Most people probably don’t think about springs until one kinks up or snaps, but most of the world’s springs are pretty crucial. The ones that aren’t go by the name Slinky.
We all use and encounter dozens of different types of springs every day without realizing it. Look inside the world of springs and you’ll find hundreds of variations on the theme of bounce. The principle of the spring is simple enough that it can be extended to almost any shape and size that can be imagined and machined. Because it can take so many forms, the spring as a mechanism has thousands of applications. Look under your car, take apart a retractable pen, open up a stapler, an oven door, or a safety pin, and you’ll find a spring or two.
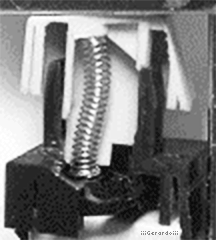
What is a Spring?
Technically speaking, a spring is an elastic object that stores mechanical energy and releases it when compressed, stretched, or twisted. The oldest form of spring known to man is likely the archery bow, followed by the flat springs of Bronze Age tweezers. Ancient Roman carriages used leaf spring suspensions for a smoother ride on those rocky roads.
Coiled springs, now the most common and identifiable, were first used in the 15th century in locks and clocks. In the 1800s, they began to pop up in beds and furniture. By the 1980s, they were buckling regularly inside of IBM keyboards.
Springs can be classified by their shape, their makeup, and their intended use. Most springs are either coiled or flat, but there are legions of custom springs in various shapes. The main uses of springs include returning something to its starting position, like a screen door; measuring force, like a scale; and storing energy for later use, like in a mechanical watch or a wind-up toy.
Springs are most often made from either metal or plastic; the choice depends on the intended application and environment. The majority are made from spring steel, which is a cold-drawn carbon steel alloy. Springs made from copper alloys like phosphorus bronze and beryllium copper provide high electrical and thermal conductivity. Plastic springs may seem impractical, but they’re quite useful in sensitive applications like food processing and x-ray equipment that call for non-metallic mechanisms made from inert materials.
No matter the composition, a good spring is one that can return to equilibrium again and again without any lasting dimensional damage. A well-designed spring should perform for a long time, which is probably why so many go unnoticed and unconsidered until they break.
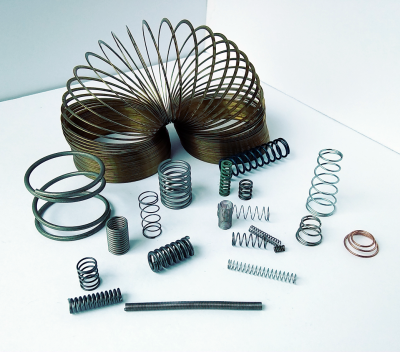
Which Spring is Which?
Ask someone to draw a spring, and they will probably scribble out a compression spring. When squeezed or compressed, they get shorter. These are easily the most common and are found in everything from retractable pens to soap dispensers to pinball plungers to car suspensions.
The Slinky is a pre-compressed helical spring whose properties were toyed with to make it walk down stairs as slinkily as possible. Take the batteries out of something and you’ll probably find conical compression spring terminals that compress more flatly to save space.
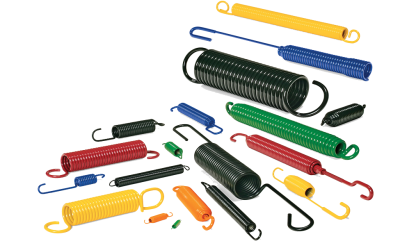
Extension springs are the second most common. When stretched or pulled, they get longer. These are the springs that snap your screen door shut and give bounce to your trampoline. They are made much the same way as compression springs. The main difference is that extension springs have hooks or ears on the ends for connecting to the load or loads that will extend them. These ears are made by bending one or more of the end coils out, usually perpendicular the orientation of the remaining coils.
The other difference is the space between the coils. A compression spring is made to compress, so the coils are spaced wide enough to give room for compression. An extension spring is made to extend, so the coils touch in their unstretched position.
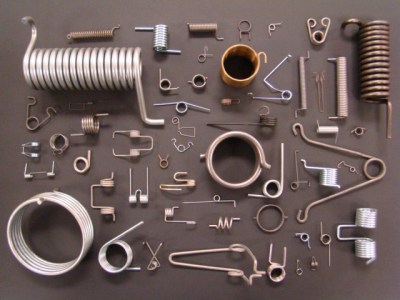
Torsion springs resemble compression springs, but are activated differently. Whereas compression strings are stressed in torsion, or by twisting the elastic material, torsion springs are stressed in bending. They are found in clothespins, pop-up electronics, and lots of other things with jaws.
