3D printing is arguably over-used in the maker community. It’s just so easy to run off a quick prototype and then… well, it’s good enough, right? Choosing the right plastic can go a long way to making sure your “good enough” prototype really is good enough for long term use. If you’re producing anything with gearing, you might want to cast your eyes to a study by [Mert Safak Tunalioglu] and [Bekir Volkan Agca] titled: Wear and Service Life of 3-D Printed Polymeric Gears.
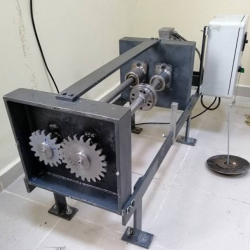
The authors printed simple test gears in ABS, PLA, and PETG, and built a test rig to run them at 900 rpm with a load of 1.5 Nm against a steel drive gear. The gears were pulled off and weighed every 10,000 rotations, and allowed to run to destruction, which occurred in the hundreds-of-thousands of rotations in each case. The verdict? Well, as you can tell from the image, it’s to use PETG.
The authors think that this is down to PETG’s ductility, so we would have liked to see a hard TPU added to the mix, to say nothing of the engineering filaments. On the other hand, this study was aimed at the most common plastics in the 3D printing world and also verified a theoretical model that can be applied to other polymers.
This tip was sent in by [Benjamin], who came across it as part of the research to build his first telescope, which we look forward to seeing. As he points out, it’s quite lucky for the rest of us that the U.S. government provides funding to make such basic research available, in a way his nation of France does not. All politics aside, we’re grateful both to receive your tips and for the generosity of the US taxpayer.
We’ve seen similar tests done by the community — like this one using worm gears — but it’s also neat to see how institutional science approaches the same problem. If you need oodles of cycles but not a lot of torque, maybe skip the spurs and print a magnetic gearbox. Alternatively you break out the grog and the sea shanties and print yourself a capstan.