. The most notable exception is Chris from Clickspring who uses a Sherline and a higher end Seig Chinese lathe. I also am sure he optimized that Chinese machine because the quality of work shows through. Here are some to check out that may have already been mentioned.
Vintage Machinery.org – the go to source for restoring old equipment. His website has manuals for hundreds of old machines.
Clickspringprojects.com – Chris makes beautiful clocks and video content. Also some metalurgy and casting.
Turnwright machine shop – a pro job shop with a lot of repair work, machine rebuilds, plasma cam, welding, machining
Abom – Adam Booth is a pro heavy machinist at work and restores machines at home. You can see how he moves them, evaluates them and improves them.
Ox Tool Works – Tom Lipton is a super precision and measurement geek and is a pro machinst at a national lab. He also shows how to evaluate a lathe.
Quinn Dunki – our author above, the “Jill of all trades”, can build you an Apple II, fix your pinball machine, race car, dishwasher, and exercise bike. New to machining, follow her quest.
Tubal Cain – probably the grand daddy of all you tube machinists. A retired shop teacher and machinist. Repair, steam engine construction, machine restoration, casting. Think of a cool grandpa with a machine shop in the basement and a foundry in the garage.
There are lots more but start there and see who those people like and subscribe to. I guarantee if you spend some time watching them you will know what to buy. They are all really approachable in my opinion and will help you out whenever they can.
One more….
NYC CNC – self taught guy who turned pro and opened his own job and prototyping shop. Very CNC centric and the go to guy for Fusion360 Cad/cam training that is the best out there. I think a lot of makers would be interested in the CAM systems since they are the combination of machining and computing.
Excellent list. If youre looking at the higher end of manual machining, my 2 go tos are Robrenz and Stefan Gotteswinter.
If you are interested in scraping or rebuilding precision slides, Stefan is a guy even Robrenz subscribes too ;)
Throw “This Old Tony” on the list too.
Really funny commentary, interesting projects, great production value, and seems to know his stuff. Also a nice emphasis on “home shop” pros/cons of various things, whereas some other channels have a more professional/industrial view given it’s their dayjob.
Stick with the old rocker tool post. Learn how to grind your own tools. High speed steel and cobalt works well for almost any hobby type lathe work. You can save a lot of money versus using carbide cutters. You can grind any shape tool you need to get into any nook or cranny to make a cut. All you need to do is slow down a little so you don’t burn them up. You can run a sharper edge with more relief to make very nice cuts with less power and less deflection. There are some older Taiwan made lathes out there with hardened ways that are quite good.
I know where you’re coming from man. Im only 34 but I learned from a guy like you who taught me exactly that. Learning how to grind your own tools is challenging but not crazy hard, once you understand cutting geometry you can make a tool to cut anything pretty easily, even from broken drills.
Carbide is used for everything even in professional shops unless you’re using a giant shell Mill without inserts, but high speed steel is actually better for certain things, and a lot cheaper. I’ve even made carbide from scratch as in from the powdered metal, I used to work as a carbide machinist. There’s actually tons of grades of carbide, but the stuff has its limitations. If you are starting out, I think you should learn with high speed steel just to understand how heat affects your work piece and your cutter because you will see if you are cutting improperly if your tool changes color and loses its temper. High speed steel tools force you to look at the temperature of the metal chips you are producing and cut at safer feed rates. If you are grinding tools of either carbide or high speed Steel you will see the difference in all of this and having the right or wrong cutting geometry on your cutter in that regard better on HSS because you may see the tool bit change color and get too hot if your angles are wrong. You won’t see that in carbide at all and if you don’t understand it you could shatter your tooling.
That being said, you’d be surprised how easily you can grind your own carbide tools too if you have a good diamond wheel, like my GRS powerhone. It goes right through HSS too
Gotta disagree with the rocker aka lantern tool post tho- unless you are doing some seriously heavy cuts that you need really high rigidity for. The quick change tool post as it currently exists when you get one well made really is nothing but an improvement. Shimming tools go bye bye- and there really is no useful purpose to having to do that, it’s just antiquated and not in any useful way
Grinding your own bits, sure, using carbide bits, yep. But lantern / rocker toolosts you can keep – a less-rigid, toolbit-angle-changing, setup-time-wasting artefact from a bygone age.
