If there’s an enduring image of how large steel structures used to be made, it’s probably the hot riveting process. You’ve probably seen grainy old black-and-white films of a riveting gang — universally men in bib overalls with no more safety equipment than a cigarette, heating rivets to red heat in a forge and tossing them up to the riveters with a pair of tongs. There, the rivet is caught with a metal funnel or even a gloved hand, slipped into a waiting hole in a flange connecting a beam to a column, and beaten into submission by a pair of men with pneumatic hammers.
Dirty, hot, and dangerous though the work was, hot riveted joints were a practical and proven way to join members together in steel structures, and chances are good that any commercial building that dates from before the 1960s or so has at least some riveted joints. But times change and technology marches on, and riveted joints largely fell out of fashion in the construction trades in favor of bolted connections. Riveting crews of three or more men were replaced by a single ironworker making hundreds of predictable and precisely tensioned connections, resulting in better joints at lower costs.
Bolted joints being torqued to specs with an electric wrench might not have the flair of red-hot rivets flying around the job site, but they certainly have a lot of engineering behind them. And as it turns out, the secret to turning bolting into a one-person job is mostly in the bolt itself.
A Desk With a View
My first exposure to tension control bolts started with getting really lucky at work. Back in the early 2000s my department relocated, and somehow I managed to get a desk with an actual window. Being able to look out at the world was amazing, but then one day the company started building an addition right outside my window. That was a mixed bag for me; true, I’d lose my view as the six-story structure was built, but in the meantime, I’d get to watch its construction from the comfort of my desk.
I watched with amazement as the steel frame went up, the ironworkers quickly and efficiently bolting the columns and beams together. One thing I noticed was that bolting seemed to be a one-man job, with a single ironworker tightening the nut with an electric wrench without the need for anyone backing up the head of the bolt on the other side of the connection. This perplexed me; how could the bolt not just spin in the hole?
I got my answer when I saw something fall out of the wrench after the ironworker removed it from the tightened connection. From my perch by the window it looked like the end of a splined shaft, and I could see that one end was obviously sheared off. That’s when I noticed that all the as-yet untightened bolts had the same spline sticking out past the nut, and it all clicked: the spline must fit into a socket inside the wrench coaxial to the socket that tightens the nut, which holds the bolt so the nut can be tightened. What’s more, it was clear that you could use this scheme to automatically torque the connection by designing the spline to shear off at the required torque. Genius!
Stretch and Snap
While I wasn’t quite right with my analysis, I was pretty close. I only learned much later (like, while researching this article) that the bolts used for structural framing are called tension control bolts, or TCBs, and that there’s a lot of engineering that goes into them. But to understand them, we have to take a look at bolted connections, and find out how they work to keep everything from buildings to bridges from falling down.
We’ve taken an in-depth look at bolted connections before, but for the TL;DR set, the short story is that bolts are essentially really strong springs. When you tighten a nut on a bolt, the bolt stretches a bit, which provides a clamping force on whatever is trapped between the head of the bolt and the nut. The degree of stretching, and therefore the amount of clamping force, depends on the strength of the material used to make the bolt, the size of the bolt, and the amount of torque applied. That’s why most bolted assemblies have a specified torque for all the bolts in the joint.
For structural steel, joints between framing members are carefully designed by structural engineers. A host of calculations go into each joint, resulting in detailed bolting plans. Some joints have a lot of bolts, sometimes 20 or more depending on the application. The hole pattern for each member is determined before any steel is cut, and each framing member usually arrives from the fabricator with the exact number of holes specified in the plan. The plan also specifies which grade of TC bolt is to be used on each joint — more on that below — as well as the diameter and length of each bolt.
