I’ve noticed, lately, that slotted screw heads are all but gone on new equipment. The only thing that I find remarkable about that is that it took so long. While it is true that slotted heads have been around for ages, better systems are both common and have been around for at least a century.
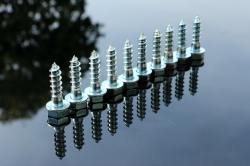
The reason slotted heads — technically known as the drive — are so common is probably because they are very easy to make. A hacksaw is sufficient for the job and there are other ways to get there, too. The only advantages I know of for the user is that you can easily clean a slotted drive and — possibly — use field expedient items like butter knives and quarters to turn the screw. I’ve heard people claim that it also is a feature that the screwdriver can pry things like paint can lids, but that’s a feature of the tool, not the screw drive.
The disadvantages, though, are significant. It is very hard to apply lots of torque to a slotted screw drive without camming it out or snapping the head off the screw. The screwdriver isn’t self-centering either, so applying force off-axis is common and contributes to the problem.
A Bit of History
Threaded wood for things like olive presses started showing up about 2,000 years ago or so. By the 15th century, metal screws appeared, but being hand-made they were not very regular and were only popular in limited applications. Job and William Wyatt patented a screw machine in 1760, but it would be ten more years before a workable model would appear.
In 1770, Englishman Jesse Ramsden invented the first workable screw-cutting lathe which he used to create micrometers and other scientific instruments. He was also a mathematician and you may know him from his contributions to optics. Around 1800, Henry Maudslay invented a large screw-cutting lathe and American machinist David Wilkinson created a similar lathe. The lathe allowed for the production of interchangeable parts which were key to the industrial revolution where people like Eli Whitney were able to move to mass production of items like guns which had previously been one-of-a-kind.
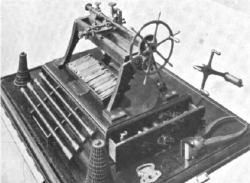
Prior to Maudslay’s inventions, lathes were generally operated with a foot treadle and the operator simply held the tool to the work piece. This was not accurate enough to cut threads, so screws were made by the freehand use of chisels and files. Maudslay’s lathe had changeable gears that allowed for different pitch threads. Wilkerson’s was a larger machine, but was not easily configurable. Even so, the government used around 200 lathes like Wilkerson’s and awarded him $10,000 for the invention — That would be about a quarter of a million dollars today.
All of this time, the heads were nearly always a simple slot. In 1744, you could get a flat blade that fit a carpenter’s brace sort of like today’s drills will take a drive bit. By 1800, though, handheld screwdrivers were common.
Cutting threads with a lathe is only one way to form threads. While it is precise, it is also expensive and weakens the metal. Cold rolling is economical and doesn’t remove any metal, but the first attempts by William Keane in 1836 failed because cast iron dies were not up to the task. In 1867 Harvey J. Harwood also attempted cold rolling, but practical thread formation using this method had to wait for Hayward Harvey and Charles Rogers in the early 1880s. Some special bolts are still cut, though, and the video below shows a modern operation, and the second video shows the more usual modern process.
Modern Problems
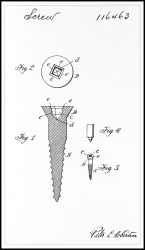
Ironically, while assembly lines became possible because of standard screw threads, they also were responsible for dissatisfaction with the slotted drive. Inventors wanted to do better. In 1908, Canadian Peter Robertson invented a square-head screw drive where the driver and the hole had a slight taper. There had been other attempts at producing similar drives, but they were all difficult to manufacture and did not catch on. Robertson’s invention was conducive to inexpensive manufacturing using a die.
This has several advantages. First, the drive is self-centering. Second, the driver won’t slip out even at high levels of torque. The Canadian Model T Ford used over 700 Roberson screws.
Ford and Phillips
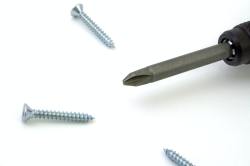
Ford found that the Robertson drive saved a few bucks on the production cost of each car, but was wary of having a single supplier. Robertson, however, had a bad experience licensing in England and was reticent to enter into another license deal.
