Because of the architecture used for the Apollo missions, extended stays on the surface of the Moon weren’t possible. The spartan Lunar Module simply wasn’t large enough to support excursions of more than a few days in length, and even that would be pushing the edge of the envelope. But then the Apollo program was never intended to be anything more than a proof of concept, to demonstrate that humans could make a controlled landing on the Moon and return to Earth safely. It was always assumed that more detailed explorations would happen on later missions with more advanced equipment and spacecraft.
Now NASA hopes that’s finally going to happen in the 2020s as part of its Artemis program. These missions won’t just be sightseeing trips, the agency says they’re returning with the goal of building a sustainable infrastructure on and around our nearest celestial neighbor. With a space station in lunar orbit and a permanent outpost on the surface, personnel could be regularly shuttled between the Earth and Moon similar to how crew rotations are currently handled on the International Space Station.
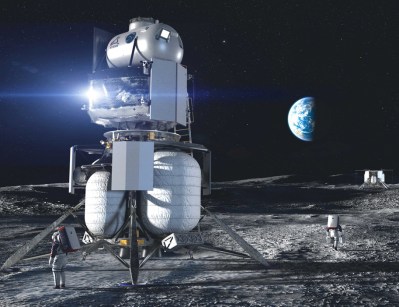
Naturally, there are quite a few technical challenges that need to be addressed before that can happen. A major one is finding ways to safely and accurately deliver multiple payloads to the lunar surface. Building a Moon outpost will be a lot harder if all of its principle modules land several kilometers away from each other, so NASA is partnering with commercial companies to develop crew and cargo vehicles that are capable of high precision landings.
But bringing them down accurately is only half the problem. The Apollo Lunar Module is by far the largest and heaviest object that humanity has ever landed on another celestial body, but it’s absolutely dwarfed by some of the vehicles and components that NASA is considering for the Artemis program. There’s a very real concern that the powerful rocket engines required to gracefully lower these massive craft to the lunar surface might kick up a dangerous cloud of high-velocity dust and debris. In extreme cases, the lander could even find itself touching down at the bottom of a freshly dug crater.
Of course, the logical solution is to build hardened landing pads around the Artemis Base Camp that can support these heavyweight vehicles. But that leads to something of a “Chicken and Egg” problem: how do you build a suitable landing pad if you can’t transport large amounts of material to the surface in the first place? There are a few different approaches being considered to solve this problem, but certainly one of the most interesting among them is the idea proposed by Masten Space Systems. Their experimental technique would allow a rocket engine to literally build its own landing pad by spraying molten aluminum as it approaches the lunar surface.
Practice Makes Perfect
While Masten might not be a household name, they aren’t exactly neophytes when it comes to landing rockets. In fact, it’s their specialty. Founded in 2004, the company has been working on a series of increasingly powerful vertical-takeoff, vertical-landing (VTVL) vehicles that have cumulatively performed over 600 flights. The latest version, the XL-1, has been selected as part of NASA’s Lunar CATALYST program to deliver multiple payloads to the Moon’s South Pole by 2022.
After more than a decade of developing rocket-powered landers in the Mojave Desert, Masten is well aware of the dangers posed by the high velocity ejecta that gets kicked up right before touchdown. They’ve found that the easiest solution is to simply add enough shielding to the bottom of the craft that soil and rocks will bounce off without doing any damage. But it doesn’t scale well, as every bit of shielding you add to the vehicle reduces its useful payload capacity.
Besides, even if you armor the lander to the point that ejected materials wouldn’t cause it any damage, it would still be boring a hole into the ground on each landing. It would still endanger nearby vehicles and structures as well; a serious problem for all but the very first missions. Because of this, Masten started researching the way the lunar surface will behave when exposed to the force of their landing engines.
It’s impossible to completely simulate lunar conditions here on Earth, as there’s no way to reduce the effect of gravity on the material blown out by the rocket’s exhaust. But their terrestrial testing was enough to convince them that they should start investigating different ways to combat the issue.
Instant Landing Pad, Just Add Heat
Masten’s concept is called the FAST, or the in-Flight Alumina Spray Technique. To use FAST, the lander would descend to within a few meters of the Moon’s surface and go into a controlled hover. Aluminium oxide (also known as alumina) pellets would then be injected into the rocket’s exhaust, where they are melted and ejected downwards. Once the alumina hits the lunar regolith, it combines with the loose material and behinds to cool and solidify.
