It’s time once again to see how those tax dollars are spent, this time in the form of a “Data Entry Keyboard” manufactured by Hughes Helicopters. This device was built circa 1986 or so, and was used in the AH-64A Apache. Specifically, this panel would have been located by the gunner’s left knee, and served as a general purpose input device for the Apache’s Fire Control System. Eventually the Apache was upgraded with a so-called “glass cockpit”; consolidating various vehicle functions into a handful of multi-purpose digital displays. As such, this particular device became obsolete and was pulled from the active Apache fleet.
The military vehicle aficionados out there may know that while the Apache is currently a product of Boeing, it was originally designed by Hughes Helicopter. In 1984, McDonnell Douglas purchased Hughes Helicopter and took over production of the Apache, and then McDonnell Douglas themselves were merged with Boeing in 1997.
So it’s somewhat interesting that this device bears the name of Hughes Helicopter, as of the time it was manufactured, they would have been known as McDonnell Douglas Helicopter Systems. Presumably they had to work through existing stock of components that already had Hughes branding on them, leaving some transitional examples such as this one.
But you didn’t come here for a history lesson on the American military-industrial complex, you want to know about the hardware itself. So let’s crack it open to see what we can learn about this piece of aviation history.
Due Diligence: What is This Thing?
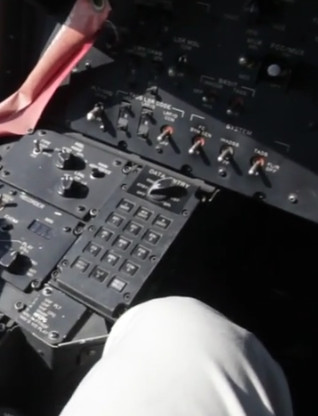
I should mention that when I first got this particular piece, I had no idea what it was. Like most of my other military finds, this one came up on an eBay Alert I had set up for surplus electronic components, and was listed simply as “Military Surplus Data Entry Keyboard”. It looked a bit beat up, but it was cheap, and I like cheap.
When it arrived a closer look revealed the contract number stamped into the data plate on the rear of the device, and searching that online brought me to a scan of Technical Bulletin 55-1520-238-23-1, “WARRANTY PROGRAM FOR HELICOPTER, ATTACK AH-64A” from 1988. Sure enough, in Appendix A “AH-64 WARRANTED COMPONENTS”, was listed “Panel Assy, Data Entry K/B O”. So now I knew this particular piece of hardware was from the original AH-64A Apache. Unfortunately, the last AH-64A was converted to an AH-64D in 2012, so finding pictures of the cockpit was a bit harder than I’d expected.
In the end, YouTube saved the day. I found somebody who uploaded video of them sitting in what must have been one of the last remaining AH-64A Apaches in 2010, and sure enough you can see the “Data Entry Keyboard” as he pans across the panel. Mystery solved.
Keyboard Dissected
It seems reasonable to start our disassembly with the keyboard itself, which is held on to the front of the device with six bolts. With the bolts removed, you’re able to pull the keyboard away and can get to work taking out the small screws that hold the back panel on.
With the keyboard broken down to its basic components, we can see that the operation is not really that different from the cheap membrane keyboards we’re all used to playing with. The mechanism here is considerably more robust of course, as it was intended for a military aircraft, but the idea is the same. Each key on the front of the device pushes a small membrane dome, which in turn makes contact with the traces on the PCB. There are metallic contacts in each dome however, as well as a tiny spring, so the tactile feedback on the keys is very good. Important when your operator is wearing gloves and potentially in a combat situation.
Internal Construction
With the keyboard itself removed, we get our first look inside the device. I was immediately struck by the absolutely gorgeous, and no doubt incredibly expensive, connectors used throughout. Presumably to protect against vibrating lose, the connectors can’t simply be pulled out, and you need a small slotted screwdriver to unscrew and separate them. They are designed so that they will only go together one way, and prevent bending of the pins since you have no choice but to evenly loosen or tighten both sides or else it will just bind. They’re annoying to deal with, no question, but you have to admire them.
