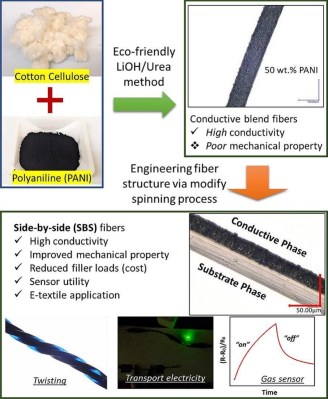
With the rise of ‘smart’ devices, it seems like only a matter of time before smart fabrics become an every day thing. Yet a complication with these is that merely threading copper wires into clothing is neither practical nor very durable, which is why researchers have been trying to find a way to combine cellulose-based fibers like cotton with another, conductive material like carbon to create an affordable, resilient material which can provide the pathways for these smart fabrics. Recently a team at Washington State University created a version that integrates polyaniline (PANI, press release for paywalled paper), which is a well-known conductive polymer.
A recent review article by Duan-Chao Wang and colleagues in Polymers covers the research in conductive fibers, with conductive additives ranging from carbon nanotubes (CNT) and graphene to various metallic compounds and conductive polymers. As noted by Wang et al., a major aspect to successful commercialization is enabling scaling and cost-effectiveness of producing such fibers. This is the core of the achievement by the WSU team, who used a side-by-side structure of a cellulose substrate and the PANI conductive covering, which should be easier to produce and more durable than previous attempts to merge these two materials into conductive fibers suitable for fabrics.
Other research by Zhang-Chi Ling and colleagues, as reported earlier this year in NPG Asia Materials, details the creation of composite, conductive fibers made from bacterial cellulose with in-situ entanglement of CNTs. With even 100,000 bending cycles not showing much degradation, this could be another good candidate for conductive fabrics. Which of these approaches will first hit mass-production is still anyone’s guess, but we might see them sooner rather than later.