Researchers recently shared details on creating foldable, self-locking structures by using multi-material 3D printing. These origami-inspired designs can transition between flat and three-dimensional forms, locking into place without needing external support or fasteners.
The 3D structure of origami-inspired designs comes from mountain and valley fold lines in a flat material. Origami designs classically assume a material of zero thickness. Paper is fine, but as the material gets thicker things get less cooperative. This technique helps avoid such problems.
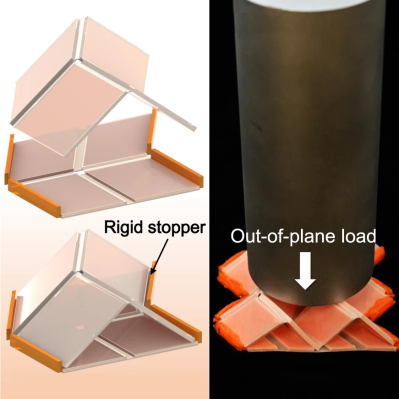
The research focuses on creating so-called “thick-panel origami” that wraps rigid panels in a softer, flexible material like TPU. This creates a soft hinge point between panels that has some compliance and elasticity, shifting the mechanics of the folds away from the panels themselves. These hinge areas can also be biased in different ways, depending on how they are made. For example, putting the material further to one side or the other will mechanically bias that hinge to fold into either a mountain, or a valley.
Thick-panel origami made in this way paves the way towards self-locking structures. The research paper describes several different load-bearing designs made by folding sheets and adding small rigid pieces (which are themselves 3D printed) to act as latches or stoppers. There are plenty of examples, so give them a peek and see if you get any ideas.
We recently saw a breakdown of what does (and doesn’t) stick to what when it comes to 3D printing, which seems worth keeping in mind if one wishes to do some of their own thick-panel experiments. Being able to produce a multi-material object as a single piece highlights the potential for 3D printing to create complex and functional structures that don’t need separate assembly. Especially since printing a flat structure that can transform into a 3D shape is significantly more efficient than printing the finished 3D shape.