The second thing that surprised me is that there are actually two separate boards inside the device, connected together with a backplane. The backplane features a standard DB15 male port, which incidentally is the only form of external electrical connection on the entire device, and is connected to the “blades” with a larger version of the screw-down connectors.
Power Supply
The first of the “blades” we’ll take a look at is the power supply. This board is exceptionally simple, in fact it looks almost homemade. The traces on the board look like they could have been masked off with a marker, and components are minimal to the extreme. The star of the show here is the Texas Instruments LM123K, a military grade 5V regulator that can provide up to 3A and can handle input voltages as high as 20V. There’s an inductor and a handful of capacitors to help smooth things out, but that’s it.
I find it fascinating that the device has its own beefy internal voltage regulator like this. It seems the kind of thing that could have been installed in a separate module and provide 5V to all of the devices in the cockpit. Perhaps from a reliability standpoint, the designers felt it was better to provide each mission critical piece of equipment with its own dedicated power supply.
Computer Board
Now I imagined there would be some interesting electronics inside this piece of equipment, it’s the whole reason I bought the thing. But I didn’t expect there would be a complete computer inside of it.
The “Data Entry Keyboard” is powered by an Intel MD8085AH/B, the military version of the venerable Intel 8085 CPU, paired with a MD8155H/B 2048-Bit HMOS RAM module. The ROM is stored on dual MD8755A/B 2 KB EPROMs. All of these components are rated “Class V Space Level” according to their respective datasheets, so if you are planning on building a Mars rover or something, this might be a good source for some otherwise very expensive chips.
Powering Up
In the previous installment of this series I successfully revived a 70 year old “CP-142 Range Computer”, so I felt obligated to attempt a similar feat on this considerably less archaic piece of equipment. I was spurred on by the standard DB15 connector on the device, as well as the fact that it was very easy to trace out the pins for power; all I had to do was check continuity between the input leg of the LM123K regulator and the pins in the connector. Knowing the regulator can handle up to 20V from the data sheet, I provided the “Data Entry Keyboard” with 12V on the appropriate pins of the connector and hoped for the best.
I probed around the remaining pins with the oscilloscope, looking to see the telltale signs of digital communication. Eventually I found something, but it seems that either I’m making naive assumptions about how this device should work (very possible), or there’s something wrong with it. There is indeed a digital signal of some sort coming out of the device, and it changes when I hit different keys or rotate the knob, but the signal is extremely weak and very garbled.
At only around 150mV and buried in some kind of background noise, this doesn’t strike me as expected behavior. My feeling is that something is bad on the board, but the couple checks I made (CPU is getting correct voltage, clock at proper frequency) didn’t show anything obviously wrong. Though with a piece of hardware this old, it could potentially be a bad capacitor hiding on the board somewhere. It would be interesting to see if any Hackaday readers might have worked with this kind of hardware before and can possibly shed some light on what I’m seeing.
Final Thoughts
I wouldn’t have expected it, but this device is actually packed with useful and valuable components. The keyboard itself can easily be interfaced with and would make an awesome PIN pad for a security system or similar projects. How many people can say they’re handling authentication with an authentic piece of hardware out of an Apache?
The computer itself, if you’re into that sort of thing, is an incredible find. As old as they are, these military grade computer components are very valuable and could be the makings of an extremely unique retrocomputer build. Dumping the existing ROM would be an interesting first step, and erasing the chips with UV and replacing the ROM with new code the next logical step.
Overall, I think this is a fantastic microcosm of military technology as a whole. The cost to build this device must have been astronomical, but once you have a look inside you can’t really deny the construction commanded the premium expense at the time. A few years later, for all the money and R&D that must have gone into this lowly keyboard, they were all chucked when the Apache was updated. No matter how much it costs to build something, you can’t stop the march of progress.
