Sticking the perfect landing can take years of practice for a human gymnast, and it seems the same is true for little monopedal jumping robots. Salto-1P, an old acquaintance here on Hackaday, always needed to keep jumping to stay upright. With some clever control software improvements, it can now land reliably on an area the size of a coin, and then stay there. (Video after the break)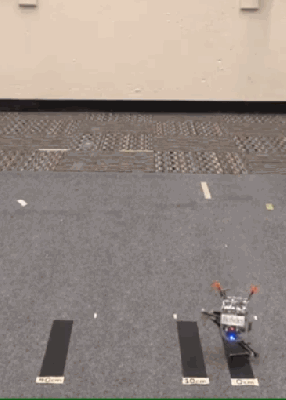
[Justin Yim] from the UC Berkeley’s Biomimetics Lab has been working on Salto for the past four years, and we’ve covered it twice before. Attitude control is handles by a combination of propeller thrusters for roll and yaw, and a reaction wheel for pitch.While it was already impressive before, it had a predictable landing area about the size of a dinner plate.
The trick to the perfect landing is a combination of landing angle, angular velocity and angular momentum. Salto can only correct for ±2.3° of landing angle error, because it doesn’t have a second foot to catch itself when something goes wrong. Ideally the robot’s angular velocity and momentum should be as close as possible to 0 at takeoff, which gives the reaction wheel maximum control authority in flight, as well as on landing. Basically a well executed takeoff directly influences the chances of a good landing. [Justin] does an excellent job explaining all this and more on the project’s presentation video. Continue reading “Little Jumping Bot Can Now Stick The Perfect Landing” →