One thing going slightly viral lately is footage of Disney’s “HoloTile” infinite floor, an experimental sort of 360° treadmill developed by [Lanny Smoot]. But how exactly does it work? Details about that are less common, but [Marques Brownlee] got first-hand experience with HoloTile and has a video all about the details.
HoloTile is a walking surface that looks like it’s made up of blueish bumps or knobs of some kind. When one walks upon the surface, it constantly works to move its occupant back to the center.
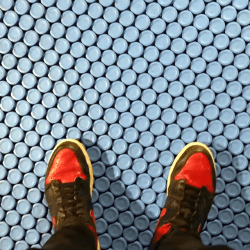
Each of these bumps is in fact a disk that has the ability spin one way or another, and pivot in different directions. Each disk therefore becomes a sort of tilted wheel whose edge is in contact with whatever is on its surface. By exerting fine control over each of these actuators, the control system is able to create a conveyor-belt like effect in any arbitrary direction. This can be leveraged in several different ways, including acting as a sort of infinite virtual floor.
[Marques] found the system highly responsive and capable of faster movement that many would find comfortable. When walking on it, there is a feeling of one’s body moving in an unexpected direction, but that was something he found himself getting used to. He also found that it wasn’t exactly quiet, but we suppose one can’t have everything.
How this device works has a rugged sort of elegant brute force vibe to it that we find appealing. It is also quite different in principle from other motorized approaches to simulate the feeling of walking while keeping the user in one place.
The whole video is embedded just below the page break, but if you’d like to jump directly to [Marques] explaining and showing exactly how the device works, you can skip to the 2:22 mark.
Continue reading “Here’s How That Disney 360° Treadmill Works”