Really cool article! Would this thing be capable of CP/M and thus Doom?
I want to see a rom dump! I wonder what, if any protections were written into the code to protect it from accidental failure.
There is a version of CP/M that runs on the 8085. One instruction in the BDOS has been changed to accommodate the difference in the status flags between 8080 and 8085, so the ‘bog standard’ CP/M-80 will not work.
vibrating lose?
Curious what kind of IP rating this has. Doesn’t seem like much, oddly enough?
For liquids it probably had to continue working as a liter of “hot liquid” was poured over it. As for vibrating lose, helicopters are the worst for vibration, constant vibration from the rotors. What surprised me was the heatsink on the voltage regulator. There is no airflow in that box, heat only gets extracted via conduction from the chassis and radiation off the exposed face.
“helicopters are the worst for vibration”
“Gliders sail on gossamer wings, helicopters beat the air into submission”
-unknown
You think rotor vibration is bad, wait till that 20mm starts cutting loose under the seats!
B^)
Toss-up which will have looser parts. Copter, or pilot?
30mm*
Initially the Apache had big issues because the fuses would pop out when the gun was fired as I recall, and they had to reset things all the time.
Also – the damn window was leaking..
And the blades would grind down very quickly in desert areas like Iraq.
It was an embarrassment really.
Isn´t that a 30mm cannon ?
With the sticker missing from the EPROM, I wonder if they felt the need to erase it before disposal.
Unlikely, though of course possible. More likely that the glue on the sticker gave up. When I open up some 30-40 year old electronics usually I’m greeted with labels that come off at the slightest touch. Often the first thing I do is tape down the surviving ones so I don’t lose any more of them.
Funny that everything is mil-spec, except the labels. :)
If it lives in a sealed dark box with no internal UV (or x-ray or gamma ray) sources the label isn’t strictly required once the lid is screwed down.
Look into various avionics communications busses — ARINC 429, MIL-STD-1553, etc… It’s probable that the digital communications are on a differential pair, possibly transformer-coupled, and possibly requiring some form of termination. See if you can trace back pins on the DA-15 connector to any particular chip on the CPU board that may be a transceiver.
I wondered if anyone was going to pick the nit about “DB15”. “DB” really referred to the 25 pin size. “DA” is, yes, for 15, “DC” for 37, “DD” for 50 pin, and “DE” for 9 pin (where I most often see “DB” misused.
Harold Hill Said: “DB” really referred to the 25 pin size.
Actually for the normal D-series pin density (referred to as High Density vs. Double Density) DB refers to two pin-count connectors: DB-25 and DB-19. The variations get even more complex for the High Density D connectors. There is a lot more here:
https://en.wikipedia.org/wiki/D_connector
Correction: The correct base-URL for the Wikipedia article is actually:
https://en.wikipedia.org/wiki/D-subminiature
But this link works too:
https://en.wikipedia.org/wiki/D_connector
Dang, I never knew. I done been sayin’ DB-9 fer years — but now thanks to you, I is smarter!
Seriously, thanks — I thought it was all DB until reading your comment.
Then there’s Apple’s bastard 19 pin D-Sub floppy connector that has no official letter size designation. The users of it were Apple and 2 or 3 other obscure things. Big Mess-O-Wires has a writeup on how he had to have a batch custom made for his Apple floppy emulators. What made it possible was some parts suppliers wanted a bunch and went in on the order. He put up a photo of *the entire world’s supply* of new D-Sub 19 connectors in boxes on his back porch.
It’s not often one gets to say they have possession of 100% of a thing like that. :)
I thought it was a HaD staff member who had those…
Same for 23 pin connector. I found a pigtail of one in a old box of parts, and quickly discovered that I won’t be able to use it for anything.
Good chance that it’s MIL-STD-1553 standard as that bus was used in the Apache and other military aircraft although I don’t see the necessary transformers. One thing to note on that protocol is the slave units will only reason when interrogated
And then it’s only name, rank and serial number!