By slowly moving over the landing site, the engine can deposit a thick enough layer of molten alumina to create a custom landing pad of whatever dimensions are required. After its completely hardened, the Masten proposal says it should have sufficient thermal and abrasion resistance for the vehicle to complete its decent without kicking up any dust or forming a crater.
Or at least, that’s the idea. Injecting solid particles into the exhaust plume of a running rocket engine is relatively unexplored territory, and it will be interesting to see what Masten finds. Will adjustments will be required to maintain stable thrust during the hover maneuver? Is there a risk that the alumina might build up inside the engine? Could it clog the engine so that relighting it becomes impossible?
The company says they will spend the next nine months researching these questions, and likely many more, before making a final decision about whether or not the technology is worth pursuing for the Artemis program. Even if it’s not ready in time for the 2022 – 2024 landings that NASA says will be the first steps towards a sustainable program of lunar exploration, the company believes the idea could still be used when the agency turns its attention to Mars in the 2030s and beyond.
Arthur C. Clarke knew that getting the freight rockets to land where you wanted them on the moon would be tricky, way back in 1956.
“Robin Hood FRS” tells the story of what happens when an automated freight rocket goes astray when landing on the moon. It’s just a couple of pages long:
https://books.google.de/books?id=pcwqAAAAQBAJ&pg=PT12&lpg=PT12&dq=arthur+c+clarke+%22Robin+Hood,+F.R.S.%22&source=bl&ots=gWgdryARPT&sig=ACfU3U3gUXepPNE5KCPSbdTGE36SzlzqnQ&hl=de&sa=X&ved=2ahUKEwjskIqG0cLpAhVB4qQKHeprAaUQ6AEwCXoECAoQAQ#v=onepage&q=arthur%20c%20clarke%20%22Robin%20Hood%2C%20F.R.S.%22&f=false
Seems like a Project Plowshare problem. Very small modern nuke to fuse the regolith should work…
That’s what I was thinking, a lunar “daisy cutter”, but the usual types would start the wailing and nashing of teeth so forget it. (We might kill all the Moon Pandas!)
Let it not be forgotten, that there are very good reasons people don’t want to violate the nuclear test ban treaty, especially when you’re mounting nuclear warheads on missiles with far more delta-V than your standard ICBMs.
Small fission bombs have poor efficiency and they would pepper the whole neighborhood with nuclear waste. If you then intend to do any geology or to extract minerals, you have to deal with the contamination.
It’s exactly the same reason why project plowshare was ended. The radioactive fallout from above-ground tests wasn’t exactly popular, and the underground tests too turned out venting radioactive steam, and then tritium started showing up in the drinking water… even the oil shale extraction blasts were unsuccessful because the oil would then contaminate the processing equipment.
How many astronauts will die of radiation exposure?
it’s so funny we are going to the moon for a permanent stay, yet we need to wear mask in public, something is not right here
It’s a sign that this rock is done for! Quick, head to the escape pods and hop to the next one!
Just an extension of “Social Distancing.”
Spray welding rocket, what a time to be alive, https://youtu.be/ByeLJsHvnzc?t=95
How about using landing rockets as usual, configured a bit differently, to allow a Mars type ‘bounce’ landing with a protected bubble. The retro jets could be safely flown away and the pad would unfold allowing the next landing to be on a metallic/ceramic smooth surface, with normal landing jets. Build more space around it with conventional landing rockets until you have a large enough pad for larger craft.
Just dropping some piles of self-leveling floor cement would do the trick. But we first need to make a cheap cement that hardens in vacuum. Maybe some epoxy?
How about an orbital laser that melts the surface, from a distance, before the rocket descends? (Just pray the laser has good aim…)
maybe something on the way, solar concentrator maybe reached 1200 ° C or 1500 ° C without atmospheric impediments.
“Maybe some epoxy?”
At least they won’t need a vacuum pump to get the bubbles out!
B^)
I want a giant spitball cannon in space shooting wads of self-leveling concrete. After it is done with the moon, time to take over the world!
self leveling concrete? this isn’t Louis Rossmann’s channel.
