Well, it’s official — AI is ruining everything. That’s not exactly news, but learning that LLMs are apparently being used to write scientific papers is a bit alarming, and Andrew Gray, a librarian at University College London, has the receipts. He looked at a cross-section of scholarly papers from 2023 in search of certain words known to show up more often in LLM-generated text, like “commendable”, “intricate”, or “meticulous”. Most of the words seem to have a generally positive tone and feel a little fancier than everyday speech; one rarely uses “lucidly” or “noteworthy” unless you’re trying to sound smart, after all. He found increases in the frequency of appearance of these and other keywords in 2023 compared to 2022, when ChatGPT wasn’t widely available.
Author: Dan Maloney2977 Articles
Hackaday Podcast Episode 268: RF Burns, Wireless Charging Sucks, And Barnacles Grow On Flaperons
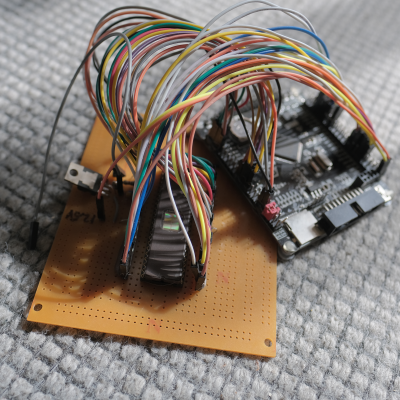
Elliot and Dan got together to enshrine the week’s hacks in podcast form, and to commiserate about their respective moms, each of whom recently fell victim to phishing attacks. It’s not easy being ad hoc tech support sometimes, and as Elliot says, when someone is on the phone telling you that you’ve been hacked, he’s the hacker. Moving on to the hacks, we took a look at a hacking roadmap for a cheap ham radio, felt the burn of AM broadcasts, and learned how to program old-school EPROMs on the cheap.
We talked about why having a smart TV in your house might not be so smart, especially for Windows users, and were properly shocked by just how bad wireless charging really is. Also, cheap wind turbines turn out to be terrible, barnacles might give a clue to the whereabouts of MH370, and infosec can really make use of cheap microcontrollers.
Grab a copy for yourself if you want to listen offline.
AI System Drops A Dime On Noisy Neighbors
“There goes the neighborhood” isn’t a phrase to be thrown about lightly, but when they build a police station next door to your house, you know things are about to get noisy. Just how bad it’ll be is perhaps a bit subjective, with pleas for relief likely to fall on deaf ears unless you’ve got firm documentation like that provided by this automated noise detection system.
OK, let’s face it — even with objective proof there’s likely nothing that [Christopher Cooper] is going to do about the new crop of sirens going off in his neighborhood. Emergencies require a speedy response, after all, and sirens are perhaps just the price that we pay to live close to each other. That doesn’t mean there’s no reason to monitor the neighborhood noise, though, so [Christopher] got to work. The system uses an Arduino BLE Sense module to detect neighborhood noises and Edge Impulse to classify the sounds. An ESP32 does most of the heavy lifting, including running the UI on a nice little TFT touchscreen.
When a siren-like sound is detected, the sensor records the event and tries to classify the type of siren — fire, police, or ambulance. You can also manually classify sounds the system fails to understand, and export a summary of events to an SD card. If your neighborhood noise problems tend more to barking dogs or early-morning leaf blowers, no problem — you can easily train different models.
While we can’t say that this will help keep the peace in his neighborhood, we really like the way this one came out. We’ve seen the BLE Sense and Edge Impulse team up before, too, for everything from tuning a bike suspension to calming a nervous dog. Continue reading “AI System Drops A Dime On Noisy Neighbors”
Chip Mystery: The Case Of The Purloined Pin
Let’s face it — electronics are hard. Difficult concepts, tiny parts, inscrutable datasheets, and a hundred other factors make it easy to screw up in new and exciting ways. Sometimes the Magic Smoke is released, but more often things just don’t work even though they absolutely should, and no amount of banging your head on the bench seems to change things.
It’s at times like this that one questions their sanity, as [Gili Yankovitch] probably did when he discovered that not all CH32V003s are created equal. In an attempt to recreate the Linux-on-a-microcontroller project, [Gili] decided to go with the A4M6 variant of the dirt-cheap RISC-V microcontroller. This variant lives in a SOP16 package, which makes soldering a bit easier than either of the 20-pin versions, which come in either QFN or TSSOP packages.
Wisely checking the datasheet before proceeding, [Gili] was surprised and alarmed that the clock line for the SPI interface didn’t appear to be bonded out to a pin. Not believing his eyes, he turned to the ultimate source of truth and knowledge, where pretty much everyone came to the same conclusion: the vendor done screwed up.
