Considering that it’s only existed for around a decade, the commercial desktop 3D printing market has seen an exceptional amount of turnover. But then, who could resist investing in an industry that just might change the world? It certainly didn’t hurt that the MakerBot Cupcake, arguably the first “mass market” desktop 3D printer, was released the same month that Kickstarter went live. We’ve long since lost count of the failed 3D printer companies that have popped up in the intervening years. This is an industry with only a handful of remaining veterans.
One of the few that have been with us since those heady early days is LulzBot, founded in 2011 by parent company Aleph Objects. Their fully open source workhorses are renowned for their robust design and reliability, though their high prices have largely kept them off the individual hacker’s bench. LulzBot was never interested in the race to the bottom that gave birth to the current generation of sub-$200 printers. Their hardware was always positioned as a competitor to the likes of Ultimaker and MakerBot, products where quality and support are paramount above all else.
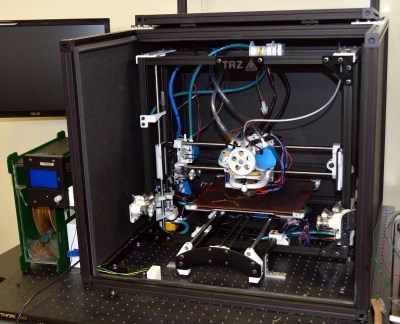
While LulzBot printers never made an impact on the entry-level market, there are institutions willing to purchase a highly dependable American-made 3D printer regardless of cost. The United States Marines used LulzBot printers to produce replacement Humvee door handles in the field, and some of the modifications that were necessary to meet their stringent requirements eventually resulted in updates to the consumer version of the printer. NASA used a highly modified LulzBot TAZ 4 to print PEI at temperatures as high as 500°C, producing parts far stronger than anything that had previously been made on a desktop 3D printer.
Yet despite such auspicious customers, LulzBot has fallen on difficult times. Consumers have made it abundantly clear they aren’t willing to pay more than $1,000 for a desktop printer, and competition above that price point is particularly fierce. Last month we started hearing rumblings in the Tip Line that the vast majority of LulzBot staff were slated to be let go, and we soon got confirmation and hard numbers from local media. Of the company’s 113 employees, only 22 would remain onboard to maintain day-to-day operations. Production on their flagship models would continue, albeit at a reduced pace, and all existing warranties would be honored. But the reduction in staff and limited cash flow meant that the development of future products, such as the LulzBot Bio tissue printer, would be put on hold.
LulzBot wasn’t quite dead, but it was hard to see this as anything but a step on the road to insolvency. A number of insiders we spoke to said they had heard a buyout was expected, and today we can report that the sale of Aleph Objects to Fargo Additive Manufacturing Equipment 3D (FAME 3D) is official. Production of the current LulzBot models is expected to continue, and some of the 91 laid off employees are likely to be hired back, but continuing Aleph Objects CEO Grant Flaharty says the details are still being finalized.
This new financial backing, provided by a venture capitalist, is certainly good news. But it would be naive to think this is the end of LulzBot’s troubles. The market has spoken, and unless the company is willing to introduce a vastly cheaper version of their printer to entice the entry-level customer as Prusa Research has recently done, it’s unclear how an infusion of cash will do anything but delay the inevitable.
For what it’s worth, we hope LulzBot finds some way to thrive. The ideal of building fully open source printers is something near and dear to the heart of Hackaday, but after the loss of PrintrBot, we’re all keenly aware of how difficult it is for small American companies to compete in the modern 3D printing market.