You’d be hard-pressed to walk down nearly any aisle of a modern food store without coming across something made of plastic. From jars of peanut butter to bottles of soda, along with the trays that hold cookies firmly in place to prevent breakage or let a meal go directly from freezer to microwave, food is often in very close contact with a plastic that is specifically engineered for the job: polyethylene terephthalate, or PET.
For makers of non-food objects, PET and more importantly its derivative, PETG, also happen to have excellent properties that make them the superior choice for 3D-printing filament for some applications. Here’s a look at the chemistry of polyester resins, and how just one slight change can turn a synthetic fiber into a rather useful 3D-printing filament.
Not Just for Clothes
Like many plastics with practical applications, PETG is a copolymer. The homopolymer upon which it is built is PET, or polyethylene terephthalate. From the polyester family of polymers, PET was first patented in 1941 by a pair of British chemists, John Whinfield and James Dickson. Like many others, they were looking for synthetic fibers like nylon, which had made a big splash when introduced by DuPont a few years prior.
Whinfield and Dickson found that a condensation reaction between the organic acid terephthalic acid, a compound originally isolated from turpentine, and the diol ethylene glycol, which is the main component of automotive antifreeze. They found that the monomers would link together into long chains, producing a substance that could be drawn into fine fibers and made into yarn. Wartime secrecy laws kept their invention, dubbed Terylene, under wraps until 1946.
Today, PET is produced by other processes. The DMT method uses dimethyl terephthalic acid, which is just terephthalic acid with two methyl groups attached. When ethylene glycol is reacted with DMT at high temperatures and under basic conditions, a transesterification reaction occurs, linking the long chains of DMT together with a small fragment of the ethylene glycol. This reaction generates methanol, which needs to be removed for the polymerization reaction to continue.
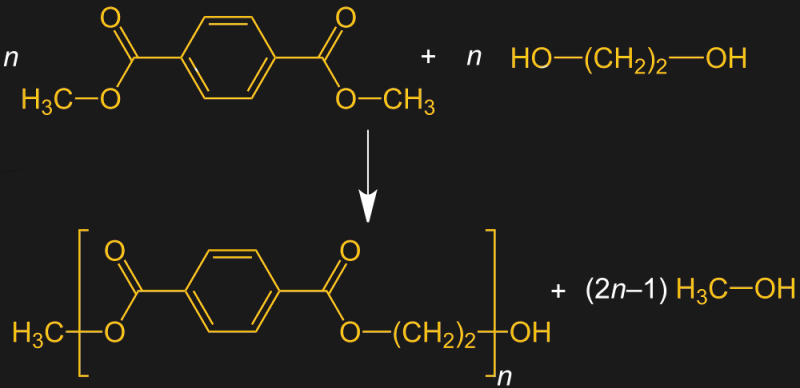
As versatile as PET is, it’s not without its weaknesses. While it’s very well suited for the manufacture of synthetic fibers, it doesn’t perform well in applications where other thermoplastics excel, like extrusion or injection molding. That’s where PETG comes in. The “G” stands for “glycol modified,” which is a somewhat confusing nomenclature. Many sources seem to think this means that glycol is added to the polymerization reaction, but as we’ve seen, ethylene glycol is already part of the polymerization reaction. Glycol modification refers to the fact that some of the ethylene glycol in the growing chain is replaced with another monomer, resulting in a copolymer with different properties than the homopolymer.
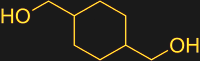
In the case of PETG, the comonomer is another diol, cyclohexane dimethanol (CHDM). This molecule is much larger than the compact ethylene glycol, but undergoes transesterification in much the same way as the smaller molecule. The effect of adding CHDM is that the distance between the terephthalic acid residues is increased, making it harder for neighboring polymer chains to nestle together. This results in a water-clear plastic with a lower melting temperature than PET that can be molded and extruded.
Best of Both Worlds
These properties make PETG and other PET copolymers extremely useful for commercial products. For the home gamer, PETG is a common choice for 3D-printing filament, and basically combines the best properties of ABS and PLA into a filament that easy to work with. It has greater strength and better flexibility than PLA, and its low shrinkage, great layer adhesion, and tenacious bed adhesion makes it less likely to warp or delaminate during printing. One nice feature compared to both PLA and ABS is that PETG doesn’t really smell like much while it’s printing. So if you’re sick of fumes that make your shop smell like an organic chemistry lab, PETG might be worth a try.
