Over the weekend, I had the pleasure of helping out at the KW Hackathon in Waterloo, Ontario, sponsored by PCH Hardware, who hosts hackathons and meetups around the world to help inspire invention and entrepreneurship. This was the sixth hardware based hackathon they have hosted.
When they host a hackathon, they gather local sponsors and provide the tools and resources for the entrants to actually develop a working prototype in less than 54 hours, that they then can pitch to a panel of judges to win some awesome prizes. Did we mention it’s free to register? The next one is in London, England.
Personally, I provided some mentorship in product design and development, but more importantly, I opened up the use of my giant laser cutter to help the teams create real prototypes, and learn more about rapid prototyping using a laser cutter. Everyone wanted to 3D print their prototypes at first — but there was a limited number of printers available, and long wait times. We introduced them to sites like www.makercase.com, a site that will generate laser cutter plans for enclosures that you specify the dimensions of, and of course, the ability to search google for “laser cut arduino case” to find pre-designed laser designs for electronics.
Some teams more experienced in CAD got creative and made cool decahedrons which actually helped create a working prototype the way they envisioned it on paper.
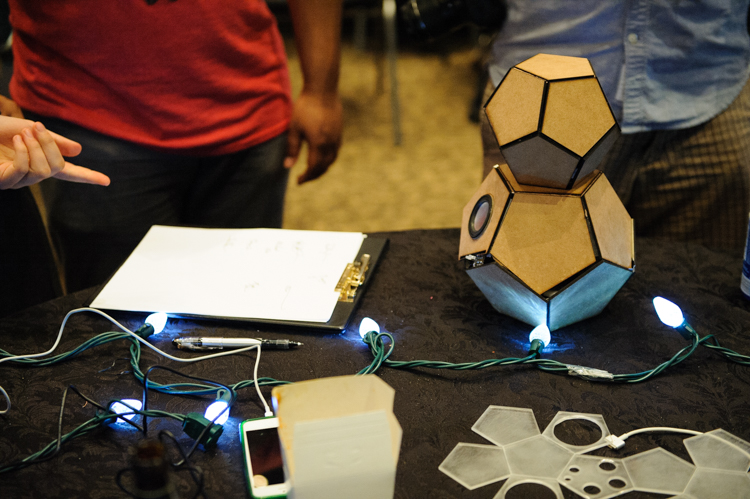
In addition to the main event, they hosted keynote speakers and workshops to help take teams ideas even further — we think Communitech (the hosting venue) really summed up the purpose of having hackathons nicely:
“Useful stuff does really emerge from hackathons: some realized ideas, but more importantly, new human hacker connections and a deeper sense of capability and our capacity to create beyond the software realm.”
Overall, the event was fantastic, and it makes us wish there were more like it. You could feel the buzz of excitement in the room when creative people got together and started designing and making things. Oh and the free food was pretty awesome too — especially for students.
For more information about the event, check out the news piece by [Darin White] for Communitech News.