New machinsts need to be aware that a lot of smaller machines cant reach the feed rates and speeds for carbide to give a good finish. Important to know that high speed steel is sharper, carbide is more durable. I also agree with skipping the lantern tool post. Been there, done that, wont go back. No good reason to use them.
My PM1127 has hardened ways as well as the G0602 and others. Chinese machines have come a long ways and are more than adequate for most hobbyists. Indexible cutters from places like Shars are reasonably priced and a good choice for beginners. I keep a few HSS blanks around for special situations, but use mostly use the indexible carbide insert tools. The HSS is not worth hassle to me as I don’t even have room for a benchgrinder in my small shop nor the time to learn proficiency and grind tools. Maybe someday after I get proficient with the other aspects of this craft I might venture into grinding HSS bits, but until then the indexable carbide saves a lot of time and I get consistant results. I wouldn’t wish the rocker arm toolpost on anyone… unless you just like to waste time shimming tools. Especially as reasonable as the QCTP’s are these days.
Anyone had the Micromark lathe or mill? I’ve been eyeballing those for years.
I have a Micromark 7X16. It is the same Chinese stuff lots of other companies sell. It is Identical to the SIEG C3 with a longer bed and different paint job.
I spent over a year re-building it (all new jibs, re-designing the apron, new headstock bearings, and re-bedding the carriage) just to get it to the point where it is useful for cutting steel with the kind of tolerances I like. The carriage jib scheme on those lathes is awe-full, so I re-designed that also.
Do yourself a favor- save up a little more money and buy bigger. 9 X whatever or bigger. The biggest machine you can move and store in the space you have. These little 7″ swing lathes are just too small to be useful for anything except tiny, soft material work, and by the time you’ve done enough lathe work to be really good on a small lathe (if it is your first lathe) you will want a bigger one anyway.
The 8×20 or 9×20 lathes are clones of the Austrian made Compact 8. Despite the original being made by Emco, it’s a pretty crappy design. The V ways are small and it has no reverse gears for left to right cutting. What’s crazy is none of the companies making clones has ever bothered to fix any of the deficiencies of the design – except for adding a half-assed quick change gearbox in two different styles.
One type has a couple of knobs for a very limited number of gearings, the other has a single, 9 position lever. Both require swapping change gears for the full range of feeds and thread pitches.
Grizzly is the only company do do a major overhaul of the Emco x20 design, as an 8″ swing lathe in their new South Bend line. It was a flop for several reasons and has been discontinued. The problems, in no particular order.
1. 8″ instead of 9″ swing. The most popular South Bend lathe of yore was the 9″ swing Workshop. Making the new one 8″ is a WTF?
2. Cog belts instead of gears in the drive from spindle to quick change gearbox. Uh, why? Gears work, they’re robust, and they’ll not slip, ever.
3. The cross slide and toolpost mount are the same exact POS used on the Compact 8 and all the clones. The most reviled part of the design and *that* is what Grizzly chose to not do anything to. The slide dovetail is narrow and low and the screw is only 5/16″ (8mm) diameter.
The headstock is a new design, looks much more robust than the typical x20 one. The bed casting appears to be beefed up a lot. The gearbox looks like it’s the old 9″ Workshop casting adapted to the new lathe. The apron looks like an all new design, made to resemble the Workshop one, while the half nut lever looks like it could be a direct copy from the Workshop lathe.
If they’d made it a 9″, not used cog belts and at the least incorporated some improvement to the cross slide, it might have been a decent lathe. In other words, a lathe sharing absolutely nothing in common with the x20.
What the x20’s do have going for them is their simplicity makes them fairly simple to convert to light duty CNC lathes. I got a barely used JET 9×20 for $50 and have been slowly working on a CNC conversion. Need to get the scratch together to buy an MC2100 PWM treadmill motor controller.