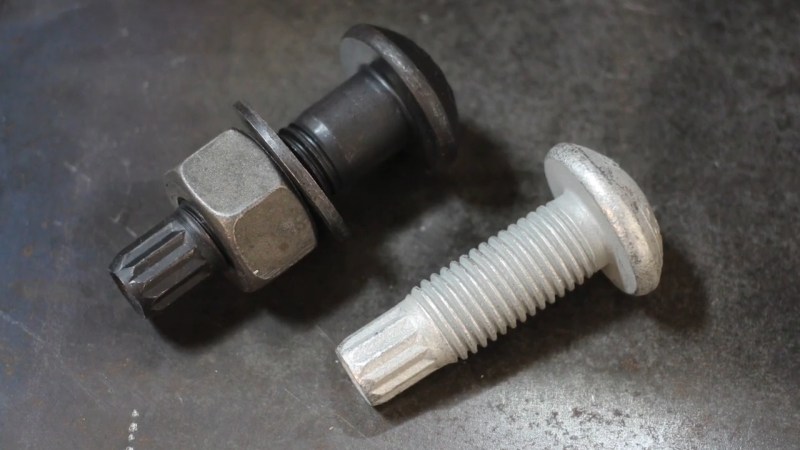
As ironworkers build the frame, they first use a spud wrench to line up the bolt holes in the two members they’re bolting together. A spud wrench is a large open-end or adjustable wrench on a long handle that tapers to a point. The handle is used to drift the bolt holes into alignment while the ironworker inserts a TC bolt into the other holes. The bolts are initially just hand-tightened, but a critical part of the assembly process, called snugging or pre-tensioning, follows.
Snugging is somewhat loosely defined as the tightness achieved “with a few impacts” of an impact wrench, or “the full effort of an ironworker” using a standard spud wrench. Everything about snugging is very subjective, since the number of “ugga-duggas” that count as a few impact wrench blasts varies from user to user, and ironworkers similarly can apply a wide range of force to a wrench. But the idea is to bring the framing members into “firm contact,” which generally amounts to about 10 kps or “kips”, which is 10,000 pounds per square inch (about 70 MPa).
Once all the bolts in the joint are pre-tensioned, final tensioning is performed. The tool I saw those ironworkers using on TC bolts all those years ago goes by many names, with “shear wrench” or “TC gun” being the most generic. It’s also known as a “LeJeune gun” after a major manufacturer of TC bolts and tooling. Some shear wrenches are pneumatically powered, but more are electrically operated, with cordless guns becoming increasingly popular. The final tightening cycle begins by engaging the TC bolt spline with the internal socket and the nut with the outer socket. The outer socket tightens the nut to a specified torque, at which point a slip-clutch shifts power transmission from the outer socket to the inner socket, reversing the direction of rotation in the process. This applies enough torque to the spline to twist it clean off the TC bolt at the weakest point — the narrowed neck between the spline and the threaded section of the bolt. This leaves the bolt properly tensioned and with just the right amount of thread showing.
Tools of the Trade
TC bolts generally come in two grades: A325 and A490. Both are based on ASTM International standards, with A325 bolts covering the tensile range of 120 to 150 kps (830 to 1,040 MPa), and A490 covering 150 to 173 kps (1,040 to 1,190 MPa). Most TC bolts have a rounded head, since there’s no need to grip the bolt from the head end. That provides a smoother surface on the head side of the joint, making it less likely to get damaged during installation. Depending on the application, TC bolts can be treated to prevent corrosion, either with galvanizing or a passivated treatment.
If a TC bolted joint needs to be taken apart, the fact that the spline has already been snapped off presents a problem. To get around this, a special accessory for the wrench known as a reaction bar is used. This is essentially an inner socket sized for the nut and an outer ring with a sturdy torque arm welded to it. The arm jams against an adjacent nut and provides the counter-rotation needed to loosen the nut.
Lot testing is also very important for code compliance. This involves picking random TC bolts from every lot to test on a Skidmore-Wilhelm machine, which hydraulically measures the tension on a bolt. Strict procedures for pretensioning and final tensioning of each bolt are followed, and results are recorded as part of the engineering records of a structure.
Nice quality article. Thank you for teaching me something new.
Agree!
Aerospace companies use similar bolts (Hi-Locks, Hucks, snap-drive nuts, etc) for controlled torque.
This seems to require that the friction of the rotating bolt be the same for each joint. Wouldn’t a better way be to measure the elongation of the bolt?
Because of that, I bet they’re pretty specific about the washer. But yeah.
Measure elongation? Maybe, but I bet it’s hard to be on both sides of the steel plate at once, sometimes.
It is true that fiction (both between nut/washer and in the threads) plays an important role – leading to variations on the preload even for the same tightening torque. As suggested, measuring elongation is indeed a more accurate way of determining preload, but is hard in practice (as Elliot mentions). I believe that in some high-end applications this is done using ultrasound during tightening.