PETG also wins over PLA when it comes to environmental factors. PETG is resistant to many solvents, and stands up much better to wind, rain, and UV exposure than PLA, making it a great choice for outdoor applications. Unpigmented PETG is also translucent when printed, which can lend an aesthetic to prints that other filaments can’t. And PETG is considered a food-safe plastic, but you’ll want to take other factors into account before using it in contact with food.
PETG isn’t perfect, of course. It is more flexible than either ABS or PLA, which may be a problem for some applications. It also has a tendency to shatter suddenly when stressed beyond its limits, as opposed to yielding gradually. And as you might expect from a polymer that descended from textiles, PETG is subject to stringing while printing. That’s easily remedied with a blast from a heat gun, but it’s still something to keep in mind if you’re looking for form over function.
If you haven’t given PETG a try in a 3D printer, you should.
I’ve also had reasonable success cutting PETG sheets with a cheap CO2 laser cutter, while not as nice as acrylic cuts the material is tougher.
How thick sheets have you tried? I want to try 2-4mm sheets, but have not gotten around to it yet. Hate acrylic as a construction material, soo brittle.
The Faraday effect is when a substance in an electric field rotates the polarization of a light beam passing through.
If memory serves, PET is probably the only common material that’s available and inexpensive for the experimenter with a high value of the Verdet constant, which is the fundamental constant for the Faraday effect.
(One application: measuring extremely high electric fields from a distance, by passing a polarized beam of light through a block of plastic near the field, and back.)
I’ve often thought that the effect could be used for something… but what? (Home-built) high speed optical switch, perhaps?
“The Faraday effect is when a substance in an electric field rotates the polarization of a light beam passing through.”
Magnetic field.
cf Kerr effect and Pockels effect but these aren’t a rotation.
Still potentially cool and not something I knew.
Whenever I read one of these chemistry articles:
http://giant.gfycat.com/UnitedImpureAlaskajingle.gif
You and me both, pal.
I’ve heard of issues with a fine dust forming on surfaces near where PETG is being printed, that has made me avoid using it until I can create an enclosure and better ventilate my printer.
are these clams false?
I’ve run at least 20kG of PETG through my printer in the last year or so, there’s no more dust next to the printer than there is in the rest of the house.
I can’t see there being any dust as it’s generally more gloopy / stringy
so if anything you might get some very thin strings when pulling it off the nozzel
I encountered the same, not sure what it is. It is easy to wipe off though.
What’s the best way to recycle it?
You know, besides putting it in a bin with three arrows on it.
I want to know the answer to that one too.
Man, I bought a spool of PETG filament about 2 months ago, and I could not get ONE decent print out of it. No matter what I tried I ended up with it gooped up on the nozzle instead of stuck to the bed. Tried a million different temps, INCREDIBLY slow speeds, overextruding, underextruding, a zillion different first layer z offsets, nothing worked. Even if I got it to start printing ok, as soon as the printer hit it’s first travel leg, it’d blob up and fail to stick. I’m back to PLA, maybe some day I’ll get masochistic enough to try again :|
Tried sugar?
https://hackaday.com/2019/01/05/sugar-as-a-bed-adhesive-for-3d-printing/#comments
I swear by PETG, love it. I guess your stuff mightve gone bad, or was cheap crap.
true though that it has different bed adhesion properties, bed temps > 50c, I use kapton tape.
Beggars belief when ppl still print in ABS, which is designed to shrink out of injection mold machines, curling is inevitable.
Ive seen shattering of PETG prints, but I feel its not supposed to do it, try and shatter a water bottle. I always assumed you can temper PETG prints to release internal stresses, I think its a great property to bend instead of shattering.
great stuff but expensive.
Oh and I can happily print at 60 mm/s, blobbing does occur but is minimal, prob to do with slight filament width variances. Stringing, not so much. Heated bed on high temp is essential. As is the extruder temp window must be within 10c of ideal.
