Since humans first starting playing with electricity, we’ve proven ourselves pretty clever at finding ways to harness that power and turn it into motion. Electric motors of every type move the world, but they are far from the only way to put electricity into motion. When you want continuous rotation, a motor is the way to go. But for simpler on and off applications, where fine control of position is not critical, a solenoid is more like what you need. These electromagnetic devices are found everywhere and they’re next in our series on useful mechanisms.
A Coil and a Plunger
A physicist will tell you a solenoid simply a coil of wire through which current can be passed. That’s it. Other than in the physics lab, though, such a simple device is not of much mechanical use, so what we tend to think of as a solenoid is slightly more complicated. A practical solenoid has a coil, but it’s also going to have several mechanical parts to make it work as an actuator.
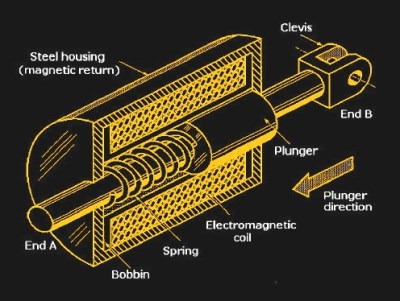
A plunger solenoid is a good example of the basics. The air core of the solenoid’s coil is partially occupied by an iron or mild steel plunger, held in place by a return spring. When current is applied to the coil, a magnetic field forms, and the plunger is pulled forcefully into the solenoid’s core. When current stops flowing, the magnetic field collapses, and the return spring forces the plunger back to the resting state. This is characteristic of most solenoids — they’re either actuated or they’re not. This makes them great for jobs that require something to be positioned in either one position or another over a short distance, like valves that stop the flow of liquid through a pipe or tubing.
Plunger solenoids range in size from the very tiny to the ludicrously large. On the small side, plunger solenoids see service as actuators for microfluidics valves in scientific and medical applications, and in the drive head for the impact style of dot-matrix printers (yes, each one of those dots is the plunger of a solenoid).
You likely interact with medium-sized solenoids on a daily basis. The click at the beginning and end of your refrigerator’s ice maker is what switches the water on and off to refill the tray. You’ll hear a similar click in fountain soda machines. And those pinball wizards among us will attest that the forces throwing that silver ball around the playfield are generated by solenoids.
Stepping up the scale, there’s a fairly large solenoid inside the starter motor of almost every car and truck on the road, at least those with internal combustion engines. The solenoid sits atop the starter motor and is responsible for connecting and disconnecting the starter from the system. The solenoid’s plunger is attached to the motor drive shaft via a lever. When the ignition key is turned, the solenoid coil is energized, pulling the plunger in and moving the lever out along the now-spinning motor shaft. This drives a pinion gear out to engage with the engine flywheel to crank the engine until it starts.
Solenoid Styles
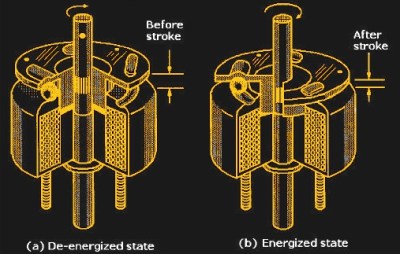
Other styles of solenoid are available, including rotary solenoids. These are exactly what they sound like: actuators that can rotate between two positions. Designs vary, but the most common types have a permanent magnet rotor on a shaft inside the solenoid’s core. When the coil is energized, the rotor experiences a torque due to the magnetic field, much like the rotor of a permanent magnet motor. The rotor only moves to a physical stop, though, and is returned to the resting position by a spring when the coil is de-energized. If the polarity of the coil is reversed, then the rotor and shaft can swing the other way, making this style of rotary solenoid bistable. Other rotary solenoids use a metal disc with ramped grooves and ball bearings; when the plunger is sucked into the core, the ball bearings force the disc and shaft to rotate along the grooves.
