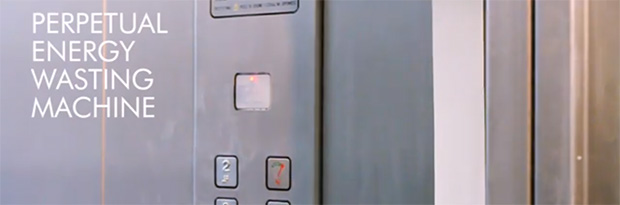
The greatest – and last – question that will ever be asked is, “How can the net amount of entropy of the universe be massively decreased”. It follows then, that the worst – and possibly first – question ever asked is, “How can the net amount of entropy of the universe be massively increased?” While for the former question there’s insufficient data for a meaningful answer, we’ve found the answer to the latter question. It’s a machine designed to waste energy, and the exact opposite of a perpetual motion machine.
The machine is set up along two stories of a building, with cables, pulleys, and levers constantly pressing an elevator button. The device is powered by the elevator doors opening, so when the elevator opens of the first floor, the part of the machine on the second story calls the elevator. This repeats ad infinitum.
Wait. It gets better. Inside the elevator car, there’s a modified printing calculator also powered by the elevator doors. Every time the doors open, it calculates the amount of energy consumed for each cycle of the elevator. It’s a hydraulic elevator without a countersink, so moving down is effectively free, but each cycle of the elevator still uses up 11.8 Kilojoules of the universe’s energy. To make the build a complete waste of resources, the printing calculator neatly empties it’s printed tape into a wastepaper bin.
We’re tempted to call this a [Rube Goldberg] machine, but that doesn’t seem to fit this machine that does absolutely nothing. Calling it a useless box is more fitting, but this is far, far more impressive than a box that turns itself off. Whatever it is, you can see a video of it in action below.
Continue reading “How Can The Net Amount Of Entropy Of The Universe Be Massively Increased?” →