Why not a large rolled up carpet (not literal) with a wheel at either end. Drop it, maneuver it to the exact spot you want it, anchor one edge and let the wheels pull/unroll?
I think Musk has the right idea, adding thrusters at the top of the rocket to ensure that exhaust does not touch the regalith.
Large mat of woven Aramid fiber?
It’s fascinating, that the resulting landingpad would be more heatresistant that the initial sprayig material. Or at least I assum it would be or else you would liquify the pad upon landing, and takeoff.
With the spraying alumina droplets, they’re splatting at high reduction in an oxygen poor environment, meaning the pad is a cemented cake of metallic aluminum droplets with regolith scattered in, more porous at the underside but getting purer and more solid as layers are added.
The rocket exhaust is high velocity but once it exits the nozzle, it should cool quickly, and a metallic aluminum pad surface will have enough thermal dissipation to make it survive the exhaust even at close range. What’s funky is you won’t have the familiar oxide crust on top of the metallic surface.
If the fuel is throttled down first when the engine is shut down the surface should get oxidised. Assuming that’s something you want.
Where does the heat go, after the rocket exhaust exits the nozzle?
I was assuming it would only lose a relatively small amount of heat as radiation, until the lunar surface (and previously deposited material) conducts the heat into the moon from contact.
A de-laval nozzle effectively turns heat into linear motion – it goes into the directed kinetic energy of the exhaust plume. When the plume expands into the vacuum, it cools down.
Of course the impact of the gas molecules against the surface will turn that kinetic energy back into heat.
Thanks for a very well thought out and expressed explanation. Another factor in the dissipation of the heat so the lead doesn’t melt in the extreme cold on the moon.
Rocket exhaust cools dramatically as it expands on its way out the nozzle. Injecting the particles where the flow is hottest gets them melted, but the when the exhaust hits the surface it’s no longer hot enough to re-melt what’s already been deposited.
I wonder how much concentrated solar energy it would take to produce a sintering effect with that regolith, granted a laser or perhaps even a maser might do a better job with less hardware (especially if nuclear powered).
But isn’t NASA working on metal printers for the ISS? Granted it’s mostly research and proof of concept now but with a good system in place they could instead build a platform in space like the landing platform used for the Mars Pathfinder probe, a tetrahedron that upon landing can unfold into flat platform sturdy enough to land on…..or instead of using it for a landing pad they might try using it as the anchor point for a space elevator.
And if they could gather and recycle some of that junk in space to build the platform then all the better.
Why not just do what we did for Apollo? There were no craters there.
Sudden outbreak of common sense. Bravo.
As the article mentions, the rockets on the Apollo lander was much smaller than would be needed to ferry the amount of weight for sustained missions. The longer the mission, the heavier the weight, the need for bigger rockets which will create a bigger crater.
Apollo didn’t create little craters. Apollo created NO craters. No dust was even kicked up. Why don’t they just do what they did with Apollo?
“Why don’t they just do what they did with Apollo?”
Because they son’t want to land in the same place? The Apollo program landing site were picked largely for ease of landing and were chosen from the part of the moon that was easiest to study from earth. The Artemis program, however, is being planned to land where it is easiest to build a outpost, which has very different requirements. At least last I heard, inside a crater near the moons north pole was a leading site, and one that we can’t study at all with earth based instruments due to the wall of the crater. This means far less certainty about what the rockets might be landing on.
If we aren’t certain what is there, how do we know that it is the easiest place to build an outpost?
I heard it was the Moon’s South Pole,
water ice may have been discovered in craters down there, and with the right site, solar panels could collect all lunar day long.
Have you ever watched the Apollo 11 landing video? It’s very clear to see through the window that the landing engine exhaust is blowing dust away. Armstrong mentions seeing it when they were 40 feet from the surface.
https://www.hq.nasa.gov/alsj/a11/a11transcript_tec.html
(GOSS NET 1) Tape 66/11 Page 316
04 06 44 45 LMP (EAGLE)
100 feet, 3 1/2 down, 9 forward. Five percent.
04 06 44 51 LMP (EAGLE)
…
04 06 44 54 LMP (EAGLE)
Okay. 75 feet. There’s looking good. Down a half, 6 forward.
04 06 45 02 CC
60 seconds.