AC, DC, and Snubbing
As electrically simple devices, solenoids can run on either AC or DC. A DC solenoid tends to be quieter because the magnetic field is constant while the coil is energized. An AC solenoid tends to chatter as the magnetic field varies and the force of the return spring overcomes it at the instant the current changes direction in the coil. This tendency can be mitigated by the use of a shading ring to alter the magnetic circuit of AC solenoids. A shading ring is just a small copper ring that sits inside the core of the solenoid so it contacts the plunger when it’s fully retracted. The magnetic field of the energized coil induces a current inside the ring, which in turn creates its own magnetic field that lags the phase of the solenoid’s field by 90°. When the solenoid’s field falls to zero as the AC waveform passes the zero point, the magnetic flux from the shading ring keeps the solenoid retracted, eliminating the bothersome chatter.
While any solenoid will run on AC or DC, care needs to be taken to observe the coil’s specs. Solenoids represent an inductive load, and so their impedance is much higher in AC applications. So if a solenoid rated for 24 VAC were powered by 24 VDC, it would probably burn out quickly as the current through it would exceed the design specs. This could be avoided with a current limiting resistor or by lowering the DC supply voltage.
Like their cousin the relay, solenoids have the potential to damage whatever circuit is controlling them. When the current flowing through a solenoid or relay coil is removed, the voltage spikes as the magnetic field collapses. If that spike gets into sensitive components, like a transistor driving the coil, the device could be destroyed. The classic remedy for this with DC coils is the snubber diode, connected in parallel across the coil with the anode on the negative side. The snubber gives the induced current somewhere to go when the power is removed from the coil to prevent it from inducing the high voltage spike. Snubber diodes won’t work on AC coils, so an RC snubber, with a small resistance and capacitance in series with each other placed in parallel across the coil, serves the same purpose.
This is only a brief look at what solenoids are and do, and how to incorporate these mechanisms into your designs.
“The solenoid sits atop the starter motor and is responsible for connecting and disconnecting the starter from the system. ”
In the case of older Fords, the “solenoid” was an electromagnetic relay that engaged the starter motor, centrifugal force pulled the starter gear to the flywheel and the Bendix spring pulled the starter gear back when the flywheel rotated faster than the starter.
This is still the predominant design in small engines. No need for a starter solenoid on something small. By small i would say under 30hp.
Older is relative. One type of ford starter used one o it’s field windings to pull in a plunger connected to linkage that engaged the pinion gear before completing the electrical circuit to the motor armature. In effect a solenoid hidden in plain sight.
Older again …my first scavenged solenoids were from old, dumped (discarded) cars. That was a long time ago and the cars were already fairly well rusted and gutted. The solenoids were the actuators for the “pointing finger” indicators which were common in the days before flashing indicator lamps front and back were standard. They were common in the “boxy” cars built in the 20s and 30s and were generally situated in the centre column separating the front and rear doors. One is visible here (https://en.wikipedia.org/wiki/Lanchester_Ten#/media/File:Lanchester_10_first_registered_Dec_1935_1203cc.JPG) just behind the driver’s side window.
Fairly easy to remove (especially when you didn’t have to worry about scratching the paintwork) and great fun to experiment with, using one of the chunky, 9v “lantern” batteries which used to be commonly available in the 60s.
“The solenoids were the actuators for the “pointing finger” indicators which were common in the days before flashing indicator lamps front and back were standard. ”
FYI, I believe they are called semaphores…
at least that is what VW aficionados call them.
Granda has a few cars with these. they always stick so we hand signal anyway
Two fingers are always better than one for hand signals anyway. :-)
The ‘moving pole piece’ as Ford called it. The starter ‘solenoid’ is actually a high current relay to switch the battery directly to the starter.
The magnetic current in the field coil pulls the coil’s core down. A lever on the other side of the core’s pivot pushes the Bendix drive into engagement with the ring gear.
Ford starter ‘solenoids’ have been a common quick fix for GM starters when the contacts inside their starter mounted solenoids get burnt to where they don’t work. That can also be done when installing a new starter or building a custom car as preventing the need for ever* having to replace your GM starter or solenoid. Google ford starter solenoid on chevy
*Barring mechanical wear or failure of the armature or solenoid windings or the carbon brushes.
My first encounter with a snubber diode was on the track changing solenoid of an 8-track player.