In the 1930s, Henry Philips building on work by John Thompson, had introduced the Phillips drive for screws. This also self-centered and was more amenable to automated methods compared to a slotted drive. Too much torque could cam out the head, though, as you’ve probably experienced. The company claimed this as a feature to prevent over tightening. GM wound up using the Phillips drive in the 1936 Cadillac, and its popularity was assured.
Robertson drive screws account for almost all screws sold in Canada and are virtually unused everywhere else. Even though most people consider the Robertson drive superior, a business decision made it a small player.
Even More
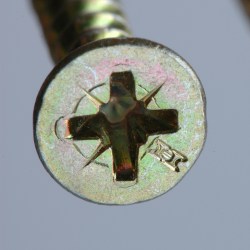
There are a staggering number of drive types out there, many of which don’t have the problems the Phillips head has. William Allen’s hex drive is used in many applications. Pozidriv is uncommon outside of Japan. Yet the slotted drive survives and Phillips remains nearly ubiquitous in much of the world.
It makes us wonder. The old saying is that if you build a better mousetrap, the world will beat a path to your door. But that doesn’t seem to be true. It is more like if you build a better mousetrap, market it successfully, build a great distribution network, and defend your intellectual property… well, you get the idea.
I focused on the driver technology, but the screw threads themselves are a fascinating design that our own Dan Maloney dove into a few years back. If you want to know more about other types of bolts and their appeal, the amusing video below has a lot of good information. It still doesn’t answer the question of why we don’t see more use of “better” drives. What do you think?
If you want to try your own bolts, maybe you need a mini lathe. Or maybe you just want some advice on getting the perfect set of screwdrivers.
thanks for calling them slotted heads instead of flat heads. for everyone who constantly gets this wrong, slotted describes the driver shape. flat describes the shape of the screw’s head.
The term “Flat Head” refers to the designer who insists on using slot head screws in their designs.
Never heard flat head to mean anything but single slot here in the uk
As “flat head” for geometry doesn’t really mean anything is a countersunk screw flat?or do you mean a pan head?
If you’re ever put a Robertson through a 2by4 there is no going back. Taper holds screw on bit, no slipping you embed it as deep as you want.
.
The only thing Philips are good for is drywall where you want it to slip once flush.
Just refer to slotted heads as “minus”, and Phillips heads as “plus”.
“Positive” and “Negative” 😉
Quite the opposite. All the wood screws we’ve got here in Poland are Pozidriv (except some hex and torx) and Phillips can rarely be seen.
True for Germany too.
PZ screws were/are THE screws for wood but are being replaced with torx.
Here in the Netherlands too, and they are labelled needinng a “PZ-2″bit (often included) so I think that’s pozidriv, not JIS
PZs are terribly common in Europe, but also in the US — they’re in every piece of IKEA furniture.
If you’re wondering why you’re stripping them with your Philips screwdriver, you’re doing it wrong. :)
I have drivers for both, but when given the choice walking down the fasteners aisle, it’s PZ 100% of the time. They lock in _much_ better.
that’s an interesting observation Elliott. Pozi drive is relatively common in Aus and my experience with it is nearly always bad. Yes I do have the correct drivers but never have the same level of positive fit as i find possible with Philips drives
Maybe my tools are at fault … or then there’s always the tool hanging on to the handle
That is weird. In Europe IKEA uses only hex heads.
I suspect most people in the US just use a phillips screwdriver on their IKEA furniture without even noticing or knowing the difference. With the predrilled holes and soft chipboard you could probably get away with a rusty butter knife.
Regarding the disagreement in other comments: IKEA uses both hex and pozidriv screws in Europe and the US. The hex head screws are usually used for structural assembly and pozidriv screws are usually used for wall mounting and for smaller fasteners (like cabinet doors), but not always. Look up the assembly instructions online for KALLAX in both Sweden and the US, for example – same instructions and it uses both.
I thought Ikea included a cheap screwdriver with its kits?
When I got a chair two years ago, I didn’t need extra tools. I think the same with a dresser.
It makes sense, especially if the fasteners are not common types. Customers won’t be tempted to use what they have, and not forced to go out a second time toget the matching driver.
