Let’s say you’ve gone and bought yourself a sweet sweet metal lathe. Maybe it’s one of the new price-conscious Asian models, or maybe it’s a lovely old cast iron beast that you found behind a foreclosed machine shop. You followed all the advice for setting it up, and now you’re ready to make chips, right? Well, not so fast. Unlike other big power tools, such as band saws or whatever people use to modify dead trees, machine tools need to be properly level. Not, “Hurr hurr my carpenter’s level says the bubble is in the middle”, but like really level.
This is especially true for lathes, but leveling is actually a proxy for something else. What you’re really doing is getting the entire machine in one plane. Leveling is a primitive way of removing twist from the structure. It may not seem like a huge piece of cast iron could possibly twist, but at very small scales it does! Everything is a spring, and imperceptible twist in the machine will show up as your lathe turning a couple thousandths of taper (cone) when it should be making perfect cylinders. All this is to say, before making chips, level your lathe. Let me show you the way.
If you have a bench-top machine, start by leveling the bench to pathetic carpenter’s standards. That is, level it with any old bubble level such that a pencil won’t roll off. Personally, all my benches use grade 8 bolts as feet, which makes leveling a breeze.
The next step is to acquire a quality machinist’s level. These differ from hardware store bubble levels in several key ways. First, they are incredibly sensitive, typically reading less than five thousandths of an inch displacement per foot (or less than 0.5mm per meter). Second, they can be self-calibrated. Third, they have precise ground surfaces on at least three sides, and a V-shaped bottom to minimize error from mating with the machine’s surface.
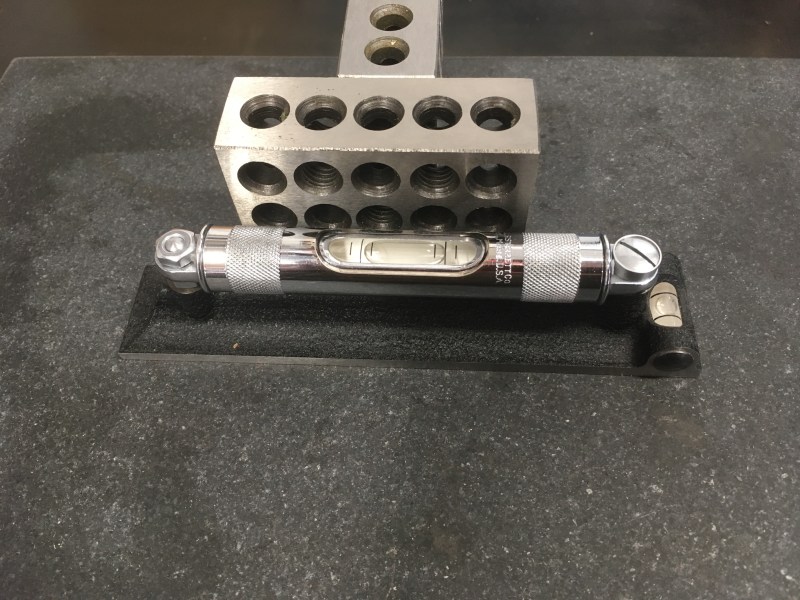
Calibrating the Level
Every time you use a machinist’s level, you need to calibrate it. The cool thing about a level is that they are “self-proving”. Here’s how that works.
First, place the level on a clean and dry granite surface plate. Rotate the level until you find an axis that is level. There will always be one, because the granite plate is a plane (as good a one as humans can make anyway) and any plane will have one axis that reads level.
Next, place a heavy straight edge against the level, such as a 1-2-3 block or an angle plate. This holds your reference. Now you can flip the level 180°, place against the reference edge, and check it again. Using the calibration screw on the level, split the difference so the bubble reads halfway between those two readings. You’ll need to go back and forth a few times. Try to touch the level as little as possible. The heat from your hands will warm it up and cause it to change shape sufficiently to lose your calibration.