The 9” south bends are great machines for the size I highly recommend them. I have had had 3 Asian mini mills x1-2 then 3. Two comments on these. Stay away from the variable speed models they lack the power you want. The gears on the x1and x2 can also be so sloppy to ruin bits especially on interrupted cuts /holes. Also the rigidity is really poor. The 220v geAr head x3 is the minimum size I would consider for a home mill after these experiences. Still quit pleased with 9” south bend, I have 4!
I would love a well outfitted southbend but everybody wants an arm and a leg for them even beat up. You are right about the variable speed being a torque limiter normally
Set up is critical for machining Metals with any hope of accuracy and sanity. Steel stand, thick concrete floor, all level and bolted! You will form the opinion that heaven must be made of thick concrete!
BIG SECRET AND TECHNIQUE TO LEVEL A MACHINE !!
1. NOTHING IS STIFF BY ITSELF. REALLY.
2. Level DIAGONALLY! Start with “catty corner” feet and put the level aligned with the line between them.
3. Switch to leveling the other two feet. You will notice that this adjustment ROTATES/TILTS **AROUND** The line between the first catty corner leveling.
4. Retrace these last two steps. It makes it incredibly easy and FAST to get a machine very level.
I use this technique (modified for many more feet) to level 140′ x 20′ Gantry table sections to within a couple of thousandths.
It’s humorously EASY. Once you understand and see clearly WHY it’s easy, leveling anything will no longer scare you.
Much better to go and use someone else’s lathe. I recently managed to do about 20 hours machining in one of my local eng factories – they were interested in the project and pleased to help: https://hackaday.io/project/53896-weedinator-2018
On moving the lathe/mill:
Home Shop Machinist’s “Projects Two” has an excellent article from a fellow who moved what appears to be a 14×40 machine into his basement. LOTS of forethought and explanation.
On old American iron:
I have a 70 yr old South bend 13×36 that is markedly inferior to my friend’s Chinese 13×40. Both are heavy, solid machines; dials and such are all metal on both machines. My SB has much more backlash in cross- and compound slides and noticeable wear on the ways. The max speed on the Chinese lathe is twice that of the SB. The SB has a leadscrew, the Chinese model has leadscrew and feedrod as well as a spindle brake. The flat belt on my SB has a tendency to slip and to come off the pulleys. Most important: the SB has wear on the spindle bearings, so much that the spindle occasionally ‘jumps’ a couple of millimeters on a heavy cut.
Bottom line: old iron is great if you know what to look for in the ‘wear’ department. (I knew some but not all.) But it may well be as much of a project as a new Chinese machine.
Miscellany:
Carbide is great for high speed and for hard stuff like 316 stainless steel, not so good for interrupted cuts; it will chip and crack.
QC tool post should probably be your first tooling purchase after bits; a lantern-post tool holder is a frustrating horror. Get a couple extra tool holders, and make sure you have one for a cutoff bit.
Learn how to use a 4-jaw independent chuck. Once you understand it you can center a job in just a few minutes, much more accurately than a 3-jaw self-centering job.
The actual cutting takes about 1/2 to 1/10th the time as the setup does. Don’t be too anxious to
I finally was able to Gggle what QCTP and Lantern post tool holder meant and look like, all this talk about them had me confused.
Quick Change Tool Post
There are a lot of old school things in Machining that are still really useful Shapers are not something for example that most places even use anymore but they are great for certain things. Lantern tool posts are one of the few things that are utterly useless because they use a rocker often to set the tool height which effectually changes the angle the tool you are using meets the Centerline of your work which changes its cutting geometry in relation to workpiece. No matter how you look at it they are utterly useless at this point. There are a lot of poorly made quick change tool posts (QCTP), and they cause a lot of problems too but a well-made one just works more properly than a lantern tool post
Who makes the lathes that the Chinese use to make these lathes ?
Believe it or not there is a lot of high-end American and swiss stuff in China they bought a lot of our old equipment especially from the Swiss after the 1970s quartz watch crisis that nearly ended the watchmaking industry.
I wouldn’t say that all of their equipment is up to par but they do have some decent equipment over there.
