Can you use brake cleaner for flux removal on PCBs? According to [Half Burnt Toast], yes you can. But should you? Well, that’s another matter.
In our experience, flux removal seems to be far more difficult than it should be. We’ve seen plenty of examples of a tiny drop of isopropyl alcohol and a bit of light agitation with a cotton swab being more than enough to loosen up even the nastiest baked-on flux. If we do the same thing, all we get is a gummy mess embedded with cotton fibers smeared all over the board. We might be doing something wrong, or perhaps using the wrong flux, but every time we get those results, we have to admit toying with the idea of more extreme measures.
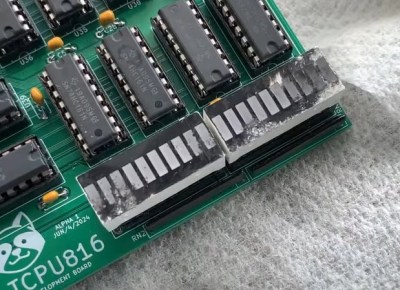
[Toast] went there, busting out a fresh can of brake cleaner and hosing down some of the crustier examples in his collection. The heady dry-cleaner aroma of perchloroethylene was soon in the air, and the powerful solvent along with the high-pressure aerosol blast seemed to work wonders on flux. The board substrate, the resist layer, and the silkscreen all seemed unaffected by the solvent, and the components were left mostly intact; one LED bar graph display did a little melty, though.
So it works, but you might want to think twice about it. The chlorinated formula he used for these tests is pretty strong stuff, and isn’t even available in a lot of places. Ironically, the more environmentally friendly stuff seems like it would be even worse, loaded as it is with acetone and toluene. Whichever formula you choose, proceed with caution and use the appropriate PPE.
What even is flux, and what makes it so hard to clean? Making your own might provide some answers.
Continue reading “Blast Away The Flux — With Brake Cleaner?”