The goal is to get the level to show “zero” in both directions. As you close in on this, you’ll need to find new axes that are more level to use as reference. Once you get zero both ways, it has self-proven and calibration is complete.
Leveling Your Machine Tool
Next, place the level on the ways (the machined parts where the tailstock slides) of the machine, down near the tailstock. Make sure the ways are clean, dry, and free of raised burrs. A 1-2-3 block may be needed for the level to sit flat. If you use blocks for this, measure them first to make sure they are the same. Inexpensive 1-2-3 blocks may not be! Precision-ground gage blocks are better, if you have them.
For a floor standing machine, adjust the feet until you get a level reading. If your machine has a lot of feet, try the “three point” method. Get your machine sitting on only three of its feet (or two feet and a screw jack). A triangle is much easier to get level. Once level, carefully lower the remaining feet until they take weight but don’t upset the level.
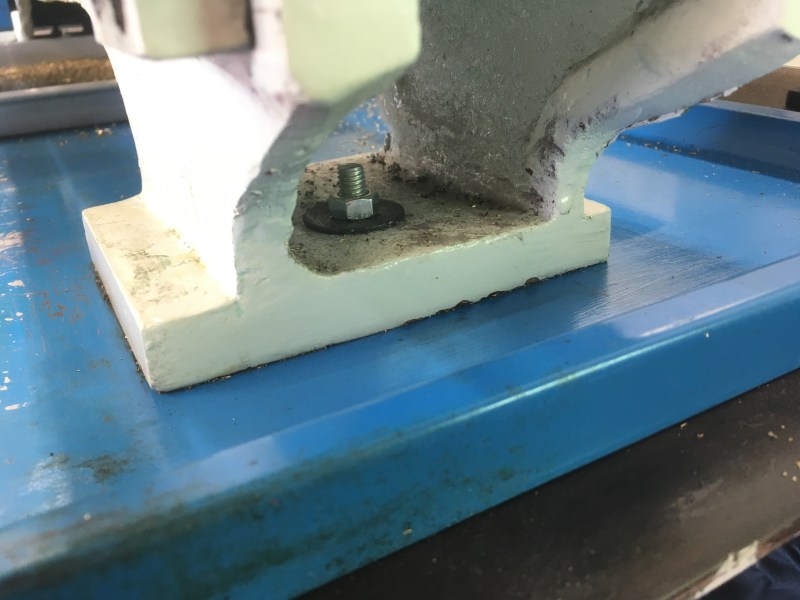
For a bench-top machine, you’ll typically shim under the feet of the machine as needed. A variety pack of steel shim stock in various thicknesses is helpful here, or sacrifice an old feeler gauge.
Do the same procedure for the ways near the headstock, and also with the level placed lengthwise on the ways. You’ll likely need to go back and forth a few times until every position reads level.
Another school of thought says that, instead of placing the level on the ways, you should place it on the cross-slide, since that’s where the cutting tool is. Personally, I think this just introduces new sources of error, but I like to double check on the cross-slide after the ways are level.
Be Zen About Releveling
Leveling is not a one-time deal, so get comfortable with it. The machine needs to be re-leveled any time it is moved, and periodically as the floor shifts or settles. Even concrete moves, so check your machines from time to time and re-level as needed. You should also check a new machine after using it for a few weeks, as the machine’s castings will “settle in” under the vibration of use. Check it again any time you suspect the machine is turning a taper, such as if you’re struggling to hit a dimension on a long part. Older machines are more flexible and will need re-leveling more often.
Once your machine is level, the next step is to really dial it in by cutting a test bar. This is a topic for a future article, so stay tuned for that. In the mean time, stay away from those carpenter types. Apparently that “wood” stuff is ruined by fire. Why would anyone bother with it?
Since this is HaD, someone needs to come up with a better way.
I don’t think there is a way to make it “better”. Faster maybe (more levels, automatically calculate the needed shim thickness, that sort of thing) but not better.
