Thanks to its innovative gameplay and quirky humor, Portal became an instant hit when it was released in 2007. Characters became cultural icons, quotes became memes and the game became a classic along with its 2011 sequel. Even today, more than a decade later, we regularly see hackers applying their skills in recreating some of the game’s elements. One beautiful example is [Joran de Raaff]’s physical rendition of a Portal Turret.
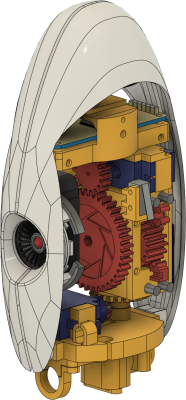
[Joran] decided to use his 3D printer to create a Turret that can move and speak exactly as it does in the game. The result, as you can see in the video embedded below, was a triumph. We’re making a note here, “huge success”. The outer shell is a beautiful shiny white, an effect achieved through patient sanding, priming, and spraying with high-gloss paint. The internals are even more impressive with servos, microswitches, and a whole array of 3D-printed gears, cams, and levers.
A motion sensor activates the Turret whenever a human moves nearby. It will then open its wings and fire its guns while playing the corresponding sounds from the game. Its brains are formed by a Wemos D1 which drives the various LEDs and servos, while an MP3 player board holds a library of sound bites and plays them through a speaker hidden inside the Turret’s shell.
After posting his creation on YouTube [Joran] got many requests for the 3D files, so he made them available and wrote a comprehensive build guide. This should enable anyone with a 3D printer to build this neat gun, without getting too much science done. If this model is too small for you, then perhaps this life-sized model is more to your liking. If you prefer your Turret small and cute, check out this plushie version.
Continue reading “3D Printed Portal Turret Moves And Talks Like The Real Thing”