I recall a big lathe from Harland and Wolff Belfast being exported as a base for a CNC lathe (This was turn a school bus spec though)
its also important to consider: the cheap lathe you have that may break in a few months, is better than the awesome ultra reliable lathe you never get around to buying.
I just bought my 5th machine. A 1968 British Parkson 2N horizontal mill with vertical head, universal head and slotting head. Only paid $800 for it, sold my mini mill to pay for it. I started out with a 7×14 mini lathe, then got the mini mill. Then Picked up a German Deckel KF12 pantograph mill for $600(The ways are in amazing condition, needed to change the motors). Then I picked up a Monarch 16CY(18.5″ swing and 78″ between centers) for $800. It’s a massive beast. It’s worn and was very dirty but still works great. It’s not going to hold super high tolerances, but it gets the job done. It will blow away any import lathe that I can afford to buy.
Not only is moving the big heavy machines difficult, but powering them can be a challenge. The Deckel was 575v 3phase so I couldn’t find a suitable VFD to drive it. The motors were seized up anyway. So I just replaced the motors with off the shelf single phase motors. Thankfully the Monarch had already been converted to single phase, I just had to wire up a new contactor for that one. I’m still working out how I’m going to power the Parkson. It has a 10HP 3phase 208v motor for the spindle, another 3HP 3 phase motor for the power feeds and yet another small motor for coolant. I’m looking at 2 VFDs to run that one and something like a 60A 240V circuit run back to the panel.
The quality of the steel in these old machines is far superior to the new machines. Not only in composition but in fit and finish as well.
If you’re interested in more information on pantograph machines and talking with fellow Deckel owners, take a wander over to the Yahoo Groups “Pantorgraph Engravers.” All kinds of good information and manuals, which was super helpful to have while breaking down my Alexander 2A and loading it into my sedan.
Knowing a few fellow basement shop machinists, the standard method for that Parkson would be a 15~20HP rotary phase converter with VFDs to do speed control on each of those motors. Generally, that kind of conversion is done to run old 80s/90s CNC mills in a home shop environment, where the VFDs are already provided as part of the control setup for the machine. If you’re not in need of the control signalling lines for limit switches and the like on the manual mill, I’d skip the VFDs entirely and just run off the rotary. Just keep in mind that you have losses in every step of that conversion so you need up size all the converters to account for that and the entire load they’ll be driving.
Sidenote: I’ve never been able to locate a single (or poly) phase to 3 phase converting VFD in anything over 3HP rating. I always assumed that you *have* to use a rotary above that size with a 3 phase to 3 phase VFD after it. Am I missing something in there?
I think that is about right. There are big VFDs but they get real expensive above 5 HP. The rotary wont be cheap either but can power all of your three phase gear assuming you are using one at a time. The two downsides to the rotary is that you have to oversize them and they are noisy. American Rotary makes some models you can put outside and works with a lot of home machinists. They sponsor Vintage Machinery.org and i think you can get a discount code from there.
” I’m still working out how I’m going to power the Parkson. It has a 10HP 3phase 208v motor for the spindle, another 3HP 3 phase motor for the power feeds and yet another small motor for coolant. I’m looking at 2 VFDs to run that one and something like a 60A 240V circuit run back to the panel.”
You must have one of these behind the house. :)
https://upload.wikimedia.org/wikipedia/commons/thumb/2/27/Melbourne_Terminal_Station.JPG/320px-Melbourne_Terminal_Station.JPG
‘just in getting a bucket of electricity for my lathe’
A couple points, speaking as a person who got into machining within the last 4 years:
1. They aren’t super-common, but deals can be found: I got a large Enco mill-drill for $400 on Craigslist, for which I successfully built a rotary phase converter from a motor that I had dumpster-sourced. And I found a South Bend heavy 10 lathe on a government auction site for $500. I had to buy it sight-unseen, but it turned out to be pretty nice. It required 3 phase power, but I just happened to have a rotary phase converter. In both cases you have to really know what you want and be ready to “pounce” when you find a good deal.
