We’ve seen many DIY headphones projects on these fair pages over the years, but not many that are quite as DIY as the Ploopy Headphones. What makes this project interesting is the sheer depth of the construction, with every single part being made from what we might call base materials. Materials such as 3D printer filament, foam and felt, and the usual metallic vitamins.
The electronics are fairly straightforward, with an RP2040 functioning as the USB audio interface and equalizer function. Audio samples are emitted as I2S into a PCM3050 24-bit stereo codec which generates a pair of differential output audio signals. These are then converted from differential to single-ended signals and passed on to the coil drivers. The coil drivers consist of no fewer than eight-paralleled opamps per channel. All of this is powered by the USB-C connection to the host computer. Whilst a kit of parts is available for this, you can make your own if you wish, as the full source (Altium designer needed for tweaks) is available on the Ploopy headphone GitHub.
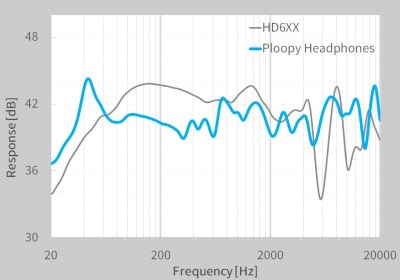
Many DIY headphone builds would likely be using off-the-shelf speaker units, with large parts of the ear cups being taken from spare parts kits for commercial offerings. But not the Ploopy. The drivers are constructed from flex PCB coils with a standard TRRS jack on each side. Magnets for these coils to react against are held in a 3D-printed frame that is attached to the outer cover. The coils are aligned with a special jig and bonded to the ‘driver foam’ with some 3M VHB tape.
The ear cups are constructed with some 3D printed rings, foam pieces, and simple woven material. The resonator plates push into the inner side of the cup, and the assembly simply screws to the driver assembly. The incredibly detailed assembly wiki makes it look easy, but we reckon there are a few tricky steps in there to trip the unwary. The headband again consists of printed spring sections, some woven material, and foam with a few metallic vitamins thrown in. That makes it sounds simple, but it isn’t.
On the whole the build looks fantastic, but what does it sound like? The Ploopy team has tested them against a pair of Sennheiser HDRXX giving a broadly comparable response, but we’re no audio experts, and the proof, as always, is in the wearing. This project seems to be the ultimate in audio tweakability, with the punchy RP2040 capable of running six audio filters at the full 48 KHz, 16-bit audio, though, the PCM3050 is capable of more.
Want to build some headphones, but need a Bluetooth interface? We got you covered. Can 3D printed headphones ever compare to the big names? We’ll see.
I glanced through their wiki and it looks like the diaphragm is foam. Is this normal? Am I completely misunderstanding how these work? I have to admit I don’t have a very deep understanding of how speakers work.
Diaphragm is made of flexible PCB. It’s glued to the foam which just holds it in magnetic field while providing enough flexibility for it to move…
no, it is foam and the coil section is pcb.
The foam is acoustically transparent and serves only as suspension. These drivers are called planar or “isodynamic”, the latter because the whole diafragm is driven with approximately the same force so it deforms less.
The driver flex board is what the diaphragm and coils are in a conventional speaker.
The role of the foam might be some kind of acoustic and mechanical dampener similar to the corrugated part of the conventional speaker diaphragm. I do not think it is a good long-term design choice (can not bear to many load changes and often disintegrates chemically over time).
the foam takes the place of a cone in a typical speaker
No. The flex PCB is both the driver and ‘cone’ (these are PMDs, there is no discrete separation between driver and driven surface). The foam is analogous to the rubber flex boot around the edge of the cone in a traditional driver. It’s purpose is mechanical, not acoustic. The foam is used as an alternative to a tensioned membrane, because tensioned membranes are a pain to fabricate.
It must have good bass, at one frequency. It shows on the graph. Resonator, that’s what organ pipes do. It’s supposed to be a acoustic coupler from a driven mass to air at all frequencies without resonating. Foam may help dampen the even worse resonance without.
This looks like an excellent job. If that bump at 31 Hz can be tamed, I’d call the headphones better than Sennheiser.
As they are likely easily customizable, inbuilt frequency tuning is likely possible. Think of an EQ filter, but as a physical arrangement of cavities/bumps/channels. Would be the closest thing to *perfect* response
In fact, it’s already been done: https://www.youtube.com/watch?v=7JbN9vXxGYE
Or, since they contain an internal uC able to run digital filters: even the response out to linear (with a small impact to absolute max volume) using inverse filtering and skip all the tedious mechanical tweaking.
Great work !! I love the whole concept. Let’s rename it as “The-no-bullshit-headphones”.
I got a question: When you receive the audio packet you cut the gain by 2 to… “fix digital distortion bug”. It seems a lot of resolution is lost here. Is there another way around ? And could you please explain why is it required ? Thx
The no bullshit headphones exists, but you have to look at the prof sector. I’ve got a Sennheiser HD25-1 and it is as utilitarian as you can get. all parts are available separately if something breaks. and the fun is: they are often cheaper than the consumer stuff.
Why does the article mention 16-bit audio when the chip is capable of 24 bit? 24 bit has a greater dynamic and seems preferable.
I consider the 24bit audio output a gimmick. You will need > 96 dB SINR in order to be able to discern them. That essentially means > 100 dB volume level, which is a great way to cause hearing loss.