For some reason, we never tire of stories highlighting critical infrastructure that’s running outdated software, and all the better if it’s running on outdated hardware. So when we learned that part of the San Francisco transit system still runs on 5-1/4″ floppies, we sat up and took notice. The article is a bit stingy with the technical details, but the gist is that the Automatic Train Control System was installed in the Market Street subway station in 1998 and uses three floppy drives to load DOS and the associated custom software. If memory serves, MS-DOS as a standalone OS was pretty much done by about 1995 — Windows 95, right? — so the system was either obsolete before it was even installed, or the 1998 instance was an upgrade of an earlier system. Either way, the San Francisco Municipal Transportation Agency (SFMTA) says that the 1998 system due to be replaced originally had a 25-year lifespan, so they’re more or less on schedule. Replacement won’t be cheap, though; Hitachi Rail, the same outfit that builds systems that control things like the bullet train in Japan, is doing the job for the low, low price of $212 million.
festo10 Articles
[Festo]’s Underwater Robot Uses Body-Length Fins
[Festo] have come up with yet another amazing robot, a swimming one this time with an elegant propulsion mechanism. They call it the BionicFinWave. Two fins on either side almost a body-length long create a wave which pushes water backward, making the robot move forward. It’s modeled after such fish as the cuttlefish and the Nile perch.
What was their elegant solution for making the fins undulate? Nine lever arms are attached to each fin. Those lever arms are controlled by two crankshafts which extend from the front of the body to the rear, one for each side. A servo motor then turns each crankshaft. Since the crankshafts are independent, that means each fin operates independently. This allows for turning by having one fin move faster than the other. A third motor in the head flexes the body, causing the robot to swim up or down.
There’s also a pressure sensor and an ultrasonic sensor in the head for depth control and avoiding objects and walls. While these allow it to swim autonomously in its acrylic, tubular track, there is wireless communication for recording sensor data. Watch it in the video below as it effortlessly swims around its track.
[Festo] has created a lot of these marvels over the years. We’ve previously covered their bionic hopping kangaroo (we kid you not), their robot ants with circuitry printed on their exoskeleton, and perhaps the most realistic flapping robotic bird ever made.
Continue reading “[Festo]’s Underwater Robot Uses Body-Length Fins”
Pneumatic Rotary Vane Joints Lend A Gentle Helping Hand
Festo has released a video showing the workings of their BionicCobot, a pneumatic robot arm developed for lending a helping hand to humans at a workstation. Since it works intimately with humans, it has to be safe, producing no harmful movements, and reacting when encountering an obstacle such as an arm containing delicate human bone. This it does using pneumatics and rotary vanes.
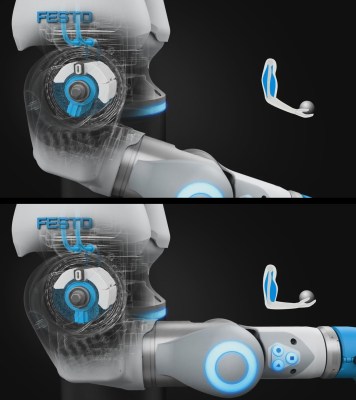
The arm has seven degrees of freedom, three in the shoulder, one in the elbow, another in the lower arm, and two in the wrist. But you won’t find any electric motor or gears. Instead each contains a rotary vane. Compressed air pushes on both sides of the vane. If the air pressure is the same on both sides of the vane then it doesn’t rotate. But with more pressure on one side than the other, the vane rotates. This is much like in a human arm, where two muscles work together to bend the arm, one muscle contracts while the other relaxes. Together they’re referred to as an antagonistic pair. In addition, each joint has a circuit board with two pressure sensors for monitoring the joint.
Using pneumatics, if an obstacle is encountered, the pressure can be released, making it instantly safe. And air being compressible, the joint can behave like a spring, further adding to the safeness. By controlling the pressure, the spring can be made more or less tense.
You can see it in action in the video below the break, along with more details such as how they use ROS, the popular, open system Robot Operating System which we’ve seen here a lot before, along with their Festo valve bank, one of which our own [James Hobson] used for his slick elysium exoskeleton. The video also covers how they handled running the hoses, the kinematics and the UI software.
Continue reading “Pneumatic Rotary Vane Joints Lend A Gentle Helping Hand”
A Robot Arm With The Tender Grip Of An Octopus
If you’ve ever experimented with a robot gripper, you’ll know that while it is easy to make an analogue of the human ability to grip between thumb and forefinger, it is extremely difficult to capture the nuances of grip with the benefit of touch feedback to supply only just enough of the force required to grip and hold an object. You as a human can pick up a delicate eggshell without breaking it using the same hand you might use to pick up a baseball or a cricket ball, but making your robot do the same thing is something of an engineering challenge.