Which i like, torx is such a nice system, i have yet to totally ruin a torx head as long as i use the right bit.
I’ve yet to ruin a torx even when using a wrong and high torque (size smaller, lost the correct size and had to finish)
Try that with any other type
I have ruined two small torx screwdrivers trying to loosen stuck screws.
Well, I ruined two torx heads a few days ago, totally. Then I noticed that I could bend the screws with my bare hands. I guess they were made of the cheapest steel possible.
Whenever I have the choice, I buy torx screws, so I have quite some experience with torx drives, and never any issues apart from the one mentioned above. I hate phillips and pozidriv (lol, they sell the torque limit of these designs as a feature!); ruined quite a few of these. Slotted heads are not just inconvenient – I have managed to tear slotted heads apart quite a few times with manual screwdrivers. Allen drives work well at larger sizes, but often fail when the heads are very small. The same for hex heads.
So torx is still the weapon of choice for me. There might be better drives, but torx screws are readily available nowadays.
Data point: The MEs at work seem to like Torx drive for all the machine screws they use on products we develop. Jeep/FCA seem to like them as well.
When I built a shed ramp for my daughter I used some Torx drive deck screws and they seemed to work fine. The bit doesn’t cam out like with Philips, but the tradeoff is that you need a [correctly set] torque clutch on your driver.
I love Torx in clean environment applications. I loathe them in dirty applications.
If any of those gets painted over, plaster or glue inside, or any other type of gunk or slight corrosion they’re an extra pain to clean to get the tool to fit in.
You can wiggle a Phillips in or Robertson clean very easily and/or get away with using a slightly undersized/oversized tool to get the screw out.
But especially when working with cars, Torx either come out perfect and you have a fantastic day or insta-strip into a perfectly round socket and your easy 30mins in the driveway $40 brake pad job just turned into up to 2 hours of close-quarter surgery on a brake calliper between an expensive ABS sensor and a flexible brake line.
There’s no in-between with Torx :D
The author should have written JIS.
Actually, it is probably the JIS drives I’m thinking of which are very similar to Pozidriv except for markings and the exact angle of the blades, but — I think — they are actually cross-compatible.
Anyone with vintage Japanese motorcycle experience will reassure you that pozidrive drivers are not compatible with JIS soft French cheese fasteners.
Yep. I have three types of “phillips” drivers in my toolbox: a set of JIS, a set of pozi, and a set of phillips.
They all work on loose and semi-tight screws, but if you have a screw with a damaged head, or one that is tight, using the right driver is a game changer with the end result being getting the screw out, or having to use a left-hand drill and ezy-out.
Had to get specific JIS drivers for meddling with Japanese built camera lenses. Philips and Pozidriv didn’t get on with them.
Slotted would have been way easier to deal with rather than a whole bunch of slightly different angled holes.
On the larger scale, while Pozidriv is prevalent here in the UK, good and compatible driver bits are a bit hit and miss. Presently liking De Walt ones. In essence, if you can put the screw on the bit and it stays there fairly firmly in a horizontal position, without it being magnetic, it’s good to go. If it falls on the floor, find a new bit. Even if it says it’s the right bit or the right screw.
The other most important thing is not to employ the second to last “joiner” who worked on my house. Took ages to get all the knackered screws out of door hinges to refit them with a better joiner. Slightly a function of the first screws not being very good, but there screws can’t take all the blame.
Not quite, it’s Philips and JIS which are (visually) almost identical being just a cross, Pozidriv have the extra cross at 45deg. JIS drivers work much better in Philips screws than visa versa. Also Pozi has pretty much replaced Philips almost everywhere at least outside the US
In Phillips the faces of the slots are tapered, which is why the drivers cam out. PZ screws have parallel faces; the extra cross is at such a small radius it is unlikely to offer any better torque resistance but it does offer better patent resistance and ensures that any drivers intended for PZ recesses cannot fit any recesses that do not have the patented feature, locking out competition.
The extra bit in the middle is not for patent purposes, or for drive, but is a consequence of the machining operation that makes the drive cross flat-sided.
After years of mangling the screwheads on shimano bicycle components I learned they use JIS instead of phillips…
A phillips screwdriver will turn JIS screws, but they won’t last long!
