Having finished the Tools of the Trade series on circuit board assembly, let’s look at some of the common methods for doing enclosures. First, and possibly the most common, is injection molding. This is the process of taking hot plastic, squirting it through a small hole and into a cavity, letting it cool, and then removing the hardened plastic formed in the shape of the cavity.
The machine itself has three major parts; the hopper, the screw, and the mold. The hopper is where the plastic pellets are dumped in. These pellets are tiny flecks of plastic, and if the product is to be colored there will be colorant pellets added at some ratio. The hopper will also usually have a dehumidifier attached to it to remove as much water from the pellets as possible. Water screws up the process because it vaporizes and creates little air bubbles.
Next the plastic flecks go into one end of the screw. The screw’s job is to turn slowly, forcing the plastic into ever smaller channels as it goes through a heating element, mixing the melted plastic with the colorant and getting consistent coloring, temperature, and ever increasing pressure. By the time the plastic is coming out the other end of the screw, and with the assistance of a hydraulic jack, it can be at hundreds of tons of pressure.
Finally, the plastic enters the mold, where it flows through channels into the empty cavity, and allowed to sit briefly to cool. The mold then separates and ejector pins push the part out of the cavity.
The mold is where all the exciting action happens, and we’ll focus on that. Most molds are made out of either aluminum or steel. Aluminum is great because it allows for cheap tooling that can be made quickly, but it has the downside of only lasting for 5-50 thousand shots (a shot is the term for one cycle of the mold to generate a part). Steel is used on most molds, and lasts for hundreds of thousands of shots.
Sometimes you can have a family mold, where you shoot multiple parts into the same mold. For example, you might have an enclosure that has a front piece, back piece, and cover, all made out of the same material. It’s better to have all three in the same mold not only to reduce mold costs but also to reduce the amount of time to make the parts (three parts in each cycle). Other times you may have a small part but need LOTS of them, like a bottle cap. For these you want multiple cavities, where instead of shooting a single cap at a time and incurring the time of waiting for each cycle for a single cap, you have lots of identical cavities and now you get lots of parts in the same cycle time.
For the really really big volumes, there are 3D molds that can produce enormous quantities of complicated parts. You will likely never be able to afford a mold like this one:
When sourcing a mold from China, there is a huge difference in price on one simple question: domestic or export. A lot of US based injection molding companies will outsource their mold making to China, have the mold shipped to the US, and then run the parts in the US. These molds are made for export and usually have higher quality steel, better cooling lines, and better consistency across multiple cavities. A mold made for import usually stays in house and the Chinese company produces your parts for you and ships them to you. They can afford to take a hit on the cost of the mold because they are making up for it in the cost of the parts.
Mold Features: Cooling Lines, Ejector Pins, Runners, and Sprue
There are a few features present in molds. Cooling lines aren’t in all of them, but they serve a useful function. As the mold is used over and over, it heats up and would eventually reach the temperature of the melted plastic. Naturally, when you open the mold only melted plastic would drip out. It’s important to keep the mold hot enough that the plastic will flow to all parts of the mold cavity before cooling, but cool enough that it will harden in a reasonable amount of time to keep the cycle time low.
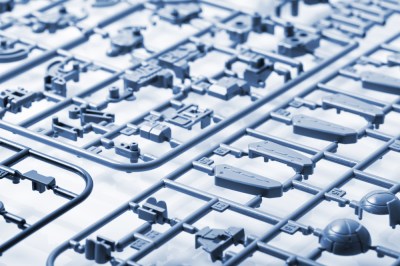
Ejector pins are little pins that press the part out of the mold. Molds are designed so that every time they open the part will be stuck on the same side of the mold. Then the ejector pins push them out. Usually the ejector pin is on the inside of the parts.
The nozzle is where the screw pushes the plastic in, and then the plastic travels through the sprue until it reaches the runners, which route the plastic to the openings of each of the cavities, called gates. If you’ve ever built a model airplane, you know what the runners and sprue are; they’re the round channels that hold the plastic pieces together. Also worth noting is the parting line, which is the line around the part where the two halves of the mold come together.