2. I could not DISAGREE more with this sentence: “When learning, you want to use high quality free-machining steels, aluminums, and brasses; not scrap Mystery Metal™ you found behind the dumpster at Arby’s.” When you’re learning and beginning is PRECISELY when you don’t want to be screwing up a $100 piece of metal. Good sources of cheap metal to turn are: dumpsters: anything made of heavy/solid metal, schedule 40 or above pipe, or brass or copper Thrift stores and yard sales: Brass goods, solid weight-lifting bars, cast iron weights and dumbbells, and anything else made of heavy metal: larger re-bar, railroad spikes. Any large-ish solid pieces of acrylic or other plastic round bar stock are nice for learning too.
Things turned from these kinds of materials tend not to be works of art, but you can get a lot of experience for cheap. My best example of a “keeper” from this kind of thing is the backplate currently holding my 8″ 4-jaw lathe chuck. I turned it from one end of a cast iron 50lb dumbbell that I found at Goodwill for $5. The iron was porous and cantankerous, but I still enjoyed it, and it works.
3. If money is tight, don’t blow big money on a QCTP. Find yourself a piece of 1″ plate steel (Mine was a bolt-on plug for 10″ flanged pipe) and a piece of 1″ steel rod (mine was some kind of heavy machinery pin that I found laying alongside the road) and make yourself a Norman Patent toolpost. It’s the first lathe project I ever did, and I’m still using it, I still love it. Maybe some day when my ship comes in I’ll buy a QCTP. And maybe not.
#2- it cuts both ways haha. If you are learning you are probably cutting small pieces of metal so cost is not normally a factor. Good steel good aluminum aren’t really that expensive to buy. Brass is expensive but the nicest thing to learn on. There is a wide range of things that look like Steel that can completely destroy your tooling if you don’t know what they are. Cheap is good but when you are learning knowing what you were cutting is often more useful because you can learn what a specific material actually cuts like. It’s hard to learn how to properly cut things when you don’t have a base of knowledge to know what you are cutting. Case in point when I was learning I tried to machine a bolt out of something that just kept destroying even carbide tools and I couldn’t figure out what the stuff was but it wasted hours of my time and a lot of tooling, but it was free and laying around a lot of other unmarked stuff. I found out later it was some special kind of super tool steel for a hydraulic shaft, probably S7 or more likely some kind of crazy variant of that because it was even tougher than S7 now that I know better. When you know what you’re cutting you know if it’s your fault if it’s not cutting properly or if you just pick something ridiculous that’s just hard to cut no matter what you do. Cast iron machines really easily most of the time but the dust from it will destroy your ways as its very abrasive.
#3- kind of agreed- I really recommend a good quick change tool post not a cheap one but there are non Lantern style holders that work really well. You can machine a simple block carefully to hold your tool solid at Centerline and it will cut really well. You will have to shim it as the tool wears though, but you can get good results with a very solid style like that as long as it doesn’t tilt your tool bit to change your cutting geometry as it approaches the work. Geometry is everything in Machining.
You’re definitely right about tooling being expensive to destroy. But for beginners, especially for those who have a less than perfectly rigid lathe, I’d recommend sticking with high speed steel tooling. If you dull your bit, then sharpen it.
But the other thing that’s invaluable is the experience. “people say you can’t turn hardened steel. Why not?” So try it. And then you’ll see. And there’s no way to really get proficient at turning various materials without actually doing it. And there’s something really cool about making a $50 part or tool out of a 2 or 3 dollar (or even free) item.
As for turning cast iron, you’re exactly right about it being abrasive. Watch some Keith Fenner or some Abom79 and you’ll see how to turn it and how to use good hygiene to protect your equipment. No better time to learn that than when you’re just getting started.
Finally, the Norman Patent toolpost is very rigid and completely adjustable, toolheight included. The only thing it lacks is angular repeatability, which is to say that you have to square it up to the axis of turning with each tool holder change.
You can get good quality metal from the right scrap yard or recycling center. I have one nearby that receives all of the scraps from the shipbuilder Marinette Marine. It usually is marked new material off cuts so you can look up what it is. Find a company that manufacturers stuff and ask about their scrap. They might give you some for a box of donuts or at least tell you who picks it up for them. The scrap yard sell it by the pound at recycling prices. It saves them the transport charges. More often then not the amount ismso small they just let it go. Show them something cool you did with it and again donuts and coffee are universal bribes.