Yes. Something involving a 555, some lasers, and a 3D printer.
You’ve forgotten the leds, flashing or otherwise.
Blue!
ARDUINO, you absolutely cannot forget the arduino!
I’m using an Arduino, a some stepper motors. I have the Arduino jammed under one of the feet of the metal table it is on to take out the wobble, and the stepper motors made really nice leveling feet for the other legs.
Yeah no, they neither have rubber layer to dampe vibration nor threaded shaft sticking out to easily adjust height. Worst machine feet ever.
Not sure if better, but way more precise, NASA Tech Briefs style:
https://www.eevblog.com/forum/projects/suggestions-for-high-resolution-tiltmeter-(inclinometer)-sensor/msg1565554/#msg1565554
At least you got the 555 involved ;)
I don’t remember any 555 there, but yes, one can use it anywhere
:o)
The vial capacitance trick can resolve 0.05 arc-second:
https://www.docdroid.net/enKb2ed/nasaames-simpletiltmeter.pdf
“555” is found a couple times in the link you posted.
ROFL, you got me with with that one!
:o)
There are bluetooth based machine levels out there. I would have loved to have them when I had to level VMCs and granite slabs.But really spendy.
I would like to see a auto-leveling Lathe yes, Z-axis zeroing would be a nice touch, auto-centerpoint would be fancy.
Sure you dont mean X axis? X is cross slide, Z is the carriage.
z is always the axis of rotation, so on the lathe it is left to right. x is front to back, y would be tool height but it isn’t ever used because tools are fixed..
Yes, the cross slide moves in X and the carriage move in Z
There are lots of sometimes angry discussions on the different machinist sites about leveling lathes, but, as mentioned above, the critical issue is getting the lathe bed in a single plane. They work fine on ships, where they are not “level”. It is just that a precision level is a relatively inexpensive way to measure extremely fine differences over a long distance.
Starrett makes carpenters levels. The KLIS24-N is good to .001″/INCH. The 98-6 ” is good to .005″ per FOOT. I have a lathe with a 48″ bed, with 24″ between the feet on both ends. Using a master precision level (Starrett 199Z or a copy), which is rated to .0005″ per foot, I could reliably detect .001″ shims. I didn’t use the $898 Starrett, I used a Chinese copy, but due to the self proving nature of levels mentioned above, you can get very good results with a little extra work.
The issue is setting the lathe up to be on the same plane in all directions so that the bed is not twisted along its length, not necessarily “level” as in “perpendicular to the direction gravity acts”. That’s why lathes work fine when set up properly on a ship.
I suppose that using a stand with three adjustable feet would be a “cheater’s way” to get the whole thing levelled onto one plane. Using three feet should mean that it naturally settles into a single plane, having the feet adjustble should mean that you could level that plane in regards to the local environment (so for example, that it doesn’t look weird when you sigh across the spinning workpiece and that nearby shelf or ductwork is not quite parallel to it).
Unfortunately, since the bed will not have been mounted in exactly the same way on 3 points when shaping the ways, they won’t be in plane with just 3 supports. You might actually NEED the 4 supports to get it perfectly in plane.
I’d be even more impressed if they got it in the same plane in some directions and not others!
Aluminum from cut-up pop cans is a cheap source for large quantities of fairly tough shims, as well.
also…motorcycle handlebar clamps :-)
That was a Quality post.
Nice one! Touché’!
Zen and the Art of Machine Tool Maintenance.
Or laminated transformer cores. My father used these to shim his big lathe.
He took an old transformer that was bolted together and disassembled it.
More than enough shims to do a larger machine
When buying a carpenter’s level, test it by doing the end for end swap before taking it to checkout.
Check its vertical and horizontal vials. Even if the surfaces you test it with are not level, a good level will deflect the bubble the same amount after the end for end swap.