There are bolts with a small hole bored through the middle about half-way through, and a strain gauge glued to the inside of the hole to measure the elongation of the bolt. The strain gauge is a “relatively” cheap way of doing it, if you absolutely must have equal known tension in your bolts.
I thought of measuring elongation by the number of turns after snugging, and in fact this has a name – the Turn of Nut method. https://www.gwyinc.com/turn-of-nut-method/
Friction can vary some without keeping you from finding the point of snugness. So once you are snug, from that point the threads per inch of the bolt is a fixed quantity and you can rotate through a fraction of a turn and get that much extra elongation.
That’s very common for engine head gasket bolts/studs.
Or all kinds of shadetree mechanicry, except without all those silly little numbers.
Ultrasonic extensometer, measures from one side. Pretty common in the non-destructive testing (NDT) industry. I used one once to tighten the head bolts on an ICE engine after replacing the head gasket. Much more accurate than a torque wrench.
Cool!
Fun fact, there are bolts that do this for you…
https://www.mcmaster.com/products/~/tension-indicating-hex-head-screws/
Can’t quite visualize the application where you use a $28 bolt instead of pulling out your torque wrench, but hey – the fact that they are made and stocked means that somebody out there buys them
Material is almost never the costliest factor in these situations, it’s the labor cost. And any connection that has a torque indication will almost certainly be inspected by someone else post-installation, so speeding that up matters too.
I’m an ironworker, never used those before (but heard of them).
With regular bolts and nuts, typically you don’t need to back them, (unless the nut can’t be turned anymore due to dirt etc.) The impact will spin the nut tight all by itself and the head will bite into the steel.
Also typically we don’t torq everything to spec, you just set the impact to whatever setting is close and use that range. With the newer impacts you can change the settings to get even closer with a phone app. Then you mark that it’s been impacted.
But every job is different.
Notice that they turn back to red from black if they become loose. This means that you can visually inspect them periodically to ensure that they are all still torqued correctly. I can imagine a lot of safety critical applications where you have bolts that are easy to see, but not easy to get to. Think about bolts inside an airplane. It would be easy to view them with a boroscope, but removing enough parts to get at them would be very costly.
Who knew!! McMaster also has much cheaper “squirter washers” that do basically the same thing, but for around $1.50/PC.
https://www.mcmaster.com/product/91358A005
Well that’s the neatest thing I’ve seen all day, very elegant and low-cost design compared to many other solutions.
There is an accepted method for essentially doing this to standard structural bolts. The AISI “turn of the nut” method requires a set rotation of the nut beyond the snug tight point, which corresponds to a set elongation since the thread pitch is known.
All bolts torqued to a spec are to trying an induce a particular pre-load on the bolt, which would result in a specific elongation. Direct bolt elongation measurement would be preferred, but how would you do that in the field? The answer is that you can’t, not in a way that allows you to place thousands of bolts in a reasonable time frame. So torque measurement is your stand-in for that. The axial load to torque relationship is very much affected by the friction between the various surfaces. There are numerous methods designed to make field torqueing (and inspector verification of that torqueing) of bolted connections faster; indicating bolts, indicating washers (called “squirters)”, TC bolts, etc. It still isn’t perfect (I’ve found loose bolts in structural connections), but it works well enough.
I briefly worked for a company that made hydraulic bolt pullers, these stretched the bolt to a specific tension the nut was then hand tightened and the pull released. This gave a an accurate tension to the bolt.
OK, that’s just wild.
… assuming the bolted material is incompressible. (Or incompressible enough for the applyable pull, but the compressibility should be specified and accounted for in critical applications. Paint should be applied afterwards, obviously.)
Those are called constant tension bolts.
We used them extensively in a shipyard I worked at.
The bolt was inserted and a “tommy nut” put on it. Them a hydraulic cylinder was screwed on the end and force applied until the bolt body had stretched the decided amount. Then the time but was tightened, but not a lot and the tension on the cylinder released.
We one had a huge 16 cylinder Sulzer diesel engine that was 167 get long. There were some 50 of these bolts on the foundation.
That was fun.
I was surprised to see these on the (plastic) screws for a replacement toilet seat I installed a few weeks ago. They supply an adapter tool to use a conventional socket to drive it. Perfect tension — no loose seat, no stripped screws.
