Now that we have decent VR goggles, the world is more desperate than ever for a decent haptic interface for interacting with computers. We might be seeing a new leap forward in this wild new haptic glove design from the Future Interfaces Group at Carnegie Mellon University.
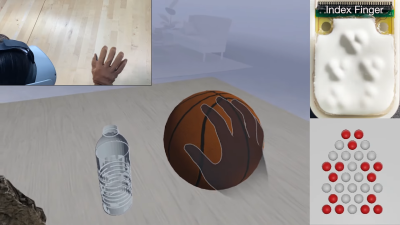
The glove gives each fingertip and thumb a small haptic pad. The pads are driven by electro-osmotic pumps, which are effectively solid-state. They use electricity to move fluid to create small dimples on the pad to provide haptic feedback to the user. The pads have 20 pixels per square centimeter, are quick and responsive, and can deform up to 0.5 mm in less than half a second.
The lightweight and self-contained electro-osmotic pads mean the haptic system can be far lighter and more practical than designs that use solenoids or other traditional technologies. The device is also high resolution enough that a user can feel pressure from a surface or the edges of an object in VR. If you watch the video, some of the demonstrations are quite revolutionary.
We’ve seen some other great haptics projects before too, like these low-cost force feedback gloves. Video after the break.
Continue reading “Lightweight Haptic Gloves With Electro-Osmotic Pump Arrays”