Doubtful that it is 1553, I would expect something that looked more like a coaxial connection for that. There is a good chance it was erased as part of a declassification, since almost everything was probably classified to some level. But it also could be looking for a voltage on a pin to indicate it needs to start.
I would not expect the device to react to keypresses at all if it would be erased. But it could be something simple, like an open collector/drain or current loop output, that only needs a pull up to work.
There are 15 lines at max. at the connector. It can not be that difficult to find out, where they go. Probably that’s no multi layer board.
s/on/only/
If it on needs to make a short haul it may even be something as simple as CAN or an open collector output (at which point the high points would be noise when the low-side driver is shut off) but I expect your theory is on the money, I was about to comment (until I saw your comment) that the scope trace and description looks somewhat like what you see grabbing one leg of a balanced differential signal with a high impedance single-ended probe and no terminating resistor.
Could be the module needs some sort of “enable” signal/pins shorted/etc. before it lights up and starts talking…
If it runs at 12 volts, it will look good mounted in your car!
Nope, at best it’d be 22-29VDC. Or it’s a 115VAC @ 400hz.
Don’t forget, that the regulator allows only 20V max. and that has to be DC. There is no rectifier on the power board.
Not with that LM123K on the frontend. Spec sheet says input voltage is 7.2 – 20 VDC.
“Overall, I think this is a fantastic microcosm of military technology as a whole. The cost to build this device must have been astronomical, but once you have a look inside you can’t really deny the construction commanded the premium expense at the time. ”
Naturally. No one wants to be in a life or death situation and their equipment craps out on them.
That’s why they award the contracts to the lowest bidder!
B^)
Have you found any obvious EMP hardening feature? I think those choppers are resistant.
“Class V Space Level” implies radiation hardening, which includes EMP resistance.
EMP resistance has more to do with the power supply and input filtering than the actual chip level used.
But a lot of those chips, the Harris-manufactured 8085 included, were done in silicon-on-sapphire which is about as immune to EMP as solid state gets. They were also frightfully expensive, but anything that’s ready to go into space is.
My dad was involved in the development of the AH-64 from the Army side. He was a chopper pilot and human factors engineer working at Aberdeen Proving Ground in Maryland during its development. I think he worked on the heads up helmet mounted targeting system testing. Its to late to ask him about this piece of equipment as he passed away in 1987.
My dad passed on more recently, I know what you mean about liking to ask him questions…
I’ve probably seen your father in photos. I went through about 100 photos of the Apache testing at APG, specifically testing it’s ability to identify targets.
Since the EPROM window is bare I suspect whatever is supposed to be in the EPROM has been erased. That might explain the weird behaviour.
Unlikely – esp given that the EPROM has been a closed box.
Next step in terms of analysis would surely be a logic analyser on the CPU?
But it’s also unlikely that it would have been fielded with its window bare. Even though the box would be sealed, those chips would be in the open before and during manufacture, and the boards might sit in the open for some time before being installed in the device.
At the company I work for, procedures would definitely have prohibited it.
In my experience with avionics, especially those for military systems, having the window exposed is likely intentional. Those systems aren’t intended to be serviced by anyone expect the vendor. Rather, if the module is determined to be faulty, a whole new one would be swapped in and the old one shipped back to the manufacturer.
The logic is that it would prevent some field tech from messing with something they don’t understand, breaking it in a subtle way, then causing the helicopter to fail spectacularly at which point finger-pointing begins happening. This way, any attempt by someone that isn’t well-versed in the device will fully disable it, requiring it to be shipped back to the manufacturer for a new one.
