[Proper Printing] clearly enjoys pushing the boundaries of 3D printed materials, and sometimes this requires building custom 3D printers or at least the business end of them. Flexible filaments can be a bit of a pain to deal with, simply because most extruders are designed to push the filament into the hot end with a simple hobbed bolt (or pinch roller setup) and only work reliably due the rigidity of the plastic itself. Once you go flexible, the rigidity is reduced and the filament often deflects sideways and the extruder jams. The longer the filament path leading to the hotend, the harder it gets. The dual belt drive extruder (they’re calling it ‘proper extruder’) grips the filament on two sides with a pair of supported belts, guiding it into the hotend without allowing it to deflect sideways. The extruder body and gears were resin printed (but, we checked — the design is suitable for FDM printing as well) proving that resin printing on modern printers, does indeed maintain adequate dimensional accuracy allowing the building of mechanisms, despite the naysayers! Continue reading “Tame Your Flexible Filaments With This Belt-Drive Extruder”
3d Printer hacks2569 Articles
3D Printing Fabrics Is Easier Than You Think
Conventional textiles made of woven threads are highly useful materials. [Sara Alvarez] has had some success creating fabric-like materials through 3D printing, and though they’re not identical, they have some similar properties that make them unique and useful.
Fabrics are made by the weaving or knitting together many threads into a cohesive whole. [Sara]’s 3D-printed fabrics are different, since the printer can’t readily weave individual fibers together. Instead, a variety of methods are used to create similar materials.
The simplest is perhaps the chainmail method, where many small individual links join together to make a relatively rigid material. Alternatively, G-code or careful modelling can be used to create fabric-like patterns, which are printed directly in flexible material to become a fabric-like sheet. Finally, the infill method takes advantage of code inbuilt to a slicer to create a pattern that can be 3D-printed to create a fabric like material by removing the top and bottom layers of the print.
[Sara] demonstrates creating a simple “fabric” swatch using the slicer method, and demonstrates the qualities of the finished product. She also shows off various applications that can take advantage of this technique.
If you’re a 3D-printing enthusiast who also loves making clothes and apparel, consider printing up some shoes – like these we’ve seen before. Video after the break. Continue reading “3D Printing Fabrics Is Easier Than You Think”
Bi-Color Filament Kicks 3D Printed Optical Illusions Up A Notch
A new video from [Make Anything] shows off a nice combo that has a real visual impact: ambiguous shapes that look different depending on what angle they are viewed at, combined with an unusual filament that enhances the effect greatly. As you can see in the image above that shows off just such an object in front of a mirror, the results are pretty striking.
Japanese mathematician and artist [Kokichi Sugihara] figured out the math behind such objects, of which his ambiguous cylinder illusion is probably the most well-known. That inspired [Make Anything] to create his own strange objects, which he showcases happily. He adds one more twist, however.
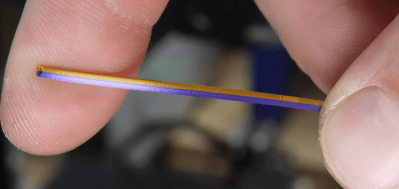
What is a natural complement to an object that looks different based on the direction from which it is viewed? A filament whose color depends on what direction it is viewed, of course! The filament in question is MatterHackers Quantum dual-color PLA, and this unusual filament is split right down the middle in two different colors, resulting in a printed object whose exact color depends entirely on the viewing angle, and the object geometry.
The resulting objects look especially striking when demonstrated with the help of a mirror, because as the object turns and changes, so does the color change as well. You can watch it all in action in the video below (embedded after the page break) which showcases quite a few different takes on the concept, so check it out to see them all.
3D printing has certainly opened up a new doors when it comes to brain-bending optical effects, like this hypnotic Moiré pattern, and perhaps dual-color filament can enhance those as well.
Continue reading “Bi-Color Filament Kicks 3D Printed Optical Illusions Up A Notch”
Portable 3D Printer Gets Even Smaller, Faster, Better
How do you improve on a fast, capable 3D printer that sports an innovative design and is portable enough to fit in a printer spool box? Judging by what went into the Positron V3 portable printer, (video, embedded below) it takes a lot of hard work and an unwillingness to settle for compromise designs. Plus a few lucky breaks and some design wizardry.
When we first reported on [Kralyn]’s innovative “Positron” printer, its chief selling points were its portability and unique layout. With a fold-down Z-axis and a CoreXY-style drive in the base, plus an interesting 90° hot end and transparent heated build plate, the Positron managed to hit most of its design goals. But there’s always room for improvement, and Positron V3, shown in the video below, has made some pretty substantial leaps over that original concept.
The V3 design keeps the basic layout of the original, but greatly improves the usability and portability, while increasing performance and build volume. The heated borosilicate build plate is now held to the Z-axis drive with a much sturdier strut, and gets its juice through a high-temperature MagSafe connector. The X- and Y-axes are now driven by pancake steppers, which along with adding idler pulleys that are coaxial to the drive pulleys, make the CoreXY drive, and hence the printer’s base, much more compact. The printer is still much, much faster than most traditional gantry design, and print quality is on par with anything available commercially. And yes, it still fits into a standard 1-kg filament spool box when folded up.