The trick is that the most common jap head is #2 philips – even on much smaller screws that look like they should be #1 – exactly like the shimano screws. Make sure to always try #2 first.
It is handy to have a narrow shaft #2 for screws down holes – I’ve had to grind a few #2 screwdrivers thinner over the years
Now the idiots at Lezyne who make my otherwise excellent multi-tool put #1 on it – there is no a single #1 head on my bike
Same here in Finland. Practically all new wood/construction screws are pozidriv (if they are not torx). Only lag screws are with hex head.
Same in the UK – PZ screws are very common here. Philips are sold but are far less popular
…and all drywall screws have PH drive, just to add confusion
Pozidrive are very common in UK as they are an invention of the British company GKN [a major engineering conglomerate] to address the shortcomings of the Phillips drive. My experience is that most damage is done by using the incorrect driver or badly worn drivers. You need to change drivers or bits as soon as they show wear. ESPECIALLY if using a power driver.
GKN have been trading for 262 years, and are one of the oldest companies in the world.
“GKN Ltd is a British multinational automotive and aerospace components business headquartered in Redditch, Worcestershire. It is a long-running business known for many decades as Guest, Keen and Nettlefolds. It can trace its origins back to 1759 and the birth of the Industrial Revolution.” [Wikipedia]
HP used PZ in Test Equipment (1980s?)
FWIW, Robertson (square) drive screws are readily available in the US, but they’re not typically stocked in the big box stores like Lowes or Home Depot. I get mine from Dunn Lumber in the Seattle area, and greatly prefer them to either Philips drive, or the abominable star-drive monstrosities the box stores seem to be foisting on the unwitting public. The screws I usually get are dual-drive, which will work with either a square bit or a Philips bit.
I remember the square drive screw being ubiquitous in mobile homes in the 80s, as far as I know they are still. Interior, though; the aluminum exteriors were hex head self tapping screws with sealant or a washer.
RV’s as well. And very annoying when trying to fix/remodel an old RV because any tiny bit of dirt in the hole seems to make the bit cam out. I finally learned to use two bits at a time, one in an extension to pound in each head with a hammer and another in the drill to remove the screw. Take the first and a hammer and pound it into every screw head to compress whatever has collected inside them over the years before trying to unscrew them. It was the only way to get most of them out.
Wonder if an old spring-loaded solder sucker would work?
I find a blast from a compressed air gun and a bit of poking with a pointy thing works best – wear eye protection though!
Star drives much like anything work best when using the correct size. Much better that the Phillips.
And taper of the philips screwdriver makes it the perfect one size fits all tool for those pesky star shaped heads. Much better than needing to have multiple tools around.
I prefer torx or hex to Philips because it’s tricky to tell what size driver to use and whether the blades are angled to mate properly. It’s possibly pozidriv vs Philips or something. 90% of the time it’s fine and 10% you strip the drive completely. Torx and hex are easier, it fits or it doesn’t and cheap drivers strip before damaging the screw.
Good quality bits help too – I was surprised how much better a Wera pozi bit works than random cheap ones; doesn’t cam out, grips much better, fits snugly, can hold the screw while lining it up, and so far has lasted for years with almost no wear.
Did Apple buy their Torx screws from a big box store when they put them in the 1984 Macintosh? It was almost impossible to find the long shaft Torx driver that you needed to open an original Mac.
The Huge advantage of Torx screws is that you can dip a magnetized driver into a pile of Torx screws and one will stick in place ready to go.
My solution to Mac opening was to take an ordinary length torx screwdriver, chuck it in the drill, and grind down the lower end of the handle enough that it could fit into the Mac.
I expected to have to buy a whole screwdriver, but I came upon a bit, kind of longish. I took some tubing, maybe brass, that was around, and cut slots to that fit the bit, and it worked fine. I still have it somewhere sround.
This may be because Seattle is close enough to the Canadian border. A few years ago I entered a boat-building contest north of Vancouver, and knowing I’d be using Robertson, ended up having to mail-order drivers because none of the midwest/rockies stores I visited had any.