The robot gripper is something that has exercised the minds of the folks at Festo, and the solution they have arrived at is as beautiful as it is novel. They have produced a gripper based upon the action of an octopus tentacle, though unlike the muscle of the real thing they’ve created a silicone tube which bends inwards when inflated. Its inner surface is covered with octopus-like suckers, some of which can be activated by a vacuum. The result is a very capable and versatile gripper which due to its soft construction is ideal for use in environments in which robots and humans interact.
They’ve put up a slick video showing the device in action, which we’ve put below the break. Tasks such as gripping a rolled-up magazine or a plastic bottle that would tax more conventional grippers are performed faultlessly.
Continue reading “A Robot Arm With The Tender Grip Of An Octopus”
Robot Ants Wear Circuitry As Exoskeleton
[FESTO] keeps coming up with new tricks that make us both envious and inspired. Take their bionicANTs for example. Watching a group of them cooperate to move objects around looks so real that you’re instantly reminded of the pests crawling across your floor, but looking at them up close they’re a treasure trove of ideas for your next robot project.
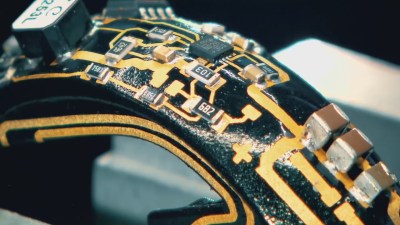
The exoskeleton is 3D printed but they then use the outer surface of that exoskeleton as a circuit board for much of the circuitry. The wiring is “painted on” using a 3D MID (Molded Interconnect Device) process. While FESTO didn’t give specifics about their process, a little research shows that 3D MID involves the 3D printed object being made of a special non-conductive metal material, a laser then “drawing” the traces in the material, and then dipping the object in various baths to apply copper, nickel and gold layers. We mortal hackers may not have the equipment for doing this ourselves in our workshops but seeing the beautiful result should be inspiration enough to get creative with our copper tape on the outer surfaces of our 3D printed, CNC’d, or hand-carved parts.
We also like how they took a the mouse sensor from under a regular computer mouse and attached it to the ant’s underside, pointing down for precision dead reckoning. For the legs they used three piezo bending transducers. However, these give a deflection of only 1.5mm in both directions, not enough for walking. They increase this to over 10mm with the addition of a plastic hinge, another idea to keep in mind when building that next tiny robot. And there are more ideas to be taken advantage of in their ants, which you can see being built in the video below.
3D Cocooner (3D Lattice Printer)
Sometimes it feels like we haven’t yet tapped into all the possibilities of additive manufacturing. Festo, a company that loves to try innovative things (and not always bring them to market), just came up with something called the 3D Cocooner — essentially, a rostock style 3D printer on its side, with a UV cure feature to allow it to build up skeletal structures and lattice style shapes.
Similar to the MX3D-Metal 3D printer (which is currently on a mission to build a bridge end-to-end — by itself), this 3D printer specializes in printing structures as opposed to the more traditional layer approach. It’s called the 3D Cocooner as it is a bionic technology platform designed to “spin” complex lattices, very similar to naturally occurring structures.
The cool thing is, it’s not actually using plastic filament like most printers — it’s actually printing using string! The string is covered with a special UV resin which is then hardened into place as soon as it is expelled from the print head — making this more like a giant robot spider than a 3D printer.
Festo Creates Bionic Kangaroo; Steve Austin Unimpressed
[Dr. Wilfried Stoll] and a team at Festo have created an incredible robot kangaroo. Every few years the research teams at Festo release an amazing animal inspired robot. We last covered their smartbird. This year, they’ve created BionicKangaroo (pdf link). While The Six Million Dollar Man might suggest otherwise, Bionics is use of biological systems in engineering design. In this case, Festo’s engineers spent two years studying the jumping behavior of kangaroos as they perfected their creation.
Kangaroos have some amazing evolutionary adaptations for jumping. Their powerful Achilles tendon stores energy upon landing. This allows the kangaroo to increase its speed with each successive jump. The kangaroo’s tail is essential for balancing the animal as it leaps through the air. The Festo team used a thick rubber band to replicate the action of the tendons. The tail is controlled by electric servomotors.
Festo is known for their pneumatic components, so it’s no surprise that the kangaroo’s legs are driven by pneumatic cylinders. Pneumatics need an air supply though, so the team created two versions of the kangaroo. The first uses an on-board air compressor. The second uses a high-pressure storage tank to drive the kangaroo’s legs. An off the shelf Programmable Logic Controller (PLC) acts as BionicKangaroo’s brain. The PLC monitors balance while controlling the pneumatic leg cylinders and electric tail motors. Unfortunately, BionicKangaroo isn’t completely autonomous. The Thalmic Labs Myo makes a cameo appearance in the video. The Kangaroo’s human controller commands the robot with simple arm movements.
While the BionicKangaroo is graceful in its jumps, it still needs a bit of help when turning and taking simple steps. Thankfully we don’t think it will be boxing anytime soon.
Continue reading “Festo Creates Bionic Kangaroo; Steve Austin Unimpressed”