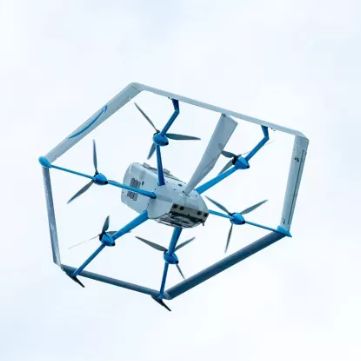
When Amazon started its Prime Air drone delivery service in 2022, it had picked College Station (Texas) and Lockeford (California) as its the first areas where the service would be offered. Two years later, Amazon has now announced that it will be expanding to the West Valley of the Phoenix Metro area in Arizona from a new Tolleson center, while casually mentioning buried in the press release that the Lockeford area will no longer be serviced. No reason for this closure was provided, but as a quite experimental service drastic shifts can be expected as Amazon figures out what does and does not work.
Amazon Prime Air features custom drones that can transport packages up to 5 lbs (~2.27 kg) to its destination within an hour, if the item is listed as Prime Air capable for your area. Along with the change in service areas, Amazon is also testing its new MK30 drone (pictured, top), which should be much quieter due to a new propeller design and have twice the range of the old MK27 as well.
Even if flying drone delivery isn’t quite a blow-away success yet, Amazon doesn’t seem to be letting up on investing in it, and it could be argued that for certain items like medication or perishables, it does make a certain sense over traditional delivery and pick-up methods.