We often think of submarines as fairly complex pieces of machinery, and for good reason. Keeping the electronics watertight can naturally be quite difficult, and maintaining neutral buoyancy while traveling underwater is a considerable engineering challenge. But it turns out that if you’re willing to skip out on those fairly key elements of submarine design, the whole thing suddenly becomes a lot easier. Big surprise, right?
That’s precisely how [Peter Sripol] approached his latest project, which he’s claiming is the world’s smallest remote control submarine. We’re not qualified to say if that’s true or not, but we were certainly interested in seeing how he built the diminutive submersible. Thanks to the fact that it started life as one of those cheap infrared helicopters, it’s actually a fairly approachable project if you’re looking to make one yourself.
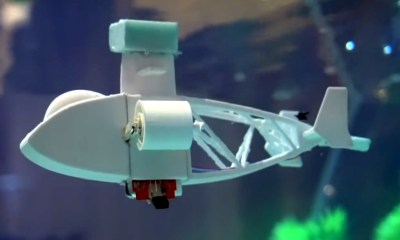
After testing that the IR communication would actually work as expected underwater, [Peter] liberated the motors and electronics from the helicopter. The motor’s wires were shortened, and the receiver PCB got a slathering of epoxy to try and keep the worst of the water out, but otherwise they were unmodified.
If you’re wondering how the ballast system works, there isn’t one. The 3D printed body angles the motors slightly downwards, so when the submarine is moving forward it’s also being pulled deeper into the water. There aren’t any control surfaces either, differential thrust between the two motors is used to turn left and right. This doesn’t make for a particularly nimble craft, but in the video after the break it certainly looks like they’re having fun with it.
Looking for a slightly more complex 3D printed submersible vehicle? Don’t worry, we’ve got you covered.
[Thanks to Blaubär for the tip.]
Two channels is plenty to control a submarine.
Example: if you create a virtual ground at half the battery voltage (small op-amp + resistors), then the motor output channel will always drive each motor backwards or forwards at half the voltage because the output is either positive or negative compared to the virtual ground. Then you modify the IR transmitter to send alternating data frames where both channels are on and off equal amounts of time. Changing the pattern lets you control both motors backwards and forwards with a speed proportional to the duty cycle.
There are non-conductive oils. If you fill the electronics compartment with oil and only allow a small hole at the bottom to equalize pressure you don’t have to otherwise try to protect the conductive electronics.
Are the materials in this OK for the fish? If so this is cool!
I would worry about the exposed motors: lubrication in the, brush shavings and eventual rust.
Awesome, just run the motors and electronics right in the water. I love it, and I’m not being sarcastic.
Does work too well in your saltwater aquariums of course…
Actually used to be a trick for “running in” electric motors for slot cars or RC buggies, dunk it in the bath while applying full power.
Parts bin here I come!
Fresh water fish sensitive to chemicals. Tropicals more so. Likely to have some floaters other than sub. May take several days for contamination to take effect. Possible a week or two. Exposure from big toy sub likely the biggest exposure to toxicity.
Relatively no control. Props made for different environment. Lots of energy lost in cavitation. Motors way too fast. Best to keep submerged. Little motors fairly resilent if kept submersed but will fail. Saltwater another issue.
Like the first proto more. Many reasons to dump original IR ASIC and roll your own MCU.
Resin prints fragile.
More expensive less fragile photo reactives available. Developing(pun) tech.