Make sure to use no or very little fan, this is because it’s very stringy even without a fan
higher nozzel temps for 3DFilaprint transparent red I use around 230
for the bed I use around 75 (on pei)
It sticks much more to the bed than pla, I’ve started using an initial layer height of around 0.3 to avoid damaging the bed
ideally you want one of those silicone nozzle socks, as during a long print you can get a bit of gloop build up which suddenly comes off in the middle of the print if your not careful
This is about my recipe as well, but instead of a higher first layer, I lower the bed temp.
225 C on the nozzle, no fan at all, with PEI at 55 C on the bed. It still sticks too hard, but it’s better than it was at higher temps. I almost suspect that one could run it unheated if everything were well tuned-in. (Never bothered.)
This all said: PETG is not PETG. The formula seems very sensitive. I printed in red and blue, which behaved about the same. Then I tried green and yellow from the same manufacture (Devil Design, in Poland, probably only makes sense if you’re in the EU) and they were significantly brittler, needed different print temps, etc. To the point that I just don’t print in those colors.
I’m used to some variability in PLA between good/bad manufacturers and across colors, but this was extreme. Is it just the nature of PETG?
I’ll try printing on kapton, I’ve been printing on blue tape. My filament was amazon-sourced Hatchbox, so I wouldn’t expect it to be junk right out of the box.
As for the shattering thing, how about stress relief? I’m brand new to 3d printing, but I’ve been working in industrial thermoforming for a few years now. We run virgin and recycled PET (and some PETG) from .012-.040″ all day every day. . .
Anything ~.028 or thicker has a tendency to crack and shatter if a cut isn’t perfect, and if it’s been sitting out in the cold long enough to drop to zero or below it almost always will regardless.
Now, in injection molding and thermoforming, you’ve got at least some period of time where your resin/sheet is being heated gradually, formed, cooled to the highest temperature possible to hold its form, then cooled ambiently as it works its way down the line. Essentially passive annealing as a byproduct of the process.
Flip to 3d printing – your filament is room temperature until it gets to the hotend, is for all intents and purposes instantaneously heated to molten, extruded immediately, and instantaneously cooled. Your heated bed may be helping with the gradual cooling, but considering how fast the previous two stages occurred, how much does it actually contribute?
“For the home gamer, PETG is a common choice for 3D-printing filament”
wait, gamer?
yeah, you know, for those of us playing along at home.
PETG will suck up moisture from the air and then it doesn’t print as well. Not only does the moisture cause print problems, it reacts with the plastic at high temps to make it more brittle. All that said, PETG is one of my go-to filaments. Dunno why people feel compelled to say “Material X is better than Y.” I pick from several different materials, depending what I want from a particular print. It’s like maple syrup vs. salsa – they’re both good, but definitely different.
So, enquiring minds want to know: can you do something to recycled PET bottles to make them into PETG?
If you figure that out a way to economically chemically cleave PET, the world will beat a path to your door. Let alone start inserting your own new chemicals and rejoining the chains.
What temperature can finished prints stand up to? Will they survive a dishwasher at 80 °C?
Not likely. Try ASA instead.
I know this is old, but I just saw that companies selling PETG specifically for food safe applications indicate it should be safe in the typical dishwasher. Looking up dishwasher temperatures they are typically 65-70 C, which is below the 80 C threshold they are likely going to soften at.
Do your own tests/research, but those are promising numbers.
I just bought a 3D printer and have just printed off a Benchy successfully with PETG, I’m very happy with the results, although they are imperfect.
I have been 3D printing with PETG for a year now … it’s a nice strong material but can be a temperamental pain sometimes, not ABS temperamental but it’s no PLA
A lot of great and accurate information in this article. The author clearly works in the industry or studied sources very well. A few points of clarification or reinforcement from the article. PETG is a class of product that has somewhere between 0 and 50% CHDM. Beyond 50%, CHDM being the dominant glycol, the nomenclature becomes PCTG, and PCT at 100% CHDM. Note, the degree of substitution will vary the properties.
So some of the varied results for 3D printing could be due to different degrees of glycol modification/substitution.
There is also acid modification where TPA can be substituted with IPA (a branched version of the linear TPA).
Lastly, copolymers is a superset of just these CHDM and IPA substitutions where all sorts of varying glycols and acids are introduced in pursuit of various properties.
I don’t have a 3D printer, so I don’t know what is all available, but mostly wanted to highlight that any offerings that simply call it PETG or copolyester/copolymer don’t necessarily mean it is a specific “thing” and performance may not be consistent across various suppliers.