The load is applied to the spring legs in the direction of the coil windings. Torsion springs are like little wound-up cantilevers that either supply torque, as in the clothespin, or withstand it as in the staple remover.
Another common torsion configuration is the torsion bar, used in some car suspensions and in the gullwing doors of the DeLorean DMC-12. Torsion springs can be flat, too, like the hairsprings in mechanical clocks, music boxes, and other wind-up toys.
The leaf spring is a type of non-torsional flat spring. Trucks and other large vehicles often have leaf spring suspensions that transfer the load evenly across the chassis.
The more complicated something is, the more springs it is likely to have. The same goes for the types of springs involved. It all depends on the need. A stapler has two: an extension spring that advances the magazine, and a leaf spring that returns the stapler to the ready position. Cars and cassette players each have many different springs, though the average car has it outnumbered by a few hundred.
These Are a Few of My Favorite Springs
Many things require specialized spring action, and for that there are many kinds of special springs, one-offs, and purpose-built wireforms, such as cotter pins or the handles of a binder clip. Springs can also be machined from a single piece of stock.
Wave springs are used in place of compression springs where tight load deflection is needed in a small space. Some electric motors pre-load their bearings with a type of wave spring that lowers noise.
Serpentine springs are the zig-zagging kind that chair and couch suspensions are made of. I suspect that the common potato masher design was based on such a spring.
Volute springs resemble a collapsible cup, and double volute springs look like croissants. Many types of tanks use volute spring suspensions in both vertical and horizontal configurations. That pair of hand pruners in your garage probably has a double volute; they don’t seem to be used for much else.
The weirdest one might be the Belleville washer. These are conical disks that are stacked up in various configurations to provide different types of bounce and are most commonly found in land mines.
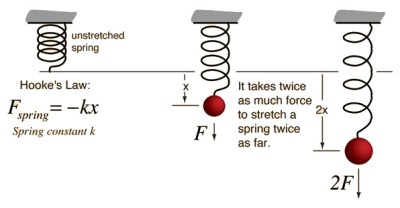
How it Works: Springs
So what gives springs their resiliency and bounce? In the case of spring steel, the elasticity is a function of the way the molecules interact. At rest, the attracting and repelling forces within are balanced.
When a compression spring is squeezed, the repelling force builds, and releasing the spring pushes the molecules apart. In an extension spring, stretching the coils builds up the attracting force, and releasing the spring pulls the molecules together.
Whenever a force acts upon a spring of any kind, the amount of movement that results in the spring is known as its deflection. Most springs actuated within their elastic limit will obey Hooke’s Law, which states that the force (F) needed to compress or extend a spring is equal to the product of the spring constant (k) times the distance traveled (x) (aka its deflection). In other words, the compression or extension of any spring is proportional to its force.
Not all of the coils of a spring will distort under load. Any spring with closed ends will have inactive coils that don’t take any stress. Perhaps most importantly, spring designs must take into account the number of active coils needed to do the work.
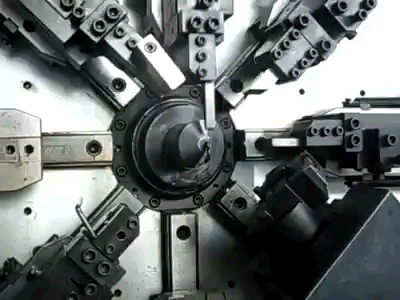
How It’s Made: Springs
For product manufacturers, there’s no off-the-shelf solution for designs that call for springs. Their springs have to be made to order based on the desired dimensions and deflection.
Metal springs start with a coil of drawn steel cord that’s either round, square, or rectangular in profile. The cord is fed into a forming machine that has been set up to make a specific type of spring. The machine might take an hour or more to set up, but once it’s dialed in, it can make tens of thousands of springs per hour.
Compression springs are simply coiled with the desired end formations and cut. When making extension springs, the machine will bend the first coil or two out at a 90° angle to form a hook. Then it coils the rest of the spring, forms the other hook, and cuts it. Some hooks are formed by hand, depending on the material and customer spec.
The finished springs are then heated to relax the metal, which relieves the stresses from coiling and helps them retain their shape after flexing. Some springs are blasted with a high-speed stream of pellets for added strength in a process called shot-peening.