“These electromagnetic devices are found everywhere and they’re next in our series on useful mechanisms.”
Achieved with hydraulics as well.
I would say more often pneumatics. Pneumatics are generally an all or nothing affair like most solenoids. If you are using hydraulics you probably want some control of the motion.
Hydraulics and Pneumatics are both actuated by an electromechanical solenoid built into a valve.
Only in larger more complicated applications, plenty that are controlled with hand operated valves.
Maybe not in modern tractors, but most of the farm tractor implements as well as skid steer loaders were all manual up to 20 years ago (now sure about how they are done now, I wouldn’t be surprised it “fly by wire” has taken a hold in modern farming.)
Or “Trafficators”, apparently (although I don’t remember hearing either term …but then there’s a lot I don’t remember nowadays :-)) https://en.wikipedia.org/wiki/Trafficators
More ways than just solenoid valves. There are hand operated valves, servo operated valves with full position control loops for hydraulics, mechanical control valves and even pneumatically operated valves using air logic systems.
I love you Jeri…You make everything make sense.
I love her too, but she didn’t write this article…
(Due to the Restraining Order, I can comment no further B^)
I watched that video to see more of that rather nice looking scope which turns out to be a Tektronix.
Then elsewhere I got inundated with Tektronix ads which I have never had before.
So have I just been tricked into watching an ad? And was HaD implicit in this – is this “educational” article really just to trick us into watching an ad?
Honest ads are one thing and I understand their reason for existing but I will not stand for being tricked into watching or reading them. I have a choice what I read and watch.
for a start, install ghostery – it blocks the FIVE active tracking things that hackaday seem to use…
Believe me, 5 is a low low number of trackers, most modern websites have 10-20 layers of crap in them.
Ghostery + NoScript will amaze you at just how f***ed up the internet is.
I really miss Controle de Scripts. That browser addon allowed fine control of what scripting was allowed to do, or not do. It could block ALL non-user-initiated popups, popunders, and auto-forwards and other annoying/dangerous automatic crap, while still allowing user-initiated (things you wanted to happen because YOU clicked something) actions to work.
Many years ago I used to repair cassette tape units in old NCR mainframe computers! One thing I remember vividly was that a large current pulse was applied (for some 200 ms) to actuate the solenoid, but then the current was reduced to a small fraction (maybe 1/4 of the peak?) to keep the solenoid actuated (the force on the plunger being stronger when it is already inside?). Clever design to mitigate thermal issues of a solenoid powered for a long period of time…
low impedance automotive fuel injectors are driven this way, its called “peak and hold”. Nowadays injector design is better so injectors are high impedance and just run straight 12v.
However, most current automotive starters actually use this technique, the solenoid is wired in series with the main motor. when the solenoid engages, the main motor is essentially a short so the solenoid see’s 12v when the solenoid fully engages it is essentially shorting itself out but the voltage drop across the contacts and little bit of wiring is enough to keep the solenoid engaged. the resulting phenomenon is when the contacts in the solenoid burn out(or the solenoid siezes) and the motor is ok, when you turn the key to crank the motor will turn real slow.
fuel injectors: That depends. AFAIK in common rail diesel they still have to do peak and hold. These injectors have to move very quickly and control pressures up to 1000bar and more in ms. Often there are several injections in one compression-work cycle. They are kicked with really high power, can be up to a kW and the demagnetization energy gets recovered. First reason for this is to demagnetize against a high voltage (faster) and second of course to save energy.
starter solenoid: typically it has two windings, the strong, pull-in winding is shorted out like you describe, but there is a hold winding.
In a pinball machine the flipper-arm also has two windings, the strong one is switched off with a limit switch contact.
Mostly correct but maybe not for the reason you think. The speed that a solenoid will achieve pulling in is a function of the current in the coil (among other things) and the current in the coil can only build as fast as the inductance of the coil will allow. If you assume the inductance of the coil is constant and independent of the plunger position then the current will build up as described: I = L * V / t so the current (and plunger force) will build more quickly if the inductance L is reduced or the voltage V is increased.
