Once upon a time, pants were created. After a while, women were allowed to wear them too. This has made a lot of people happy and been widely regarded as a good thing. There is a problem, however – bathroom signage is largely predicated on the idea that there are two rigid genders which all humans must be sorted into, and they’re defined by whether you’re wearing pants or a dress. [Robb Godshaw], among others, disagrees with this, and set about building a gender fluid bathroom sign.
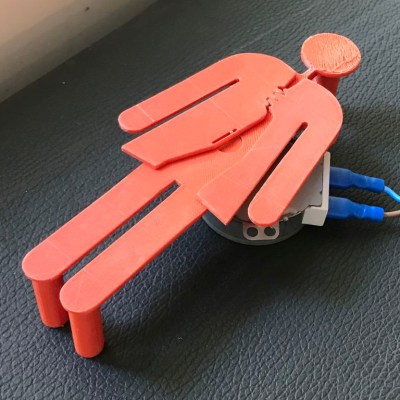
The project seeks to exploit the traditional symbols of “male” and “female” – the human figures wearing pants or a dress – by creating a sign that switches between the two every 15 seconds. This is likely to initially confuse – one might imagine the bathroom is actually changing its gender designation rapidly, forcing users to complete their business in an incredibly short timeframe. However, the message behind the project is to highlight the absurdity of defining gender by pants, colours, or indeed in a binary nature at all. [Robb] also helpfully points out that all humans have to pass waste, regardless of gender.
The sign is built with 3D-printed components, using a crank mechanism to actuate the moving parts. The mechanism is designed to give equal time to the pants and dress configurations. [Robb] shares the important details necessary to replicate the build, such as how to assemble the metal crank pin insert with a paperclip and a lighter. It’s particularly tidy the way the mechanism is integrated into the parts themselves. In true hacker style, the motor is a standard microwave oven turntable motor, which can be harvested easily from a junk appliance and can be plugged straight into mains power to operate, if you know what you’re doing. If you don’t, check out our primer on the topic.
Overall, the project is a great use of hacker techniques, like 3D printing and harvesting parts, to make a statement and start a conversation, while being fun, to boot. We’ve also seen some of [Robb]’s work before, like this giant hamster wheel for people. Video after the break.