Most consumer-level springs are cold-wound. For wire diameters above 16 mm, they are hot-wound as you can see below. Hot-wound springs are found in automobiles, farm and construction equipment, and locomotive suspensions.
Roll Your Own Coils
Let’s say you have some design that could benefit from springiness. If you can’t find the one you need in that spring assortment from Microcenter, you can make your own out of music wire if you have access to a lathe and a mandrel. [ThisOldTony] can help with the details. Have you made your own springs? Let us know in the comments.
Though we have just begun to scratch the surface of the subject of springs, we hope you’ve gained respect for these hard-working mechanisms.
” Ancient Roman carriages used leaf spring suspensions for a smoother ride on those rocky roads.”
I’ve always found it amusing when reading a piece of fiction that has a carriage in it in which a rough ride is part of the narrative.
That would be because of the roughness of the roads of the day rather than a lack of suspension. Smooth roads weren’t really necessary until bicycles and automobiles started turning up.
https://upload.wikimedia.org/wikipedia/commons/8/8c/PompeiiStreet.jpg Singing, the bicycle built for two…legionaries. ;-)
I mean it would still be pretty rough compared to what we’re used to. They still had wood-spoked wheels with perhaps a metal band around them. And those early leaf springs most likely didn’t have a lot of give or travel.
I recently saw a Clint Eastwood western set in the middle of the 19th century. The seat of a horse drawn cart or open carriage was held up by paired leaf springs that probably had a foot of travel. What would have made the ride unpleasant was the lack of damping.
Spring is in the air
She had me at “These are a few of my favorite springs”
B^)
Tis the season to loosen up on the tension, cycle that rhythm and relax for an even ride for the long term… not forgetting k. Note: Think repeating what I wrote sounding like Barry White.
Boing.
Cing! (circlip goes supersonic)
“Jesus Clip”, as in “Jesus, Where Did hat Clip Go”?
Yup, that’s the one.Only that I call it Einstein-Rosen bridge generator despite it’s shape.
You did not mention ceramic springs. My Father and I invented those back in the mid 1980’s. They were precision machined from transformation toughened zirconium oxide using diamond tooling. We made many coil springs to exact customer specifications including one that flew on Space Shuttle mission STS-60 in 1994. These springs could take over 3,500 degrees F, and are not bothered by acid, and have a very low thermal coefficient of expansion and do not suffer from metal fatigue. One of them we made was 6″ long and could compress to 3″ long. This was an incredible breakthrough as before this, the only way they had tried to make springs was by winding some prefired material around a coil form and then firing it. These did not spring much at all and were very unpredictable in their properties. We also made some from aluminum oxide as well. I should do a write up for Hackaday on these as I still have a few of them laying about and I am still amazed at what they can do.
Clifford, is that you?
I have no idea who Cliffird might be…sorry. My name is Bill
Lol, I was referring to this paper from 1979
https://link.springer.com/article/10.1007/BF02833979
Looks like ceramic springs might have been invented before you guys.
Ah, sorry. yes, I have seen that paper…it’s been a while but, those “springs” were not machined and they looked a lot better on paper than when they tried to produce them.
+1
That’s super interesting, never even heard of such a thing. Which is unsurprising considering their niche applications, but it’s great that such things are manufacturable. Well done.
Thank you very much. They were/are very expensive to make but, for many applications, especially in aerospace, they were the only part that would do the job. DARPA wanted to use them in anti-personnel mines because the spring was the only part detectable with a metal detector and, I was not happy about that. We supplied them to Coors and Corning Glass, two giants in the ceramic industry that could not make them themselves. An engineer at Coors told me they had been trying for years.
Why didn’t you refuse to sell to DARPA?
Well, in a way, we did. They did not want to pay what it cost to make them so, that project ended up going nowhere anyway.
I just thought how a really expensive part could have been used in a cheap, mass produced thing like such a mine. But financial calculation in weaponry is not always easy to understand.
That’s neat. I learned something new and will keep in mind.
Believe me, I wanted to. That’s a great story!
Thank you Kristina.
Solid aluminum oxide machined springs using monocrystaline diamond tooling? I’ve used MCD tools before, but I’ve never heard of sapphire springs before, and that’s essentially what this sounds like. Article please!
