It seems hard to imagine, but in the early part of the 20th century, there weren’t a lot of great options for creating copies of documents. The most common method was to use carbon paper to create multiple copies at once from a typewriter or a line printer. All that changed with a company called Haloid. Never heard of them? They later became the Xerox company.
The underlying technology dates back to 1938 (invented by a physicist who was also a lawyer). In 1944, they produced a practical copier and shortly thereafter sold the rights to Haloid. The Haloid company originally made photographic copy machines that used wet chemistry.
In 1959, the Xerox 914 (so called because it could copy a 9″ x 14″ document) came on the scene (that’s it, below). The 650 pound copier could make seven copies per minute and came with a fire extinguisher because it had a tendency to burst into flames. If you didn’t want to spend the $27,500 price tag, you could rent for only $25/month (keep in mind that in 1959, $25 would buy about 25 pounds of T-bone steaks). You can see a commercial for the 914 in the video below.
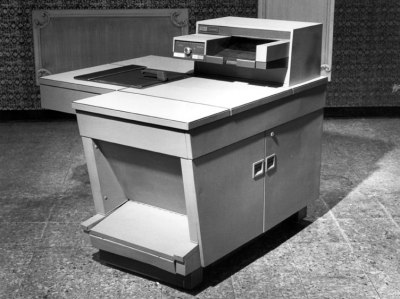
In the commercial, you’ll see them make a big deal out of the fact that the print was dry. That’s because a lot of previous machines used actual photographic processes with wet chemistry. Obviously, that also took special paper.
Even Further Back
If the copier didn’t exist until recently, how did people make copies before? Turns out there were lots of ways to make copies of varying degrees of bad quality or extreme trouble. In some sense, the best copies were made by scribes just writing down a second copy of things. There were a variety of machines that would capture what you wrote and make a copy by mechanical or other means. A polygraph (not the lie detecting kind) allowed Thomas Jefferson to write letters and make a copy. The machine moved a pen to match the movements of the author’s pen, thus making a near perfect copy. With a few adjustments, this became the pantograph which not only does the same job, but also can shrink or enlarge the copy. Carbon paper was widely used to make multiple copies of handwritten and typewritten documents.
Continue reading “Retrotechtacular: The Incredibly Difficult Task Of Copying A Document” →