While robots have been making our lives easier and our assembly lines more efficient for over half a century now, we haven’t quite cracked a Jetsons-like general purpose robot yet. Sure, Boston Dynamics and MIT have some humanoid robots that are fun to kick and knock over, but they’re far from building a world-ending Terminator automaton.
But not every robot needs to be human-shaped in order to be general purpose. Some of the more interesting designs being researched are modular robots. It’s an approach to robotics which uses smaller units that can combine into assemblies that accomplish a given task.
We’ve been immersing ourselves in topics like this one because right now the Robotics Module Challenge is the current focus of the Hackaday Prize. We’re looking for any modular designs that make it easier to build robots — motor drivers, sensor arrays, limb designs — your imagination is the limit. But self contained robot modules that themselves make up larger robots is a fascinating field that definitely fits in with this challenge. Join me for a look at where modular robots are now, and where we’d like to see them going.
Many Robots Combined for Larger Tasks
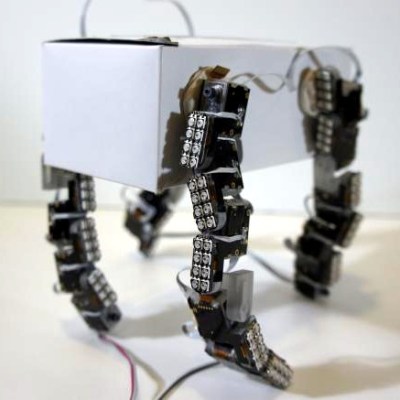
On the surface, this seems like an incredibly useful, although often overlooked, idea. A small swarm of robots can be tasked with many different functions such as moving, manipulating tools, and solving a wide variety of other problems. The robot can decide for itself the best way of doing these tasks and form itself into the correct shape for whatever function it needs to perform. Another key feature of a robot like this is that it could do many of these tasks simultaneously. For example, half of the robot could separate and hold an object while the other half manipulates a tool to use on the object.
The modularity is precisely what makes this type of robot so useful. While a single general purpose robot like Baxter can be tasked with manipulating one thing on an assembly line, for example, it might still have a whole other arm that isn’t being used. It’d be nice if that arm could be detached and put to work doing something useful. Another perk of something like this is that a robot built on these principles wouldn’t be constrained by a single point of failure. If it happens to get damaged, malfunctioning modules can be replaced, or in the event that replacements aren’t near, the rest of the robot can go about its task while waiting for reinforcements to arrive. By design, a modular robot can communicate with all other parts of itself regardless of which parts are connected, where they are, or what they are doing.
Future Benefits of Modular Adaptability
When robots start seeing wider use outside of the controlled conditions of a factory where terrain can’t be predicted, adaptation is the only thing that will make their use feasible. Wheeled robots are a nightmare in rocky terrain. Legged robots can succeed there but will be slower than wheeled when back on pavement. A robot that can be loaded with special purpose modules likely to be needed and switch them out itself when necessary.
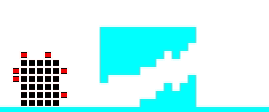
Researchers envision robots that can go where people can’t, like search and rescue operations in rubble following a natural disaster like an earthquake. Modular robots could succeed in situations like these by reorienting themselves to fit into much smaller spaces than traditional robots. An interesting way to visualize this is shown here, part of the cellular automata research conducted at the Rus Robotics Laboratory.
Other applications for modular robots are in situations where weight is a major concern, and where the multi-use functions would go a long way, such as in space. There are many other applications for modular robotics, as the upsides aren’t just for niche applications like disaster relief and space exploration, but would help in virtually any situation. A good way to wrap your head around some of these future uses is to look at how Science Fiction authors are “using” them. Neal Stephenson goes out of his in the novel Seveneves way to explain in detail the use of modular robotics as the workhorses of space operations.
Like Robot Democracy: Who’s in Charge of the Whole Made from Many Individuals?
Currently, modular robotics hasn’t progressed as far enough to produce useful useful robots like Baxter. But there is a lot of serious work being done in labs within academia and elsewhere to move the state of the art forward. Back in 2013, we saw a lab at MIT create a set of blocks which could move independently and arrange themselves into different lattice configurations. This is the cellular automata from above put to the test. The modules, called M-Blocks were at first limited in that they were remote-controlled and could only move in one relative direction. A proof-of-concept they were impressive and the work has continued.
Another lab producing some interesting results in this field is the ModLab at the University of Pennsylvania. They are currently working on many projects including Variable Topology Trusses, a single-actuator flying robot, and of course the SMORES shapeshifting modular robot. These robots have four degrees of freedom, as well as an actuated magnet that allows them to interact with other modules or with metal surfaces. This is one of the more versatile modules we’ve seen so far, but they still have the same issues as other modular robots which boils down to communicating with a large array of objects, and deciding in a decentralized way how to best perform tasks.
