[3DPrintBunny] is someone who continually explores new techniques and designs in 3D printing, and her latest is one she calls “pause-and-attach”, which she demonstrates by printing a vase design with elements of the design splayed out onto the print bed.
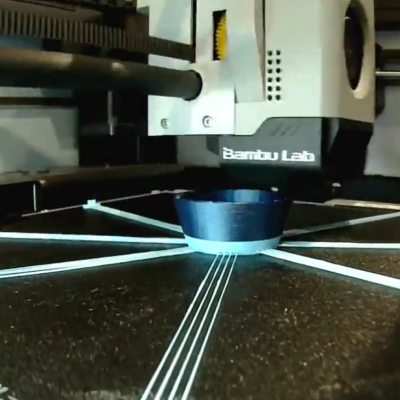
At a key point, the print is paused and one peels up the extended bits, manually attaching them to sockets on the main body of the print. Then the print resumes and seals everything in. The result is something that appears to defy the usual 3D printer constraints, as you can see here.
Pausing a 3D print to insert hardware (like nuts or magnets) is one thing, but we can’t recall seeing anything quite like this approach. It’s a little bit reminiscent of printing foldable structures to avoid supports in that it prints all of its own self-connecting elements, but at the same time it’s very different.
We’ve seen [3DPrintBunny]’s innovative approaches before with intentional stringing used as a design element and like the rest of her work, it’s both highly visual and definitely it’s own thing. You can see the whole process in a video she posted to social media, embedded below.
Continue reading “See The “Pause-and-Attach” Technique For 3D Printing In Action”