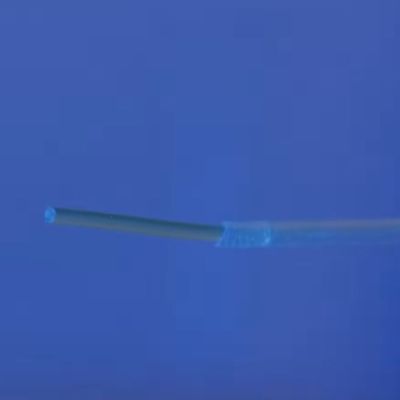
PVA filament is an interesting filament type, for the reason that while it can be printed with any FDM printer, it supposedly readily dissolves in water, which is also the reason why PVA glue sticks are so popular when doing crafts and arts with young children. This property would make PVA filament ideal for printing supports if your printer can handle two different materials at the same time. So surely you can just pick any old PVA filament spool and get to printing, right? As [Lost in Tech] found out, this is not quite the case.
As an aside, watching PVA supports dissolve in water set to classical music (Bach’s Air from Orchestral Suite No. 3) is quite a pleasant vibe. After thus watching the various PVA prints dissolve for a while, we are left to analyze the results. The first interesting finding was that not every PVA filament dissolved the same way, or even fully.
The first gotcha is that PVA can stand for polyvinyl acetate (the glue stick) or polyvinyl alcohol (a thickener and stabilizer) , with the ‘PVA’ filament datasheets for each respective filament showing various combinations of both types of PVA. This results in wildly different properties per filament, both in terms of Shore hardness, their printability, as well as their ability to dissolve in water. Some of the filament types (Yousu, Reprapper) also have an outer layer and inner core for some reason.
Ultimately the message appears to be that ‘PVA’ filament requires a fair bit of research to have any chance of having a relatively trouble-free printing experience.