There are plenty of hard jobs out there, like founding your country’s nuclear program, or changing the timing chain on a BMW diesel. Making your own mechanical watch from scratch falls under that umbrella, too. And yet, [John Raffaelli] did just that, and prevailed!
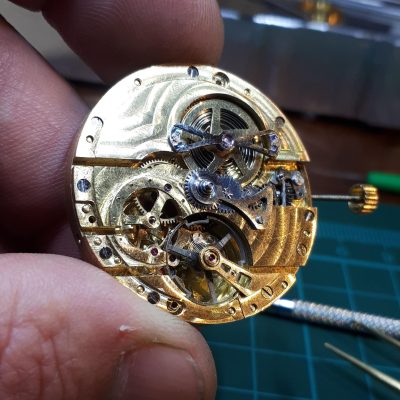
Only a handful of components were purchased—[John] grabbed jewels, sapphire crystals, the strap, and the hairspring and mainspring off the shelf. Everything else, he made himself, using a fine touch, a sharp eye, and some deft work on his machine tools. If you’ve never worked at this scale before, it’s astounding to see—[John] steps through how he produced tiny pinions and balance wheels that exist at sub-fingertip scale. Even just assembling something this tiny would be a challenge, but [John] was able to craft it all from scratch and put it together into a functioning timepiece when he was done.
The final piece doesn’t just look great—we’re told it keeps good time as well. People like [John] don’t come along every day, though we do have one similar story in our deep archives from well over a decade ago. If you’re cooking up your own bespoke time pieces in your home workshop, don’t hesitate to drop your story on the tipsline!