Fans of retro computers from the 8-bit and 16-bit eras will be well aware of the green death that eats these machines from the inside out. A common cause is leaking electrolytic capacitors, with RTC batteries being an even more vicious scourge when it comes to corrosion that destroys motherboards. Of course, time rolls on, and new generations of machines are now prone to this risk. [MattKC] has explored the issue on Microsoft’s original Xbox, built from 2001 to 2009.
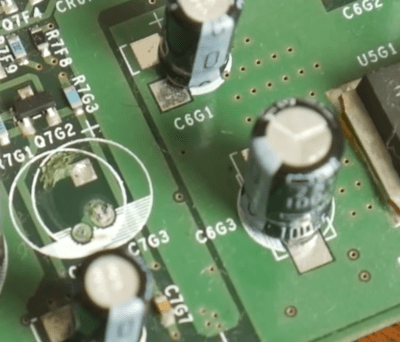
The original Xbox does include a real-time clock, however, it doesn’t rely on a battery. Due to the RTC hardware being included in the bigger NVIDA MCPX X3 sound chip, the current draw on standby was too high to use a standard coin cell as a backup battery. Instead, a fancy high-value capacitor was used, allowing the clock to be maintained for a few hours away from AC power. The problem is that these capacitors were made during the Capacitor Plague in the early 2000s. Over time they leak and deposit corrosive material on the motherboard, which can easily kill the Xbox.
The solution? Removing the capacitor and cleaning off any goop that may have already been left on the board. The fastidious can replace the part, though the Xbox will work just fine without the capacitor in place; you’ll just have to reset the clock every time you unplug the console. [MattKC] also points out that this is a good time to inspect other caps on the board for harmful leakage.
We’ve seen [MattKC] dive into consoles before, burning his own PS1 modchip from sourcecode found online. Video after the break.
Edit: As noted by [Doge Microsystems], this scourage only effects pre-1.6 Xboxes; later models don’t suffer the same problem, and shouldn’t be modified in this way.
Continue reading “Save Your Original Xbox From A Corrosive Death”