Molds with Multiple Parts
Most molds are simple in that they only require two parts that come together and apart. They are way cheaper and last longer. But sometimes it’s necessary to have features that require undercuts or side holes or things that are just not possible with a simple mold. There are still lots of creative solutions to avoid this, and workarounds that get you close, but in general you should aim for a straight mold. When that’s not possible, though, you have sliders and lifters, which are parts of a mold that come in from a side, and significantly increase the cost and complexity of a part. That’s why you’ll often see side holes off the parting line; it’s a way to create a hole without needing a slider because it’s just two halves of a hole put together at assembly time.
On sloppy molds that have been run for a long time, you’ll see something called flash. This is where the metal has worn down, usually at the parting line or the ejector pins, and thin slivers of plastic are formed in that empty space. Sometimes it’s cheaper to just employ someone with a knife to cut off the flash, but usually it’s an indication that it’s time for a new mold. You’ll also see ribs, which add strength to the part without adding lots of bulk. And you’ll see that the whole part has a consistent wall thickness.
Bosses (for holding screws) should be offset from the walls to prevent the walls from being too thick there. When you have thick sections, they tend to shrink when they cool, leading to a thing called a sink mark. You’ll see them on poorly designed parts. If you want to physically touch these things, check out the Protomold Design Cube (or check out their extensive resources for designing parts to be injection molded).
Understanding Setup
Injection molding is not cheap, and is not great if you only want a few of something. Generally, a factory will charge a fee every time you want to do a run of parts because they have to pay for the significant amount of time it takes to insert your mold into the machine, run parts until the mold is the right temperature, and get all the plastic from the previous job out and the colored plastic for your job in the screw.
If you’re looking for prototype quantities, like one to a couple hundred, there’s another option called casting, in which a positive is machined, then a silicon mold is created around that positive, and then a resin is poured into the mold (often under vacuum to fill all the voids and get the air bubbles out). This results in a part that is similar to what would be made with injection molding, but with a cheaper mold that’s good for only a few to a few hundred shots depending on the mold material and part complexity. We’ll cover casting later.
There is also research and development going into 3D printed molds. These are still very new and the quality fairly low, with the number of shots possible still extremely limited, but it’s promising. A third option, especially for small parts, is the drill or arbor press method, in which you make your own mold using a CNC out of aluminum, then heat up pellets and use the arbor press or drill press to force it into the cavity. One group even created a Kickstarter around the arbor press injection mold and managed to deliver, and someone else used a 3D printer to extrude plastic directly into a mold.
Injection molded parts are everywhere, and there are a lot of resources for learning how to design parts. A lot of things can be done very cheaply in high volume assuming you design your part specifically to be injection molded. In low volume, though, this is not the droid tool you are looking for.
As always Bill does a great job of explaining technical and industrial manufacturing. Thanks Bill!
More details on cnc machining-https://www.cncmachiningptj.com/CncMachining
Hehe I still have a Protomold Cube here from one of the K fairs in Düsseldorf.
If you guys ever have the chance to go there – do it! It’s 3 days worth of loud, crazy plastics-machines plus everything the industry needs.
What about multimaterial? Like the toothbrush-grips that have a soft gripping part and a sturdy plastic piece for stability? Can they do that in “one shot” on the same machine, or is that usually two seperate machines doing the hard plastic part first and then put that piece in an other mold on a second machine that adds the soft rubbery plastic?
And what about simulating molds? I’ve seen some software addons for the larger CAD tools that seem to be made specifically for mold designs and plastic flow simulations, but i’ve never bothered to check the details of what these tools really can do, since i’m only using CAD for some 3D printed parts.
You’re talking about a process called overmolding, and yes, it involves doing one shot with hard plastic, then putting that piece in a different mold and doing the second material.
Yes, there’s software that will model the molds, but you generally don’t need to worry about it unless you are designing the mold yourself. If you’re just designing a part, it’s good enough to have a basic idea of the general rules for design, and let the mold company handle the mold design.
More details on overmolding – https://www.creativemechanisms.com/blog/overmolding-prototype-design-development
Some parts, like two color car rear lights can be done in a single “rotating” mold. It take two shots to inject the part, but you get a complete part every cicle. I also made some complex molds for two material parts (Car air intakes) with sliders to separate the two cycles.
Multishot rotational molds are really amazing. Each shotbis the same cycle time and the mold rotates 180 degrees or 90 etc through all the shots. Finishednpary drops out. Maybe Bill can also talk about inserts or the edm process for making molds skippy
Yeah, those rotating platens are all fun and games until a setup guy puts the wrong clamps in the wrong place. Then when you go to start it, the mold opens up and tries to rotate, but the clamp slams into the tie bar!