We love this design, and the story of how the V3 came about and the intermediate V2 that didn’t make the cut is a fascinating case study in design. And as a bonus, [Kralyn] will open-source the V3 design, so you can build your own as soon as he releases the files.
Continue reading “Portable 3D Printer Gets Even Smaller, Faster, Better”
Flexible Grip For Hammer Made With 3D Printing Pen
When it comes to putting a flexible grip on a tool, you might reach for a self-fusing silicone tape or other similar product. However, [Potent Printables] has discovered you can easily create a flexible grip using a 3D-printing pen and some flex filament.
In this case, a hammer first gets a layer of blue painters tape wrapped around its wooden handle. This serves as a base layer to promote good adhesion. A simple paper template was then printed as a guide for creating the graphics on the flexible grip. Flexible filament was fed through the 3D pen, with the red and black details of the graphics printed first. Then, white flex filament was used to make the rest of the flexible grip. A wood burning tool was then used to smooth out the first layer of flex filament, before a second layer was added on top.
The result is a flexible white grip on the hammer which is stuck fast, likely due to shrinkage as the plastic cooled after printing. We’ve seen some other creative grips made with 3D printing before, too. Video after the break.
Continue reading “Flexible Grip For Hammer Made With 3D Printing Pen”
3D Printed Linear Actuator Is Cheap And Strong
Motors are all well and good for moving things, but they’re all about the round-and-round. Sometimes, you need to move something back and forth, and for that a linear actuator will do the trick. While they can be readily sourced for under $50 online, [Michael Rechtin] genuinely felt like reinventing the wheel, and managed to whip up a 3D-printed design that costs under 20 bucks.
The basic design is simple, consisting of a small motor which is geared down through several stages using simple spur gears. The last gear in the train is tasked with turning a lead screw which drives the arm of the linear actuator back and forward.
For simplicity, [Michael] used a 24V brushed DC gearmotor for its low cost and the fact it already has a step-down gearbox integrated into the design. It’s paired with a couple more 3D-printed spur gears to provide even more torque. Instead of a fancy lead screw, the build instead just uses a quarter-inch bolt sourced from Home Depot, which can be had much cheaper. This pushes a 3D-printed arm back and forth thanks to a nut stuck in the arm. It’s all wrapped up in a neat-and-tidy 3D-printed housing. The design is able to push with a force of roughly 220 lbs. For a more practical idea of its strength, it can readily crush an empty soda can.
The video on the design is great, showing how important features like limit switches are added, and how the wiring can be neatly hidden away inside the housing. We’ve seen [Michael’s] work before, too, like strength testing various types of 3D printed gears. Video after the break.
Continue reading “3D Printed Linear Actuator Is Cheap And Strong”
3D Printing Hack Leverages Vase Mode Structurally
Conceptually, FDM 3D printing is quite a simple process: you define a set of volumes in 3D space, then the slicing software takes a cut through the model at ever-increasing heights, works out where the inner and outer walls are, and then fills in the inside volume sparsely in order to tie the walls together and support the top layers that are added at the end.
But as you will find quite quickly, when models get larger and more complex, printing times can quickly explode. One trick for large models with simple shapes but very low structural needs is to use so-called ‘vase mode’, which traces the outline of the object in a thin, vertical spiral. But this is a weak construction scheme and allows only limited modelling complexity. With that in mind, here’s [Ben Eadie] with a kind-of halfway house technique (video, embedded below) that some might find useful for saving on printing time and material.
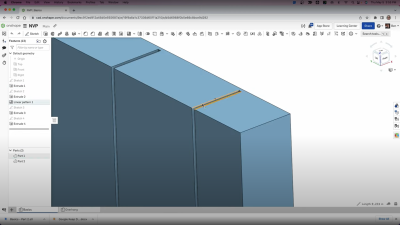
The idea is to use vase mode printing, but by manipulating the shell of the model, adding partially cut-through slots around the perimeter, and critically, adding one slot that goes all the way.
First you need a model that has an inner shell that follows the approximate shape of the outer, which you could produce by hollowing out a solid, leaving a little thickness. By making the slot width equal to half the thickness of the nozzle size and stopping the slots the same distance from the outer shell, vase mode can be used to trace the outline of shape, complete with supporting ribs in between the inner and outer walls of the shell.
Because the slot is narrower than the extrudate, the slot walls will merge together into one solid rib, tying the objects’ walls to each other, but critically, still allowing it to be printed in a continuous spiral without any traditional infill. It’s an interesting idea, that could have some merit.
There are other ways to stiffen up thing printed parts, such as using surface textures, But if you’re fine with the thin shell, but want to have a little fun with it, you can hack the g-code to make some really interesting shapes.
Continue reading “3D Printing Hack Leverages Vase Mode Structurally”