You also find them on the little screw that locks a backflow preventer onto your outside hose spigot. In this case the slotted head shears off so the homeowner can’t remove it.
The problem with that application is that sooner or later the rubber washer degrades and you have to go over to your Dad’s house and lie upside down in the dirt for half an hour, carefully drilling the screw out with a Dremel in order to change a part that should take 5 seconds.
Ask me how I know this
How do you know this?
Fortunately, in my case, I was able to get the backflow preventer off of the faucet, and drill out the screw on the drill press.
You have my sympathy.
Did it come off easily, or did you force it?
Excellent article!
I bumped on a couple of minor things here. First, “kips” is simply short for kilopounds and kips per square inch is generally (e.g. in AISC 360) abbreviated ksi. I have never seen “kps” used in structural engineering, though I can’t speak to other disciplines. Second, while the process is described correctly, the term “pretensioning” refers to actually applying the specified torque to the bolt, as it is tension applied to the bolt before loading the connection.
“The outer socket tightens the nut to a specified torque, at which point a slip-clutch shifts power transmission from the outer socket to the inner socket, reversing the direction of rotation in the process.“
I don’t follow the reasoning here. The tool has a gun shape; the operator is not going to be able to apply much torque themselves. So the tool is torquing the nut and the bolt relative to each other. So if the direction of rotation (that is, of the bolt and nut relative to each other) is reversed, doesn’t that just mean the bolt gets unscrewed?
Put differently: does the slip clutch slip before or after the shearing torque is reached? If before, how does it get sheared off? If after, why have a slip clutch?
There’s likely no clutch, or torque setting on the tool at all. The gun doesn’t turn because the clockwise torque applied to the nut is countered by a counter clockwise torque applied to the bolt. The end of the bolt shears off when the torque gets high enough to shear it off. That torque is designed into the bolt itself.
Yeah, that was my take as well. Still, presumably Dan Maloney actually did research for this article, so it’s hard to square that with his description.
Maybe he meant differential, rather than clutch? The thing would need a differential to keep it from twisting the operator’s wrist off once the bolt sheared off. But slip clutch is pretty specific…
Maybe a clutch could be part of it, if there’s a kick when it shears and starts spinning.
As for a differential, the way I’d design something to get something to counter-rotate on the same axis at the same speed is to drive the carrier of a planetary gearset with a motor and put the spline on the sun and the socket on the ring. (Well, do that after a gear reduction, anyway) That’s already got differential action. Even once the sun starts turning very fast because it’s sheared, there’s going to be some force trying to rotate the ring because it can’t reach infinite speed with friction and such, I would think. I wonder if that torque is enough to need to clutch out to save their wrist? It’s not my specialty, but if there is one that may be why.
@spaceminions
That’s not what a differential does. (It’s also definitely not what this tool does; the bolt doesn’t rotate while tightening, and there’s certainly no need for them to rotate at the save rate. Take a look at the video.) A differential would be used here to isolate the torque from the handle while still torquing the nut and bolt relative to each other.
Ben, I did watch the video, and in the video it’s clear that the spline on the bolt is rotated at the end to shear it off. And during the shearing process, the tool doesn’t seem to move, so the forces applied to the operator’s wrist must be manageable. The article tries to say that a clutch is used to allow the spline to be rotated once it’s time. But that doesn’t explain it, because the bolt is what sets the torque, and it does so by shearing, so the tool seems like it is just applying torque in both directions the entire time. And doing that would make the most sense if it makes sure that the torque in each direction is equal, to spare your wrist having to correct.
I guess it could technically do that with a motor with two rotors and no stator, all powered by a bunch of slip rings or something, or it could have two separate motors that it carefully balances, but that sounds way less reasonable than powering a gearset that lets you use only one regular motor.
And what I described before was using epicyclic gearing to produce two opposing outputs, only I went further to guess that the numbers of teeth will affect the torque split by affecting the speed ratio. But you don’t agree with that. Maybe you’re saying none of that is right, or maybe you’re saying that’s not a differential or it’s not necessary to balance the ratios. So then what exactly is it that you’re saying it does?