So, there’s a lot of information not touched on here.
1) Mold design is an art. What isn’t said here is that parts are actually molded larger than they come out, and there’s a shrinkage factor which good mold makers will ask about. You’ll note that this is dependent upon material, so not only are molds expensive, they don’t tolerate material change well.
2) Mold flow analysis can be done rather easy, if not cheaply. It’s used to find knit lines (where separate flows meet), potential areas for short shot, cycle times based upon known flow rates, where gates need to be placed for material inflow, and to suggest where pockets of gas may accumulate and require a vent.
3) Overmolding and double barrel injection are pretty common practices in the industry. Overmolding takes an initial shot, and then adds a second shot of material. Thing baby carrier handles. The main body is a relatively sturdy polypropolene, and a much softer plastic is overmolded onto the handle. It can be done, but it gets expensive quickly.
4) Overseas shops are generally difficult to work with and through, unless customers have very wide expectations. It’s commonly said that a commodity molder can easily hire Chinese/Taiwanese mold shops without an issue. It’s a very different story when you want parts made to exacting tolerances. You might save 30k on a 250k mold, but you take a lot of risks. Maintenance is difficult after receiving it, it takes about 7 weeks to get the mold to the US by slow boat, and you’ll spend a small fortune on the PPAP/qualification process if you have to ship a material there for first shot, then ship the samples to the US for dimensionals, then ship the mold to the US. When all is said and done, non-domestic shops are generally only beaten out with large, simple, and multi-cavity molds.
5) Texture and reinforcement. I can’t believe this is never mentioned at all. Texturing a part is actually a process by which the mold is etched to create a positive surface texture. What is even more amazing is a reinforced polymer. Those glass beads are insanely abrasive, and the surface of the molds actually have to undergo surface hardening in a vacuum to create enough surface hardness to withstand shots.
6) Materials matter in molds. I’m betting people don’t think about it, but those huge slabs of steel are actually x-ray inspected before the milling and machining process. They do this because even small occlusions would completely waste immense amounts of machining time.
7) What about the gas assist? I’m betting people don’t think about this, but the chairs at McDonalds are actually a reinforced polymer that is hollow. Despite this, the chairs are injection molded. The entire frame is molded, partially cooled, and then a stream of nitrogen is pumped into the part at a gas plug. Overflow pucks are generated, where the still liquid inner material is pushed out of the part. Gas assist can create immensely complicated parts with large reinforcement, while keeping weight of the part surprisingly low. Lego might be interesting, but the strength of injection molding with the weight savings of blow or rotary molding are truly something amazing.
8) No real talk about cycle time here. I know this might be tangential, but cycle time is a huge part of the cost of parts. By slightly changing the design of a mold, or even slightly altering the model, you can shave 10-30% off of the cost of a part. It’s insane, but I’ve seen a “minor” engineering change request produce a mold whose cycle time was nearly halved. The cost of injection molding is in three places, cycle time, mold construction, and setup costs.
9) What really kills me about all of this is that there are some basic calculations to figure out what is necessary in injection molding. My favorite rule of thuimb is that per every square inch of part perpendicular to the barrel you need a certain tonnage to push the material. I’ve experienced 2000 ton presses, and double barrel 600 ton presses. The parts these things can create are massive. If you want an idea, check out the front hoods and back pieces of golf carts. Those things are produced in one shot, and the things are massive.
There’s a lot more to cover, but I’m already long winded. What you should know is that there are various failure modes for injection molding. Some are:
Knit lines (discontinuities where two flows merged, creating a weak point)
Short Shot (shot weight or velocity was insufficient to fill the part)
Splay – Contamination – Cold Slugs (discontinuities where injected material was inconsistent)
Sunbursting (a visible patter where cooling was accelerated, creating visual defects)
Delamination – Shininess – Streaking (setup parameters were wrong, causing various failure)
Also of concern, what material do you specify?
Virgin material is crazy expensive, but the material properties will more closely conform the the material supplier specification.
Regrind material (generally 10-20% is standard) reuses old bad parts, finely ground so they can be remelted. Lower cost, but material properties may degrade.