All the same arguments about leveling machine tools apply to 3D printers, too. I have always put leveling feet on my printers and adjust them whenever a machine gets moved. I started with a bubble level but found it wasn’t sensitive enough, so I later went to placing a large ball bearing (like 1.5″ diameter) on the t-slot and adjusted so it wouldn’t roll. But that isn’t so good for use on some of the other parts of the machine, so I got a digital protractor like this one:
https://images-na.ssl-images-amazon.com/images/I/61ATtV1UxuL._SL1024_.jpg
It’s a lot more sensitive than a bubble level and really helps dial in the leveling. It’s also good for ensuring that the XY plane is perpendicular to the Z axis, something a lot of printer builders neglect.
“Spin Slowly And
Keep Plumping”
Sounds like good general advice to me.
“Spin slowly and keep plumping”
Keep plumping?
But, I’m trying to lose weight!
B^)
I have a bubble level that is sensitive to .0005″ in 10″. I can guarantee this device is not that sensitive.
+1
The Starrett at .0005″/ft is about five times more sensitive (asin(.0005/12)=.0023 degrees). Please also keep in mind that resolution is not accuracy.
“…make the noise!”
I wonder if a CNC machine compensates for leveling with software, instead of tedious manual adjustments…
It wouldn’t be too hard to implement.
Otherwise each foot could have a stepper driving a lead screw to adjust each feet of the machine to make the leveling process far easier.
I would implement it by having a small stepper, connected through some gear reduction before it turns the lead screw to extend/retract the leg. And to stop the machine from forcing the lead screw and gear set to turn from the weight of the machine, we can have a spring pushing a toothed block onto the first gear that is on our stepper. This block would then be retracted by a solenoid when we wish to level the machine, effectively breaking our system without the need for power to keep the breaks engaged.
Since the force needed to make the toothed block slip will be increased by the gears as well, so ideally, the gear being kept in place by our block might only need 5-10 N/m to make the block slip a tooth, but if our gear reduction is 1:500, then we suddenly need 2500-5000 N/m to turn our lead screw, And this lead screw in turn will also increase the force needed to unlock our break.
So a ballpark estimate for our back of the envelope breaking system might be able to support around a ton per leg before the break slips.
And with a 200 step per revolution stepper, and a lead screw with 1 mm per thread (single start), would be able to make 10 nm adjustments… (the real world would though toss in lots of reasons for why we wouldn’t get that resolution.)
Though, I don’t suspect a system like this would be cheap.
Would wax motors exert enough force? It’s not like a large amount of movement will be needed. Locking into place would be the other part.
https://wikivisually.com/wiki/Wax_motor
I don’t think you understand how heavy a real machine is.
A small bench top lathe can be fairly light weight. Around 15-50 Kg is not unheard off.
While larger lathes can go into the hundreds and sometimes even thousands of kg.
Though, do note how 5000 N of force is roughly about 500 kg per leg. So a machine with 4 legs can then weigh up to 2 tons, including the work piece. Yes, this would be highly insufficient for a 12 foot long lathe that can weigh in excess of 10 tons. But on the other hand it would be fairly sufficient for a more realistically sized lathe for the average garage.
Though, one can always redesign the system to high specifications to allow for far greater loads.
No, CNC machines are carefully leveled and then they use granite or ceramic squares to make sure all the axes run squarely. Smaller VMCs only take maybe an hour. In reality when you level a machine you are just returning it to the same position as when it was manufactured.
+10. Machinist by day here in a forge die shop- hes absolutely right. I have watched pro cnc riggers install, level, and use these calibrated granite mastersquares, along with ball bar calibrator units.
To anyone who wants precision in their real tools- and yes, 3d printers too- learning to level if you have a real calibrated level isnt that hard. Article actually covered basic leveling and even calibration check well.
It sounds harder than it really is- calibrated levels actually have marks graduated on the bubble vials, so they are easily measured in a real increment. Easier to gage level actually than with a normal carpenter level.