I find that Robertson bits tend to wear out quickly, almost as quickly as Phillips bits. Torx and PoziDriv are theoretically the best for delivering the most torque, although small Torx bits can actually be snapped off by applying too much torque.
not sure i agree. i haven’t used a robertson drive, but you can tell right off that it has the problem of sizing. a small screw has to have a small drive by necessity, and a bigger screw wants a bigger drive for greater strength (or it will cam out too), so you have to have a bunch of different robertson drivers handy.
i have this problem with allen wrenches already…i’ve got a big set of english and of metric, and of course i have backup sets purchased when i couldn’t find the original sets. and they’re surprisingly eager to cam out, especially if you use the wrong size. whomst amongus has never used a 3mm on a 1/8″? and once you’ve cammed out the wrench itself, good golly you might as well throw out the whole set. but you won’t, you own’t even throw out that wrench because having a cammed out wrench of some odd size is so much better than not having it at all. the cycle continues. it’s awful.
philips is great because it’s the best self-centering, and you can compensate for its tendency to cam out by Just Pushing Harder. unless you are aiming for maximum torque, i usually have good luck one-size-fits-all for philips, though i can lay my hands on 4 different sized drivers. and they’re so ubiquitous, it doesn’t seem foolish of me to own 4 of the same philips screwdriver the way it does to own 4 complete sets of allen wrenches.
compared to philips, i find that slotted drive is pretty good about not camming out, especially if you use the right size. and again, i really only own 4 sizes of slotted drivers and that seems to be sufficient. but that lack of self-centering is brutal. the big consolation prize for slotted drive is if the head isn’t actually recessed then you can turn any torx or security bolt or whatever screw into a slotted drive with common tools!
overall my favorite is philips drive within a hex head. 99% of the time it’s more convenient to use the philips, but if you strip it, or if you need more torque, or so on, the hex head is always there to save the day.
“i have this problem with allen wrenches”…”and they’re surprisingly eager to cam out, especially if you use the wrong size.”
I think you are treating cam-out and stripping as the same thing. Cam-out is where the tool is rejected when torque is applied, and this may, or may not, damage the tool or the screw drive. Stripping is where the tool damages the drive in the screw so as to make it difficult or impossible to turn the screw using normal means.
Allens tend to strip when the tool isn’t fully engaged or the wrong size tool is used, but rarely cam out.
that’s a good point, or an interesting distinction anyways. though i have yet to see a cam out event that didn’t damage the screw or drive. :)
but i’ve had both with allen. not sure why. i’ll cop to operator error but that doesn’t fix the problem.
I find it hard to imagine how you have cam out with allen, which has parallel sides so there is no outwards force generated when you apply torque.
I’ve stripped many an allen key, usually super cheap non-CrV ones, but I don’t think I’ve ever had one pop out of a screw head the way a Phillips/PZ bit does
You need to closely inspect your allen wrenches. I’ve only seen an Allen wrench cam out when the tool was worn or the fastener head was damaged by the previous user.
“philips is great because it’s the best self-centering, and you can compensate for its tendency to cam out by Just Pushing Harder.”
And that’s how screws get stripped out, especially if some chucklehead is improperly using the ‘ugga dugga’ machine to drive the screws. (aka an impact driver, or a drill with the clutch locked out or turned too far up.)
I have… a *lot* of bits for just about everything, normal heads, traditional security screws, and the goofy ones like the dreaded Pentalobe screws Apple is so very fond of.
Robertson square hole would also takes up a lot of space in the screw head for really tiny screws.
Torx solves the Cam-out issue with Allen.
If I have to deal with removing screws that I don’t have a bit for or a Cam-out one, I usually dremel a slot head with a cutting wheel. :P
Exactly, once a pozi or torx screw drive hole is worn or corroded, you can only get it out by cutting a slot and then maybe using an impact driver with a flat bit to get it moving.
I agree with what you say about slotted not stripping as easily as philips under the right circumstances. If you have the correct size driver and perfect alignment, slotted will actually take quite a bit of torque.
I would, in fact, argue that a slotted screw, with the correct driver, will take more torque than others as the torque is applied at the largest possible radius from the screw centre.