This is also to keep the module from being useful to a reverse engineer in attempting to gather intelligence on the helicopter and/or building one of their own. A vehicle like this would have been right in the thick of it and we were nervous about our designs falling into the hands of the Soviets / Chinese so they can either discover weak points to exploit or to integrate the technologies into their own systems (To be fair, we also did that a lot with their equipment). And while a keypad doesn’t seem like it needs that much protection, it would’ve been easier to just follow the same procedures as the rest of the avionics suite. Although you could gather quite a few useful clues about how everything operates from a device like this, especially since it would interface with targeting, communications, and IFF systems.
“…having the window exposed is likely intentional.”
HIGHLY unlikely. While it takes concentrated ultraviolet light to erase EPROM chips quickly, direct sunlight will erase them in a matter of days or weeks, and even fluorescent lighting will do the job over a few months. AND, long before an EPROM is considered “erased”, its error rate and tolerance to variations in supply voltage and temperature, as well as its noise margins, are degraded. The bits in an EPROM are recorded as an analog electric charge on a capacitor (just as in a dynamic RAM cell), so “erased” is a relative term, and there is no way to determine in the field wither an EPROM has been partially erased, except perhaps by running it through millions of read cycles and looking for misreads.
Leaving EPROMs with unprotected windows is not consistent with designing for military applications. It’s far more likely that there were originally opaque labels in place. These may have used gum-based adhesive (as most such labels used in the 1980s were), which would have dried out and stopped gripping years ago.
Just how omitting labels from EPROMs would prevent people from messing with them or reverse engineering them is not only unclear, but laughable. Are you implying that these were left uncovered so that when the enemy opens the box, the EPROM is instantly erased? Really? As noted above, it takes considerable time for EPROMs to be accidentally erased.
Furthermore, we’re talking about the 1980s here. I was in the military then, and what we didn’t fix in the field was fixed at “depot” level, by other military technicians with the appropriate training and test jigs. It was not general practice to return modules to the manufacturer, and certainly not for low-tech modules like this. In fact, most government contracts prevented this kind of control on the part of the manufacturer.
You can not consider an EPROM with exposed window a viable tamper protection. There is too much time to cover it, before it is erased even with a proper UV lamp.
When produced that window would have been covered, if only to prevent it losing it’s programming during a servicing action. If it’s not covered now it WILL have lost it’s programming. The datasheet for that part says it takes about 3 hours exposure to daylight to fully erase the data. Exposure to more intense light at the 300-400 nanometer wavelength will mean the data is lost even sooner.
You would have to figure out what kind of bus it was built to communicate with. The military aircraft use some bus standards that are not common outside of that environment. The signals will probably be balanced and you may need some syncclock signals to make the communication work. One reason for the local power supply is that aircraft power systems are incredibly noisy (and 400 Hz usually) and there are lots of transients due to coming on and off of power carts and engine generators (which fail quite regularly). They don’t really know on day one what systems are going to be used in the future so rather than try to engineer a one size fits all power supply for a certain bus, it is easier to let each black box support its own requirements in terms of stability and filtering. Power stability and noise (you really have no true earth reference obviously) are the worst issues in aircraft systems. Even something like small cracks that develop is aircraft parts over their lives have been know to oscillate at high frequencies and cause RF noise. I actually worked on a problem like that for the Air Force. It showed up as an intermittent reboot of a device only while in flight and only once in awhile.
Excellent info, thanks for sharing. From that perspective, letting each device handle its own regulation makes a lot of sense.
I saw some (expensive) military 38510 spec ICs on there. Its testing requirements were so severe, that often most parts did not survive to the end of the required tests. I only saw two metal can bulk capacitors on there, which I suspect are solid tantalum and they don’t degrade as badly as liquid electrolytics that dry out. They can’t be too large either, maybe 100 uF or less? Where I worked, we did some mil spec stuff (early 80’s to late 90’s) for the FAA and those parts were harder and harder to get and more and more expensive. Manufacturers just gave up on that market because of its low ROI. Radiation hardened parts are even worse. Intel’s data back then for a UVEPROM spec’d about 10 year life after programming, so I expect that there are “gaps” in the code. The FAA experienced those memory gap problems and eventually (as implied by Intel’s spec) instituted a refurbishment program to update older UVEPROMs. By then (circa 2007?) , it was essentially impossible to get mil parts, so they used commercial parts (duh?) which were mostly gray market parts by then.