Color packages. This is a personal bugbear. The colorant is generally color, and UV protection. If you’re cheap, and want an outdoor enclosure, you generally buy polypropolene and add black colorant. The issue is that cheap colorant will lead to premature UV damage, and that black plastic could be a white chalky mess in less than 6 months of solar exposure. Again, materials are one of the cheapest parts of molding, and you should spend the extra on a good material. It can save you a recall, produce better parts, and decrease your overall cost by eating into cycle time.
Injection molding is a heck of a lot of fun, and there’s a lot to learn. While I can appreciate the video, it seems to be only the barest minimum look at the process. If you’re even slightly interested there’s a world of information out there.
I agree… hot runner systems, multi-cavity molds, process validations. Lots to learn about, even in the traditional injection molding business. Some of our machines even have robotic sprue pickers.
Then you have non-traditional molding machines used for making overmolded connectors, PCB’s or cannula assemblies. Often using rotary table or shuttle designs. Where I work we even have molds that would fit in your pocket (1.5″ cubes).
Brilliant reply, can I be the first to vote you should write a comprehensive guide to this for newbs?
Also, can I ask for your thoughts on this:
I looked at getting some obsolete car parts (rubber CV gaiter w/steel insert) made a while back, the per-part cost was really low (local low-volume rubber moulding co) but the mould would have been 5k+ so not viable for me to get a few spares made, even if I could sell a few extras on.
Step forward a year or two and I’ve bought myself a small CNC mill, so I’m now thinking maybe I could machine the mould at home from aluminium (OK it’d wear quick but I’d only be doing tens of parts from it, not thousands) but I have no idea if that’d fly at all – I understand that “pro” moulds are super high precision, polished, etc. but wondering if it would work at all (survive a few tens of uses with less than professional finish / requiring lots of trimming etc.) or if there’s no way it’d even work?
Basically if I could save 5k on the mould the rubber co have all the heated presses etc. to use the mould and would happily bang out parts for me for material + labour and life would be awesome.
Talk to this guy… http://polybushings.com/
Though for a gaiter, one off and low volume, I’d think of 3d printing a plug that could be sprayed or dipped (ever seen rubber glove manufacturing?)
Hmmm…. The off-the-cuff response is no. There are obvious safety concerns, milling tolerances, design choices, and quite a bit of other things to consider.
The long answer is as follows:
1) Do you know the material you are working with? I’m talking cooling time, required mold surface finish, flow rates, and shrinkage factor. All of this is essential for actual dimensional tolerances on your part. If you have enough tolerance to wing this then a different method of production would be better (I have no experience, but a poured silicon mold may be a better fit here).
2) What are your machining tolerances? These have to be very tight at the parting lines, and the vents have to be specifically designed such that internal gasses can be released while the injected material will not pass out of the mold.
3) What material are you going to use for machining? “Aluminum” is a bad joke. The aluminum alloy that you need must be completely free of internal defects, must polish and maintain polish well, and more importantly it must withstand abuse. Depending upon who is shooting your parts, the molds can be damaged rather easily.
4) I’m going to call this last section everything else. You have to make sure the gates leading into the part will allow enough flow to fill it completely. You’ve got to place the gates so as to minimize knit lines. You’ve got to have a plate manufactured to hold the mold into the injection molder, and these plates are hugely dependent on the shooter’s machinery. The material in question must be purchased, dried, and otherwise processed before shooting (and you don’t really buy “just a little bit” of raw material from most of the suppliers I’m aware of). Basically, there are about a dozen huge questions that are impossible to answer cheaply. That $5000 for a mold is insanely cheap, considering the design work associated with it. If you can actually get a mold that cheap then there’s either a misunderstanding of scale, or you’ll be ordering from a Chinese shop. Either way, injection molding is not a realistic bet for this level of project.
Thanks for a comprehensive reply there, good stuff. I guess I’m not making my own injection mold, no matter how rough a result I’m willing to accept.
The $5000 (well, gbp5000) for a mold is not a chinese job, it’s one thing the UK is good at – low-volume high-end engineering. That’s why we have so many motorsport teams and low-volume sports car companies here.
