Everyone knows what its like to get a hankering for a specific food. In [Attoparsec]’s case, he wanted waffles. Not any waffles would do, though; he needed waffles in the form of a labyrinth. Those don’t exist, so he had to machine his own waffle maker.
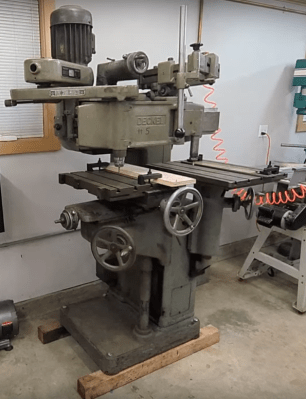
Most of us would have run this off on a CNC, but [Attoparsec] isn’t into CNCing–manual machining is his hobby, and he’s not interested in getting into another one, no matter how much more productive he admits it might make him. We can respect that. After a bit of brain sweat thinking of different ways to cut out the labyrinth shape, he has the opportunity to pick up an antique Deckle pantograph mill.
These machines were what shops used to do CNC before the ‘computer numeric’ part was a thing. By tracing out a template (which [Attoparsec] 3D prints, so he’s obviously no Luddite) complex shapes can be milled with ease. Complex shapes like a labyrnthine wafflemaker. Check out the full video below; it’s full of all sorts of interesting details about the machining process and the tools involved.
If you don’t need to machine cast iron, but are interested in the techniques seen here, a wooden pantorouter might be more your speed than a one-tonne antique. If you have a hankering for waffles but would rather use CNC, check out these design tips to help you get started. If pancakes are more your style, why not print them?
Shoutout to [the gambler] for sending this into the tip line. We think he struck the jackpot on this one. If you have a tip, don’t be shy. Continue reading “Antique Mill Satisfies Food Cravings”