Now, is this a bug, or is this a feature? Opinions will vary, of course. We assume that the company will claim it’s intentional to provide only two of the three pins needed to support a critical interface, while every end user who gets tripped up by this will certainly consider it a mistake. But forewarned is forearmed, as they say, and hats off to [Gili] for taking one for the team and letting the community know.
More Mirrors (and A Little Audio) Mean More Laser Power
Lasers are pretty much magic — it’s all done with mirrors. Not every laser, of course, but in the 1980s, the most common lasers in commercial applications were probably the helium-neon laser, which used a couple of mirrors on the end of a chamber filled with gas and a high-voltage discharge to produce a wonderful red-orange beam.
The trouble is, most of the optical power gets left in the tube, with only about 1% breaking free. Luckily, there are ways around this, as [Les Wright] demonstrates with this external passive cavity laser. The guts of the demo below come from [Les]’ earlier teardown of an 80s-era laser particle counter, a well-made instrument powered by a He-Ne laser that was still in fine fettle if a bit anemic in terms of optical power.
[Les] dives into the physics of the problem as well as the original patents from the particle counter manufacturer, which describe a “stabilized external passive cavity.” That’s a pretty fancy name for something remarkably simple: a third mirror mounted to a loudspeaker and placed in the output path of the He-Ne laser. When the speaker is driven by an audio frequency signal, the mirror moves in and out along the axis of the beam, creating a Doppler shift in the beam reflected back into the He-Ne laser and preventing it from interfering with the lasing in the active cavity. This forms a passive cavity that greatly increases the energy density of the beam compared to the bare He-Ne’s output.
The effect of the passive cavity is plain to see in the video. With the oscillator on, the beam in the passive cavity visibly brightens, and can be easily undone with just the slightest change to the optical path. We’d never have guessed something so simple could make such a difference, but there it is.
Continue reading “More Mirrors (and A Little Audio) Mean More Laser Power”
Mining And Refining: Uranium And Plutonium
When I was a kid we used to go to a place we just called “The Book Barn.” It was pretty descriptive, as it was just a barn filled with old books. It smelled pretty much like you’d expect a barn filled with old books to smell, and it was a fantastic place to browse — all of the charm of an old library with none of the organization. On one visit I found a stack of old magazines, including a couple of Popular Mechanics from the late 1940s. The cover art always looked like pulp science fiction, with a pipe-smoking father coming home from work to his suburban home in a flying car.
But the issue that caught my eye had a cover showing a couple of rugged men in a Jeep, bouncing around the desert with a Geiger counter. “Build your own uranium detector,” the caption implored, suggesting that the next gold rush was underway and that anyone could get in on the action. The world was a much more optimistic place back then, looking forward as it was to a nuclear-powered future with electricity “too cheap to meter.” The fact that sudden death in an expanding ball of radioactive plasma was potentially the other side of that coin never seemed to matter that much; one tends to abstract away realities that are too big to comprehend.
Things are more complicated now, but uranium remains important. Not only is it needed to build new nuclear weapons and maintain the existing stockpile, it’s also an important part of the mix of non-fossil-fuel electricity options we’re going to need going forward. And getting it out of the ground and turned into useful materials, including its radioactive offspring plutonium, is anything but easy.
Continue reading “Mining And Refining: Uranium And Plutonium”
No Active Components In This Mysterious Audio Oscillator
What’s the simplest audio frequency oscillator you can imagine? There’s the 555, of course, and we can think of a few designs using just two transistors or even a few with just one. But how about an oscillator with no active components? Now there’s a neat trick.
Replicating [Stelian]’s “simplest audio oscillator on the Internet” might take some doing on your part, since it relies on finding an old telephone. Like, really old — you’ll need one with the carbon granule cartridge in the handset, along with the speaker. Other than that, all you’ll need is a couple of 1.5-volt batteries, wiring everything in one big series loop, and placing the microphone and speaker right on top of each other. Apply power and you’re off to the races. [Stelian]’s specific setup yielded a 2.4-kHz tone that could be altered a bit by repositioning the speaker relative to the mic. On the oscilloscope, the waveform is a pretty heavily distorted sine wave.
It’s a bit of a mystery to [Stelian] as to how this works without something to provide at least a little gain. Perhaps the enclosure of the speaker or the mic has a paraboloid shape that amplifies the sound just enough to kick things off? Bah, who knows? Let the hand-waving begin!
Continue reading “No Active Components In This Mysterious Audio Oscillator”