Well, we never made sapphire springs as sapphire is single crystal al203 and does not have the properties required for a successful spring. Alumina, which is poly crystal al203, does but they are not very strong whereas transformation toughened zirconium oxide has the perfect properties for this application. We made some aluminum oxide (99.7%) springs for Coors, one of the best manufacturers of technical ceramic materials in the world. but I have no idea what their application was. If you, or someone could tell me how to post photos here (do I need a host site like photobucket?) I will take some and show you. I still have some smaller versions sitting right on my shelf.
I remember Tomorrow’s world, doing a peice on refined cement, springs . Might have been ceramic. Was that your work?
No, we were in the technical ceramics field working with materials like aluminum oxide (99.7%, 99.5% and 96%.) zirconium oxide, iron oxide, YIG (yttrium iron garnet) YAG, (yttrium aluminum garnet, sapphire, etc. These are very specific materials with exact properties and values as are published by their manufacturers and used in the aerospace and electronics industries.
I was wondering if this “transformation toughened zirconium oxide” can (and could you reference the patents as I am wondering if can be made for hobby apps in the home shop) be used for pulse jet reeds since those are springs.
I guess that would be another spring not noted also. Reed valves.
I was also wondering about lining of the interior pipe of the pulse jet and wondering what your thoughts are as I first think better reflectors like silica glass with other additives that would insulated better like zirconium oxide… though my budget is more like talc, titanium dioxide, aluminum oxide, etc. and not absorb like say silicon carbide. However, some glaze materials and other applications I find a more reasonable priced higher dollar oxide source though wonder if impurities will turn the material into a flux instead of a insulator. I might be thinking wrong though as I haven’t worked in the foundries lab for for years… about the time since I worked on the pulse jet.
https://www.facebook.com/photo.php?fbid=2537045099690610&set=p.2537045099690610&type=3&ifg=1
Better image for the reed: https://www.facebook.com/photo.php?fbid=2538892792839174&set=pcb.719059788218336&type=3&theater&ifg=1
Note that this Pulse Jet FB site is impressive and sure does bring back memories. I still have to photo graph all my plans as I have a lot of the same info as I’m sure many of us who got into the hobby at the time.
https://patents.justia.com/patent/4771022
https://encrypted.google.com/patents/EP0279102A3?cl=tr
I found these two pretty quickly. The 2nd one by Corning is I think when they created a spin-off company to produce “Zycron” which actually was one of the first materials I decided to use to try to make a precision machined ceramic spring and it worked. They were never able to produce springs so, they had us make them for them. I do not think there is any way possible to make these materials in the home shop due to the pressures and temperatures required. Also, each material takes a very specific and well researched firing curve/cycle or all of the properties will be way off. Back in the 80’s, I thought about making some reed valve petals for a pulse jet from these materials but it turned out not to be a good application due to the mechanical shock involved.
To brittle over time at the higher temperatures or some sort of jerk or snap material specific issue?
Have you tried any coatings are are the thermal expansion and contraction properties to different to coat on another suitable or the optimal current market reed material?
How about as a reflector plate just inside the reed valves? The gentleman noted he is using a reflector plate in his FB Pulse Jet Group specific pulse jet in a comment on one of my posts referencing this HaD article.
I was also wondering about coatings for on the inside too.
Isn’t the phase changes of materials amazing at higher temperatures along with their final STP or designed operating conditions properties. Just amazes me the different phases that most aren’t even aware of… other than maybe water being more publicly published as having a bunch of phases outside of the traditional three (solid, liquid, gas) or maybe fourth for some (plasma). Mu-metal heat treating might be for some or the opposite Metglas rapid solidification manufacture also more well known in electronics industries.
I volunteered firing the kiln at Lake Michigan College when I was going to school there since I had two work study positions also so was around campus more off times. Is interesting bridging the foundry, heat treating and ceramics for… other than pressure controls… the potential home advanced complex using social electronic media support tech workshop.
I’ll have to read into high pressure and controlled critically high temperature furnace operations. There must be a way that isn’t dangerous. :-)
Thanks for the reply also. The information is kindly very much appreciated. There has to be some area of opportunity and I’m used to tolerance and confidence statistical intervals to push the boundaries of what couldn’t be done last week.
@PirateLabs Are you still active on this website? I have some questions about the zirconium springs!
Piano wire comes in many gages and makes excellent springs and stiff tool points. A rod in a vise held drill will do without a lathe. Bend a 90 degree end and stick the end into the chuck jaws and pull and wind. Angling the wind point will allow you to make stretched and compressed types.