For the record, starrett 98 normal machinists level 12″ long is about 200$. If you own either machine tools, or a pool table- its worth every penny.
And really you are creating a solution for a problem that does not exist. You would add thousands in cost to a machine that only needs to be leveled once it is installed and if it is ever moved. Many machines will sit in the exact same spot till they wear out and hauled off for scrap.
It’s not about leveling the machine, it’s about bending it straight. We usually epoxy the lags into the concrete.
This needs a link in this thread somewhere…
https://www.youtube.com/watch?v=THkb-x35fwc
Somewhere on the information super highway there is a PDF titled “Rollie’s Dad’s Method of Lathe Alignment.” It’s worth a read because it describes another way to true a lathe without levels, much like Old Tony’s video. The method requires a dial indicator and a round bar.
Thanks for sharing this! The best part of Tony’s video is the explanation of why bed twist causes it to turn tapers. A lot of new folks struggle to understand this part and Tony explains it very well. I wanted to include this information in the post, but there just wasn’t a way to do it in the space I had.
In reality if you lathe is on a three point mount system on a wood bench or sheet metal you dont need to level it. Most of the time you dont really need to level the lathe. The math works out so that even if there is a slight twist in the bed the difference in diameter will be so small that most home shops could never even measure it.
Some lathes, like the Monarch 10ee dont even need to be leveled, they are so stiff with their cast iron base that they are not going anywhere. The manual even says they dont need to be leveled.
Where you are really going to level lathes and machine tools in general is when they start getting large. Big old Monarch 16″, yep, you need to level it. VMC, level and square it. Some times you actually have to put studs into the ground to pull the machine into level.
Leveling a lathe end to end really isn’t necessary. What is necessary is to adjust any twist out of the bed.
Take a plate cylinder that’s about 180″ by 27″o.d. and weighs roughly 400 pounds. Chuck it up and run it in a steady rest while you bore the ends for the plates.
Having the lathe level reduces the tendency of the cylinder to try walking out of the chuck jaws.
Also helps with keeping ya undies clean! ;)
I missed a zero there. Weight should have been roughly 4000 pounds.
Come guys, Give us a ten~15 min window to edit. please!
“Come guys, Give us a ten~15 min window to edit. please!”
That will require logging in instead of just punching in the nick you chose. To allow eiditing, you need to make sure the one who’s attempting that is the same person who wrote the original post.
Send in a DNA sample. ;-)
I’m not convinced it would require a login. This site already have something working with IP address, browser sessions and/or cookies that was allowing me (and nobody else) to see my post while it was waiting moderation for a few hours yesterday. Clearly the site can already identify the computer/browser/IP address of the post creator.
Some lathes need leveling and some dont; depends on the mass of the machine and the design. A lathe will only twist or warp under its own weight so say a small emco lathe will not deform much. its just not heavy enough [mine is about 170 kg, approx 1700N of downforce on two pedestals centered under the bed] The heavy sheetmetal bench that came with it can flex somewhat but the base is still supported along the centerline of the machine. A bigger lathe with feet on all corners is a different story alltogether.
Happy chipping!
Those small Asian lathes can benefit from being firmly bolted to a stiff piece of steel. The 7x size can be sprung a bit with the pressure of a single finger on the headstock. Ideally, you’d take the lathe apart, clamp the bed upside down on a big mill and cut the bottoms of the feet flat and to the same height. Then you’d mill top and bottom of the beefy hunk of metal to bolt it to. Then you’ve a start on getting it straight.
I would imagine this is generally, true but…The lathe bed could be sprung as a function of clamping while it is being machined. Even if the surfaces are all parallel/flat as machined, when it is removed from the tooling, it will spring back affecting the newly cut surfaces. I have a 9×20 Enco machine lathe and I had to put two elongated feet under the original mounting points so that I could manually “rack” the bed to a more-or-less co-planar condition. Full disclosure: my lathe *was* tipped over in a gravel driveway by movers so my observations are based on a small and contaminated. However, I’ve seen similar examples to the hypothetical one I laid out above during my involvement in the manufacture of thousands of large machined parts. Even in forgings which are annealed from the supplier, removing material affects the balance of internal stresses in much the same way a dead tree segment (aka 2×4) can be straight and true, but when ripped lengthwise, produce two warped pieces.