I don’t pine for the old days much. Give me an Atmel (Microchip) AT Mega328 or any ARM chip and I will get it to run circles around that old stuff.
Seems the heatsink on the voltage regulator is a bit pointless as it is sealed in an almost airtight box.
If there were no heatsink it might overheat. Either the surface of that airtight box is large enough to conduct away the generated heat, the generated heat is intermittent or some combination of both. Connecting the regulator directly to the housing was probably problematic due to vibration issues.
The environmental control system on the apache was more for the computers than the pilots.
How do I tell this reporter the truth about how this exact keypad was placed in 3 AH 64B models in 1986. I was the Product Manager of the B model prototypes. Rockwell Collins is the source of that data entry device.
It isn’t visible in any of the pictures, but there’s actually a little mesh panel in the back of the black box. Still doesn’t seem like it would get much air flow in there, but at least it’s not completely sealed.
For anyone interested in teardowns of similar tech, try the msylvain59 youtube channel.
Maybe the bus is transformer coupled and you are seeing the capacitive leakage between the windings? This is common in aircraft.
I once bent one of those soft gold pins removing a similar connector on a signal processor unit inside an electronic warfare pod. I was unaware you needed to alternate loosening each end a little bit at a time. I was just a 3-level (apprentice) in my first week out of tech school (USAF). My supervisor came by and showed me an old 7-level (craftsman) trick. Take a retractable ball-point pen and remove the ink tube. Insert the tip of the pen over the gold pin and (very) gently bend the pin back into the upright position. He showed me this after I had already attempted to bend the pin back with a scribe and yes I broke the pin off. Turn-around cost on that unit was about $4,000. Sorry, taxpayers. Never made that mistake again.
I come across a bent pin in a D-sub connector about once a week. The ball point pen trick may increase the survival rate.
Thanks!
*shhhh* We will not tell anyone you’re bending up the serial ports on the servers.
Tech school still in Biluxi, or already moved to Wichita Falls?
Couldn’t say where it is now, but back in 1998-1999 the tech school for electronic warfare technician (2A1X7) was indeed at Keesler AFB in Biloxi, Mississippi.
I feel for ya, I bent a few pins inside an AGP video card slot years ago. I figured I had one chance to try to fix it without breaking the dang things. For those that don’t know the AGP bus slot had alternating fingers of contacts that were wide and narrow on alternating ends, wiki has a picture. The problem was when I went to seat the card the 1st time, some of the fingers smashed flat to the bottom of the socket rather then glide over the card edge. It looked like if I tired to bend them at all I would just break them off and have to toss my MB. So I took a soda can and cut a piece to shim in the slot. I gently pushed it in first and used it pry up the connectors that now would not stay in their proper spots. I then inserted the video card behind the shim. Took a pair of pliers and pulled the soda can shim out of the slot that was now between the contacts and the card now properly seated in the slot. I crossed my fingers and fired up the system. It worked for the life of the system. I never once tried to take that card out again.
Soda can shim, that is using your noggin!
It looks like someone forgot to take their meds today.
Looks a lot like the construction techniques we used for inertial navigation systems at Litton around the same time, except for that regulator heatsink. All of our stuff was conduction cooled by clamping the board edges to the housing and using thick copper planes, or even a sheet of aluminum in the center of the board.
Spent over a decade working on these things. The noise you are seeing is expected. The data lines effectively require the main bus to operate. There is a way to bench test the box, but you may need some more detailed schematics to build the rig. Otherwise, most of your article is on point. As for ruggedness, I think this particular box is one I have only seen broken by improper handling and never through electrical or mechanical failure.
Awesome information, thank you.