This is, to an extent, compensated for in a cross-head by having more working flanks (4 rather than 2)
If you play around with old machinery (> 100 yo) you find some very large slotted screws. The carriage angle of one of my lathes is held on by 4 x slotted screws with a 9/16″ (14.2mm) head.
The nice thing about Allen wrenches is that if you wreck one by rounding off the tool, you can just grind it a few mm shorter and you instantly have a new tool. Of course, if the tool were made of decent steel you wouldn’t have rounded it off in the first place. The ones they sell at Harbor Freight or come with cheap furniture are trash. Buy quality tools and you won’t have problems. The Bondhus hex and torx drivers are pretty good, especially for the price.
yeah! if i didn’t have to buy 20 of them at a time, i would definitely have higher quality allen wrenches. :)
Fwiw, both Bondhus and Wera sell individual Allen keys.
Note that if an allen wrench is rounded off, you can just grind off the rounded off tip, and the part above will be pristine and still the correct size. Of course, you can only do this so many times until the tool is too short to use.
And now I see that my comment is quite redundant. So it goes…
Not to worry. I’ll just gring off the tip of your comment, then it’ll be as good as new.
Just Pushing Harder works fairly well for driving a screw into material, but when trying to remove a screw pushing opposes the direction I want the screw to move. Too many times I’ve had to resort to Vice Grips to remove a Phillips head screw, or if the screw is recessed drill off the head.
Sometimes you can use a Dremel tool to transform the Phillips into an oldfashion slotted head.
Someone mentioned that.
It fails if the screw is recessed
I’ve opened a lot of hard drives for the magnets by using this scheme.
But I think I have a good selection of bits now.
One correction, you say Pozidrive is uncommon outside Japan. In UK virtually all “cross head” wood screws are Pozidrive while machine screws are almost always Philips.i wish we would standardise to one type!
And worse, even thought Phillips head drivers (sorta) fit, they really don’t, and one ends up trashing the screw, the driver, or both. :(
Still used in drywall screws.
And this is because If you use a machine made for driving drywall screws it may depend on cam out to release the screw.
I’ve used two kinds: a Makita that cams out and a more advanced Hilti with a spring-loaded clutch.
Even though both use bits and could drive any type of screw, the Makita probably wouldn’t release anything other than Philips.
And common in British cars too. I got a set of PZ when I got my old Jaguar. They work very nicely.
British screw fasteners are a unique breed all to themselves. :-)
Had a Raleigh 3-speed in the 60s. Nothing available at the store would fit the fasteners. Not good when a nut fell off and your fender was flapping. Remember the huge stamped flat “wrench” they gave you that was so big it wouldn’t fit anywhere (even if the hex hole was the correct size)?
British Bicycles used a completely standard thread. But that stamdard was British Standard Cycle.
https://en.wikipedia.org/wiki/British_Standard_Cycle
Philips screw heads and screwdriver are called – word by word literal translation – “crucifix” head screws(bolts)/screwdrivers in Eastern Europe. That is why vampires refuse to grab them.
I recently inherited a big box of assorted screws from my Grandfather, accumulated over his life and the first thing I did was throw all the slotted ones away. There were some gigantic lag bolts that were slotted and I found myself wondering how big the clearance hole would need to be to make sure that you could drive them all the way home without a flat head screw driver slipping out.
“It is very hard to apply lots of torque to a slotted screw drive without camming it out…” a large number of gunsmiths would beg to differ. The problem is that most people own slotted screwdrivers that are tapered, which most assuredly does want to cam out and/or strip the slot when any decent amount of torque is applied. Gunsmiths, however, use hollow-ground screwdrivers for slotted heads that ensure a proper parallel engagement with the slot. Hollow-ground combined with the correctly sized driver (if you use an undersized driver you’re just applying torque to two points rather than the entire surface area of the slot) makes it nearly impossible to cam out.
I second that, it all depends on the screw driver, I wish I could get old school machine screws, all new stuff have smaller heads so do not look right on vintage machinery.
Here here! I would bet 90% of the issues with screws are directly related to an improper driver selection by the user or improper driver fit due to cheap screws.