04 06 45 04 LMP (EAGLE)
Lights on. …
04 06 45 08 LMP (EAGLE)
Down 2 1/2. Forward. Forward. Good.
04 06 45 17 LMP (EAGLE)
40 feet, down 2 1/2. Kicking up some dust.
04 06 45 21 LMP (EAGLE)
30 feet, 2 1/2 down. Faint shadow.
04 06 45 25 LMP (EAGLE)
4 forward. 4 forward. Drifting to the right a little. Okay. Down a half.
04 06 45 31 CC
30 seconds.
04 06 45 32 CDR (EAGLE)
Forward drift?
04 06 45 33 LMP (EAGLE)
Yes.
04 06 45 34 LMP (EAGLE)
Okay.
04 06 45 40 LMP (EAGLE)
CONTACT LIGHT.
04 06 45 43 LMP (EAGLE)
Okay. ENGINE STOP.
04 06 45 45 LMP (EAGLE)
ACA – out of DETENT.
04 06 45 46 CDR (EAGLE)
Out of DETENT.
04 06 45 47 LMP (EAGLE)
MODE CONTROL – both AUTO. DESCENT ENGINE COMMAND OVERRIDE – OFF. ENGINE ARM – OFF.
(GOSS NET 1) Tape 66/12 Page 317
04 06 45 52 LMP (EAGLE)
413 is in.
04 06 45 57 CC
We copy you down, Eagle.
04 06 45 59 CDR (TRANQ)
Houston, Tranquility Base here.
04 06 46 04 CDR (TRANQ)
THE EAGLE HAS LANDED.
Plenty of dust was kicked up, but because of the vacuum it behaved more like sandblasting medium than the dust you’re used to. It shoots off away from the point of impact at high velocity and drops to the ground on a ballistic trajectory with no billowing.
Which is what you don’t want to happen when you land near settlements, where the rubble and dust you kick off lands like a hail of gunshot on anyone moving outside of the shelters.
From the article:
“The Apollo Lunar Module is by far the largest and heaviest object that humanity has ever landed on another celestial body, but it’s absolutely dwarfed by some of the vehicles and components that NASA is considering for the Artemis program. There’s a very real concern that the powerful rocket engines required to gracefully lower these massive craft to the lunar surface might kick up a dangerous cloud of high-velocity dust and debris. In extreme cases, the lander could even find itself touching down at the bottom of a freshly dug crater.”
It isn’t a matter of degrees. Apollo created NO dust and NO crater. Why do we suddenly think that these rockets will create a situation that didn’t even exist with the last rockets?
Bob stepped on my foot, but no damage done. Why would running over my foot with a car do any damage?
First, it’s a bad example because running over the end of someone’s foot often does no damage, and stepping on the higher parts of someone’s foot often does serious damage.
But you are onto the real issue. Rocket thrust is by its nature spread out across the surface. The landing legs are putting FAR more pressure per square inch on the surface. Do we even have any real world examples of rocket engines burning craters in earth when landing or taking off? The SpaceX ASDSs don’t seem to have any particularly hardened or armored surfaces. It just seems like normal decking steel rated for the weight.
They didn’t leave much a crater sure, but you can *see* the dust being blasted away in the landing footage from the Apollo missions. For example.
I see vapor from the rocket. I don’t see a change to dust, unless you claim that they are already seeing dust at 30+ feet.
That’s a pretty neat trick you can do there Phelps, being able to see vapor from a rocket in vacuum.
Are you saying that you think you can’t see rocket exhaust in vacuum?
“you can’t see rocket exhaust in vacuum”
I’d be happy see evidence to the contrary. But any footage you see of rockets in vacuum don’t have visible vapor. A dirty aluminum-fueled solid-fuel rocket might have bright particulates, and the exhaust gas might be visibly incandescent for a short distance from the nozzle if it’s dark enough to see it. But visible “vapor” from a hydrazine/N204 engine firing in vacuum? Nope.
See, for example, the ascent footage of the lunar modules: same fuel as the descent engine. No visible exhaust, let alone vapor. Even the relatively dirty RP1-fueled Falcon 2nd stage’ Merlin engine, ten times the size, shows a little sooty exhaust, but no vapor.
