During the Second World War, the United States was pumping out weapons, aircraft, and tanks at an absolutely astonishing rate. The production of military vehicles and equipment was industrialized like never before, and with luck, never will be again. But even still, soldiers overseas would occasionally find themselves in unique situations that required hardware that the factories back at home couldn’t provide them with.
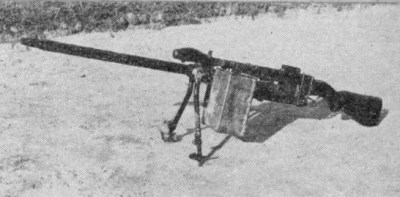
Which is precisely how a few United States Marines designed and built the “Stinger” light machine gun (LMG) during the lead-up to the invasion of Iwo Jima in 1945. The Stinger was a Browning .30 caliber AN/M2, salvaged from a crashed or otherwise inoperable aircraft, that was modified for use by infantry. It was somewhat ungainly, and as it was designed to be cooled by the air flowing past it while in flight, had a tendency to overheat quickly. But even with those shortcomings it was an absolutely devastating weapon; with a rate of fire at least twice that of the standard Browning machine guns the Marines had access to at the time.
Six Stingers were produced, and at least on a Battalion level, were officially approved for use in combat. After seeing how successful the weapon was during the invasion of Iwo Jima, there was even some talk of putting the Stinger into larger scale production and distributing them. But the war ended before such a plan could be put into place.
As such, the Stinger is an exceedingly rare example of a field modified weapon that was not only produced in significant numbers, but officially recognized and even considered for adoption by the military. But the story of this hacked machine gun actually started years earlier and thousands of kilometers away, as Allied forces battled for control of the Solomon Islands.
Continue reading “Stinger: The Hacked Machine Gun Of Iwo Jima”