What you’re missing is, torque is relative. If you were using this tool to tighten a bolt, while you were using it you could freely turn the handle back and forth with little resistance and no effect on the taste at which the nut was being screwed down. The torque is decoupled from the handle entirely, despite the fact that the handle is where the motor is. That’s what requires a differential. It’s technically correct to say that torque is applied “in both directions”, but only because (by Newton’s first law) all torque is applied in both directions.
Er. Third law, that is.
I’m not missing that; in fact that’s exactly what I was trying to tell you, but you insisted it doesn’t work that way.
It’s been 4 years since the last article in this series
So, it is still a series.
It’s still serial murder if there are years between the victims. I think Dan deserves the pass here, especially ‘cos this was a really interesting article.
I just had a metal building up and I was wondering how they were doing it with one person (and two supervising, grrrrr)
The artwork is great, as usual. But wait… an octagonal nut? This is blasphemy!
Do any of these report the shear force at the end so you can double check the bolt grade is correct?
fantastic write up. thanks
Damn fine write up. holokrome puts out some of the best (accessible) literature on torque and thread if you are interested in the realm. They make good stuff too.
Sounds like someone’s gonna have a fun time with this articles subjects cousin, Torque-to-yield fastener.
Minor nit: the reaction bar is solely to allow use of a powered wrench without the operator having to provide the reaction force (important when you’re up on a scaffold or suspended in a harness) and works identically for TCBs and regular hex bolts. The reaction bar will do nothing when a TCB has had a nut freeze onto the bolt – the bolt & nut will just spin in the hole no matter how fancy a tool you use. The solution is the same as any bolt: cut a head into the opposite end to hold it in place, cut one head off and pull the remains through, or drill the thing out.
You will see TC bolts on buildings but probably never see them on bridges. Instead of being called “tension control” they should be referred to as “torque control”.
A dry (unlubricated) bolt requires more torque to turn the nut and it may not get the tension required to bring the layers together tight. A dry TC bolts can snap after reaching the it’s torque value and appear to be good but in reality did not get the proper tension.
To make matters worse, the code does not allow one to lubricate TC bolts in the field.
With most buildings, it may not be critical but it is for bridges. The difference is the static loads on most buildings compared to the cyclic loads on bridges.
Bridges use Direct Tension Washers (DTI) washers, some times refered to as Load Indicating Washers. DTI washers can be verified in the field that they have the required tension even if the bolt was dry.
DTI washers have protuctions that requires the bolting crew know which side the protuctions go on. That plus the right size feeler gauge to measure the gaps between the washer and structures once the protuctions are compressed. Need to keep on eye the bolting crew that might be tempted to hammer the protuctions flat before installation.
Another alternative is the “turn of the nut” method to ensure you are getting proper tension. It does require the bolt up crew is properly trained on how to “match mark” the turns. Many steel erectors do not which leaves the bolting inspector questioning if it was done properly.
The code does not prohibit bolts from being lubricated in the field if DTI washers or if the “turn of the nut” method is to be used.
I recommend lubricating bolts with a wax based lubricant to get better tension for less torque.
The article claims that rivets were replaced by these tension bolts, but I was taught that rivets were replaced by welding components together – at least in structural welding.
This seems somewhat promotional.
Your suspicion, in this crazy mixed up world, is possibly warranted. But it’s misplaced here at Hackaday.
We have never run anything promotional, and will not. Our ads are very obvious — they are in the banners. Our content is absolutely editorially independent.
Which is all to say: Dan saw these things out in the wild, thought they were neat, did his research, and wrote this piece up for you.
This is an excellent “FYI” post, thank you!
One of the most impressive things I’ve ever seen was a demo from a structural engineering colleague featuring a saw-tooth anti-vibration washer. He showed me a simple setup with a bolt, washer, and butterfly nut, and get this—he tightened it just by blowing air on it! Then he asked me to try undoing it, and let me tell you, it was nearly impossible by hand. Incredible.
For industries like transportation (think railways, airplanes, etc.), constant vibration leads to expensive maintenance and significant risks if components loosen. This soluion the best engineering trick I’ve seen for vibration issues, hands down!
I’ve have had vibration issues in electrical switchgear (my professional life) and next time I have that application I will be looking to use this principal. I also plan to use them when I buy my kids a treehouse (well, I’m telling everyone the treehouse is for the kids, but we all know it’s going to be dad’s man cave!).
Youtube video from manufacturers: https://www.youtube.com/watch?v=IKwWu2w1gGk