Peak and hold is used fairly widely for solenoids as well as larger stepper motors among other things but has the disadvantage of dual voltage driving the coil which complicates the driver design whereas a dual coil system can use a fast coil with low inductance with a slower coil catching up a short time later and both coil drives only need to be the same simple driver circuit in many instances. That is unless fast reset of the plunger is also required. If that is so then the same equation above applies and the forward voltage of the ‘snubber’ diode clamps V to a low value which makes the decay of the magnetic field quite gentle and therefore the release of the plunger is delayed.
Unfortunately, the inductance is not (and cannot be) constant so it is just not this simple. If the inductance were in fact constant and independent of the plunger position then the plunger would experience no force at all. The force the plunger feels is proportional to the change in inductance relative to the change in position, or dL/dx. The end result is that as the current builds and the plunger moves in response the inductance increases which slows the rate at which the current is increasing and thereby slows the response of the solenoid. The mathematics to describe these effects and the reactions of the plunger are somewhat more complex. I suggest a good text on the subject if interested to satisfy your curiosity.
I am not a fan of the term ‘snubber diode’ as it seems confusing to me. I find ‘freewheeling diode’ less ambiguous and less likely to be confused with the diode in a low loss snubber. An RC snubber is rarely ever used in a DC solenoid situation and actually has two purposes in a typical AC circuit: one is to present an instantaneous current to a thyristor to meet the holding current specification for the thyristor until the coil current can take over and the other purpose is to dissipate the energy from the coil when de-energised. When a coil is de-energised while it has a magnetic field built up, the magnetic energy must be dissipated somewhere. The snubber capacitor is chosen to be of a big enough value to absorb that energy and the resistor is chosen to dampen the second order circuit formed by the snubber capacitor and the coil to a value typically around critical damping (approx 0.7) or more up to around Bessel damping (approx 0.86). Any more than that is overachieving and likely to represent excessive power dissipation in the resistor under normal energised coil conditions (in AC circuits of course).
I hope that wasn’t an excruciatingly dull read and I hope maybe I’ve made a few converts away from ‘snubber’ diode when ‘freewheeling’, ‘catch’, ‘back EMF’ or even ‘anti-parallel’ are much better terms. :-)
can a solenoid be hacked to make a rail gun?
No. As the name implies, a rail gun needs rails, thick heavy copper rails. You could hack solenoids to a coil gun. A simple one stage CG is not more than a solenoid with a free moving plunger.
Cue ElectroBoom and his mini coil projectile launcher:
https://www.youtube.com/watch?v=mdZo_keUoEs
If you disconnect the bit holding the plunger on, it can’t NOT be a rail gun.
[if you want a boring answer, you’re tallking about a coil gun / Gauss gun, rather than a rail gun. They use coils just like that, but designed to have particularly good characteristics for firing projectiles]
The function of solenoids is replicated in things like central-locking actuators by a small motor. Not as fast to operate, but still plenty quick enough. Operating current is lower and they have much better ‘stroke’ power (the pull power at the maximum extent is the same as the minimum extent), and most operate push-pull. With some smarts, they can also do position (ie: partial plunger movement) useful for control of hydraulic systems in tractors etc.
Unless a rapid response (such as fuel injectors) is required, they are almost the go-to now.
Interesting start to solenoids.
Any chance of a follow-up article talking more about their pros and cons, how to spec them and design mechanisms for them, etc? That’s the stuff that always stumps me. Typically a solenoid feels strong or is strong on paper, but fails to actuate a mechanism.
V8 solenoid engine. https://www.youtube.com/watch?v=uhYEdD94vH0
When is someone going to build such a setup inside an internal combustion engine? Now that would really be an electric conversion. Start with the basics, convert a single cylinder Briggs & Stratton, then do a V-twin. Work up to an inline 4 cylinder car engine, then a V6 or V8.
Wouldn’t that be fun at a car show? Hot rod looks like it has the common 350ci Chevy but it’s really an electric solenoid motor.
Another way many of us probably interact with solenoids every day: card access. Electric strikes and (some) electrified crash bars make use of solenoids for locking/unlocking.