(I do not exclude myself from that statement which is why I have several brands of #2 bits in my tools; a #1 bit from Wiha and Wera will fit screws differently, although both excellent manufacturers in my opinion)
the HUGE advantage of robertson drive screws that almost always goes unmentioned is that due to the taper they are dead simple to start – they don’t fall out of the screwdriver if you hold them upside down with a non-magnetized head. They are colour coded for size, they rarely cam-out or strip (unlike phillips).
Better tell Leo over at Sampson Boat Company that he’s using the wrong fastener type. I think (large) slotted screws are pretty common in boat building and I don’t see them changing anytime soon. Hey it’s worked for a few hundred years, why change now? https://youtu.be/9HEmOAxjBFI?t=345
I think he also mentioned in one of the videos that the choice to go for slotted fasteners was both to keep in with tradition and because slotted fasteners are easier to clean when covered with old fairing compound
You also need to think about the kind of screw. Taper wood screws only have a few turns (vs metal and self tappers). The also disengage to low torque with a turn or less.
These make a slot head much less of a disadvantage on tapered wood screws, than with all the other other kinds of screw
Recommended, for your reading pleasure: “One Good Turn: A Natural History of the Screwdriver and the Screw ” (Witold Rybczynski)
Available at your favorite local bookseller, or soulless global internet sales channel, as you wish.
I read it out of the library. It probably tells you more than you need, but it’s short. I think it started as an article in The Atlantic.
Recently replaced some circuit breakers at home. Guess what? The wires clamp via screws with a square drive. So I’d say Robertson drive is common in the electrical industry in the US.
the terminal screws on most outlets are triple-cut: Slot, Phillips2, Roberts 3mm
And curiously, UK terminals are always slot-cut, never phillips/pozi. I recon it’s part of a standard somewhere.
True for the older ones, I notice the newer ones will accept a Philips driver as well. Which is nice. Same for duplex outlets (but I despise the new “safety shutters”) and switches.
im quite fond of torx. i live in alaska and a lot of builders complain that they can only get torx screws. being close to canada i guess its just cheaper to import hardware from there than to get it from the lower 48. yet somehow they cost more than phillips at the hardware store. its more an availability thing where you need x, now, and they only got y. but as the guy who actually has to turn those screws, and with a 30 year old drill at that, i appreciate not having my drive (or worse, my bit) strip out every 10th screw like what would happen with phillips heads.
I won’t use anything but Robertson for decks, and any future right-to-repair legislation needs to force manufacturers to lay off of security screws in an attempt to force obsolescence. It’s like you spend gut-wrenching amounts of money on an ac blower motor and it’s held in place by rubber grommets and hairpins, and a some cheap toy requires a bit that’s more expensive than the target.
There are 6 sixes of Robertson screw heads, the middle two sizes account for the overwhelming majority of screws and most people will never encounter either the smallest or largest sizes.
I absolutely love Torx. VW has been using them in cars exclusively for at least two decades AFAIK and they are in electronics like printers, older phones (which are not glued together yet) and even the most shitty screwdriver sets have torx bits here in EU.
But, but…. I’m having extremely big problem finding metric screws with torx head in hobbyshops in both Czech and Slovak republic. Torx wood screws no problem. But torx metric screws? Absolutely nonexistent. I’m hoarding every torx M3 and M2.5 screw from old laptops and apliances because otherwise I can get them only in pricy specialized shops despite the fact that they are used everywhere around here.
Interesting point made in an other comment; slot heads are easier to clean, so, in applications that will get filled with rust, paint, gunk, etc and still need to be used, the slot is probably the best choice.
I’d hate to clean layers of rust and paint from lots of torx heads (like might happen if used on a boat Hull or something).
I’ve done this recently while renovating a house. Painted-over phillips screws received two light hammerings (90deg rotation) with a small slot screwdriver to dislodge the paint, then came out nicely with a phillips driver.
The torx screws in a partially-rotted deck was more of an issue. My eventual solution was turning a 2mm drill bit by hand to dislodge debris, tap a torx driver in with a hammer, wiggle clockwise slightly, then turn anticlockwise by hand, hoping that the head didn’t shear off the rusted shaft. I got up to ~50% success rate by the end of the job.