The comment above about dipping a form sparked my interest, sounds a lot more DIYable, especially with a pattern part to take a mold from. Will investigate that…
Don’t forget this software freebie for “students” http://www.autodesk.com/products/moldflow/overview
i used to work for a mold making company(my first job ever, spent quite a few years working on and off there), we did small batch runs for test runs or very specific parts, different enclosures for already existing products are fairly common for “special editions” or licensed products where one company needs to rebrand an already existing product.
doing a proper mold profile using test runs is a whole service in and of itself, especially if you are reworking molds.
there are quite a few processes used in making the molds so we had access to quite a few fun processes, like EDM, several cnc mills and lathes and some weird metal shaving machine i havent seen anywhere else since, it would remove shavings in a scraping motion and would produce some absolutely beautiful surfaces.
That would be a shaper. It’s a very antique technology that predates milling machines with rotating cutters. With the right tool profile and a super fine feed setting a shaper can produce a nearly mirror finish.
https://www.youtube.com/watch?v=V4D9jKRvFhs
Haha! I’ve seen two at my job; sure enough they are very old ugly machines. When you want a flat surface they give it to you!
thanks, always wondered what the English name for them were, the translation was scraper and nothing ever turned up when i searched for it
Pretty interesting, having worked with such machines before (not really as operator though, mostly inspecting and packaging the finished parts as well as maintaining pellet supply to the machine). I still work at the same company, AHT Cooling Systems, but in a different area. Plastic parts are not our trade, but we produce what we can in-house with 10 injection molding machines ranging from 65 to 1400 tons of locking force. However, unlike the description in the article, in our case colored parts are made from colored pellets only most of the time.
That’s interesting that you used the Protomold cube in this article. I am an injection molding technician at Protolabs here in Minnesota. I have actually molded that part. It’s funny because it has built in molding defects on the part in order to give the customer a visual idea of molding issues that can arise from poor part geometry. Sometimes, as a technician, it can actually be difficult to create the defects that are necessary in the part. We haven’t decided if that is a sign of good molding or bad molding! ;)
I have several of your gadgets, including both the cube and the demo mold. Also, molding defects only occur when you don’t want them, so your pretty much doomed there.
Yeah, there are thick walls that are supposed to have visible sink and thin walls with gas trapping and flowlines, but getting so many defects at the same time can be tricky.
The demo mold is really, really cool! I also like the texture sample ball. This is the first molding shop that I have worked in where they make products that they encourage employees to keep a few parts because they are unique pieces. Don’t get me wrong, nobody keeps customers’ parts, but the protomold in-house parts are fair game!
I keep retains of all my projects, beside QA master retains. In most cases I will keep a representative of the first article batch. I don’t know how many time they have proven useful when question arise. I also keep cosmetic flaws from cool projects to serve as show-and-tell parts. Mostly to show my wife, who acts impressed as not to hurt my feelings.
Yeah, keeping sample parts is part of our process flow. Since Protolabs is essentially a prototyping shop, our quality sysyem is a little less stringent than a traditional molding shop, so last part comparison is often needed.
However, we do run “sensitive” parts, like personal patents and government contracted parts, so just grabbing parts and taking them home can be a big no-no.
My father-in-law does mold repair, polishing and engineering changes by hand. Once a product begins to show irregularities along the seam of the mold, flashing begins to appear. That indicates some kind of wear on the rig that was previously producing parts with little or almost no flashing. The impressive part of his job is when he lays these massive molds on the ground and begins the processes of filling and polishing on-site. It’s detailed work and it’s becoming a rare skill.
Tons is not a unit of pressure…just saying.
It’s tonnage. It is a measure of clamp force pressure. It is how many tons of force are holding the mold halves together. If your injection pressure exceeds your clamp force, your parting line will blow open and cause flash
Oh, I just saw that he did not use tons in the way we molders do. Yes, here in the states, injection pressure or plastic pressure is almost exclusively measured in psi. (Pounds per square inch) I guess technically 2000 psi is a ton per square inch, but that’s pretty wonky. I’ve seen plastic pressures exceed 45,000 psi, so you can imagine the pressures involved!
This page on ICOMold’s website gives a really good explanation of clamping force, a.k.a. clamp tonnage: https://icomold.com/knowledge-base/clamp-tonnage-injection-molding/
I didn’t realize that most molds are rather simple and only require two parts to come together and apart. My brother is working on a class project, and he mentioned that he is going to need to do plastic injection molding for the assignment. Since it sounds like multiple parts won’t be that big of an issue, I’ll set some time aside to learn more about molding so that the project can be completed. http://www.pacific-im.com/plastic-injection-molding-and-assembl
The mold is updated very quickly, and only by updating can the power be maintained.