For what it’s worth, dead trees don’t bother my lathe tooling, but the guts (read: sawdust) gets everywhere, absorbs lubricious oil and then cakes up in hard to reach places. Dust collection helps, but doesn’t prevent this.
It grows on trees. Not much talconite production happening in my neighborhood.
Taconite?
What about mounting your lathe to a generous slab of granite, and placing the whole lot on a rubber mat? Polished granite slabs are commonly used in kitchen table tops and are usually remarkably level, One can get the necessary size as an off cut. The rubber mat will ensure any difference between the granite and your workbench will be accommodated.
> and are usually remarkably level
What you call “remarkably level”, machinists call raw stock. What you call “very level”, machinists call “yeah, now we can start to make it level”.
For the real stuff Vintagemachinery.org, tells you all, see vids on youtube also.
Put the level on the carriage and run the carriage back and forth. The plane in which the carriage moves is what matters. On a Vee bed lathe the carriage does not ride on the flats on top of the ways. If you reference level to those you may or may not get the carriage moving in a plane.
On an old lathe it will also let you test the amount of wear. A proper level is 0.0005″/10″ or 10 arc seconds per 2 mm bubble movement. The Chinese ones are $50-80 depending on the length.
Machine tool setup is Geometry 101 to exacting standards. Unfortunately, it seems that not many people consider geometry relevant these days, so they don’t learn it.
Have a read of this thread if you are actually interested in the concept of level.
https://www.eevblog.com/forum/projects/suggestions-for-high-resolution-tiltmeter-(inclinometer)-sensor/msg1531160/#msg1531160
Especially the results of walking near a sensitive level on a concrete floor.
There is no need to learn geometry, you only need to respect it.
Then you’ll look up the formula when it becomes relevant. Most of the time though, you’re not using a formula, which is all “learning geometry” is; memorizing the formulas. If you merely respect that it matters if things are lined up, you’ll take steps to do so, and if it involves a formula, these days that is not much of problem to look up.
In the past you’d have to find an old math book of some sort and hope it has a “table of formulas” in the back; so having “learned” it instead was a notable advantage, as libraries didn’t fit in pockets.
https://goo.gl/images/KDa8Jo
As mentioned more than once, it’s twist removal that’s the aim, and a sensitive level is the simplest tool for that job.
As dropped in place, my 3/4 ton lathe had outrageous twist, but a $200 machine level simply dropped onto the flat top of the cross-slide allowed checking ends and middle of the bed by cranking the saddle back and forth. The ends are now immeasurably close to the same plane, and the middle of the 40″ travel is out by 0.006 degrees. That’s half a thou across the ways, and good enough for the work I do, not to mention within the manufacturer’s spec., so I can’t complain.
As for using transformer laminations as shims, a single thickness of newspaper sends the machine level miles off-scale.
We’re adjusting by a thousandth of an inch or less on the levelling screw to stay within one graduation of the level.
https://www.youtube.com/watch?v=Q1zBtJhgwBI
This FTW
Hey, some of you guys are way, way, waaaaay overthinking this. I’ve had to level my lathe once. It took about 15 minutes, and it hasn’t changed again yet. And those precision levels are .0005/foot or maybe 10 inches. .005/foot is woodpecker territory. There aren’t too many lathes out there that will cut perfectly straight for say, 2 or 3 feet. You have to mess with them. Figure out where the taper is, and adjust for it. If I can get my POS (Enco 14 x 40, someone gave it to me), to cut pretty straight for 4 inches I’m doing better than expected. The Hardinge toolroom lathes at work cut pretty straight, but those are $30,000 each.