We’d love to say that all of our projects worked perfectly on the first try, but the average Hackaday reader is a bit too experienced to buy a fib like that. The reality is, DIY projects rarely get everything right out of the gate. It takes some time to identify issues and work out all the kinks. But of course, that’s half the fun.
For a perfect example of this process, check out the latest update on the 3D printed DSLR camera mount that [isaac879] has been working on. When we last checked in with this project over the summer the mount was already impressive, but with the latest improvements and the addition of a whole new axis of movement, this homebrew camera motion system is an extremely compelling project for anyone who wants to take their project videos to the next level.
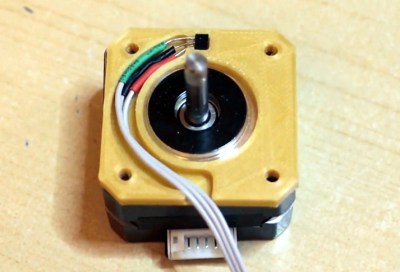
Back in June, the mount [isaac879] showed off was only capable of pan and tilt. But as you can see in the video after the break, he’s since mounted that to a track made of 20×40 aluminum extrusion and added another stepper motor. This allows the pan/tilt mount to move itself back and forth on the track to get those slick panning shots that all the cool kids use in their videos nowadays.
But even if you’re not interested in the slider aspect, the core pan/tilt mount has also received a number of refinements over the last few months. Perhaps the most obvious is the switch over to thinner and lighter stepper motors. Reducing mass is always an improvement with a moving system like this, and in the case of the pan motor, the shorter can prevents a potential collision with the camera itself. Obviously the smaller motors are weaker, but [isaac879] considers that a feature; the mini motors will just start skipping steps if things get bound up instead of potentially damaging your expensive camera.
He’s switched to flange bearings to help hold the frame together, improved wire routing, added a mounting point for the electronics, reprinted the pinion gears in a flexible filament to help absorb some vibrations, and switched over to TMC2208 stepper drivers. The new drivers may actually be one of the biggest usability upgrades, as they allow the entire mount to move faster and more accurately. Critically, [isaac879] also reports the new drivers have solved a troublesome vibration issue he was seeing when the camera was moving slowly.
Obviously you can throw together a simple pan and tilt mount with a couple of servos and some zip ties if you only need to use it once or twice, but a project of this caliber would rightfully become a permanent fixture in your workspace. Perfect if you’re looking to up your project photography game.
[Thanks to Steven for the tip.]
The AccelStepper library includes MultiStepper.cpp, .h for the purpose of driving multiple axes synchronously. Wouldn’t this work for you?
From the Multistepper page:
“Caution: only constant speed stepper motion is supported: acceleration and deceleration is not supported All the steppers managed by MultiStepper will step at a constant speed to their target (albeit perhaps different speeds for each stepper).”
You would need to write your own acceleration planner on top of Multistepper which would make it kinda pointless in my opinion. I believe this I why I got frustrated with Multistepper in a previous build.
Funny enough, I’ve been printing that during the last week or so.
Modified it a bit though, to fit a 600D, which is about a cm wider than his 200D. Widened the U-shaped part, pulled the gear side support further outside and also made both side supports a tad taller to have more space for the lens to move about.
I have a system that uses AccelStepper and controls practically any number of steppers with full acceleration control!
The same system could be deployed on this framework.