Some guitar wire is coiled like a spring.
What happens if you make a spring of that?
Other than endless “I heard you like springs, dawg” and springception memes.
Probably some very poor properties unless you have very specific need for that kind of spring.
The coiled bit is coiled round a straight wire core, the coils have hardly any spring, they are just there to add weight/thickness. If the core snaps the coiled bit just gets pulled apart & goes floppy.
Thanks for pointing out some of the amazing uses of springs throughout history and in modern day applications. As a 4th generation spring maker (yes that is a thing), this article makes me bounce for joy.
I’m honored that you liked my article!
It probably put a spring in his step!
Belleville springs are most commonly found in car clutches in the uk, tho I guess this is regional as some areas no doubt have more landmines than manual vehicles.
Belleville springs are also used in high pressure steam valving.
They fit nicely around the valve stem.
Good call, never make that connection. I always called them concentric leaf springs or something like that since they’re split into pedal-like segments.
We don’t have many landmines or manual vehicles here in the US, but my BMW motorcycle has one. Which is strange for a bike. There are a lot of strange things on those boxers.
They often preload bolts. There are a number in the ISS docking systems.
While I understood they where springs when I first countered them, but I didn’t know they had the moniker Belleville Washers until now. My experiance with them is in their use in adjustable relief valves use in the oil field. In applications where to pressure was very high, and the amount of fluid being bypass could be measure in barrels. As in 42 gallons per barrel.. Torsion bars holding up gull wing doors sounds exotics, but the body part torsion bars hold up more is deck lids. The evolution of the springs that hold up vehicle hoods is interesting. At first they used that flat coils spring that quickly worn out be cause of the weight, so hinge that used linear coil springs was developed. When those proved to be too heavy duty when cars started shedding weight it as back to the flat coil springs. The reason the hoods GM pickups of the mid ’70s would buckle is that people where too lazy to go to center of the hood to pull it shut. worn out torsion bars that hold up pickup tool box lids can be pain
You left off a useful spring common in industrial and robotic design: constant force springs. They’re the wound spools of flat spring steel; you can find little ones inside of a retractable badge holder, keychain, or cable. Because the same amount of spring is deforming as it unrolls, you get the same force throughout the unrolling process. Using this, you can counter-load against gravity or make things that retract automatically in a smooth uniform motion.
I always wondered what the heck was inside those- just figured some variant of a measuring tape coil spring or something. Would love to see a diagram of that
Century Spring here in Los Angeles has my business.
https://youtu.be/XoSgeA4P9NY
Geez, all the way up to 2″ hot coil! Never have I wanted a catalog so much.
Well in my defense, they are here close by. I have been able to “Second Source” springs from Japan, simply by walking into the store. Amazing stock.
No offense but this reads like a high-/primary- school project paper, and with the mention of ‘cassette players’ it might indeed have been on the shelf a bit?
“The Slinky is a pre-compressed helical spring…”
Is this true? What does pre-compressed mean? Is this an extension spring?
Pre compressed means the spring actually wants to be shorter than it can physically be due to the coil thickness. When the spring is fully contracted the coils still have some residual force pushing the spring coils together. And yes, a slinky is an extension spring.
Don’t forget Jam Handy’s rendition of Spring Fever
https://archive.org/details/0141_Case_of_Spring_Fever_A_M00910_08_28_42_00
One thing I never found a reference for is spring efficiency — how much of the energy you put in comes back out as motion (as opposed to heat). Some springs are designed to be inefficient.
I made a spring before with steel wire.. I had the wire fully annealed, then slow cooled. Then i coiled it up around a round rod, annealed it again, then tempered it till it turned blue. turned out pretty good. the size of spring was pretty small as i was doing this with a propane torch and i’m limited by the size of the flame i could make.
Coil Springs Largely are Torsion Springs.
They are just coiled up nice and neat.
I did finite element analysis on them. The tension is in the outer surfaces working its way inward.
Many things use rubber in place of a spring… If it’s rubber, is it still a spring? I replaced my bicycle suspension with rubber anti vibration mounts + a 3d printed mount. Rubber seems to have better damping on its own.
I watched several of those spring machines work work during a supplier visit. It wasn’t quite the process I expected, but fascinating to watch. You can learn a lot by visiting suppliers.
It’s worth mentioning one source for tiny leaf springs is the bristles left behind by a passing street sweeper.
Very Interesting,