“Apache Data Entry Panel”
What data is being entered, and for what purpose?
(Guidance, ammo load, fuel specifications?)
As with most military electronics, the button/switch labels are kinda cryptic.
(let’s not get into the crypto means graph argument again!)
It’s an H6 Name as required for getting a National Stock Number. Unfortunately it’s a requirement, though some documentation might have a common name in parenthesis.
+1 for 1553 communications. It’s probably a RT, which means it will sit there waiting for a command from a BC before it sends anything. Think master/slave on a I2C bus. It’s not going to ack unless it’s addressed properly.
And if its addressed by the enemy, all they are getting is name,rank and serial number
B^)
Why thank you, my good sir!
I will now reevaluate my comment on the spelling error in the article so as to remove any vagueness and puns on my part.
Ahem:
“Dear Mr. Nardi and Bdjdjjxb,
It has come to my attention that in paragraph 14, line 3, the word complete is misspelled as compete. It’s an understandable error, one I have oft made myself. Thank you for such a complete and verbose teardown. Also, thank you Bdjdjjxb, for pointing out the unclarity in my original post.
Keep up the good work,
-Olsen
In the AH-64D (and AH-64E) there’s a KU (keyboard unit) next to the left knee of both the CPG (co-pilot gunner) and the pilot. It serves similar purposes (and more) as this panel did for the A-model.
Great write-up!
If the 1553 comments are right then I guess you must have been side-channeling a military system! Tut tut!
Milspec electronics are always so pretty.
I have been collecting these boxes for some time, too. It seems the main reason they are decommissioned is that the buttons wear out, given that most of them still have life in them when powered up. Absolutely cool stuff.
About the signals: most likely it’s a current loop, not voltage level signalling.
Yep, I also thought about that, it’s very common in industrial applications to avoid noise, so why not in military aircrafts.
Those keys look to be of a similar, more military grade version of the “Buckling Spring” mechanism with the cost reduced domed membrane from the IBM Model M keyboard
Have you tried making a differential measurement across both pins of the 1553 pair?
https://en.wikipedia.org/wiki/MIL-STD-1553
That unit sold historically between $4000 and $7000.
https://aerobasegroup.com/part-number/7219510034603_01-210-7710
BTW, it also says it is ITAR controlled. That might make life interesting if it is still true.
ITAR Controlled – Which translates into someone possibly knocking on your door and asking where you bought the device so they (the Government) can trace back to the organization that let it out in the wild. This just might end up as a bad day for someone! And BTW, if you do get a visit they won’t be leaving without your new toy!
ITAR Controlled just means don’t sell it overseas. You’ll find even mundane items of everyday use such as certain laser pointers are also ITAR Controlled. If it is still truly ITAR Controlled and the OP sells it overseas he could be in violation. The sad reality is that the entire newer AH-64D and E models are already available overseas. Even these Data Entry Keyboards, if any exist in government stock, are sold by the Security Assistance Management Directorate (probably CECOM) via the DoD and DoS to other nation states and organizations.
Those D sub miniature connectors are all over aircraft avionics, including those manufactured today.
There is huge inertia in aviation, once something has been shown to work safely and reliably it is very difficult to get it changed.
Connectors with machined contacts are a different beast to the rolled or stamped ones in consumer grade stuff
One year later….. IEEE 1553 bus. Midshift B32 will bring up SP1 read codes. I have worked on AH64 A’s, D’s, and now E’s for a combo of almost 20 years.
28 VDC
“The 5V supply looks like they could have just supplied the whole cockpit with it”. I was building control panel systems for my job and we tried this and ran into a common issue; field wiring causes resistive losses due to poor contact with pins/wiring and creates a voltage drop below 5V. Most devices which take 5V are super picky about the voltage they take so if it drops below 5V your devices start acting weird.
From experience, your much better off putting a voltage regulator/power supply in each component instead of using a single 5V supply ad hoping you don’t get too much dust/oil in your electrical connections.