Pozidriv was also used in HP test equipment in the 70s and 80s when they switched over to torx. Much easier to work on with PZ drivers.
Someone mentioned deck building: here in the US, wood or composite-wood deck boards are almost exlusively fastened with the square heads. One of the first time I’ve encountered them, but in every big box lumber store here, look at the decking screws- they’re all square hole heads (Roberson’s, I suppose).
I hate those tamper proof Torx screws, the ones which have a pin projecting from the slot.
IBM used to use those security Torx in early PCs, especially in the power supplies. I looked everywhere for a Torx driver that fit them, with no luck. I tried drilling a hole in the tip of a purchased tool, but I lacked the skills and tools to accurately bore into the hardened steel.
I eventually realized that the pins were just tack-welded into the screw heads, and with a pair of thin tipped needle-nosed pliers, I could easily break the pins out. After that, I could drive them with a regular bit, and I never worried about those stupid screws again.
My approach is a drift pin and a hammer!
The tamper proof Torx also have the advantage that they require a “special tool” to remove, which confers some regulatory advantages related to customer [non]accessibility, meaning insulation and safety requirements for the stuff inside are more lenient (and therefore, cheaper to build)
Apparently they’re not always used to keep people out, I learned recently that they’re also easier for automated manufacturing because they grip the bit better. I tend to use my security Torx bit set for all Torx screws in my house, and just use the regular ones for outdoor or other larger scale construction projects.
I wouldn’t have thought slotted screws were used anywhere since the 70’s.. I haven’t seen them on anything since then, and certainly have never bought them..
Compaq used Torx screws everywhere on their PCs in the 90’s, sometimes with a slot cut across. Meanwhile IBM continues to almost exclusively use slotted screws, most often cut across a hex head. And they loved to get all the screws torqued down to what must have been just below the yield strength of the screw or the metal they were screwed into. A set of very good nut drivers and sockets, plus extensions and a good 1/4″ ratchet were in the PC tech’s toolkit if they worked on IBM PCs.
What would make a Bad Day was when someone brought in an Aptiva that someone had tried to use a flat screwdriver or a worn out 1/4″ socket on. Same for when I had to work on a Compaq that had been mauled with a flat screwdriver or a hex key instead of the proper sized Torx driver. Compaq’s assemblers also loved their auto-too-much-torquing screwdrivers.
I have tubs of those Compaq combo screws from a long time stripping interesting or useful things from ewaste computers. I’m not sure why I thought I’d need those, but I have actually used them in normal computer cases when I can’t find a screw with the right thread and a normal hex+Phillips head.
I see it as very fitting that this brick follows blockchains
Impact Drivers are amazing at taking out nearly-stripped screws. The repeating impact is great at applying some rotation to the screw, then allowing the bit to fall back down into the head each time instead of camming out and spinning.
Spent almost a decade in cabinet making shops and it was all Robertson or Phillips here in the US. Some screws were cut for both. Greatly prefer the Robertson, but they were also higher quality screws. Cheap drywall screws from big box stores can *easily* have their heads snapped off with an electric driver. Even worse, I snapped the tip off a P2 driver and NOTHING could get it out of the screw head, must have friction welded it ;)
I don’t think “rare outside Japan” can be correct. I’m in Scandinavia and I get really annoyed if I see a Phillips screw. Pozi is so much better and what you usually get at box-stores. =)
“Pozidrive is uncommon outside of Japan”. Funny how we use it all the time in Northern Europe, then.
PZ screws were the main type of screws sold since the 80’s here in The Netherlands. Since the last decade they are being replaced more and more with torx.
So I guess when you mean Japan, you mean Europe, centering on The Netherlands, as they had (still have ?) the closest trade relation with Japan for centuries.
Once again an article written by an American that has no idea about things outside of their own country. Like the centimetre, the pozidrive screw is ubiquitous the world over. Like the inch, philips screws are used by some people but are predominantly a US thing these days. Most other countries have transitioned to the better product, for some reason the USA is determined to hold on to outdated ideas.
You still use checks to pay for things, use inches to measure things and it would seem old fashioned screws to fasten things.
One place where slotted screws are still very common is watchmaking. Putting other drive patterns on such tiny screws is apparently difficult.