Here’s an idea that [Nephlonor] shared a couple years ago, but is worth keeping in mind because one never knows when it might come in handy. He 3D printed a marble run track and kept the generated tree supports. As you can see in the image above, the track resembles a roller-coaster and the tree supports function as an automatically-generated scaffolding for the whole thing. Clever!
As mentioned, these results are from a couple of years ago; so this idea should work even better nowadays. Tree supports have come a long way since then, and are available in more slicers than just Cura.
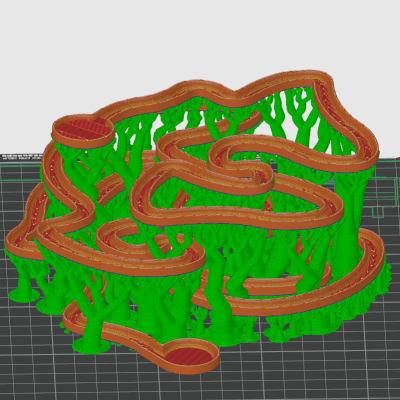
If you’re going to do this, we suggest reducing or eliminating the support interface and distance, which is the spacing between the supports and the rest of the model. The interface makes supports easier to remove, but if one is intending to leave it attached, it makes more sense to have a solid connection.
And while we’re on the topic of misusing supports, we’d like to leave you with one more trick to keep in mind. [Angus] of Maker’s Muse tucked a great idea into one of his videos: print just the support structure, and use it as a stand for oddly-shaped objects. Just set the object itself to zero walls and zero infill, and the printer will generate (and print) only the support structure. Choose an attractive angle, and presto! A display stand that fits the object like a glove.
You can watch a brief video of the marble run embedded below. Again, tree supports both look better and are available in more slicers nowadays. Have you tried this? If so we’d love to hear about it, so let us know in the comments!
Continue reading “Tree Supports Are Pretty, So Why Not Make Them Part Of The Print?”