Launching things with electromagnetism is pretty fun, with linear induction motors being a popular design that finds use from everywhere in hobby designs like [Tom Stanton]’s to the electromagnetic launchers on new US and Chinese aircraft carriers. Although the exact design details differ, they use magnetic attraction and repulsion to create a linear motion on the propulsive element, like the sled in [Tom]’s design. Much like the electromagnetic catapults on a Gerald R. Ford-class carrier, electrical power is applied to rapidly move the sled through the channel, akin to a steam piston with a steam catapult.
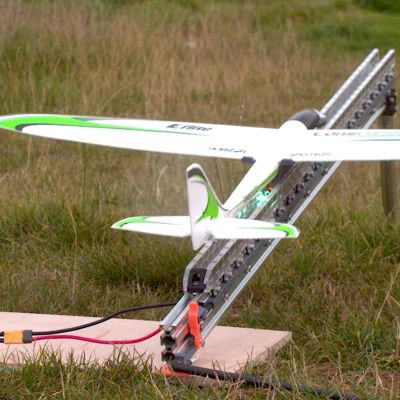
For [Tom]’s design, permanent magnets are used along both sides of the channel in an alternating north/south pole fashion, with the sled using a single wound coil that uses brushes to contact metal rails along both sides of the channel. Alternating current is then applied to this system, causing the coil to become an electromagnet and propel itself along the channel.
An important consideration here is the number of turns of wire on the sled’s coil, as this controls the current being passed, which is around 90 A for 100 turns. Even so, the fastest sled design only reached a speed of 44 mph (~71 km/h), which is 4 mph faster than [Tom]’s previous design that used coils alongside the channels and a sled featuring a permanent magnet.
One way to increase the speed is to use more coils on the sled, with a two-coil model launching a light-weight model airplane to 10.2 m/s, which is not only a pretty cool way to launch an airplane, but also gives you a sense of appreciation for the engineering challenges involved in making an electromagnetic catapult system work for life-sized airplanes as they’re yeeted off an aircraft carrier and preferably not straight into the drink.
Continue reading “Launching Model Airplanes With A Custom Linear Induction Motor”