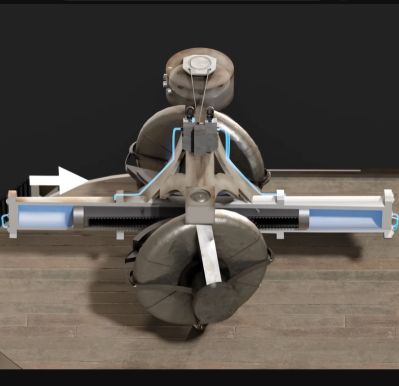
Everyone who has ever handled a spinning gyroscope found themselves likely mesmerized by the way it absolutely maintains its orientation even when disturbed. Much of modern technology would be impossible without them, whether space telescopes or avionics. Yet during the early 20th century a much more radical idea was proposed for gyroscopes, one that would essentially have turned entire trains into gyroscopes. This was the concept of the Gyro Monorail, with Louis Brennan being among those who built a full-sized, working prototype in 1910, with its history and fate covered in detail by [Primal Space], along with an accompanying video.
At first glance it may seem rather daft to have an entire train balancing on a single rail track, using nothing but gyroscopic forces to keep the entire contraption level and balanced even when you feel the thing should just tip over. Yet the gyroscopic system that Brennan created and patented in 1903 turned out to function really well, and reliably kept the train on its single track. Key to this was the use of two gyroscopic wheels, each spinning in an opposite direction, with a pneumatic system linked to a gear system between the two wheels that used the gyroscope’s precession in corners to quickly establish a new balance.
Despite this success, investors were unconvinced, and regular trains were already firmly established, and the system would also require that each car had its own gyro system. Even so, the idea of the gyro monorail never truly died, as evidenced by the recently created German MonoCab-OWL project. This targets converting single-rail sections into dual-rail, bi-directional service with no infrastructure investment required.
Thanks to [Stephen Walters] for the tip.
Continue reading “The Gyro Monorail: How To Make Trains Better With A Gyroscope”