^^^ What he said- yes. If you have a kind supplier through a local scrapyard, go for it! Unless it’s titanium or very exotic stuff like Vasco Max (which is a maraging steel used for missle headcones and ITAR controlled), most of these Metals in small quantities, aside from anything with high copper content like brass, bronze, or raw copper, are really not that expensive as scrap in small quantities. Many places I’ve worked for will give stuff away if you don’t take a ton of it.
Find your local machine shop and try to get ahold of shop supervisors not secretaries and tell them who you are and ask if they could sell you any cut off scrap. You might be surprised.
Just remember if you see colors painted on pieces of metal there are industry standards for what those colors mean and they can often tell you what type of metal you are dealing with. If you don’t know there is always a spark test on a bench grinder that can help you narrow down what you are working with. If you go to a machine shop there is a good chance if they give you something they can identify it for you.
After a very long search I decided to buy a new China lathe (Bernardo Standard 165) with digital indicators for all axe.
It’s quite hard to find used machines in Germany. All the machinists and workshops don’t sell the old machines. Besides the old machines are much heavier than the china, which can be a problem with transporting and setting up the machine. I spend the rest of my time budget in working with the machine not repairing the old one ;) (at least now).
I just wanted to mention my experience on trying to set up shop in my basement. My first two machines I bought as a pair one was around column Mill and the other was a Sheldon 10 inch lathe with change gears. They weren’t bad but the round column was kind of a pain in the neck. I always wanted to do try to improve by finding a lathe with a quick change gearbox and a square column Mill. My next purchase was a 9×20 Enco, which really wasn’t any better than my Sheldon lathe and I sold it after about 2 weeks of playing around with it. I then ran across a deal where a man’s father had died and he had several machines in his garage I ended up buying a square column Mill and a hardinge second operation lathe. The Chinese Square cplumb Mill was actually a 9 by 40 and quite heavy and so was the hardinge lathe. They were pretty difficult to move around. I managed to get the square column Mill in my basement but I couldn’t get the hardinge lathe down the steps and clear my 5 foot basement door head. I didn’t want to risk taking the organs apart because I had read in the manual that add some kind of elaborate speed control system that should only be taken apart by Factory mechanic or something like that. So it’s still sitting up my pole barn which isn’t really a very good environment for an nice machine like that but unfortunately I had no choice. I then found a 9 by 20 CNC Lathe for sale at a university for Fairly cheap price. I manage to get it in the basement without any problems. My plan was to retrofit it with a centroid control system gecko drives. I had problems trying to get information about using the centroid control system and wound up not using it, in fact that project is still ongoing. I picked up a couple of small Shapers and a small surface grinder tool cutter I managed to get them in the basement just fine so I’ve got a few machines in the basement shop now which are all projects. When I started this effort I talked to a tool and die maker I work with and his suggestion was to buy new chinese-made machines and not try to buy old American stuff that was worn out. This came as quite a shock to me because he’s kind of the buy American type guy but I learned that he had in fact bought Grizzly machines in his job and was very happy with them. I mentioned to him that I had heard that all Chinese machines were just kits that needed to be completely redone and he said that wasn’t the case with his machines he was able to barely clean the cosmoline off of them and go to work . I didn’t do this and in hindsight I kind of wish that I had, because the money that I’ve invested in these machines, that need complete retrofitting and refurbishing, I could have easily bought new Chinese machines and I would be cutting chips instead of working on machines.
It’s great you elaborated on the importance of looking for higher quality machines means that you can take care of the machine as long as possible so it’s definitely okay to go overboard when it comes to buying an investment such as this. Another thing to keep in mind is that it’s challenging to find a vintage piece that’s ready to run at an affordable price, so if you do find one of those, get it right away and start using it because it’s hard looking for quality that falls within your own budget. If I had a chance to use a lathe milling machine I would look for something that’s serviceable yet at the same time affordable.