(But I suppose one could claim it’s all a hoax, and the engine was actually firing in atmosphere, on Earth. Or perhaps it really was the moon, but the cameraman taking the ascent footage edited out the exhaust before uploading the video back to Earth.)
Why not move the nozzle(s) to the top of the rocket, similarto the ‘launch escape system rockets’ used for the Apollo (and other, I’m sure) rockets. If the nozzle(s) are further away from the surface, there will be significantly less ‘high velocity ejecta’, and it could be mitigated completely.
This is actually SpaceX’s solution to the problem in their proposal. They would land with smaller radial engines mounted halfway up the side of the Starship, rather than the primary engines.
Though it’s worth noting that Starship would stand approximately 50 meters tall, so they have a considerable advantage there. No other lander proposal could put anything close to that sort of distance between the surface and the engines.
Could even have like a crank up tower deally, with a bunch of retros on top of it. Didn’t they have a fixed setup like that to separate the stages on one thing.
Cory Doctorow wrote a story in which a pre-placed robot made solar-sintered bricks out of the dust. I think his story was on Mars, but it would work even better on the moon. (more sun, less atmosphere).
Drop autonomous robot to make bricks and build a pad. Land on it a few months later….
Yep. This is the logical, inexpensive and safe solution. The other solution is just dropping a huge-ass pre-fabricated landing pad onto the surface, even if it’s in the wrong place. It’s expensive but could work.
Nah, just send the SeaBees
I don’t know that I would want to live in a plywood moon base.
When my wife was a Navy Nurse, when she’s arrive on the site of field maneuvers, she’d visit the SeaBees shack and leave them a large bag of Tootsie Pops. She learned early to be nice to people who provide the hot water for showers.
They need to find the properties of compressed regolith bricks. Some robots and solar power could be the ticket, and start with interlocking pavers. (We never go back and they are like Wall-e?)
I was thinking of an article I saw a while back that talked about doing the same thing on the moon. Use what’s already there to start with….
So anyway, what’s the plan for rescuing the next men on the moon, when it turns out they misunderestimated the setting time of the aluminum or plastocrete or whatevs, and cemented themselves to the moon.
I’m wondering if they’ll be using text to speech in the helmets while singing “daisy daisy”
https://www.youtube.com/watch?v=1B488z1MmaA
Land a robot bulldozer and a LASER leveling system. It’s a simple setup, used for decades (minus the robot driver) to scrape farm fields flat and pitched at a precise angle. A rotating LASER is atop a pole or tripod, adjusted to level (for a construction site) or tilted (for a field) then a pair of sensors, mounted closely one above the other, waits for the beam to hit. If it hits the upper sensor the control system raises the blade. If it hits the lower sensor, it lowers the blade.
So rob-o-doze flattens a spot, then to solidify the surface apply some urethane resin. Smooth-On makes a couple of them that “kick” in about 30 seconds after mixing and are fully cured in a couple of minutes though still a bit flexible until they cool down. The robot could apply a gentle spray of such a resin to the surface, mixed right as it exits the nozzle. It would soak into and bind the regolith.
Once a layer is solidified, spread a layer of regolith over then resin it. Repeat as needed until the landing pad is the desired thickness. Some finely powdered metal or ceramic could be mixed into the last couple of layers for increased heat resistance.
If a rig is assembled on the Moon to pick up and carry modules for the base, then the number of landing pads required would be reduced.
“Their experimental technique would allow a rocket engine to literally build its own landing pad by spraying molten aluminum as it approaches the lunar surface.”
I suspect aliens may have a patent on his. Burn spots, crop circles, etc.
After the first landing, shouldn’t the dust and small rocks be blown away ?
One big engine will dig a hole, but a number of small ones, distributed around the vehicle, will dig less,
especially if canted outward. The vehicle should be pretty light at touchdown, maybe 1/4 the mass
of a full up lander, especially if liftoff isn’t expected. (cargo) or the ascent stage is much smaller.
No mention of how much extra propellant is needed due to the heat absorbed in melting the alumina.
That sounds like an awesome idea. I own the onlyBlock 2 Apollo Guidance Computer that has been powered up since the last moon mission. Please check out my website www. spacecomputer.org.
Doesnt the problem seem to be the mass of aluminium you would need and the fuel necessary to burn it? Seems very costly in spaceflight terms to me.