Controlling a large swarm of objects with no central command structure also gets exponentially harder as the number of modules or units goes up. For inspiration on how to effectively address this hurdle, though, we can look to large groups of drones, which can be programmed for control by one person but also all act as a group in unison with each other based on a set of predetermined rules. A lab at MIT was able to develop a decentralized control algorithm for these “swarms” of drones which allows them to act in more efficient ways while still being able to follow an overall control command. We have seen similar projects for orienting ground-based swarms as well which can act in a prescribed way but still have modularity as a core principle.
No Hands, No Feet, Just Modules
Another major drawback of the M-Block design (keeping in mind that it was never intended to be used as a functional modular robot) was that the modules could not manipulate anything themselves, but could only move in relation to other modules. This is where modular robots like Dtto have been able to push the field forward.
Dtto built upon a design scheme using two parts that are linked by a hinge. The outside of each half can attach to another Dtto module which itself has a hinge in the middle. Each module can control its hinge, giving the robot the ability to move easily under its own power as well as connect and disconnect sections of itself at will from 10 different locations on each module. This is credibly versatile as it multiples a single degree of freedom per module, into movements and angles necessary for just about any task.
Dtto was named the Grand Prize winner of the 2016 Hackaday Prize, and with good reason. The project gave us insight into how a robot like this would work in practice. The project envisions no central command for the modules, tasking them to decide as a collective how to assemble themselves to accomplish a goal. And Alberto Molina continues to work on the design, below is a demonstration of an improved clamping system that adds face rotation to the original design.
Modules making up a Dtto robot communicate wirelessly with one another, are inexpensive (a key of modular robotics), can be 3D printed easily, and are completely open-source from the hardware to the software. There have been several groups working on their own Dtto builds and proliferation like this will bring more hands to add to the software design and build on the great work already in place.
Limiting Factors We Need to Overcome
While the world of modular robotics continues to grow and expand, we can expect to see many developments in this field. For this concept to work, the modules need to get smaller and more compact while at the same time becoming stronger so they can move the bulk of a larger assembly. They will also need to improve their ability to communicate with each other, and support a larger and larger number of modules. Software for these swarms is at least equally as difficult a nut to crack as the hardware design — modular robots need to problem solve without even knowing what shape they will yet take.
But these issues are certainly worth our time and effort. The usefulness of a self-orienting robot that can overcome malfunctioning parts without intervention will be a game changer.
Robot Builders Wanted
As I mentioned earlier, the current challenge of the 2018 Hackaday Prize asks you to show off your own robotics design. Twenty people will walk away with a $1,000 cash prize and move onto the finals where the $50,000 Grand Prize and four other top prizes await.
Of course you can build a module-based robot like Dtto if you wish, and we’d love to see it! But the Robotics Module Challenge is open to many more concepts. It’s about open hardware designs that others can use in their projects, learn from, and respin for different purposes — from simple electronic boards, to complex assemblies, and everything in between. We want to see the neat tricks and good ideas that bring our robot filled future a bit closer to now.
Need a quick start? If you’re in the Bay Area, join us Saturday for the Beginning Robtics Workshop.
Is that third robot in Johny5 is intended ?
To me it seems the microbots of Big Hiro 6 are the inspiration…
A R T ….. https://vimeo.com/42048511
I tried to get a project going in the Silicon Valley Forth Interest Group in the 1980’s. National had come out with a single package sort of stacked dip that ran Forth. Forth can be entirely built from a very small set of primitives. I wanted to start defining a similar set of hardware and mechanical primitives. At the time, it was to be a set of primitives for spacecraft operation to reduce cost with off the shelf options that are plug-and-play and self calibrating – as in a pulse on a thruster is enough to determine moment of inertial, mass of the craft, etc.
There was no interest then. It looks like maybe there is no interest in this now.
There is surely no interest now, but what if the language was something like Lua instead? Then there might be lots of interest, depending on other factors.
My robot beats all these. How do I enter it?
Interesting. Now to use robots to perform task that chain gangs and mentally sane humans or even domesticated animals are better not to be doing, i.e. developing extremely cold/hot, deep sea, space based or interplanetary systems in those environments prior to humans even consider going. Oh wait… there are still to many Pan Troglodytes in human roles that hostile took over where humans once implemented and maintained… especially in first World countries… or at least extorted or bribed their way into those roles. Robots can’t be blackmailed or extorted or bribed if designed logically. Huh, logic. Thanks for the update on robots.
To deal with the computational aspect of a modular robot swarm, we should seriously consider a distributive approach. With an MCU like a cortex M7 or better in each module, a swarm should have a computation capacity to handle this well. We also need to build modules that have different capabilities that can be connected to the rest of the various robots in the swarm. There should be various locomotion modules using wheels and/or legs, modules that can grip objects, camera modules, pure and combination compute modules that may or may not have additional capabilities, etc. Pure compute modules may have much more powerful processors than others without compute capabilities. All modules would be able to connect to other modules, possibly including compatible modules made by others or other organizations.